The Vision for Heartland Polymers Comes to Fruition; Building Sustainability into Its Foundation
Sustainability is at the heart of the Heartland Polymers story. Being only the second polypropylene plant to come online in a decade, they have a lot to say about it as they initiate production. Owned by parent company Inter Pipeline, the company began construction in early 2018 on the Heartland Complex, which was completed mid-2022. The operation just announced in March 2023 that they have entered full commercial production and are the first integrated propane dehydrogenation and polypropylene complex in North America built on a single site.
“Thanks to the dedication and hard work of our operations team, I am proud to report that our propane dehydrogenation plant has been providing a reliable on-site source of feedstock to our polypropylene production since the end of 2022. Heartland is responsibly producing and shipping polypropylene to customers daily, and we continue to focus on optimizing our service,” said Todd Karran, CEO at Heartland Polymers.
The facility was designed with environmental stewardship as a core value since its inception and is expected to be the lowest emitting operation of its kind. Verified by an independent third party, the company reports that it expects the Heartland Complex to emit 65% lower greenhouse gas emissions than similar operations around the world. The plant uses hydrogen produced as a by-product at the propane dehydrogenation facility as fuel for HPC to reduce GHG emissions by approximately 130,000 tonnes per year. “This sets us apart and delivers on our promise of something new and different to serve the needs of our customers,” Karran said.
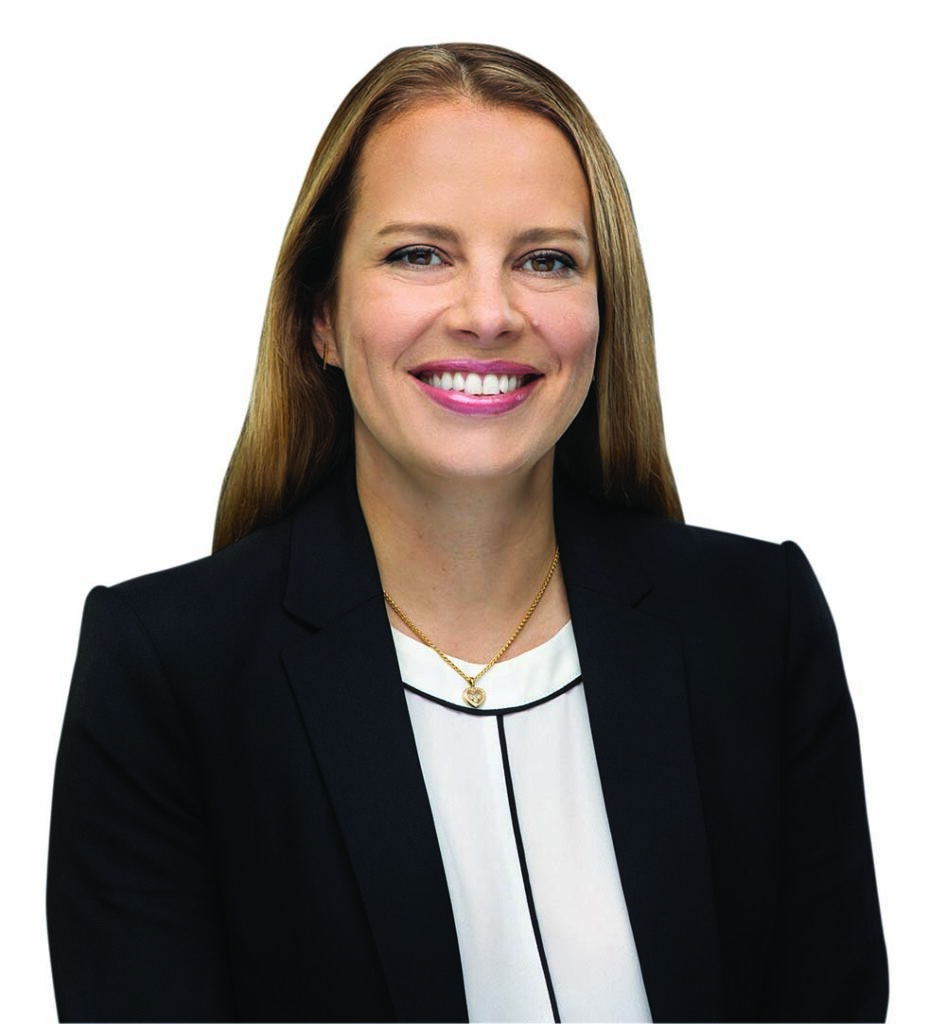
Our pellets are 35% less carbon intensive than the average North American pellet
Amelie Delisle, Vice President of Petrochemical Commercial, Heartland Polymers.
and 65% less than the international average and it is verified by an independent third-party study. We’re very proud of this.
With a workforce of approximately 300, and centrally located in the stable climate of Alberta, Canada on 220 acres, and direct access to a vast railway system, the plant production capacity is expected to be 525,000 metric tonnes per year or 1.16 billion pounds per year – enough to fill 16 rail cars per day.
With the project since 2011, we caught up with Amelie Delisle, Vice President, Petrochemical Commercial at Inter Pipeline. Inter Pipeline is the parent company to Heartland Polymers. She has spent the last 10 years seeing the vision for this plant come to life and shares its evolution with International Fiber Journal.
The facility was designed with environmental stewardship as a core value since its inception and is expected to be the lowest emitting operation of its kind.
IFJ: Tell us about the beginnings of Heartland Polymers.
Amelie Delisle: I am currently the Vice President of Petrochemical Commercial, but my role in Heartland started many years ago when we first began looking at the PDH project in late 2011, early 2012. At that time, I was working for Williams Canada, in oil and gas, and I’ve been with the project since the conception stage. It is special to be with it from very early on, so I consider myself lucky to have had that privilege; not everyone that gets that chance in their career.
The project grew organically over time. Williams was a producer of both propane and polymer grade propylene (PGP). As the only PGP producer in Canada, it gave us a unique position to identify the opportunity and to contemplate a project of this scale. Over several years, the propane project grew to also include a polypropylene plant. Initially, we looked at bringing on partners, and after the 2016 Inter Pipeline Ltd. acquisition of Williams’ natural gas-liquids businesses, we decided to pursue it ourselves.
For anyone who’s gone through acquisition, sometimes that can introduce a little bit of uncertainty – but for our project it was actually a great opportunity as Inter Pipeline stepped up and moved the project forward, including the plans for the polypropylene plant.
Fast forward to 2023, and we’re now producing polypropylene from Alberta propane.
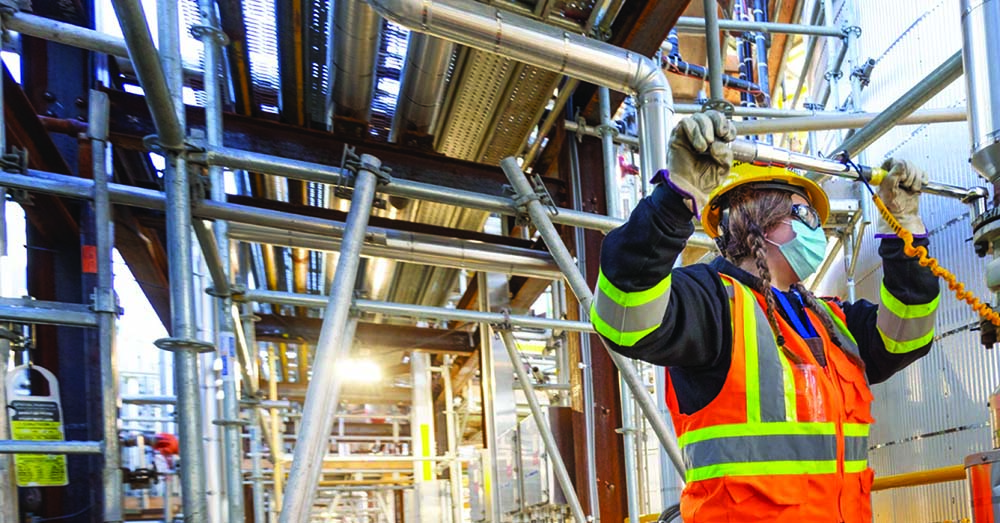
IFJ: What are some of the challenges you overcame getting to where you are today?
Delisle: This was a very exciting, but challenging, project to enter the polypropylene market. It was also a step up for Inter Pipeline, as that was not a current market for them. We identified any gaps in experience and hired qualified people to join our team to fill them.
With construction starting in 2018, another challenge that I’d be remiss not to mention is the COVID pandemic that hit at the height of our construction when we were having peak workforce at the site.
Our site is a relatively small footprint, so having thousands of people on a site while we were trying to social distance and keep everyone safe, that introduced many logistical challenges.
IFJ: Share the vision and the implementation of the sustainability aspect, such as recyclability, that is a core theme for Heartland Polymers.
Delisle: Decisions along the way from a design perspective allowed us to kind of organically get to that point of sustainability. I’ll give you a few examples. Our pellets are 35% less carbon intensive than the average North American pellet and 65% less than the international average and it is verified by an independent third-party study. We’re very proud of this.
Furthermore, our sustainability comes from three elements. The first is scale. We are a relatively large-scale plant, so that always helps on a per unit basis. Next, our power and steam are generated or produced by an on-site cogeneration plant which provides much lower carbon than other power sources or grids in the world right. And, finally, because we are co-located with our PDH plant, one of the PDH by-products is hydrogen. We use that to fuel the plant. Hydrogen is kind of the darling fuel right now as a zero-carbon fuel. I’m grateful that our team had foresight many years ago to design that into the plant, without knowing that industry would be where it is today.
Another example of sustainability is water conservation. Traditionally, plants like this use water for cooling. We made the decision very early on utilize A-frame condensers and glycol systems to minimize water consumption. Carbon gets all the attention right now, but water conservation is right behind it.
IFJ: This is only the second PP plant to come online in the last ten years. How is your plant positioned to serve your customers?
Delisle: First, I think our location provides an advantage to our customers. As you know, resin production is somewhat concentrated in North America. With Heartland being north of that base, we offer the diversity of sourcing, so if ever there is a weather event that impacts a region, typically it will not also impact our facility at the same time, offering a diversification. Also, we can provide security of feedstock. We’re an integrated plant – meaning the entire operation is based on a single-site, from feedstock to shipping – and propane is very abundant in Western Canada, especially here in Alberta, therefore we don’t foresee ever being feedstock constrained.
We were very deliberate in developing our market entry strategy, evaluating customer needs with market research, and combined with a fresh energy. We wanted to understand what customers wanted and what they were not seeing in the market and provide a continuous feedback loop in our approach to market to continue improving and evolving along with our customers.
Currently, Heartland is focused on the film and sheet extrusion sector as a point of market entry, then fibers, obviously, is one of our target markets, as well as injection molding. Those are the high-level market segments.
We offer technology to provide the customer with communication. With our new fleet, GPS is attached to each vehicle for better tracking by customers of all shipments. We have a robust customer portal to bring transparency to our customer, keeping those open lines of communication open so that they can plan for delivery.
We just announced that our PDH/PP has entered full commercial production, as the only single-site propane dehydrogenation (PDH) and polypropylene (PP) complex in North America. This sets us apart and delivers on our promise of something new and different to serve the needs of our customers.
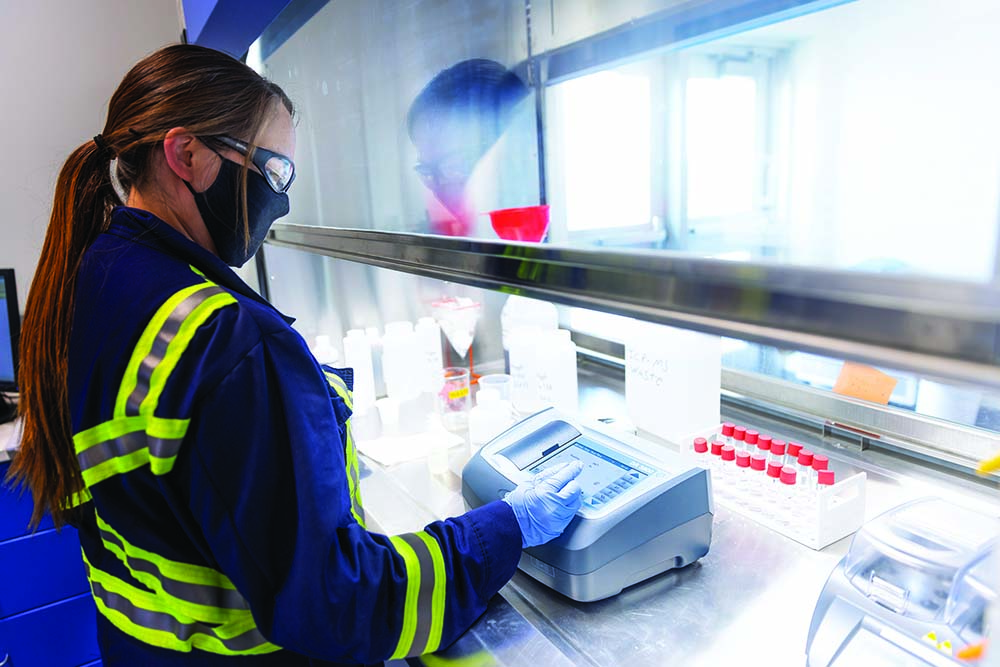
IFJ: During construction, you partnered with the Women Building Futures program. How did that work? What attracted you to this industry?
Delisle: We’re very proud of our work with their program that seeks to bring women into the trades, providing education and opportunities. It was a very successful program during construction, and we had over 25 students working and being mentored on site. We are looking at opportunities to grow more programs with WBF.
As a woman in the industry, my background is engineering and physics. Working in Canada as an engineer looking for opportunity here early- to mid-2000, the energy industry was a strong pool for engineers. I think my evolution and the fact that I stayed with the industry is what is most unique. It happened organically and I was lucky to be with Williams which had a smaller footprint in Canada and provided me great opportunities to learn. Initially, we were working on projects that recovered offgas from oil sands upgraders, and we were effectively reducing their oil carbon footprint, which was something relatively new at the time. Then, the excitement that this project brought was really what got me to stay with it and to grow alongside it in my career.
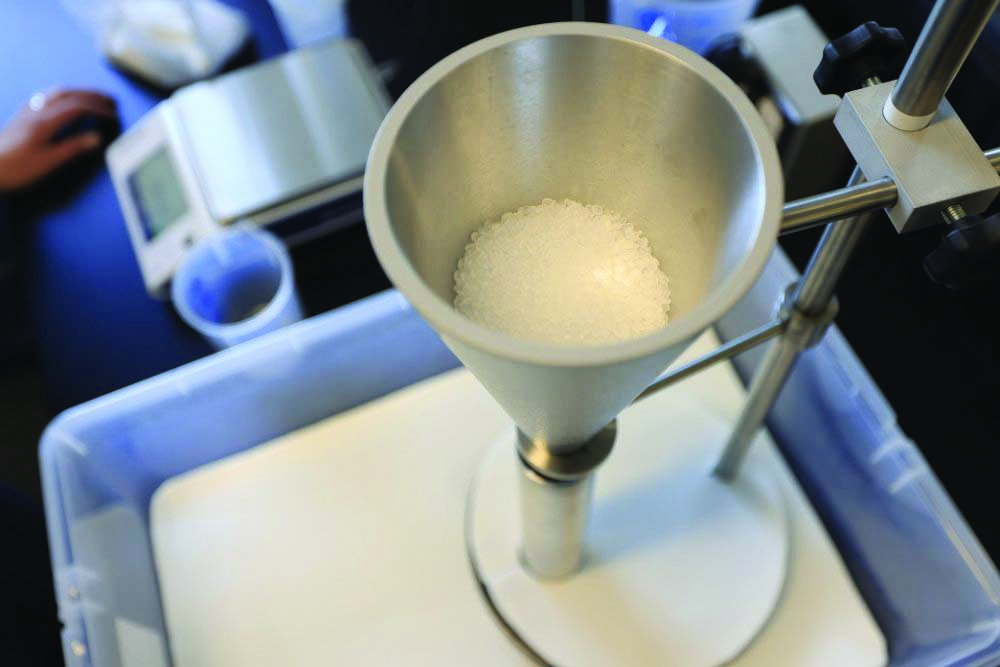
IFJ: What are Heartland’s future strategic goals?
Delisle: Heartland will continue to evolve with our customers, and to keep improving in the emissions and the sustainability space. We are also looking at a blue ammonia and blue methanol projects. The industry is talking about a lot about hydrogen, and the this project that our parent company, Inter Pipeline is evaluating would be a really a great way to bring hydrogen to market. It is another exciting opportunity. Finally, there’s also always the question to explore if we have capacity for a second PDH plant. We don’t have plans today, but it’s certainly an opportunity that we will keep a close eye on.
IFJ: How did you develop your product with recyclability in mind and providing the customer what they have come to expect from PP?
Delisle: We began by looking at the market research and the technology we selected to ensure that we could offer a wide range of products. On the recyclability side, this is evolving, and we recognize that, but we have some great partnerships in place. I’ll point to our work with Plastics Research in Action (PRIA), working with them on potential uses for plastics at the end of their lifecycle. We work to honor its Responsible Care Mandate, to “do the right thing and be seen to do the right thing.” For instance, we are working with them to help develop methodology to measure microplastics in water streams and really excited about the research and the opportunities it brings.
At this point, Heartland Polymers is really getting off the ground, we are fully open for business and we are committed to working with the customers to optimize and tailor our business to suit their needs for today and for the future.