Electrification, Lightweighting, and Sustainability Targets Are Creating Opportunities for Natural Fiber Automotive Composites
In the automotive industry, composites can help reduce aerodynamic drag, rolling resistance and vehicle weight while offering more flexibility in terms of body panel shape than traditional materials, such as metal.
But despite these advantages, the significantly higher cost of materials and manufacture of composites remains one of the biggest hurdles in replacing steel structural elements, particularly in mass-production vehicles, where cost is more important than for high-performance, low-production volume vehicles, where composites are now widely used.
In volume terms, the principal applications for automotive composites include under hood components, exterior components and interior components, such as door panels, seat backs and trunk liners, while their use in suspension components and drive shafts is also increasing.
Better Together
Composites are simply a combination of two or more materials, either natural or artificial, with different physical and chemical properties that perform better together than as individual materials.
The individual component materials do not lose their unique identities entirely: they integrate and impart their most valuable properties to enhance the final product or outcome, such as higher efficiency, strength or durability.
Polymer composites contain reinforcing agents, typically fibers, within a polymer matrix. Such fiber-reinforced composites typically incorporate synthetic fibers, such as glass or carbon fibers, and the polymer matrix is usually a thermoset resin, such as an epoxy or polyester resin, which irreversibly hardens during thermal or chemical curing.
The most widespread and well-known composite for automotive – and aerospace – applications is carbon fiber reinforced polymer.
The reduced weight of composite compared with traditional components – usually steel and aluminum, as well as injection-molded components – is a major advantage for the automotive industry.
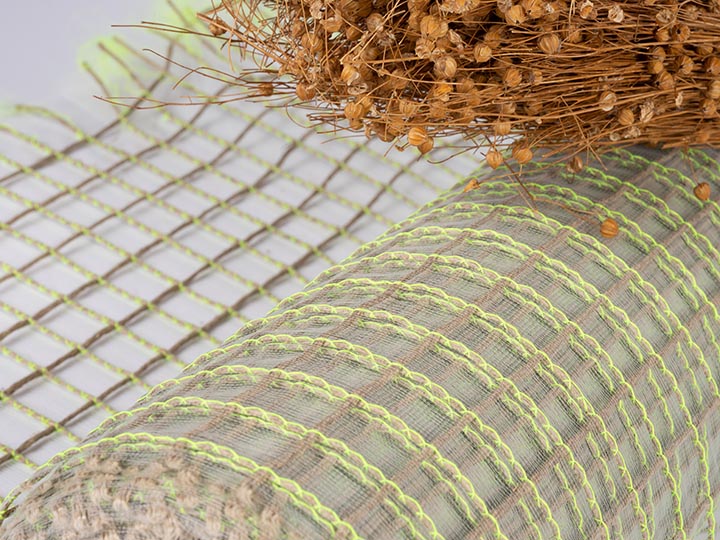
Energy Saving
Fiber-reinforced composites are generally more durable than traditional materials, are corrosion resistant, can withstand higher loads and are lighter. As a result, composites do not need to be replaced as often as components made from traditional materials – and in automotive applications they can also save energy as they are less dense than metal.
The reduced weight of composite compared with traditional components – usually steel and aluminum, as well as injection-molded components – is a major advantage for the automotive industry.
Advanced in-vehicle technology and safety features have tended to make cars heavier in recent decades, so lightweighting using advanced composites has allowed automakers to reduce overall vehicle weight and improve fuel efficiency.
Meanwhile, as the automotive industry begins to shift from internal combustion engines (ICEs) to electric powertrains, composite materials offer key advantages in terms of sustainability as well as lightweighting.
For example, batteries in battery electric vehicles are heavier than ICE vehicle batteries, which requires lightweighting elsewhere in the vehicle to maximize the vehicle’s range and efficiency.
Market Growth
The automotive composites market is forecast to grow as opportunities for lightweighting, requirements for fuel efficiency and global regulations for emissions reduction continue to drive the penetration of composites into passenger vehicles.
According to a recent study from Reports & Insights, the market was estimated to have reached a value of US$9.5 billion by the end of 2022 and is expected to hit US$16.5 billion by 2030 with a compound annual growth rate of 7% over the forecast period.
It is the low-volume, high-end vehicle and motorsports market where composite materials have seen the most gains in recent decades, particularly with the use of carbon fiber materials for high-performance, lightweight vehicles. On the other hand, the market for mid- and high-volume production vehicles, which is more cost-sensitive, has been slower to adopt composites.
Yet, a steady increase has been seen in the use of continuous glass fiber-reinforced polymers in applications such as leaf springs, as well as sheet molding compound for such applications as body panels and frames, bulk molding compound for housings and support structures, and injection-molded thermo-plastics for bumper frames, lift gates and seat structures.
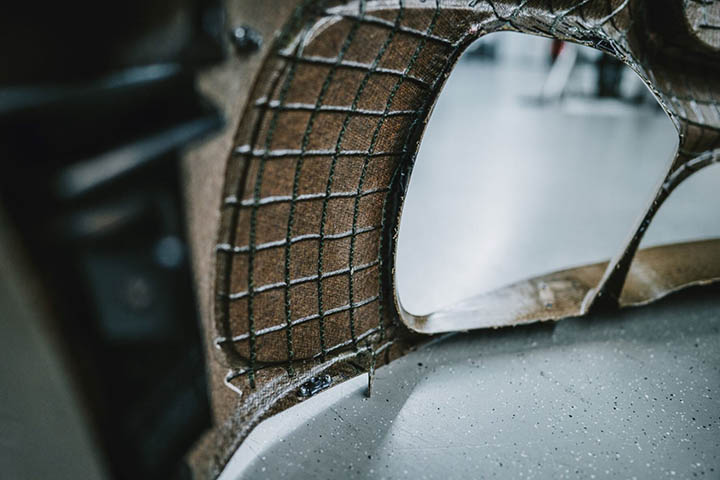
Vehicle Interior Applications
The use of natural fibers in automotive composite materials is increasing owing to new legislation and directives that are forcing automakers to reuse and recycle materials.
Eco-friendly natural fibers that are lightweight, strong and low cost have already started to replace glass fibers and mineral fillers in numerous applications in the automotive sector. Many European models now commonly use thermoplastics and natural fibers for interior and structural parts, increasingly for interior applications in mass-produced vehicles.
However, the use of natural fibers has some limitations, particularly with regard to moisture absorption and poor fiber-matrix bonding. In addition, there are concerns about durability, quality, consistency, availability and processing temperature limits.
The principal natural fibers being used in the automotive industry are bast fibers, such as flax and hemp, grown in Western Europe, and sub-tropical fibers. such as jute and kenaf; other fibers, such as banana, sisal and short wood fibers, are also being considered for specific end-uses.
The main applications of natural fiber composites in automotive interiors include door panels, seat backs and trunk liners, as well as headliners, package trays and dashboards.
Several premium automakers have begun investing in high-performance composites made from natural fibers.
Sunroof Frame
Several years ago, automotive interiors supplier International Automotive Components (IAC) launched its lightweight FiberFrame natural fiber sunroof frame on the 2017 Mercedes-Benz E-Class.
Developed with BASF, the proprietary innovation is made of 70% renewable raw material content in the form of natural fibers and provides up to 50% weight savings compared with conventional metal-reinforced sunroof frames.
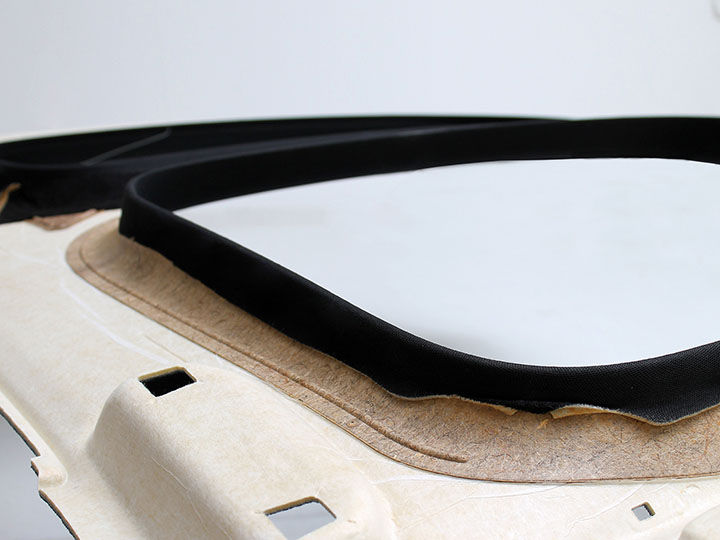
The fiber mat is molded with a thermoset binder and is manufactured in-house by IAC in a hot-molding process. The fibers are bonded together by BASF’s Acrodur 950 L binder, which ensures the loading capacity and heat resistance of the lightweight composite component. The binder is water-based and low-emission and strengthens the natural fibers.
OEM Investment
Several premium automakers have begun investing in high-performance composites made from natural fibers. Last year, several vehicle manufacturers, including BMW, Volvo and Porsche, made a CHF32.4 million investment in sustainable lightweighting specialist Bcomp.
The strategic investors comprised automotive venture capital from BMW i Ventures, Volvo Cars Tech Fund and Porsche Ventures, alongside Airbus Ventures, Generali and existing investors.
The Fribourg, Switzerland-based company’s fiber-based solutions are said to enable weight and carbon dioxide (CO2) emission reductions compared with standard materials, with applications ranging from Formula 1 and automotive, to aerospace, yachts and infrastructure.
The natural fibers used are derived from flax to form a composite made of layers of ampliTex reinforcement fabrics and powerRibs fiber reinforcement grids. The composite can be compression-molded to form automotive interior panels.
Bcomp’s calculations show that compared with regular plastic parts, the natural fiber-based composites are up to 50% lighter, use up to 70% less plastic and generate up to 60% lower CO2 emissions.
All the automotive original equipment manufacturers (OEMs) associated with the investors already have first-hand experience with Bcomp technologies.
BMW has tested and validated the ampliTex and powerRibs technologies in leading motor racing categories since 2019. Starting with the iFE.20 Formula E race car, the technologies were also used for parts of the 2020 BMW M4 DTM bodywork and include the recently announced BMW M4 GT customer racing exterior and interior. The next step is transferring the technologies and scaling their impact to road cars.
Concept Car
Volvo first worked with Bcomp in 2018 for the Volvo Ocean Race Recycled Plastics Demonstrator Vehicle, followed by its recent concept car, the Volvo Cars Concept Recharge in 2021, where it has used Bcomp’s natural fiber composites for the lower storage areas, back of the headrest and the footrest. On the exterior, they are used for the front and rear bumpers as well as the sill moldings.
Bcomp’s composites are also being used by Electric GT on its Tesla Model S P100DL racecar and by Volvo on its XC60 hybrid sport utility vehicle, while Polestar, a Swedish premium electric performance car brand jointly owned by Volvo and Geely, aims to adopt Bcomp materials for most of the interior panels of the Polestar 5, the production evolution of the Polestar Precept, which is expected to be launched in 2024.
Meanwhile, Porsche worked with Bcomp to develop the first natural fiber composite motorsport door in 2019, with the project being listed as a finalist in the JEC Innovation Awards.
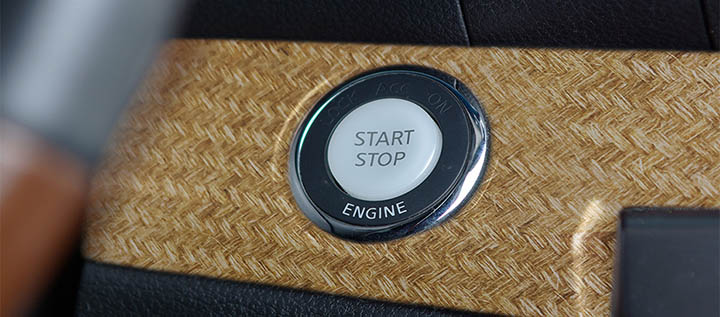
Porsche Motorsport then used ampliTex and powerRibs in the production of both exterior and interior vehicle components for the Cayman 718 GT4 CS MR, culminating in the launch of Porsche’s fully electric Mission R concept car in 2021.
Many of the Mission R’s add-on parts are made using Bcomp’s natural fiber reinforced plastic. The material can be seen on the car’s exterior, such as the front splitter, the doors, the side skirts and the diffuser.
Bcomp is now supplying its natural fiber technologies to HWA, a development partner of German automaker Mercedes-AMG, for the new front bumpers on Mercedes-AMG GT4 race cars.
Bcomp’s bodywork solutions will provide a sustainable alternative to the GT4’s existing carbon fiber panels, offering equivalent mechanical performance in stiffness and weight and improving safety.
Motorsport Partnership
As well as investment, BMW and Bcomp are strengthening their partnership on the motorsport side, with the Swiss company now an official BMW M Motorsport partner with the new BMW M4 GT4 racing car.
BMW Group Research and Bcomp are also setting up a development collaboration with the aim of using a higher proportion of renewable raw materials for components in future vehicle models, with the German OEM aiming to lower its vehicles’ lifecycle carbon emissions by more than 40% by 2030 compared with 2019 levels.
Using renewable raw materials and natural fibers, such as hemp, kenaf or flax, which are particularly well suited to use in visible and paneling parts in vehicle interiors, will minimize material usage while also achieving a weight reduction of up to 50% over conventional materials.
This in turn will help lower the energy consumption of the vehicles in which they are used. As an added benefit, the natural materials will bring down the calculated CO2 figure, as the original plants absorbed CO2 while growing and released oxygen.
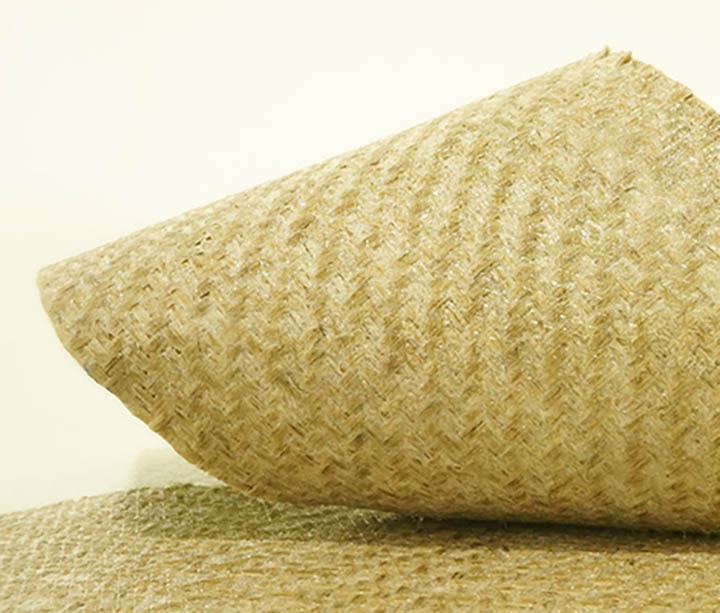
Recycling Challenge
The irreversible setting of molecular bonds on a nano level after molding means that recycling is hugely challenging for composites. In addition, the use of fillers and additives that provide additional properties or sensor elements enabling multi-functionality further increases the difficulty of separation of the individual components.
This will become even more important as various end-of-life regulations come into force for the collection, sorting and component separation of consumer products. As well as recycling, which may not be cost effective, this may require the implementation of circular economy practices, such as the refurbishment, reuse and repair of components, being considered from the start of the design phase for automotive composites.
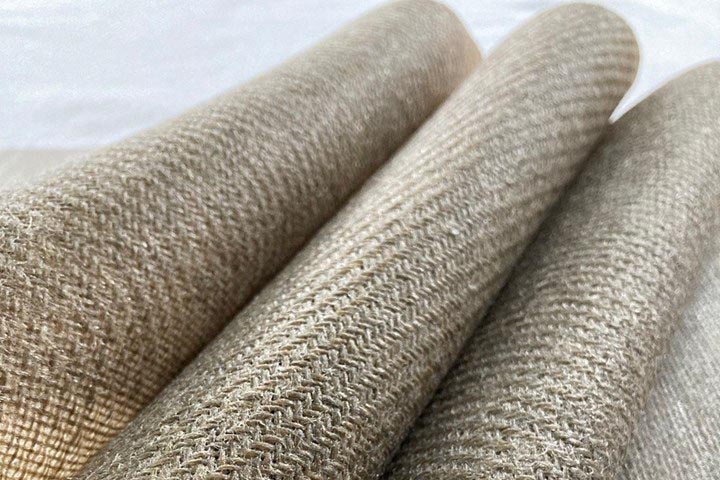
Green Composites
Most of the so-called green composites available on the market today are either a hybrid of natural fibers with petroleum-based resins or synthetic fibers with bio-resins – “all-green” composites made from 100% biomaterial (i.e., natural fibers with bio-resins) have so far achieved limited success owing to issues of cost, adhesion and durability.
In an industry in which mass-manufacture is still largely metal-based, the use of natural fibers as reinforcement in thermoplastic or thermoset automotive composites will undoubtedly continue to grow rapidly and extensively.
However, questions remain over their future availability, and more particularly about the ability of producers to meet demand, especially in a rising market, where electrification and sustainability targets will dominate future thinking.