Calcium carbonate, which is ubiquitous in nature, can be found everywhere in daily life. It is used widely as a coating agent for paper or cardboards and for paints; as an additive in food pharma and cosmetics; as a soil fertilizer in agriculture; for water remineralization; for flue gas desulfurization; and many other applications.
In plastics, the first applications date back to the 1950s when Omya first introduced surface-coated calcium carbonate for PVC applications. Since then, the mineral has played an integral part in many formulations for wire and cables, pipes, conduits and profiles. Later on, other polymers, such as PS, UP, PUR, PA, ABS and PET, were established.
Polyolefins reflect a major part of calcium carbonate applications. Sheets for thermoforming, PP raffia tapes and injection-molded articles typically contain up to 40% of the mineral. Shopping bags are loaded with 5% to 30% calcium carbonate.
The improved performance with calcium carbonate is used to downgauge film thickness. BOPP (Biaxially Oriented Polypropylene) films take advantage of the cavitation functionality of carbonate particles. The voids created with 7% to 25% calcium carbonate particles help to reduce the density to 0.5 g/cm3 and boost the opacity of the films. If the addition rate of calcium carbonate is increased further to 40% to 60%, an open cell structure can be achieved. This effect is used to produce breathable hygiene films for diapers and other applications. The membrane function is characterized by a high water-vapor transmission rate in combination with a good water column, even for very thin films down to 8 g/m².
Such demanding applications require specific properties of the calcium carbonate powder. It is therefore essential to develop tailor made solutions to fulfill the specific requirements of these markets. In the case of extruded polymer fibers, factors such as processing temperature, polymer composition, die build up and post extrusion processing must be considered. Recent developments have demonstrated that it is possible to produce calcium carbonate grades, which perform well under these restrictions.
Calcium carbonate for fibers & nonwovens
A good example of addressing the challenging requirements in fiber applications is the development of the new calcium carbonate for PP spunmelt and dry-laid fibers. This product is specifically designed to provide an attractive solution, which creates value for the PP nonwovens industry. It is a natural, very pure and fine ground calcium carbonate. The particle size and the particle size distribution are tailored to achieve outstanding processability and fiber properties. A new, improved proprietary surface treatment is applied to the carbonate to achieve excellent dispersion of the mineral particles in the polymer matrix while allowing enhanced processability and optimized compatibility. The product is food contact-approved according to U.S. Food and Drug Administration and European Union regulations.
To successfully apply the new product, the whole value chain has to be considered. Calcium carbonate is produced by grinding calcium carbonate mineral into a fine powder. To apply this mineral to PP nonwovens, a masterbatch concentrate has to be produced in an intermediate compounding step. To ensure good processability and product quality, the compounding technology needs to provide excellent dispersion of the mineral.
Omya recommends compounding 70% calcium carbonate in the appropriate PP resin. Dispersion quality can be checked with a filter pressure test at 25 µm sieve. To dilute the masterbatch concentrate pellets in the nonwoven, it must be mixed with virgin PP and fed to the nonwoven process (Figure 1). A typical formulation may contain around 14% masterbatch with calcium carbonate. Depending on the optical requirements, 2% of color masterbatch may be added. The PP is typically a homopolymer with a melt flow of 25 to 35 g/10 min at 230°C and 2.16 kg.
To establish the value proposition of calcium carbonate, extensive technical evaluations have
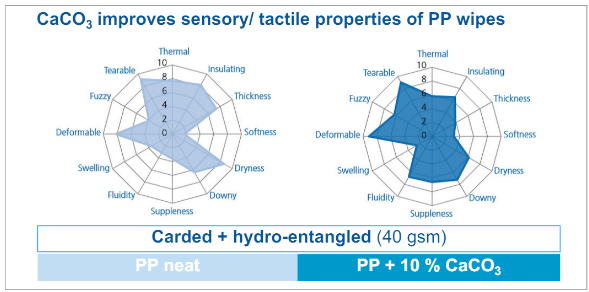
been done with well-known research institutes. Processing trials have been done on a Hills nonwoven line at the European Centre of Innovative Textiles (CETI) in Tourcoing, France. Further trials on a Reicofil 4 line have been conducted at the Sächsische Textilforschungsinstitut (STFI) in Chemnitz, Germany.
The successful trials were essential to ensure the processability of calcium carbonate on industrial lines. The trials were conducted with different technologies. Spunlaid nonwovens have been produced with thermal calendering. Further trials with spunlacing or hydroentanglement have been conducted. Also, trials with staple fibers, which were carded and hydroentangled, have been completed. In all trials, 10% calcium carbonate (Omyafiber 800 from Omya AG, Switzerland) was incorporated in the nonwovens via the addition of 14% masterbatch.
The trials could demonstrate that calcium carbonate caused no die build-up at the spinneret nor any extrusion pressure evolution during processing. The processes ran stable without any fiber breakage. The evaluations helped to establish the know-how to optimize the process. Essential is an adequate purging step and an adjustment of the product parameters to optimize the nonwoven performance.
Calcium carbonate provides value that pays off. Raw material savings are substantial. But not only costs are attractive. In spunlace and carded fabrics it creates natural cotton like haptics and softness. The tactile properties of PP carded wipes were evaluated by a sensory panel at the renowned French institute IFTH according ISO 13299. The results of the improved tactile properties of PP carded wipes are shown in Figure 2, where carded PP wipes with and without Calcium Carbonate are compared. At high and low grammage fabrics it improves tensile strength and elongation. The higher whiteness with calcium carbonate allows substantial savings in titanium dioxide (TiO2) and provides a matt aspect (Figure 3).

Calcium carbonate drives sustainability
The fiber and nonwoven industries – like many that are heavily dependent on plastics – have been working to decrease the environmental impact of its production and products. The major players in the industry have all adopted goals to reduce the environmental footprint of their products through multiple approaches encompassing the entire production/use/end-of-lifecycle.
Common metrics include:
- Impact of the raw materials on the Global Warming Potential (GWP) of the product
- Ability to recycle post-industrial or post-consumer waste
- Increasing the use of “natural” and “renewable” materials
- Reduction in the use of resin
There may be additional factors depending on the composition of the article. For instance, manufacturers utilizing biopolymers may wish to measure compostability, but these are less common.
Therefore, a reasonable question is how do additives – in this case ground calcium carbonate – impact the above metrics?
In brief, calcium carbonate is beneficial from a sustainability perspective as it has a substantially lower carbon footprint than PP resin¹,² and improves the emissions profile, while also displacing resin. In addition, ground calcium carbonate is a natural and, as we will explain, a renewable raw material,³ which is also compatible with common recycling processes.
According to the numbers given by the Plastics Division of the American Chemical Society, the production of PP causes the emission of the equivalent of 1860 kg CO2 per ton of resin¹. Therefore the carbon footprint of fiber grade calcium carbonate is 84% lower than that of neat PP.
Since calcium carbonate is a naturally occurring mineral, it does not involve any energy consuming chemical reaction. Therefore, the carbon footprint is substantially lower than any synthetic polymer. To establish sound numbers for lifecycle analysis studies the IMA, an industrial mineral organization in Europe, has initiated an independent evaluation of the emissions needed to produce calcium carbonate grades for industries like plastic processing. The calculation is based on the European EU27 energy mix. One important parameter in lifecycle analysis is the CO2 emissions or carbon footprint, which is dependent upon the specific grade of calcium carbonate. For coated and fine ground calcium carbonates like those used in polyolefin applications, the CO2 emission to produce 1 ton of calcium carbonate is only 300 kg.²
This is much lower than the carbon footprint of PP resin used for the nonwoven production. According to the numbers given by the Plastics Division of the American Chemistry Council,¹ the production of PP causes the emission of the equivalent of 1860 kg CO2 per ton of resin. Therefore, the carbon footprint of fiber grade calcium carbonate is 84% lower than that of neat PP. In other oil-based polymers, the benefits due to the addition of calcium carbonate will be similar.
An additional material commonly used in nonwoven production is TiO2. Used at relatively low levels (0.1% to 3%), TiO2 has a calculated GHG equivalent footprint of 5300 kg CO2 per ton of TiO2.⁴ This is a factor of 17.6 higher than calcium carbonate. As mentioned before, calcium carbonate can provide an at least partial replacement of TiO2 in nonwovens formulation, and thus can add value to increasing sustainability in that fashion.
Approximately 4% of the Earth’s crust consists of calcium carbonate, making calcium carbonate one of the most common raw materials available in nature. Calcium carbonate is ubiquitous in nature and is continuously replenished by means of natural cycles in rivers, lakes & oceans, or formed as minerals in the form of shells, skeletons, stalactites and stalagmites. Commercial grades of calcium carbonate are produced from natural sources, such as limestone, chalk, or marble, which are widely available around the world.
The results of two recent independent university studies conclude that the annual replenishment of calcium carbonate varies from 8.8 to 14.5 billion tons/year in different environments. The annual consumption of calcium carbonate in various markets being in a range of 4.5 Billion t/year, the replenishment rate (according to the ISO 14021 definition) exceeds the consumption rate. Therefore, calcium carbonate meets the criteria for a renewable material.³
Thus, we can conclude that, calcium carbonate is a bio-mineralized or naturally produced resource, which is constantly renewed by various natural processes, ensuring that reserves are available for many future generations.
Recycling factor
While we are unaware of any studies focused on the recyclability of PP nonwovens containing calcium carbonate, it is an established fact that polyolefin articles containing calcium carbonate have been part of the plastics stream for decades. When the density impact of calcium carbonate is accounted for in the separation process, resins containing this mineral can be melted, mixed with other resin sources and re-extruded with no particular loss of performance. In fact, it even helps mixing different fractions and by that improves homogeneity. Logically the same would be true for PP nonwovens containing calcium carbonate.
In summary
Using the LCA numbers described above, a simple calculation can demonstrate the impact of calcium carbonate addition on the GWP of a PP nonwoven. At a recommended addition level of 10%, calcium carbonate will reduce the equivalent CO2 contribution of a nonwoven by 8.5%, assuming a contribution of 300 kg/MT for calcium carbonate and 1850 kg/MT for polypropylene.
In the same fashion, resin usage is reduced by 10%, equivalent to the amount of mineral added, when basis weight is held constant (Figure 4).
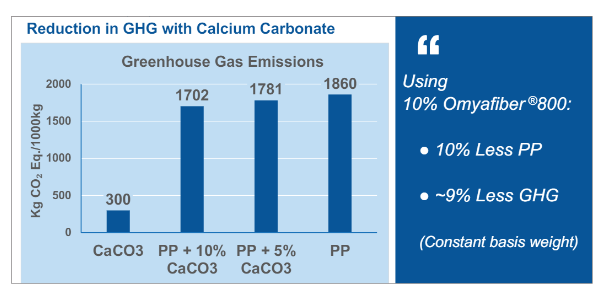
Parting thoughts
Further process costs can be saved during fiber processing. Increased thermal conductivity with calcium carbonate lowers the temperature window for optimal bonding by 5°C to 10°C. This results in energy savings during nonwoven production. The magnitude of these savings is highly dependent on the specifics of the production line and operating conditions and is beyond the scope of this paper.
Calcium carbonate is a naturally occurring and renewable mineral. It provides value to polypropylene nonwovens. By replacing 10% polypropylene with calcium carbonate, the equivalent CO2 emissions can be reduced by 8.5%. Main benefits are the improved sustainability, opacity, haptic properties, and cost savings.
NOTE: This development was done by Omya. Omya is a global producer of calcium carbonate for industrial applications. It is a privately owned Swiss company with more than 175 plants and own mineral deposits around the world. Omya implements sustainable business principles throughout the entire organization. More detailed technical results are available from Omya for further discussion.
References
1. Franklin Associates, a Division of Eastern Research Group, Inc. ”Revised Final Report: Cradle-to-Gate Life Cycle Inventory of Nine Plastic Resins and Four Polyurethane Precursors Prepared for the Plastics Division of the American Chemistry Council,” August 2011, https://plastics.americanchemistry.com/LifeCycle-Inventory-of-9-Plastics-Resins-and-4-Polyurethane-Precursors-Rpt-Only/
2. Sustainable Solutions, Inc, ”IMA-NA Calcium Carbonate Life Cycle Assessment”, 2016, https://cdn.ymaws.com/www.ima-na.org/resource/dynamic/blogs/20171019_170108_21129.pdf
3. Calcium Carbonate Association – Europe, ”Calcium Carbonate is a Renewable Raw Material,” 2016, https://www.ima-europe.eu/sites/ima-europe.eu/files/publications/Renewability%20Statement.pdf
4. Titanium Dioxide Manufacturers Association, “The Carbon Footprint of Titanium Dioxide Pigment,” 2013, https://tdma.info/life-cycle-inventory/ (for most up to date results).