The popular phrase “hanging by a thread” really means something in yarn applications for protective wear, as well as in medical, automotive and aviation. Manmade fibers for these sectors have to fit specifications precisely, to be on the safe side for both producers and end-users – and Retech develops godet rolls as the key manufacturing components to ensure standards are met. These threads – some literally life-saving – are made of polyamide, polyester, polypropylene, aramid, carbon, bio-based and many other polymers, categorized as technical yarns and high-performance fibers.
Retech, backed by 45 years of experience in heat treatment and drawing manmade fibers of any material, recently launched two innovative godet rolls – the Ø 250 mm model developed for technical yarns and the Ø 320 mm model for temperature conditions needed for high-performance fibers such as aramids.
Technology advantages
“Retech as the market leader for heated godets to draw fibers to perfection has outstanding technology in heating the rolls by induction,” said Ralph von Arx, CEO, Retech AG. “Over the recent years we further developed our system to reach highest temperatures and to achieve long life-time of the equipment.”
Key advantages of Retech’s technology include:
- Working with standard net frequency 50/60 Hz, which is a big advantage for the yarn producer as there is no additional and expensive equipment needed to create middle or high frequency.
- To heat and conserve heat on the right spots, while minimizing temperature transfer to bearings, ensures efficiency. Or, in other words, to deal with the energy losses in the right way and to take advantage of them is a key attribute of Retech‘s godet technology.
- As Retech puts all of its effort into the optimization and further development of heated godets, the company is leveraging the newest and most modern technology. Not only the heating, but also the entire control system is state-of-the-art. Temperature transmission systems, as well as temperature controllers, have been implemented to provide Industry 4.0 and and data analysis for trouble-free and foresighted technological equipment that is future-proof. Meanwhile, safety features help to extend the service life and provide information about the current condition of bearings and induction heaters.
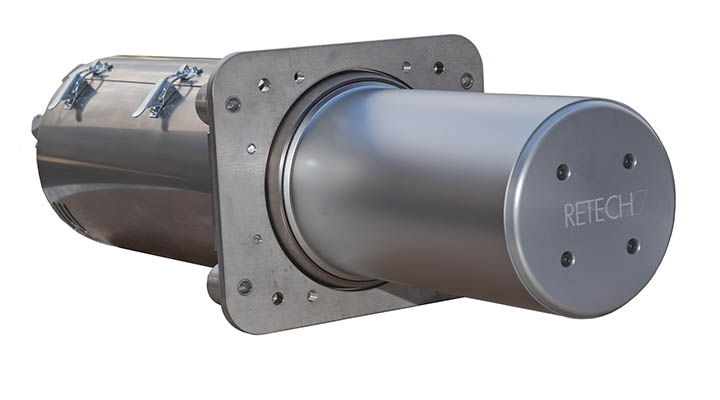
High-tech for a secretive business
Yarn engineering is a secretive business when it comes to sensitive applications, as well as future developments. Customers build on Retech expertise and trust its wide range of key components in perfectly meeting requirements such as temperature, speed and torque. But only in rare cases does the customer provide any information about the yarn and its final characteristics.
“Comparing required customized solutions shows us trends regarding the market demand for godet rolls. It becomes our ambition to innovate the one godet roll meeting these latest customer needs,” said Ralph von Arx, CEO, Retech AG.
Identifying a strong demand for technical yarns with maximum strength, Retech addressed this with the newly launched type Ø 250 mm roll, with an ideal length of 420 mm to process eight or twelve threads at a time. The extended diameter of 250 mm allows a significantly higher speed with the same dwell time. Additionally, the higher motor torque guarantees the very best results in yarn tenacity. Speed can be ramped up to 6500 m/min – applying a torque value of 15 Nm through the full speed range – and the temperature reaches 250 C with a temperature profile of +/- 1.5 C over the whole working width of the godet roll.
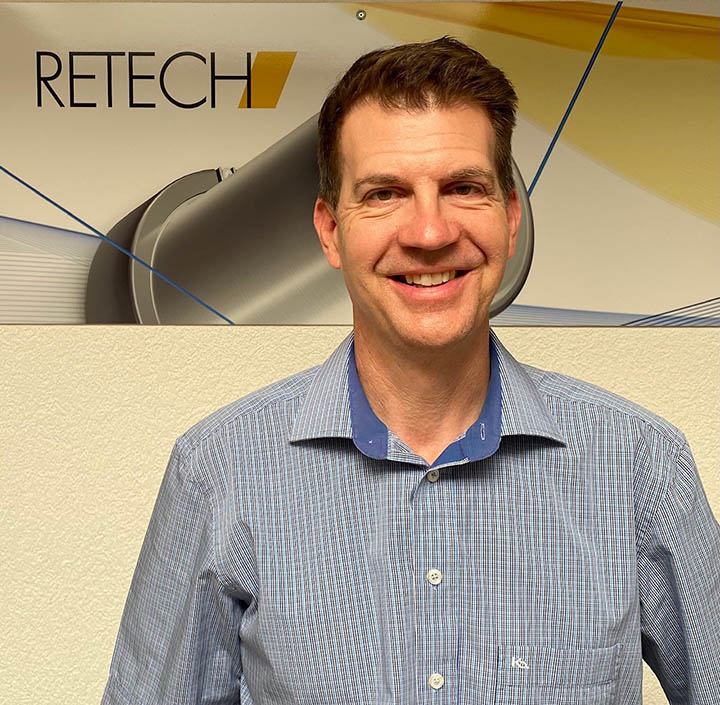
When comparing its performance with the popular Ø 220 series, the Ø 250 provides added speed and torque, making it possible to process a much wider range of yarn counts.
Reaching to the limits of strength boundaries
Retech has built a strong reputation for using technology to enable a larger diameter and the required heating capacity within limited space. Results have been excellent, and successful projects also tend to lift expectations even further. “We continuously touch today’s technical limits and stretch to tomorrow’s possibilities when developing. We take the risk, and try to optimize at the edge,” said von Arx. The new type Ø 320 mm, specially developed for high-performance fibers, has become Retech’s latest pride, and evidence of its efforts to support today’s yarn engineering ideas.
Featuring various length, this type is ideal for serpentine yarn paths to multi-enlacement and suits practically all machine concepts and yarn paths. For high-performance fibers, it is essential to optimize heat entry into the yarn, so the first step must be to extend the dwell time, which in turn is influenced by speed and diameter. The top diameter of Ø 320 mm allows the number of revolutions per minute to be reduced, resulting in optimum dwell time – while taking the advantage of an enlarged contact area. Unique yarn characteristics are made possible by temperatures up to 400 C, along with torque values of 35 Nm and speeds up to 1500 m/min.
Aramids are the strongest textile fibers, with para-aramids having high glass transition temperatures nearing 370 C. Heat treatment under tension increases crystalline orientation for unique tension values – all perfected when mechanical drawing orients the polymer chains in the fiber direction. For two reasons, the Ø 320 mm model is the ideal godet to produce sophisticated products such as aramids: (1) it meets technical requirements for heat, torque and speed; and (2) it performs at the required precision. Retech’s reliability in use is founded on precise temperature measurements and adjustments – a major aspect of the company’s continuous developments.
Until the ultimate
Committed to constant innovation and improvement, Retech engineers have already worked on perfecting the new generation of temperature transmitters. Changes in the temperature control of the individual induction heater zones have improved power input and load distribution. More uniform power input into the inductor reduces the pulsation of the induction heat and prolongs the lifetime of the induction heater itself, as well as of the motor bearings.
The smooth-running high-precision drives become even smoother, which brings significant advantages. For example, monofilament, producers are able to make yarn of finest titer without the slightest variation in diameter. Last but not least, the changes additionally have a positive effect on the power grid, making its utilization more even, with fewer peaks, and facilitating a more balanced running of the mill’s system load.
The culture of ongoing enhancement and the desire for perfection make Retech a reliable partner when it comes to yarns for challenging – and especially life-saving – applications. “Producers can rely on us. We never stop until we can draw our customer’s fibers to perfection,” said von Arx.