Lenzing’s nature-based innovation is witnessed in both product and process as the company progressively meets the demands of the textile industry. In product, Lenzing provides specialty fibers of stringent quality in the known brands of TENCEL™, Lenzing ECOVERO™, VEOCEL™ and LENZING™. Together, the fibers of these brands form the basis for a variety of textile and nonwoven applications in fashion, home goods, hygiene, as well as industrial applications such as automotive and protective wear. In process, Lenzing advances circularity by following a business strategy with a strong focus on raw material security, water stewardship and sustainable innovations, and other initiatives.
In fact, they have established an ambitious goal to halve carbon emissions per tonne of product by 50 percent by 2030 and achieve carbon-neutral production by 2050, both targets recognized by the Science Based Targets Initiative[i]. They are almost a quarter of the way there, achieving 18% reduction of specific greenhouse gas emissions as of 2022. Yet, carbon emissions are just one part of the environmental Lenzing story.
Environmental Action
Lenzing dedicates significant resources to accelerating circularity with the development of innovative ideas, as they continually evaluate the entire value chain of their process and production – from wood to fiber. It’s been recognized that within the value chain, the garment dyeing process is among the most pressing of environmental concerns. After all, 20% of the earth’s available fresh water is used in industry, with the fashion textiles being a major culprit. Demin in particular, as discussed on fiberjournal.com, is a real challenge for textile producers.
“Efficient use and processing of all raw materials is essential to safeguard the environment,” says Rex Mok, Vice President of Fiber Technical Marketing and Development at Lenzing. “By adopting circular business models, we have made progress in countering the wastefulness of the textile business. Our latest advancement is a new approach that not only delivers the desired wash-down aesthetics previously reliant on resource-intensive denim dyeing and bleaching but also significantly curbs water and energy usage. Here again, we prove to our customers that we are invested in their sustainability journey, too.”
Furthermore, according to other research:
- CNN cites: Every year, the textile industry uses 1.3 trillion gallons of water to dye garments – enough to fill 2 million Olympic-sized swimming pools. Most of this water, loaded with harmful chemicals and dyes, flows untreated into rivers and streams.
- Another study shows that up to 200,000 tons of dyes are lost to effluents every year during the dyeing and finishing processes.
In addition to denim, achieving greater design possibilities for knit apparel, as well, is the focus of Lenzing’s most recent breakthrough with their new approach to conserve water and energy consumption and reduce waste.
With just one round of dyeing, this new Lenzing approach encompasses yarn pre-treatment and specific knitting structures and patterns, reducing the need for multiple washes in traditional dyeing.
How it Works
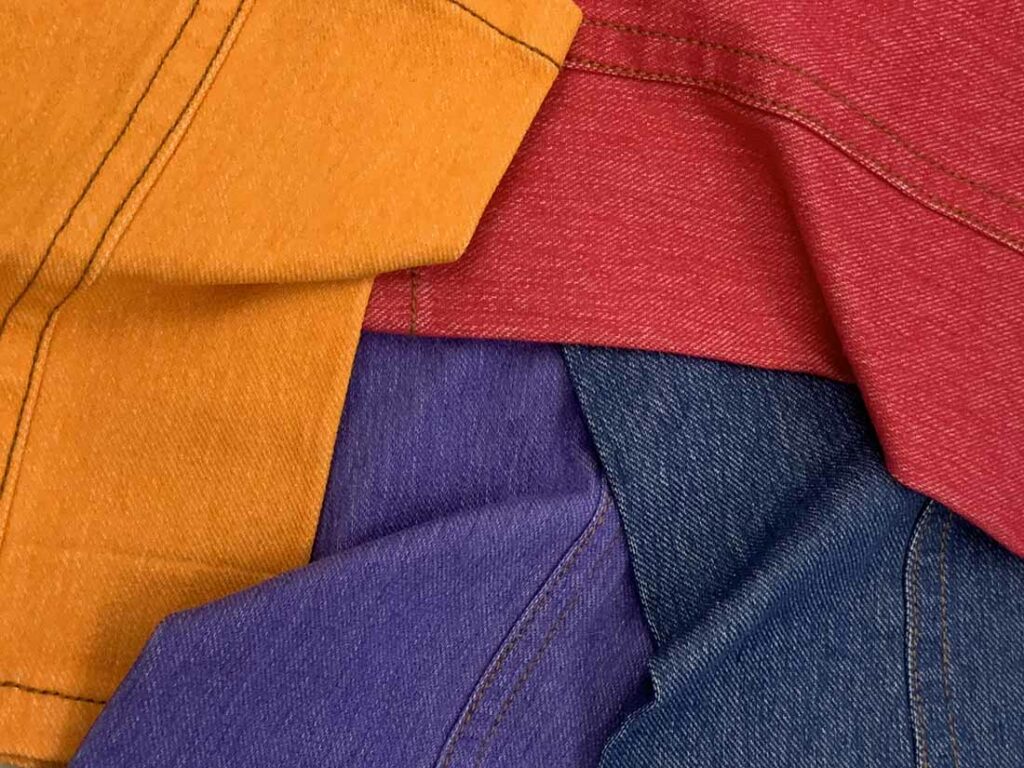
Lenzing understands fashion brands and consumers want access to current textile trends, like wash-down aesthetics, which is a water intensive dyeing process. Just announced, the company has now pivoted to a new way of producing dyed ready-to-wear denim and knit garments with wash-down aesthetics – reducing water in the process. With just one round of dyeing, this new Lenzing approach encompasses yarn pre-treatment and specific knitting structures and patterns, reducing the need for multiple washes in traditional dyeing. This helps reduce water, energy, and chemical usage by up to 50%, 40% and 90% respectively[ii], and illustrated Lenzing’s unwavering efforts to optimize the use of raw materials in the textile industry.
Water preservation is now an inherent ecological achievement for Lenzing’s customers who leverage the specialty fibers made from the renewable raw material wood, which are grown in sustainably managed forests and plantations. Customers can be confident on Lenzing fiber applications and processes that meet their growing needs for saving resources and growing their sustainable story. The new approach to dyeing textiles is just one more way Lenzing delivers values to its partners and manages a closed loops for process chemicals and water.
Confidence in Applications
The advantages of this new approach are worthy of consideration. In response to customers’ increasing desire for earth-friendly options, the new way of achieving dyed ready-to-wear and knit garments utilizing less water in the process can be applied to both TENCEL™ Lyocell or TENCEL™ Lyocell with REFIBRA™ technology, and it can even be customized to achieve multiple shades of color, wash-down and fade-out effects. With access to greater design possibilities for knit apparel and denim looking garments, customers can be confident in Lenzing to deliver quality fibers, while also helping companies attain their own ESG goals into their brand story.
Furthermore, there is no extra cost to change any production processes for textile manufacturers, making it a cost-effective solution for brands who want to increase their environmental responsibility credentials. The new way of dyeing complements the existing production processes used by yarn makers and fabric mills, allowing for enhanced production efficiency and sustainability, without any prohibitive infrastructure costs. The best news is, it can enhance energy efficiency in the production process, thereby potentially saving money.
“With this new approach, we are driving the industry towards circularity by introducing an eco-efficient alternative to achieve a diverse range of color shades in ready-to-wear, knit apparel and denim-looking garments,” said Mok. “So far, the initial response we’ve received from value chain partners has been positive and we will be continuing to work with mill partners to drive its wider adoption and explore new applications within the textile value chain.”
[i] Lenzing is first wood-based fiber producer with approved science-based targets, Lenzing, 2019
[ii] ECOFAST™ Pure Sustainable Textile Treatment Application Manual, DOW, 2022