In the dynamic and global textile fiber industry with its various manufacturing processes and end-uses, news and information is breaking on a daily basis. International Fiber Journal is tracking stories relevant to our industry from manmade to natural to bio-based fibers, innovations in nonwoven, woven, braided and technical textiles, technologies for additives, bonding, coatings and polymers, and applications from apparel to hygiene to transportation, and more. Here we will post news stories relevant to textile fibers and their downstream applications on an ongoing basis. Please check back for regular updates. If you have news that you feel should be added to this summary report, please email it to Matt Migliore at mmigliore@inda.media.
Most recent update: April 29, 2021
Berry Global enters agreement with Borealis for access to circular polyolefins
Berry Global has entered an agreement with Borealis, a leading supplier of polyolefin solutions, for access to its first volumes of the in-demand circular polyolefins made from chemical recycling. This announcement adds to Berry’s access to the 600 million pounds of post-consumer recycled (PCR) content by 2025, allowing Berry to further support customers with circular polyolefins.
“Investments in chemical recycling with partners like Borealis are critical to Berry and our customers as we collaborate across the value chain to solve the global commitment achieving net-zero emissions by 2050,” said Jean-Marc Galvez, president of Berry’s Consumer Packaging International Division. “Plastics are a critical solution as we advance toward circularity. As the preferred substrate for its lower greenhouse gas emissions, Berry’s design expertise with circular resins is an important factor in the journey to demonstrate the value of giving plastic multiple lives.”
Berry will use the polypropylene from chemical recycling to manufacture food packaging for longtime global brand owners, creating a package made exclusively from resins made from chemical recycling. A preferred substrate for food, plastic provides high levels of product protection, while also being increasingly recycled. The package will be manufactured at one of Berry’s existing European manufacturing facilities and will launch in the upcoming quarter.
Source: berryglobal.com
BASF reports strong Q1 2021 results
BASF increased sales by €2.6 billion in Q1 2021 compared with the first quarter of 2020 to €19.4 billion. This was mainly due to higher prices and volume growth, according to the company.
Compared with the same quarter of the prior year, income from operations (EBIT) before special items rose by 42 percent to €2.3 billion. This was primarily attributable to considerably higher earnings contributions from the Materials and Chemicals segments. The Surface Technologies segment also recorded considerable earnings growth thanks to the recovery in automotive production. All regions contributed to the considerable increase in the BASF Group’s earnings in the first quarter of 2021.
EBIT rose by €855 million compared with the first quarter of 2020 to €2.3 billion. Income from operations before depreciation, amortization and special items (EBITDA before special items) increased by €602 million to €3.2 billion and EBITDA rose by €748 million to €3.2 billion in the same period.
“We were able to carry over the tailwinds from the strong fourth quarter of 2020 into the first quarter of 2021,” said Dr. Martin Brudermüller, Chairman of the Board of Executive Directors of BASF, expressing one of the core messages to shareholders at this year’s virtual Annual Shareholders’ Meeting. “BASF had a strong start to the year 2021.”
The Board of Executive Directors and the Supervisory Board propose to the Annual Shareholders’ Meeting of BASF SE a dividend of €3.30 per share for the 2020 business year. This is equal to the dividend per share paid for the 2019 business year. If this dividend proposal is accepted, around €3 billion will be paid out to shareholders on May 4, 2021.
Read the full story on BASF Q1 financials: https://www.basf.com/global/en/media/news-releases/2021/04/p-21-184.html
Source: basf.com
Don Rusch named director of Textile Technology Center at Gaston College
Don Rusch has been appointed as the new Director of the Textile Technology Center (TTC) at Gaston College. Rusch will oversee all day-to-day aspects of the TTC and will be working with the new Manufacturing and Textile Innovation Network (MTIN), a network that partners Catawba Valley Community College’s Manufacturing Solutions Center (MSC) with Gaston College’s Textile Technology Center. He will oversee 25 employees at the Textile Technology Center.
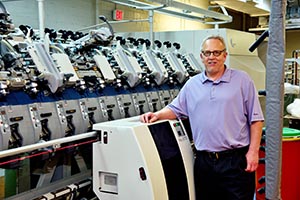
“I am truly excited and grateful for the opportunity to serve Gaston College and Textile Technology Center. In my new leadership role, I look forward to working with industry partner’s and clients as we continue to focus on key areas of growth and innovation for the state and region,” said Rusch.
A graduate of the North Carolina State University Wilson College of Textiles, Rusch has a vast array of experience from Fiber Science, Process & Product Development, Technical Services and Operational Management with companies such as Eastman-Kodak, Springs Industries and Beal Manufacturing. He has also worked extensively in the Product Development Labs at the TTC.
For more information on the Textile Technology Center at Gaston College, visit https://www.gaston.edu/textile-technology-center/ and for more information on the Manufacturing and Textile Innovation Network (MTIN), visit www.mtinusa.com.
Source: gaston.edu
Arkema says it will start new bio-based polyamide 11 plant in Singapore first half of 2022
Announced in 2017, Arkema says it is on track to deliver its new bio-based polyamide 11 plant in Singapore by first half of 2022. When complete, the plant will represent the biggest integrated bio-factory in the world dedicated to high-performance polymers, according to Arkema. It represents a 50% increase in global polyamide 11 capacity for the company.
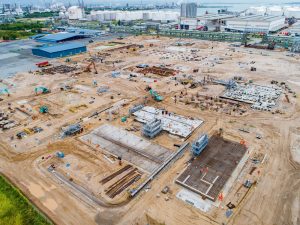
The total investment in the region, which also includes downstream polymer capacities in China, is approximately €450 million. To finance this new plant in Singapore, Arkema successfully placed its first ever green bond in October 2020, for a total amount of €300 million.
This investment supports strong growth in demand for advanced bio-circular materials. Rilsan polyamide 11 is recognized worldwide for its superior properties and performance in very demanding applications, significantly contributing to the development of sustainable solutions in fast-growing sectors, such as new energy vehicles, 3D printing, as well as consumer goods, electronics, sports and lifestyle markets.
Source: arkema.com
Lenzing Group publishes Sustainability Report 2020
The Lenzing Group presented its Sustainability Report 2020 on World Earth Day. Featuring the title “Stand up for future generations,” Lenzing emphasized its commitment to taking responsibility beyond the products it makes. The non-financial report, prepared in accordance with the reporting standards of the Global Reporting Initiative (GRI) and the Austrian Sustainability and Diversity Improvement Act (NaDiVeG) and reviewed by KPMG Austria GmbH Wirtschaftsprüfungs- und Steuerberatungsgesellschaft, illustrates how the company is responding to global challenges around sustainability.
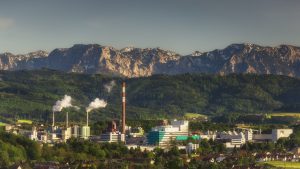
In 2019, Lenzing made a commitment to reducing its greenhouse gas emissions by 50% per ton of product by 2030. The overriding target is to be climate-neutral by 2050. The implementation of two key projects in Brazil and Thailand represents a part of this commitment from Lenzing. The production plant in Thailand was conceived as a CO₂-neutral site and can be supplied with sustainable biogenic energy. The plant in Brazil will feed more than 50% of the electricity generated into the public grid as renewable energy and feature a positive net CO₂ balance.
Lenzing also sets standards for circular economy. The company developed the REFIBRA recycling technology. REFIBRA enables the production of new lyocell fibers on a commercial scale from cotton scraps derived from manufacturing cotton clothing as well as from used garments.
In line with the vision, “We give waste a new life. Every day,” Lenzing strives to make textile waste recycling a commonplace and standard process, just like paper recycling. Lenzing set a new sustainability goal for itself in 2020, as the company aims to manufacture staple fibers on an industrial scale containing up to 50% recycled material by the year 2025.
According to its report, the Lenzing Group operates in line with three strategic principles within the context of its “Naturally positive” sustainability strategy: partnering for change; advancing circularity; and greening the value chain. On this basis, Lenzing has defined various focus areas in order to demonstrate its commitment to further advance the Sustainable Development Goals (SDGs) of the United Nations:
- Sustainable raw material sourcing
- Decarbonization
- Responsible use of water
- Sustainable innovations
- Partnering for systemic change
- Encouraging and empowering people
- Enhancing community wellbeing
Source: lenzing.com
EDANA presents 20th edition of OUTLOOK conference in virtual format
The latest edition of EDANA’s OUTLOOK conference, presented virtually, attracted 596 delegates from 173 companies across the nonwovens, personal care, hygiene and wipes markets. Held from 21-23 April, the new format was a key component in ensuring participants could actively engage, managing over 3,000 video and chat meetings via a virtual platform, as well as a varied choice of conference presentations, panel discussions and live Q&A sessions.
The conference examined emerging global drivers, market trends, sustainability initiatives and new product developments over three days. With 50 companies promoting new products and insights via company stands and over 6,000 new online contacts made, the event served participants from across the supply chain.
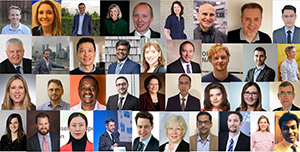
“In the midst of a year unlike any that’s come before, this edition clearly exceeded my expectations for such an online event, and I felt a lot of activity going on. It was an encouraging indicator for future events also” said Mikael Staal Axelsen, CEO of Fibertex Personal Care and Chair of the EDANA board. “All credit to the team and presenters for such a strong topical program that attracted such a large active audience.”
The 20th edition of OUTLOOK opened with a keynote speech on “The outlook for the global economy in the aftermath of the global pandemic” from Robert Ward of The International Institute for Strategic Studies, with the second day’s opener by Kaushik Mitra focusing on the topical issue of raw material shortages. The rest of the conference program featured 45 presentations covering regional updates from the U.S., India, Africa and China, as well as a broad range of expert presentations on new product and process innovations.
Source: edana.org
DSM, MKU Ltd cooperate to provide police ballistic protection in Brazil
Royal DSM and MKU Ltd announced that, through collaboration, they will provide next-generation armor technology with Dyneema unidirectional (UD) material to support the Sao Paulo police.
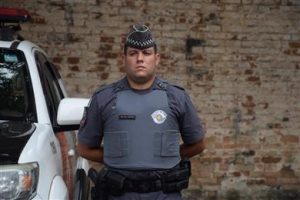
The hybrid vest solution developed by MKU utilized predominantly Dyneema UD material to reach new levels of performance and protection while simultaneously enhancing user comfort and mobility. In soft armor applications, Dyneema offers up to 35% weight reduction, while still protecting against both legacy and emerging threats.
The Sao Paulo police, which is comprised of more than 100,000 officers, is the first law enforcement agency in Brazil to initiate a tender for personal protective equipment based on the latest National Institute of Justice (NIJ) .06 standards for body armor, which provide comprehensive and rigorous compliance for the performance and testing of ballistic materials. In addition to NIJ .06 certification, the tender set is extremely lightweight requirements for level IIIA soft armor vests.
“Together with Dyneema material MKU, was able to deliver a level IIIA soft armor vest that increases wearer ergonomics while reducing weight by more than 20% when compared to the incumbent aramid material,” says Marcelo van de Kamp, Global Business Director, Personal Protection of DSM. “We’re proud to provide a solution that meets the strict requirements of the Sao Paulo police to ensure the brave men and women of their department are protected with Dyneema.”
In addition to the lightweight armor requirement, the vests were also thoroughly tested to ensure performance with NIJ ballistic reports, NIJ certification and in-house ballistic testing both during the tender process and after the vests were received.
“MKU is committed to providing the latest and most cutting-edge solutions to the Sao Paulo police,” says Neeraj Gupta, Managing Director of MKU. “These vests not only offer the best protection, they are extremely light weight and comfortable to wear.”
In line with DSM’s commitment to protect people and the environment they live in, the world’s first ever bio-based HMPE fiber was introduced in 2020. Bio-based Dyneema boasts the same exact performance as conventional Dyneema with a carbon footprint that is 90% lower than generic HMPE.
Oerlikon to acquire INglass S.p.A., expanding polymer processing capability
Oerlikon has signed an agreement to acquire Italy-headquartered INglass S.p.A. and its hot runner systems technology operating under its HRSflow business.
According to the Oerlikon, this strategic acquisition is a significant step in expanding Oerlikon’s current man-made fibers business into the larger polymer processing market. The acquisition accelerates and enhances existing organic initiatives to diversify and strengthen the company’s core high-precision polymer flow control capabilities, products and services. The completion of the transaction is subject to customary regulatory approvals and is expected by the second quarter of 2021.
To reflect Oerlikon’s expansion into a larger high-growth market, the Manmade Fibers Division will be renamed as Polymer Processing Solutions Division. This division will have two business units: Flow Control Solutions and Manmade Fibers Solutions. The business unit Flow Control Solutions will combine the expertise of Oerlikon Barmag’s existing gear metering pumps business line and INglass’ HRSflow operations. The business unit Manmade Fibers Solutions will continue to focus on growing the existing chemical fiber machinery and plant engineering business, offering plant solutions for the production of polyester, polypropylene and nylon.
Source: oerlikon.com
Klaus Heinrichs to retire from Monforts after 30 years
After almost 30 years with the company, Monforts Vice-President Klaus Heinrichs will retire at the end of May. Klaus began working in marketing for the company in 1992.
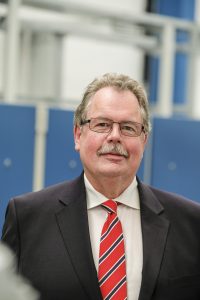
“[Klaus] has always been a guarantor of successful product launches for Monforts technical and technological highlights such as the TwinAir principle of independent airflow regulation, the
Hercules LTM stenter chain, the Econtrol dyeing technology or the Montex Coat device – to mention only a few,” said Monforts Marketing Manager Nicole Croonenbroek. “Later, he also took care of customer service, sales administration and exports in his uniquely calm and quietly spoken style.”
Klaus has also been active on the VDMA’s Exhibition and Marketing Committee since 1993, which he chaired from 2005 to 2008.
“Klaus always enriched the industry discussions with practical and future-oriented proposals and thus also advanced ITMA,” said Thomas Waldmann, Managing Director of the VDMA Textile
Machinery Association. “We sincerely thank him and wish him all the best for this new chapter of his life.”
“We will miss Klaus as a colleague and as a manager because of his skills, character and his engagement,” added Monforts Managing Director Stefan Flöth. “He truly represents the Monforts commitment to our customers to be helpful, accurate, fast and reliable, and we keep him as a friend. I’m sure the many friends he made throughout the world during his career with the company will join us in wishing him all the best for his next phase of life together with his family.”
Source: monforts.com
Infinited Fiber to build flagship production factory in Finland
Circular fashion and textile technology group Infinited Fiber Company is looking for a location in Finland to build a flagship factory to produce regenerated textile fibers for the global market. Infinited Fiber Company will decide on the location by September.
The plant’s entire output is intended for export. Infinited Fiber Company is currently negotiating offtake agreements with several global fashion and textile brands and believes agreements will be in place before the end of 2021, securing the factory’s entire output capacity for several years.
The total investments for setting up the flagship plant are estimated at around 220 million euros. Infinited Fiber Company expects its currently ongoing evaluation into financing options for the plant to be completed soon. The plant is expected to be operational in 2024.
International technology group ANDRITZ will be a key supplier of the process equipment for the new plant.
Infinited Fiber Company’s technology turns cellulose-based raw materials, like cotton-rich textiles, used cardboard, or rice or wheat straw, into Infinna, a unique, premium textile fiber with the natural, soft look and feel of cotton. Infinited Fiber Company currently operates pilot facilities in the cities of Espoo and Valkeakoski, Finland, with a combined nominal capacity of 150 metric tons/annum. The planned flagship factory will have an annual capacity of 30,000 metric tons/annum and will use post-consumer textile waste as feedstock.
“This marks an exciting next phase for Infinited Fiber Company. We are seeing great demand for our circular Infinna™ textile fiber from global fashion brands. Setting up our own plant is a response to this demand. While technology licensing remains central to our long-term business strategy, this plant will speed up the availability of Infinna to the global fashion and textile market in the short- to medium-term,” said Infinited Fiber Company cofounder and CEO, Petri Alava.
“Finland has a long history of cellulose-based industries, excellent engineering capabilities and a strong drive to become a leader in circularity. We are currently considering several potential locations across Finland where the existing infrastructure is supportive of our plans,” Alava said.
Source: infinitedfiber.com
Berry Global initiates $70M expansion of Benson, North Carolina, plant
Manufacturing company Berry Global Inc. is investing $70 million in expanding its Benson, North Carolina, plant, a project that will bring 63 new jobs to the town, according to a report by the Raleigh News & Observer.
The Johnston County North Carolina board of commissioners and Benson town board unanimously approved performance-based economic incentives for Berry Global during a joint meeting as part of a working agreement.
The international Fortune 500 company, headquartered in Evansville, Ind., makes plastic packaging and nonwoven fabrics, including disinfectant wipes. The company has been based in Benson since the 1960s and is the town’s largest private employer with more than 215 people working at its plant on 1206 Chicopee Road.
The expansion is believed to, in part, support production to meet growing demand for disinfecting wipes.
Read the full Raleigh News & Observer report on this story: https://www.newsobserver.com/news/business/article250610364.html
Source: newsobserver.com
BASF, Quantafuel and REMONDIS to cooperate on chemical recycling of plastic waste
BASF, Quantafuel, and REMONDIS have signed a Memorandum of Understanding (MoU) to jointly evaluate a cooperation in chemical recycling including a joint investment into a pyrolysis plant for plastic waste. It is intended that REMONDIS supplies suitable plastic waste to the plant, and BASF uses the resulting pyrolysis oil as feedstock in its Verbund system as part of its ChemCycling project. Quantafuel intends to provide the technology and to operate the plant. The company is a specialist for the pyrolysis of mixed plastic waste and the purification of the resulting pyrolysis oil; the technology is jointly developed and being held with BASF.
The location of the pyrolysis plant will be evaluated together. To maximize a circular economy for plastics, the parties will identify which of the waste plastics provided by REMONDIS could undergo chemical recycling in the future.
Pyrolysis oil derived from plastic waste is fed into BASF’s Verbund production, saving the same amount of fossil resources. Since the pyrolysis oil is inserted directly at the beginning of the chemical value chain, the final sales products have the same properties as products made from fossil feedstock. The share of recycled material is allocated to the end products according to a third-party certified mass balance approach, which allows BASF to offer its customers certified products carrying the name Ccycled.
Each year, almost 20 million metric tons of plastic waste in Europe go unrecycled. By establishing chemical recycling as a complementary solution to mechanical recycling, it is possible to bring back more plastic waste into the materials cycle, which would otherwise be incinerated. The pyrolysis technology can be used to process plastic waste streams that are not recycled mechanically, e.g. for technological or economic reasons.
“BASF has set itself the goal to process 250,000 metric tons of recycled feedstock annually from 2025 onwards. In this regard, it is important to use feedstock derived from plastic waste that would otherwise not have undergone recycling,” said Dr. Lars Kissau, senior vice president of Global Strategic Business Development at BASF’s Petrochemicals division. “Partnering with companies from the waste management and recycling sector as well as innovative technology providers is an ideal constellation to build a sustainable circular economy model for previously non-recycled plastic waste. However, solving the plastic waste challenge will only be possible in a favorable regulatory environment.”
Legislation on the European Union and national level will create the framework for chemical recycling and therefore shape the ability to contribute to a more circular economy for plastics. This includes acknowledging that products based on chemically recycled feedstock are counted towards achieving recycled content targets.
“In order to achieve the sustainability objectives set by the European Union in its visionary Green Deal, it is essential to increase recycling quotas wherever technically and economically feasible,” said Jürgen Ephan, managing director REMONDIS Recycling. “We believe that chemical recycling can provide a meaningful contribution and are therefore happy to join forces with BASF and Quantafuel on the way towards a higher rate of recyclability.”
“Remondis and BASF are excellent partners for realizing an ambitious project like this in Central Europe on a tight timeline, and operating it successfully for the long term,” stated Kjetil Bøhn, CEO of Quantafuel. “We are steadily moving forward in the ramp up of our initial plant in Skive and are happy to now start implementing the roll-out of the technology.”
Source: basf.com | quantafuel.com | remondis.de
FiberVisions, Avgol partner with Polymateria Global to bring natural biodegradation to polyolefin fibers and nonwovens
Indorama Ventures’ FiberVisions and Avgol worked closely with scientists at Polymateria to commercially harness the biotransformation technology pioneered by the UK-based company. The technology alters the properties of polyolefins to make them biodegradable in a natural process.
“We are delighted to be partnering with Polymateria to bring their revolutionary technology into our fibers business and sustainability portfolio more broadly,” said D.K. Agarwal, CEO of Indorama Ventures. “The collaboration between our businesses over the last 18 months has been exemplary and created a credible and scalable solution to an increasingly visible environmental issue.”
The biotransformation technology allows the companies to bring a unique managed lifecycle to disposable products and further expand an already extensive catalog of fiber or spunlaid offerings. The focus of these efforts will be in the launch of non-oxo-degradative components for personal protection masks and face coverings, hygiene, agricultural, industrial and homecare applications.
The use of biotransformation technology will support application in non-virgin resin recycling while providing a solution for fugitive used articles, including those items that have not been properly recycled or disposed of. This process involves the material decomposing into a wax, wherein the wax is further degraded by environmental bacterial action into carbon dioxide, water and biomass.
“This is an incredibly exciting collaboration for Indorama Ventures and Avgol,” said Shachar Rachim, CEO of Avgol. “Our business remains dedicated to developing sustainably sound materials, and the development of entirely biodegradable components is an important step in bringing the first 100% biodegradable-recyclable Hygiene products to the market. This collaboration underscores our commitment to commercialize innovative products which are environmentally focused.”
The parties have been developing prototypes of component fiber and nonwoven products. The first prototypes developed through the partnership have been tested and are compliant with the stringent testing for biodegradability defined in British Standards Institute’s (BSI) new standard for Biodegradation, PAS9017. In meeting this standard, fiber and fabrics are confirmed to form no harmful microplastics as part of the biodegradation process.
“With 32% of all plastic winding up in our natural environment each year we need to ensure we are working with partners who can enable scalable solutions to address what is becoming close to a 100 million tons per year problem. Indorama has a strong track record on sustainability and shares our mission and values. The trust that has emerged between our businesses has been grounded in science and a shared mission to tackle the plastic pollution pandemic at scale,” said Niall Dunne, CEO of Polymateria.
Sources: avgol.com | fibervisions.com | polymateria.com
BastCore completes $2.8M oversubscribed Series A financing
Manufacturing industrial hemp fiber processing & technology company, BastCore, announced it has completed an oversubscribed Series A financing for $2.8 million.
The Montgomery, Alabama-based firm intends to utilize the proceeds to further enhance its proprietary decortication and degumming technology, hire new personnel, and meet the demand it is seeing from for its hemp fiber product.
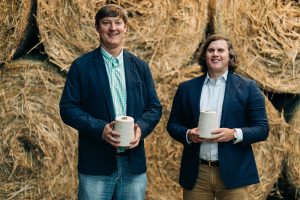
“The addressable market opportunity is massive”, said BastCore Managing Director, Austin Bryant. “Billion dollar opportunities are great, but when you have proprietary technology that can solve the processing issue for the farmers and help them monetize their product in addition to capitalizing on a trillion dollar market opportunity in terms of end consumer products, now you have my attention. We always say that we are building more than just a company here, we are building an industry.”
BastCore, which was founded in 2014 specializes in processing industrial hemp and has the opportunity to supply the raw material for over 25,000 industrial use cases and applications. BastCore works closely with all its partners to ensure product traceability and transparency. “Global supply chains are in the process of disruption. Our partners demand transparency and traceability. BastCore is extremely well positioned to capitalize on this trend, and we look forward to providing good manufacturing based jobs here in the US,” said BastCore CEO, Coleman Beale.
Poseidon Asset Management participated in the oversubscribed round. “Poseidon has been investing in cannabis and hemp since our first fund was launched back in 2014,” said Poseidon Asset Management Managing Director, Morgan Paxhia. “Our capital has helped to create thousands of jobs and millions in tax revenues and we believe this economic energy is coming to the US industrial hemp industry. We have limited our exposure to US CBD as we saw too much money flooding into that space, but industrial hemp for textiles, automotive, construction, etc., are many multiples the size of CBD, with much greater plant utilization. BastCore has developed innovative industry leading technology capable of supporting and transforming massive industries. This is a great American story in the making.”
Source: bastcore.com
VDMA launches ‘Textile Machinery Newsroom’ portal
VDMA’s “Textile Machinery Newsroom” is now online, providing technical and marketing information for textile and nonwovens manufacturers. The portal includes supplier news, a sourcing service and the VDMA’s Webtalks webinars section.
Companies can now participate and book technology Webtalks webinars either alone, in pairs or in a three-part format. The next two webtalks, “Design for Recycling” and “Digitalization in Textile Finishing,” are scheduled for April 21 and April 28, respectively.
“Design for Recycling” will feature three different experts covering various topics:
- Prof. Dr. Stefan Schlichter, ITA Augsburg: Design for Recycling – using artificial intelligence for sustainable lightweight solutions,
- Jochen Schmidt, KARL MAYER Technische Textilien: Sustainable products produced on KARL MAYER machines, and Martin Würtele, KraussMaffei Technologies: Sustainable composite technologies made by Krauss Maffei Technologies.
The speakers and topics featured in “Digitalization in Textile Finishing” include:
- Ralf Stange, Thies: Digitalization in textile finishing – integration of energy and maintenance management
- Axel Pieper, Brückner: Digitalization, energy and maintenance management for dry finishing machines
- Jürgen Jerzembeck, Setex: Manufacturing Management System view on integrated energy and maintenance management in textile finishing.
Registration: Design for Recycling and Digitalization in Textile Finishing
Source: vdma.org
Kelheim Fibres joins ZDHC ‘Roadmap to Zero’ program
Bavarian viscose specialty fiber manufacturer Kelheim Fibres has joined the ZDHC program “Roadmap to Zero.” The nonprofit organization ZHDC, with more than 160 contributors worldwide, has set itself the goal of completely eliminating harmful substances from the textile value chain.
The ZDHC guidelines provide producers of Man-Made Cellulosic Fibers (MMCF) with uniform criteria for measuring indicators such as wastewater, air emissions and other process-related parameters. The measured data is independently monitored and published.
Kelheim Fibres, the world’s first EMAS (Environmental Management and Audit Scheme)-validated viscose fiber producer, sees its ZDHC contributorship as another building block on the road to more sustainable fiber production.
“We want to develop our industry with our know-how towards a greener future. Sustainability is an integral part of our corporate philosophy and strategy. We fully support ZDHC’s vision of a widespread implementation of sustainably chemistry, driving innovations and best practices in textile, apparel and footwear industries to protect consumers workers and the environment,” said Craig Barker, CEO at Kelheim Fibres. “ZDHC provides us with access to a range of best practices in chemical management and gives us the opportunity to network and learn from each other with like-minded industry partners. ZDHC’s collaborative approach will accelerate the shift to a more responsible industry and we want to contribute to that.”
Source: kelheim-fibres.com
Asahi Kasei opens new European R&D Center
Asahi Kasei, with its sister company Asahi Kasei Microdevices Europe GmbH, has relocated the Asahi Kasei Europe R&D Center to its new location at the “C-View Offices” at Düsseldorf Harbor, Germany. from its prior location in Dormagen, Germany. The building features open office and meeting space, a showroom featuring a display of materials and solutions ranging from sustainable microfiber materials for interior seat and headliner coverings to foam products and separators for battery applications, and laboratory space for various materials, such as engineering plastics, synthetic rubber, as well as for battery and coating materials.
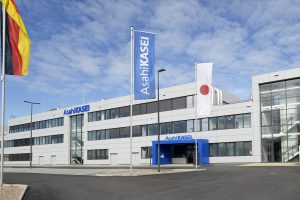
“This relocation marks the next important milestone of Asahi Kasei’s expansion on the European market,” said Hideki Tsutsumi, Managing Director at Asahi Kasei Europe. “Europe is at the forefront of an evolution in the automotive industry that is said to happen once in a century. In addition, it is the forerunner in environmental topics. Uniting sales, marketing, R&D and technical service activities at one single location will enable us to quickly address the changing demands by customers and to enhance joint projects with local partners.”
Source: asahi-kasei.com
Freudenberg launches an Eco-calculator to help customers improve environmental footprint
Freudenberg Performance Materials launched its Eco-calculator to help customers assess and choose Evolon textile solutions for bedding and bath towels based on their entire life cycle, from raw material through the laundering phases to product end-of-life. The tool evaluates eight environmental criteria, including the carbon footprint, water impact, and eco-toxicity, to provide information on how customers can save energy and water during subsequent care steps for the relevant textile.
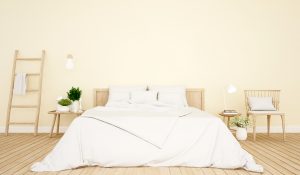
The Eco-calculator relies on data provided and validated by independent external experts, who conducted a Life Cycle Assessment focusing on textile applications such as bed linen, bath towels and workwear used in hotels and hospitals. The Eco-calculator also takes account of data from washing tests to evaluate the durability and the consumption levels of water, energy and detergent required by the different fabrics. The testing program simulated industrial wash cycles to assess 12 different textile articles. Each type of product was evaluated in terms of the water, energy and detergent consumption required for its care as well as its appearance and mechanical properties over washings.
“Our Evolon experts help our customers determine the scenarios they wish to evaluate, for example by varying the weight of the materials, the types of finish, the number of washing cycles, or the country of use. Based on this data, the Freudenberg experts provide an economic and environmental evaluation using the Eco-calculator,” said Jean-François Kerhault, Business Segment Manager Evolon at Freudenberg Performance Materials. “This information can help our customers to evaluate the environmental footprint of their own finished products. They can include the data in their own product eco-design approach, or meet new market requirements about information on the carbon footprint.”
Source: freudenberg-pm.com
Elsner Engineering launches online training program and ‘Keep On Rollin’ video series
Elsner Engineering launched its ELSNER University online training program with virtual educational programs on machine operation, maintenance and adjustment procedures. The program is designed for customers and prospective customers to learn best practices for maximizing throughput while keeping production running optimally.
Elsner also recently launched a new video series “Keep On Rollin'” with Jay Roth, the company’s director of sales, sharing stories about the history of Elsner innovations, to tours around the facilities to interviews with key team members.
Elsner University: https://www.elsnereng.com/elsner-university.html
View the first of Elsner’s video series “Keep On Rollin'”.
Source: elsnereng.com
PFNonwovens to add new line, capability in Czech Republic
PFNonwovens, a global producer of nonwoven fabrics with operations in Europe, the United States and Africa, is investing in a new technology designed to boost nonwoven product performance at its site in Znojmo, Czech Republic. This new technology allows PFN to make proprietary premium, apertured and 3D embossed fabrics to expand and diversify its product portfolio for the medical and hygiene markets. Installation and commissioning of the new line is scheduled for Q2 2021.
PFN’s Chief Technology and Product Development Officer, Tonny de Beer, commented that “We are very excited to combine this technology to add even more value to our premium and ultra-premium softness solutions and to enhance our bio-sourced nonwoven portfolio. We will be able to offer new patterned topsheets with higher absorption, beautifully textured backsheets with improved breathability, and we will launch several new compelling product applications for our hygiene and medical markets.”
“PFN remains focused on delivering precisely tailored solutions to meet specific customer needs. This investment provides our customers an easy and visually distinct way to differentiate their products from their competition, while providing better value to the end-consumers”, said Shane Vincent, PFN’s Chief Commercial Officer & Global Head of Business Development.
Source: pfnonwovens.com
Lenzing expands E-branding service to include VEOCEL brand
Lenzing is introducing its E-branding service for certification and licensing to the VEOCEL brand to elevate supply chain transparency for nonwoven fibers. The Lenzing E-Branding Service provides the VEOCEL brand a platform designed to showcase the use of sustainable, high-quality and ethically sourced materials.
The Lenzing E-Branding Service unifies registration, application and approval in an online system designed to eliminate the use of paper, and reduce response times, with the aim to enhance efficiency by digitizing workflow. As a digital hub for VEOCEL brand partners, the platform includes features to apply for new licenses, monitor application status, and manage existing licenses. Simultaneously, the platform will act as a support portal, showcasing the latest branding guidelines and support for VEOCEL brand certified products.
“We are excited to expand our industry-leading Lenzing E-Branding Service to VEOCEL brand customers and partners. The expansion showcases Lenzing’s unwavering commitment to sustainability for nonwoven applications, accelerates the digitalization of the industry and sets new standards for driving greater transparency,” said Jürgen Eizinger, vice president of Global Nonwovens Business, Lenzing AG.
Source: lenzing.com
Teijin to mass produce nanofiber filament made from recycled polyester
Teijin Frontier Co. announced its technology to mass produce a new version of its Nanofront ultra-fine polyester. It has developed new polymer-control and spinning techniques for Nanofront to be made from recycled polyester materials and expects it to replace its conventional Nanofront made from petroleum-derived raw materials in a wide range of fields, including sportswear, functional clothing, industrial uniforms, and more.
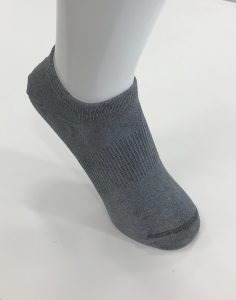
The key was the company’ “sea-island” composite-fiber processing technology, which distributes two types of polymers into the fiber’s “sea” and “island” parts, then dissolves and removes the “sea” part using an alkaline, etc., treatment, and finally extracts only the “island” part as raw yarn. The new technology will enable Teijin Frontier to produce all of its polyester fiber products with recycled raw materials. The company is forecasting sales of recycled-polyester Nanofront to reach JPY 300 million in fiscal 2021 and JPY 800 million in fiscal 2025.
Source: teijin.com
NXTNano to add three nanofiber lines; expanding production capacity to meet strong demand expected through 2023
NXTNano, LLC, has begun to install three additional HYPR-Spun Nanofiber production lines, with the first of the lines expected to be operational in June, and all three within the 2021 calendar year. The new lines will take NXTNano’s total line count to six, supporting the production of high-volume nanofiber manufacturing up to a maximum roll width of 2.15 meters.
“2020 was an incredible year for NXTNano,” said Andrew McDowell, NXTNano, LLC’s Director of Sales. “We saw rapid adoption of the technology into a number of new markets, and more importantly we have a social obligation to continue serving our mask, respirator, and indoor air purification customers who have taken up the fight against COVID. In existing markets we expected COVID to produce a pronounced slowdown, but that never materialized. As a result of the growth and new projects moving to commercial sales, the time has arrived for us to add capacity”
The number of markets commercially consuming nanofiber has continued to exhibit strong growth, with forecasts for CAGR above 36% though 2023.
“I’ve spent nearly my entire career in nonwovens and filtration, over 30 years now, and the last nine months have been unique to anything I’ve seen before,” said Alan Smithies, NxtNano’s vice president of technology. “The growth has not been without challenges, but I firmly believe we as a company have stepped forward and embraced them. Our head count is now over 80 people, more than two and a halftimes what it was in 2019, and we are putting out full truck loads of material every day.”
Source: nxtnano.com
Freudenberg reports gradual recovery amid pandemic
The Freudenberg Group reported sales of $10.1 billion globally for its 2020 financial year, a decrease from the previous year’s $10.6 billion. The company reported a profit from operations of $768.4 million compared to $940.5 million the year before. At $1.31 billion, cash flow was above the comparable figure of $1.1 billion for 2019. Freudenberg continued to invest, spending $511.9 million, 5 percent of sales (5.1 percent in 2019), on research and development. At the same time, investments in tangible assets totaled $329.3 million globally. The international rating agency Moody’s Deutschland GmbH, Frankfurt am Main, confirmed its credit rating of Freudenberg at A3, with a stable outlook, as in the previous year.
“For Freudenberg, the past 12 months have been extraordinarily demanding and challenging,” said Dr. Mohsen Sohi, CEO of the Freudenberg Group, commenting on the results of the last financial year. “So far we have managed the crisis comparatively well.”
Freudenberg’s Business Groups producing for the automotive, textile and mechanical engineering sectors faced a challenging economic environment in the beginning of the year, while Freudenberg Home and Cleaning Solutions (FHCS) reported sales of more than $1 billion for the first time. Freudenberg Filtration Technologies (FFT) also benefited from new product and service solutions such as special system checks for COVID-19 and hygiene audits. Demand at Freudenberg Medical (FM) also grew.
In May 2020, Freudenberg acquired 100 percent of the shares in Low & Bonar PLC, London, United Kingdom, now Low & Bonar Limited, Edinburgh, United Kingdom. Low & Bonar is a global manufacturer of technical textiles. The company will be integrated in the Freudenberg Performance Materials Business Group. Klüber Lubrication München SE &Co. KG (part of Freudenberg Chemical Specialities), Munich, Germany, acquired Traxit International GmbH, Schwelm, Germany, in January 2020. This company is a producer of wire drawing lubricants and has supplied a full range of lubricants for all applications to the wire drawing industry for about 140 years.
The sustainability of products and processes has been part of Freudenberg’s corporate responsibility for many years. In 2016, Freudenberg developed a company-wide sustainability strategy. In the “Sustainability Drives Climate Action” project, Freudenberg is developing a position with respect to the challenges and opportunities of climate change. Freudenberg intends to reduce CO2 emissions by 25 percent by 2025. The opportunities and costs of climate neutrality for Freudenberg are to be identified in 2021. The company plans to have its energy balance improved by purchasing green electric power and is committed to offsetting CO2 emissions.
Source: freudenberg.com
Dornbirn GFC announces virtual format for 60th Anniversary edition
The Dornbirn Global Fiber Congress, celebrating its 60th anniversary in 2021, announced that this edition of the event will be presented virtually due to ongoing travel concerns related to the COVID-19 pandemic. The event will feature an interactive platform to bring participants a “live feeling“ during the congress, according to event organizers.
This virtual edition of Dornbirn GFC will feature presentations from top experts from industry and research presenting the latest scientific results. Organizers said 90 lecture slots have already been allocated. Lectures will take place in parallel in two lecture halls. Panel discussions, breakout sessions and virtual meeting lounges will provide opportunities for networking and information exchange. A virtual exhibition area with 25 exhibitors will also be offered:
Featured conference tracks include:
- Fiber innovations
- Sustainability and Circular Economy
- Nonwovens and technical textiles
- Surface modifications and additives
In related news, the first edition of Dornbirn GFC-Asia was presented March 23-24, 2021, in Daegu, Korea. More than 200 participants took part in the online event in Korea, with 32 presentations offered.
Source: dornbirn-gfc.com
The LYCRA Company announces leadership changes
The LYCRA Company announced the appointment of Yafu Qiu, chairman of The LYCRA Company, and Julien Born, chief commercial officer of The LYCRA Company, as co-chief executive officers following the retirement of David Trerotola. The co-CEO structure is intended to better implement The LYCRA Company’s new strategic development plan for the next five years and will bring greater operational focus and tap into each leader’s experience and skills in the areas most beneficial to the company to solidify its industry-leading position and drive its long-term success.
Trerotola served as the company’s chief executive officer since 2019, following the Ruyi Group’s acquisition of the business. He began his career in 1994 with DuPont and retires after 20 years of service to The LYCRA Company and its predecessor companies.
Julien Born, currently the company’s chief commercial officer, will serve as co-CEO and lead the overall operations of the company and implement its ambitious growth vision. Born joined the business in 2007 and, since 2018, led the company’s apparel business, where he managed the global commercial organization, helped strengthen R&D and innovation capabilities, and oversaw manufacturing assets. Born has also spent significant time in Asia, where he led that region over an eight-year period, with assignments in Shanghai and Hong Kong. Born has had a diverse 24-year career spent in the U.S., Europe and Asia, as both an executive in large multinational companies and as a business owner of a full-service corporate licensing agency. A native of Switzerland, Born holds a bachelor’s degree from Arizona State University’s W.P. Carey School of Business and a Swiss baccalaureate degree.
Qiu, in addition to continuing as chairman of The LYCRA Company, will focus his co-CEO role on the company’s relationships with key stakeholders, board governance matters, strategic planning, and capital structure adjustments, including the strategy and timing of an initial public offering.
Source: thelycracompany.com
FET supplies advanced melt-spinning technology to Center for Textile, Indonesia
Fibre Extrusion Technology Limited of Leeds, England has installed a new FET-100 Series Laboratory Melt Spinning System for continuous filament yarn applications at the Center for Textile, Indonesia. The FET-100 system will play a vital role in driving technological innovation in the Indonesian textile industry. With this installation, the nation’s fiber manufacturers now have access to advanced melt-spinning facilities for developing and testing novel fibers for global applications. This laboratory melt spinning system is multi-polymer capable and can produce both mono and bi-component formats.
A ceremony commemorating the event was presented on March 18, bringing together industrial leaders and Ministry of Industry figures with Mr. Agus Gumiwang Kartasasmita, the Minister of Industry, launching the ceremony. FET representatives and the innovation agency BSP were also in attendance.
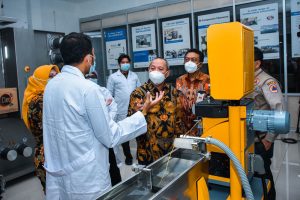
The Center for Textile, Balai Besar Tekstils of Bandung, has the task of carrying out research, development, cooperation, testing, certification and competency development of the textile sector, under the control of the Ministry of Industry (Kementerian Perindustrian). The Ministry has a stated objective that Indonesia becomes a “Resilient Industrial Country” based on innovation and technology.
This event was also streamed online for textile businesses to view in light of COVID protocols and was covered on local television. The Indonesia Textile Association and the Indonesia Synthetic Fiber Manufacturer Association were also involved in promoting the ceremony.
Source: fetuk.com
The LYCRA Company’s COOLMAX EcoMade fiber made from 100% textile waste
The LYCRA Company launched its COOLMAX EcoMade fiber made from 100% textile waste. A depolymerization and refining process converts textile waste scraps from garment manufacturers into fibers with properties comparable to virgin polyester.
“We are pleased to announce this new product as textile waste represents a substantial sustainability challenge, as the equivalent of one garbage truck of textiles is sent to landfills or incinerated every second,” said Julien Born, chief commercial officer, The LYCRA Company. “This offering exemplifies the approach we have to develop products and technologies that support a more sustainable future for our vast global customer base.”
Source: coolmax.com
Clariant adds R&D facilities, brings new technology developments to China
Clariant’s Additives business announced the addition of new R&D facilities and joint application technology developments at the One Clariant Campus (OCC) in China.
The new Additives R&D Center will be integrated in the Clariant Innovation Center China in Shanghai. It aims to bring faster lead times and more speed in development efforts for various application sectors, including E&E, 5G, automotive, packaging, fibers & films, adhesives, coatings and inks. Supplementing Clariant’s additives’ production facilities in China, the R&D Center will offer customers opportunities for joint development and application testing, at every step of the value chain. From polymerization to compounding and conversion, all the way to performance testing.
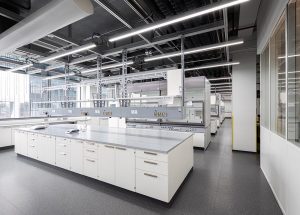
“Demand for high-end additives is growing strongly in China,” Francois Bleger, Head of Clariant Additives business. “As local manufacturers develop more sophisticated processes, technologies and products to align with market needs and China’s environmental goals, sustainable additives can be key to boosting progress effectively and efficiently. Our new Additives R&D Center creates the exciting opportunity to be more agile in our additive development and foster China-relevant innovation together, from the start of the creative process. In a nutshell, innovation for customers, with customers, at the heart of the main markets.”
At Chinaplas 2021, Clariant will also introduce several new additives to the region from its EcoCircle initiative to support manufacturers in achieving these goals.
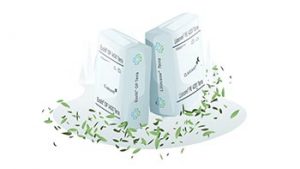
EcoCircle supports the transition from a one-way plastics value chain to a circular plastics economy by going beyond a simple product focus, looking at the entire value chain, and identifying the most sustainable and viable solutions. This includes the development of sustainable solutions for mechanical recycling and the use of certified renewable raw materials to produce high-performance additives. Qualifying products carry a designator based on their mass-balance or real renewable carbon content to help manufacturers identify products with key advantages. Among others, this includes Terra for products with a high renewable content, minimum 50% Renewable Carbon Index (RCI) based on mass balance certification or real renewable content; and VITA for products from natural origin with at least 98% RCI real renewable content.
New for the Chinese market is the Exolit OP Terra range, renewable-based halogen-free flame retardants. A like-for-like drop in alternative to Clariant’s fossil based Exolit OP products, they achieve UL 94 V-0 rating with stable flame retardancy even after multiple recycling processes. Application areas include electronic and electrical
equipment, and automotive components.
Licocare RBW VITA will also be presented to customers in China for the first time. Clariant’s fully sustainable, practically 100% renewable, non-food competing bio-additives solutions offer multiple processing and end-product enhancements to biopolymers, such as Polylactic Acid (PLA). And in doing so, Licocare RBW VITA opens up opportunities for brands to consider biopolyme
rs as a viable, low carbon footprint alternative to fossil-based plastics. Clariant also introduces Licocare RBW 330 VITA, a new renewable-based solution that nucleates polyamides, reducing the cooling time and shrink/warp, yielding faster cycles, and leading to better molding costs.
Source: clariant.com
Trinseo, BASF jointly announce business collaboration on circular feedstock
Trinseo and BASF announced the intention to expand their businesses with the production of styrene based on circular feedstock. The enhanced collaboration between Trinseo and BASF aims to increase efforts by both companies in the development and management of styrene featuring an improved environmental profile.
Trinseo has recently been procuring first supplies of the synthetical chemical styrene based on circular feedstock from BASF for use in its Solution-Styrene Butadiene Rubber (S-SBR) and polystyrene (PS) products. S-SBR is commonly used by tire manufacturers while PS products are used in applications such as food packaging and appliances.
“By creating synergy across the value chain, the Trinseo-BASF collaboration is an important move towards helping our customers reach their sustainability goals as well as the development of a truly circular economy,” said Nicolas Joly, Vice President, Plastics & Feedstocks of Trinseo. “The initiative is also in line with Trinseo’s 2030 Sustainability Goals announced earlier this year.”
“CO2 emission reduction and a circular economy are BASF’s paramount targets. Using circular feedstocks instead of virgin fossil resources contributes directly or indirectly to an improved CO2 footprint of subsequent products,” says Klaus Ries, Vice President for BASF’s Styrenics Business Europe. “While our customer Trinseo procures biomass balanced (BMB) styrene for their downstream business already, styrene Ccycled will be available in the near future”.
Sources: basf.com | trinseo.com
INDA launches on-demand nonwoven trainings and key issue webinars
INDA is offering a series of on-demand training courses and issue-awareness webinars for nonwoven and engineered fabric professionals.
“We are pleased to offer on-demand options for critical training and issue awareness content for all levels of professionals seeking to advance their career development. On-demand allows participants around the world the convenience of managing when, where, and for what duration they access this valuable content,” said Dave Rousse, INDA President. “This new offering meets today’s need for digital access to essential materials.”
INDA now offers training options in on-demand, live virtual, and traditional in-person formats.
INDA’s on-demand program includes:
- Elementary Nonwovens Training Course — designed for non-technical professionals, this five-hour course provides newcomers the basics of nonwovens in simple, clear, concise language.
- Intermediate Nonwovens Training Course — designed for industry professionals with five-plus years nonwovens’ experience or a technical background, this seven-hour course is a bridge between INDA’s Elementary Nonwovens Training Course and the Advanced Courses.
- WIPES Academy (Training Course) — designed to cover every major facet of the wipes sector, including design, materials, production, cost implications, and packaging.
- Filter Media Training Course — designed for professionals wanting to learn more about the development, testing and application of nonwovens in filtration.
INDA’s on-demand webinars include:
- New ASTM Performance Standard for General Public Facemasks and the Design Opportunities for Engineered Materials — Details the two performance levels of the new facemask standard, the test methods, and the opportunities created for facemask designers and filter media makers to differentiate and create competitive advantage.
- Plastics Concerns in the Nonwovens Industry — Details the state of play in the EU and in North America, where legislative initiatives related to plastics have been introduced in California, Canada and the U.S. Congress and the threats these initiatives pose to the industry.
- Spunbond/Spunmelt/’Spunlace’ Capacity/Demand Scenarios Prompted by the Pandemic (coming Apr. 6) — Details the developments in these sectors, with data from INDA’s 2020 North American Supply Report, and an analysis and insights on developments caused by the pandemic response for wipes, medical gowns, and facemask materials.
For more details on INDA’s courses and webinars: pathlms.com/inda/courses
Source: inda.org
* International Filtration News is owned by INDA, Association of the Nonwoven Fabrics Industry (inda.org).