In the dynamic and global textile fiber industry with its various manufacturing processes and end-uses, news and information is breaking on a daily basis. International Fiber Journal is tracking stories relevant to our industry from manmade to natural to bio-based fibers, innovations in nonwoven, woven, braided and technical textiles, technologies for additives, bonding, coatings and polymers, and applications from apparel to hygiene to transportation, and more. Here we will post news stories relevant to textile fibers and their downstream applications on an ongoing basis. Please check back for regular updates. If you have news that you feel should be added to this summary report, please email it to Matt Migliore at mmigliore@inda.media.
Most recent update: November 27, 2020
Fibre Extrusion Technology exceeds £25 million in biomedical sales with 40th melt-spinning installation
Fibre Extrusion Technology Limited of Leeds has exceeded £25 million in sales in the biomedical sector with its 40th melt spinning system installed recently at a leading suture manufacturer in China.
FET has built strong relationships with several multinational companies, designing and supplying a wide range of equipment, ancillaries and turnkey solutions for strongly regulated biomedical applications. As the market leader in melt spinning systems, FET has been the default supplier to the medical sector, collaborating with clients over extended periods of time, often providing multiple systems to key clients.
FET’s experience is in high-quality medical-grade textile materials from both synthetic resorbable and non-absorbable polymers used in the manufacture of sutures and other medical devices.
FET can melt spin numerous material formats from resorbable polymers, such as multifilament and monofilament, non-woven structures, bi-component filaments and hollow filaments.
Source: fetuk.com
Braskem and Haldor Topsoe achieve first production of bio-based MEG from sugar
Braskem, the largest petrochemical company in the Americas and a world leader in the production of biopolymers, and Denmark-based Haldor Topsoe, a global leader in supply of catalysts, technology, and services for the chemical and refining industries, have announced that they achieved their first-ever demo-scale production of bio-based monoethylene glycol (MEG). As a result of the collaboration between the two companies, the MOSAIK technology development has been progressing according to schedule at the demonstration unit located in Lyngby, Denmark.
The demonstration unit was started up in 2019 with the primary goal to demonstrate all key design features of the pioneering technology that transforms sugar into renewable MEG. Since then, the remaining process units of the plant have been built and put into operation, and the production process has been optimized.
MEG is a raw material for PET (polyethylene terephthalate), which has numerous applications and is an essential feedstock in sectors such as textiles and packaging, especially beverage bottles. Currently, MEG is predominantly made from fossil-based feedstocks, such as naphtha, gas, or coal. The global MEG market represents a value of approximately US$ 25 billion.
The technology will also co-produce, in a lower quantity, monopropylene glycol (MPG), which has a wide variety of applications ranging from unsaturated polyester resins (UPR), commonly used in construction materials, to cosmetic products.
Source: braskem.com.br
Asia Pacific Rayon publishes sustainability report
Asia Pacific Rayon (APR) has released its inaugural Sustainability Progress Report covering the first 18 months of its operations from January 2019 to June 2020. Formally inaugurated by Indonesia President Joko Widodo in February 2020, APR is a vertically integrated operation from renewable fiber plantations to high-value textile manufacturing facilities, located in in Riau, Sumatra.
APR’s effort to report on its sustainability performance underscores the company’s commitment to responsible viscose production. The report, themed “Creating Sustainable Value, From Plantation to Fashion,” details APR’s sustainability efforts which are focused on clean manufacturing, sustainable sourcing, and initiatives in support of employees and communities.
Notably, APR has attained a string of certifications relating to manufacturing, sourcing and product. It is the first viscose manufacturer in Indonesia to receive the internationally recognised STeP by OEKO-TEX certification. APR’s products carries the labels of OEKO-TEX Standard 100, USDA Biobased, MADE in GREEN by OEKO-TEX, Medically “Tested-Tested for Toxins” by FKT. It obtained ISO 9001 for quality management and 14001 for environmental management systems, and OHSAS 18001 for occupational health and safety management systems. Its PEFC Chain of Custody certification confirms sourcing from 100% certified dissolving wood pulp.
Further, in September 2020, APR updated its sustainability policy, strengthening its clean manufacturing commitment to the ZDHC Roadmap and adopting a time-bound roadmap to meet the emissions and consumption levels set out in EU BAT.
Read the full report: https://www.aprayon.com/wp-content/uploads/2020/11/apr-sustainability-progress-report-jan2019-jun2020.pdf
Source: aprayon.com
İlay puts a premium on energy efficiency with new Montex stenter installation
İlay Textile is based in Bursa, Turkey, with a plant that extends over 50,000 square meters from fabric weaving and warp knitting, via extensive dyeing, finishing and printing operations, to final garment making-up and packaging. Aligning with its mission of continuous progress in error-free and resource-efficient manufacturing, İlay has just taken delivery of a new Monforts Montex stenter range, with a working width of two meters and eight TwinAir chambers.
“This installation provides us with much improved control options for all process parameters and compared to the old stenter it is replacing, we are particularly impressed with the energy savings we are making,” says the company’s production director Fikri Savaş.
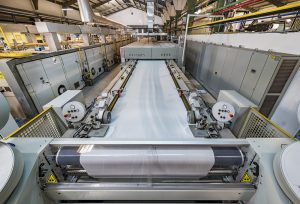
Achieving energy savings on Montex stenters has been a key focus for Monforts designers and engineers in Germany for many years.
With the TwinAir heating chamber system within a Montex stenter, top and bottom airflows can be regulated completely independently of each other, ensuring heat is only applied when and where it is required. The Optiscan balancing system ensures continuous automatic evaluation of the distance between the nozzles and the fabric for highly economical and contact-free drying.
The resulting constant evaporation rate within the stenter ensures optimum energy utilization.
In addition, TwinAir chambers feature special paneling for low heat radiation, careful sealing of all connecting positions and chamber access points, and air locks at both the entry and the exit.
The new Montex line was completed at İlay Textile in August 2020, with no problems during either installation or commissioning.
“The owners of Neotek followed the assembly carefully and supported us in every way so that we could produce with the machine as soon as possible,” Mr Savaş concludes. “The technicians who installed the machine and put it into operation were very sociable and worked very harmoniously with our own team.”
Source: monforts.de
Virtual Hygienix conference attracts 240+ attendees in hygiene and personal care
Over 240 professionals from 18 countries throughout the supply chain participated in the sixth edition of INDA’s Hygienix conference, presented in an all-virtual format, Nov. 17-19.
Session topics included: The Absorbent Hygiene Industry under COVID-19; U.S. Economic Forecast and Industry Statistics; Packaging and Labeling Challenges; Innovative Developments and Intellectual Property; Smart Diapers; and Principles of Sustainability and Elderly Care. Virtual Hygienix™ included presentations from 24 industry experts along with 6+ hours of virtual live personal engagement.
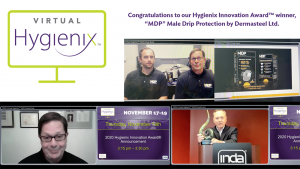
Presentation highlights included:
- Colin Hanna, Director of Research, and Pricie Hanna, Managing Partner, Price Hanna Consultants – presented challenges, resiliency, and recalibration of sourcing and risk management strategies at multi-levels in the absorbent hygiene product supply chain.
- Lindsey Piegza, Ph.D., Chief Economist, Stifel Financial Corporation, presented an outlook on the U.S. economy from a pre- and post-election perspective, including comments on a potential stimulus package and the impact of recent vaccine developments on the economic outlook.
- Bryan Haynes, Ph.D., Senior Technical Director – Global Nonwovens, Kimberly-Clark Corporation presented on the future of sustainable plastic alternatives and the impact of the European Union Single Use Plastics Directive on some of these alternatives, as well as Kimberly-Clark Corporation’s sustainability 2030 strategies.
The event included the announcement of INDA’s Hygienix Innovation Award to Male Drip Protection from Dermasteel Ltd. – a leak protection product, with a patent-pending, proprietary design that is discreet, form-fitting, and tailored to the male anatomy. This new product provides effective containment of bodily fluids, protecting the wearer’s skin while affording him comfort and confidence.
Other nominees for the Award included a new class of adhesives, Full-Care 6217, from H.B. Fuller and High Gel Strength (HGS) SAF from Technical Absorbents Limited.
The next Hygienix is scheduled for November 15-18, at the Westin Kierland hotel in Scottsdale, Arizona.
Source: inda.org
* International Fiber Journal is owned by INDA, Association of the Nonwoven Fabrics Industry (inda.org).
Autoneum debuts tufted carpet solution made of recycled PET
With Relive-1, Autoneum is launching a tufted carpet that meets the highest requirements of sustainable mobility. The tufting technology for the compact to premium class, which has been awarded the “Autoneum Pure” label for outstanding environmental friendliness, is also more durable than the carpet standards common in these vehicle segments and convinces with excellent cleanability.

With Relive-1, Autoneum now offers a premium technology for automotive carpets that not only is aesthetically pleasing, but also has an exceptional environmental performance. With Relive-1, only recycled PET bottles are used to manufacture the carpet yarns. Autoneum reuses this raw material, thus conserving natural resources and reducing plastic waste – while at the same time ensuring that new, high-quality carpet systems for future vehicle generations can be produced cost-effectively from used PET bottles. Moreover, Relive-1 is an important step towards mono-material constructions and consequently, zero waste tufted carpet production.
Compared to standard carpets in compact to large class vehicles, Relive-1 carpets are more robust thanks to significantly higher abrasion resistance, and easy to clean thanks to the vertical alignment of the filaments and the water repellency of polyester. As a result, small particles such as wood splinters, dust or pebbles as well as liquids can be removed easily with no residual traces, which is a key benefit for recreational vehicles like SUVs.
Source: autoneum.com
Shemesh Automation expands executive team, names Anna Kingsley Chief Marketing Officer
Shemesh Automation is responding to increased demand for its packaging machinery solutions by expanding its executive team with the appointment of Anna Kingsley as Chief
Marketing Officer (CMO).
The US is already a major stronghold for Shemesh and with the addition of Kingsley, the company is hoping to take the business to new heights. Kingsley is an award-winning marketing leader, with 30 years’ international business experience. She’s worked in marketing for global brands (such as Coca-Cola, Virgin and Match.com), as well as for Dixons (PCWorld/Currys).
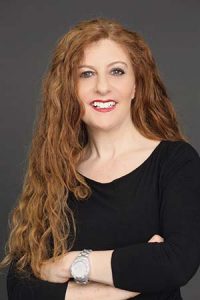
Shai Shemesh, Shemesh Automation’s CEO commented, “Ms. Kingsley joins us at an exciting inflection point. Anna brings substantial experience, knowledge and leadership in marketing to the role. She has demonstrated a rare ability to combine strategic and blue-sky thinking with creativity and a strong commercial acumen. Anna is a great leader and is vital to our next growth stage. I have no doubt that she will be key in taking the business to new heights in 2021.”
Kingsley commented: “One of the many amazing aspects of this job is that I can take a holistic view as well as applying my hands-on experience, in every marketing channel. I’m already enjoying working on a winning marketing strategy, which I hope will propel Shemesh even further in the global high-end packaging machinery arena.”
Source: shemeshautomation.com
Kelheim Fibres joins ETP ‘Bio-Based Fibres’ and ‘Circular Economy’ programs
The Bavarian viscose specialty fibers manufacturer Kelheim Fibres has partnered with the European Technology Platform for the Future of Textiles and Clothing (ETP) in two strategic programs: “Bio-Based Fibres” and “Circular Economy.” The two three-year ETP programs aim to bring key players from industry and science together to develop a long-term strategy to actively shape the sustainable realignment of the European textile industry.
“We have been manufacturing bio-based fibers for almost 85 years – these fibers are made from the renewable material wood and they are fully biodegradable at the end of their product lifecycle. As an alternative to crude-oil based materials, these fibers are becoming increasingly popular in various applications. Part of the reason for this is the fact that we can functionalize our specialty fibers during the production process and give them the exact properties that are required for different end uses. In terms of performance, they can keep up with synthetic materials,” explained Marina Crnoja-Cosic, Ph.D., head of New Business Development at Kelheim Fibres.
But Kelheim’s sustainability criteria also include the full life cycle of their products: When a textile, after its use, can become the raw material for new fibers and new products, for Crnoja-Cosic that is a huge advantage in terms of sustainability. “We want the best possible result – bio-based fibers and circular economy are the way to get there.”
Source: kelheim-fibres.com
EURATEX ReHubs aims to upcycle textile waste and circular materials in Europe
EURATEX, the European Apparel and Textile Confederation, proposes the development and set up of European Textile Recycling Hubs (ReHubs), with the aim of upcycling textile materials in Europe. According to EURATEX, the traditional linear textile business model (from virgin materials to products and then waste), results in high consumption of raw materials and generation of waste, which contributes significantly to the large and negative environmental impact of the global textile industry.
While apparel is only one of several textiles’ applications, the global apparel production and consumption appear to have doubled over the past 15 years, generating higher waste.
Even if the amount of textile waste separately collected in Europe has increased over the last five years from an estimated 2 mln tons in 2014 to 2.8 mln tons in 2019, this volume is expected to increase substantially once the EU waste legislation will be put into practice by the end of 2024.
In less than four years textile waste shall be collected separately and could total an amount between 4.2 to 5.5 mln tons which should be dealt with ideally within the EU. The ReHubs program aims to support this effort.
Source: euratex.eu
Techtextil NA to present webinars on sewing tech & advanced manufacturing through 3-D printing
Techtextil North America is offering a virtual conference Nov. 18-19, with sessions focused on Readily Available Sewing Technologies and Advanced Manufacturing Through Direct Write 3-D Printing. Techtextil kicked off a monthly webinar series in October, providing attendees the opportunity to learn from the brightest minds in both industry and academia. Divided into two tracks, each program is a carefully curated selection of sessions covering the most pivotal advancements in research and technology, exploring the latest trends and insights into the future of textile-related industries.
Readily Available Sewing Technologies will take place Nov. 18 at 2:30 PM EST. This presentation/panel hybrid session will explore the latest technology available to sew and seal materials, featuring a panel of experts who will each give a brief presentation on a specific technology in their wheelhouse, followed by a question-and-answer led discussion that will dive deeper into the efficiency improvements, production improvements, and maintenance impacts that are currently available in the sewing and sealing marketplace.
The session will be moderated by Dan Berzack, President, Sewn Products Equipment Company and feature a panel including:
- Rick Frye, Director of Engineering & Sales, Brother International Corp.
- Jairo Duran, Sales Manager, Juki
- Warren Shannon, Operations Manager, Mitsubishi Electric Industrial Sewing Machines
Advanced Manufacturing Through Direct-Write 3-D Printing will follow, taking place on Nov. 19 at 2:30 PM EST.
This highly technical session will explore the increasingly popular use of direct-write 3-D printing for the manufacture of a wide range of products for biomedical, electronic, and structural applications (among others). Learn what challenges remain in terms of process control, design of inks/paints, and the effects of process inherent heterogeneities, which are limiting the expansion of applications of this manufacturing approach.
The session will be moderated by Dr. Naresh Thadhani, Professor & Chair, School of Materials Science and Engineering, Georgia Institute of Technology and feature presentations by:
- Adam Jakus, Ph.D., Co-Founder & Chief Technology Officer, Dimension Inx
- Dr. Sabit Adanur, Professor, Samuel Ginn College of Engineering, Auburn University
- Dr. Jerry Qi , Professor and Woodruff Faculty Fellow, Woodruff School of Mechanical Engineering, Georgia Institute of Technology.
To explore the series and register for sessions, visit the Virtual Symposium microsite: https://techtextil-texprocess.us.messefrankfurt.com/atlanta/en.html.
The next edition of Techtextil North America will take place August 23-25, 2021 in Raleigh, North Carolina.
Source: techtextil-north-america.us.messefrankfurt.com
Fitesa’s new equipment investments and upgrades add 55,000 MT/year of spunmelt and meltblown capacity
Fitesa, a leading global supplier of spunmelt nonwovens, announced more information about new equipment and debottlenecking/upgrade projects that will increase the company’s capacity by 55,000 MT/year.
Latin America will lead the capacity expansion with a new multibeam Reicofil 5 line to be installed in Cosmópolis (Brazil). Construction is in an advanced stage and the line will arrive in July 2021. Once this new line is installed, the site will become the most advanced spunmelt nonwovens production location in the region, according to Fitesa.
In Gravataí (Brazil), one upgraded and redesigned meltblown line started 3 months ago to produce N95 meltblown grades and help the fight against COVID19. In addition to the above-mentioned line, one additional Reicofil meltblown line is being assembled to start before the end of 2020.
The total investment in the region will increase Fitesa’s production capacity by 30,000 MT/year and triple the company’s pure meltblown supply availability, fulfilling the rising demand from the healthcare and hygiene markets.
Stand-alone meltblown capacity is also being added in other regions, with new machine start-ups coming on stream in November 2020 at the plant in Trezzano Rosa (Italy), before Christmas 2020 in Peine (Germany) and in January 2021 in Simpsonville, South Carolina (USA). These lines will complement Fitesa’s product portfolio in Europe and North America with high-quality filters for surgical facemasks and respirators.
In addition to the above mentioned investments Fitesa is adding projects to increase production volumes, modernize the assets, and enhance the flexibility of the current asset base. As a result, in Q2 and Q3 2021 another 20,000 MT/year of spunmelt capacity (evenly split between the U.S. and Europe) will become commercial to continue serving the healthcare and hygiene markets with nonwovens for medical gowns, drapes, diapers and sanitary products.
“2020 has been a challenging year for all of us. I am pleased with our ability to respond fast in approving new investments that continue to expand our presence in the hygiene and healthcare markets, while also moving forward with important existing projects,” says Silverio Baranzano, Fitesa’s CEO. The aforementioned existing projects include the acquisition of Freudenberg Hygiene Brazil, Fiber Dynamics and Tredegar Personal Care, as well as the start-up of a new Reicofil 5 in November of 2020 in Thailand, which all together adds an additional 130,000 MT/year to the company’s portfolio.
By the end of 2020, Fitesa will have significantly increased its participation in the films and elastics market, while consolidating its position as one of the largest spunmelt manufacturers worldwide.
Source: fitesa.com
Ascend Performance Materials announces price increase for intermediate materials
The price increase takes effect immediately and includes the following terms:
Material |
Price Increase |
Terms |
Hexamethylene |
$350/MT |
|
Adiponitrile (ADN) |
$350/MT |
|
Acrylonitrile (AN) |
$200/MT |
|
Adipic Acid (AA) |
$100/MT |
|
Customers should contact their local sales representative for additional information.
Ascend Performance Materials makes high-performance materials for everyday essentials and new technologies. Based in Houston, Texas, and with regional offices in Shanghai, Brussels and Detroit, Ascend is a fully integrated material solutions provider with eight global manufacturing facilities in the United States, Europe and China. The company makes plastics, fabrics, fibers and chemicals used to make safer vehicles, cleaner energy, better medical devices, smarter appliances and longer-lasting apparel and consumer goods.
Source: ascendmaterials.com
Suominen upgrades line in South Carolina
Suominen increases its capabilities in the Americas by upgrading one of its production lines in Bethune, South Carolina, USA. The investment will widen Suominen’s offering to its customers in the US in line with the Suominen strategy targeting growth and profitability.
“This investment allows us to produce new innovative, top quality products which are the result of joint product development with one of our major customers,” says Petri Helsky, President and CEO of Suominen.
The total value of the investment is approx. EUR 6 million and the investment project will be finalized during the second half of 2021.
Source: suominen.fi
Indorama Ventures announces Q3 2020 financial results
Indorama Ventures Public Company Limited (IVL), a global chemical producer, has announced its third quarter 2020 financial results as follows:
3Q 2020 Performance Summary
- Reported net profit is THB 380 million in 3Q20 and THB 1,104 million for 9M20. Performance this year provided us significant insights into the growth of the future market, while the company remains on a path towards enhanced incremental performance progress, from 4% ROCE towards our target ROCE of 15% by 2023.
- In 3Q20 delivered record sales volume of 3.6 million tonnes, registering growth of 18% year-on-year (YoY). Sales volume grew to 3.2 million tonnes, or 4% YoY on a comparable basis.
- IVL achieved an operating cash flow of US$ 354 million in 3Q2020 while operating cash flow for 9M20 was US$994 million, thus providing ample liquidity of US$ 2.5 billion in cash and cash equivalents as well as unused credit lines.
- Project Olympus (a business transformation and cost excellence project) delivered a savings of US$ 21 million in 3Q20 and US$ 64 million in 9M20. Full year budget of US$ 76 million in savings is expected to exceed targets by over 15% in 2020 with relentless focus on multiple initiatives.
Outlook
- IVL has embarked in 2020 on a transformation journey that will enhance its business excellence and aims to deliver US$ 582 million of additional, sustainable, EBITDA by 2023. This target has been expanded from the US$ 352 million announced at our Capital Markets Day at the start of 2020 after a rigorous analysis process and the support of relevant domain experts to validate our operating teams’ initiatives in all of our three major business segments globally.
- IVL is making progress towards ESG targets and its pledge to recycle 750,000 tonnes of post-consumer PET, with a commitment of US$ 1.5 billion towards our ESG and recycling infrastructure globally by 2025.
- IVL strengthened leadership and recruited both digital and Lean Six Sigma function leaders to support technological adaption across IVL.
- IVL is well on its way to implement S4 Hana (ERP) across global operations and introduced a Global Business Service (GBS) office.
- IVL has organized IVL leadership in a clear manner to leverage and deliver performance. With Mr. DK Agarwal as CEO responsible for all three reporting segments and enabling functions under the Chief Strategy Officer. Meanwhile, the Chief Financial Officer and Chief Human Resources Officer are making appropriate governance structures for organizational effectiveness.
Source: indoramaventures.com
BGN Technologies, ECOIBÉRIA establish collaboration agreement to research PET biodegradation
BGN Technologies, the technology transfer company of Ben-Gurion University of the Negev (BGU), has signed a research collaboration agreement with ECOIBÉRIA in the field of plastic recycling by bacteria, based on research from the team of Prof. Ariel Kushmaro and Prof. Alex Sivan, both from the Laboratory of Environmental Biotechnology and Avram and Stella Goldstein-Goren Department of Biotechnology Engineering at BGU.
Polyethylene terephthalate (PET) is the most abundantly used polymer in the world, with multiple applications in the textile industry as well as in food and beverage packaging. It is estimated that about 56 million tons of PET are produced yearly worldwide, mostly as single use packaging material. Therefore, intense efforts are directed towards recycling and reuse of the PET plastic materials.
Prof.’s Kushmaro and Sivan and their team have been studying plastic biodegradation and have discovered several bacteria species that are able to biodegrade polyethylene, which was previously considered a non-biodegradable plastic mainly because of the highly stable carbon−carbon (C−C) bonds of the polymer backbone.
Based on these findings, the research collaboration project will assess the biodegradation of PET by previously identified bacteria as well as novel ones, with the aim of developing an efficient biodegradation process of PET whose products will be used as raw materials for recycled PET in the future.
“ECOIBÉRIA’s mission is to guarantee the sustainability of the production and consumption models and assist in the transition from the linear economy to the circular economy, through the transformation of PET plastic waste into valuable secondary raw materials,” said Mr. Jorge Lemos, CEO at ECOIBÉRIA. “We believe that BGU’s innovations in the field of bacterial biodegradation of PET complements our technologies and has the potential to become an important contribution to our plastic recycling efforts.”
Source: in.bgu.ac.il
INVISTA, Hengli announce licensing agreement around INVISTA’s P8 PTA
INVISTA’s technology and licensing group, INVISTA Performance Technologies (IPT), and Hengli Petrochemical (Huizhou) Co., Ltd, a subsidiary of Hengli Group (Hengli), have reached agreement to license INVISTA’s P8 PTA technology for two PTA (purified terephthalic acid) lines. These two lines will be installed at Xiachong, Daya Bay, Huizhou City, Guangdong province, China. The kick-off meeting was successfully concluded on October 23, 2020, between Hengli, INVISTA and CTCI (the engineering contractor).
Hengli is also operating another 5 PTA lines on Changxing Island (Dalian), all of which utilise advantaged INVISTA PTA technology, with a total capacity of 12 million tonnes per annum.
Adam Sackett, IPT vice president PTA, commented, “We are very pleased that our industry-leading P8 PTA technology has been selected again by Hengli Group. Our companies have a decade-long cooperation, and we look forward to working together on this new project, leverage the learning on Hengli PTA 4/5 and deliver a successful project.”
INVISTA’s industry-leading PTA technology, including its latest version of P8 technology, is available as a license package from IPT.
Source: ipt.invista.com
2020 ‘Hot Button Report and Ranking’ recognizes sustainability standouts in the viscose supply chain
Today, 52% of the global viscose supply has been deemed “green shirts” in the 2020 Hot Button Report and Ranking by environmental organization Canopy. This news represents a significant breakthrough for the fashion industry and the viscose supply chain.
A “green shirt” rating indicates that a producer has been audited and assessed as low risk, or has taken substantive action to eliminate known risk of sourcing rayon and viscose from ancient and endangered forests. Today’s report shows over half of the global viscose supply has attained that milestone and more than 90% of the entire viscose supply chain now has a publicly available CanopyStyle policy in place.
While eliminating ancient and endangered forests from the man-made cellulosic fiber (MMCF) supply is a crucial first step, it is actually the minimum bar of brands and producers’ CanopyStyle commitments. Canopy’s partners have also committed to investigating, trialing, and scaling up next-generation solutions. These NextGen Solutions include using recycled, post-consumer textiles, agricultural residues and/or microbial cellulose to make the pulp that forms the basis of MMCF fabrics like rayon and viscose. A third, and vital component of the CanopyStyle vision is translation of supply chain shifts into lasting conservation in critical forests around the globe.
“It’s incredible to see how quickly the majority of viscose production has moved, and now we need the rest of the industry to keep pace,” said Nicole Rycroft, Canopy’s Executive Director. “In addition to many of the leaders reducing risk, we’re buoyed by the substantive advancements of Next Generation Solutions, as well as conservation gains in key landscapes. This year’s Hot Button ranking is good news for all sustainability conscious brands, as well as for the world’s forests and climate.”
This announcement comes at a pivotal time as a majority of the 320 brands in the CanopyStyle initiative, worth 578 billion USD in revenue, are implementing their commitments to only source from producers ranked with green shirts. This includes companies as diverse as Inditex (parent company of Zara), Stella McCartney, Amazon, H&M, Levi’s, Target, Marks and Spencer, and Gap Inc.
The top-five fiber producers recognized on the Hot Button Report and Ranking include: Aditya Birla, Lenzing, Eastman Chemical Company, ENKA, and Kelheim Fibres.
Source: canopyplanet.org
Read the full report at: hotbutton.canopyplanet.org
Mogul invests in two new meltblown lines
Mogul has invested in two new meltblown nonwoven lines. Mogul Gaziantep facility will house the new investments. Both lines are 160 cm wide in 15-100 gram range with electrostatic charge capabilities. The lines will meet N95 and higher efficiency masks and high efficiency filter applications, as well as other industrial applications.
The first line will start by January 2021 and second line will start approximately June of 2021.
Source: mogulsb.com
DuPont Biomaterials, DyeCoo partner to provide sustainable dyeing solution for Sorona fabrics
DuPont Biomaterials and the Dutch company DyeCoo, specializing in the development of cleaner dyeing technologies, announced a patented, sustainable dyeing process for fabrics made from polyester or recycled polyester and Sorona. This dyeing solution enables fashion designers and brands to deliver high performance clothing and a lesser environmental footprint.
Fabrics made from a combination of Sorona with polyester or recycled polyester can be sustainably dyed on an industrial scale with the CO₂-based process, developed and patented by DyeCoo. This process uses no chemicals and no water, thus does not cause any wastewater and requires no wastewater treatment. The CO₂ used for the process is reclaimed from existing industrial processes, recycling 95% of it in a closed loop system.
Short batch cycles, efficient dye use, no wastewater treatment all contribute to significantly reduced operating costs and the ecological footprint, making this solution extremely appealing for mills, brands and consumers focused on sustainability.
The dyeing process applies reclaimed CO₂ as the dyeing medium in a closed loop process. Used in a pressurized, super-critical state, CO₂ has a very high solvent power, allowing the dye to dissolve easily. Thanks to the high permeability, the dyes are transported easily and deeply into fibers, creating vibrant colors. Reacting in a similar way to this dyeing process, polyester and Sorona fibers are perfectly matched in the creation of high-end fashion fabrics, which come with superior performance, higher quality and an extremely low ecological footprint.
Source: sorona.com
Sateri announces sustainability vision for 2030
Sateri, a major global viscose producer, announced its sustainability vision for 2030 to guide the company’s strategic growth in the coming decade. The vision is anchored around four key pillars in response to environmental and social challenges faced by the cellulosic fiber industry: Climate and Ecosystem Protection, Closed Loop Production, Innovation and Circularity, and Inclusive Growth.
The Vision comes with a time-bound roadmap and measurable targets. It encompasses notable targets including net-zero carbon emissions by 2050, achieving 98% sulphur recovery rate at all its
mills by 2025, utilizing textile waste and producing viscose products with 50% recycled content by 2025 and 100% by 2030, and supporting more than 300,000 local families and smallholder farmers to develop sustainable livelihoods.
Sateri’s 2030 Vision was conceived after months of discussions with management members and external stakeholders including customers, brands and NGOs. The process was facilitated by Jeremy Prepscius, vice preside of Asia Pacific for BSR, a sustainability consultancy.
Source: sateri.com