In the dynamic and global textile fiber industry with its various manufacturing processes and end-uses, news and information is breaking on a daily basis. International Fiber Journal is tracking stories relevant to our industry from manmade to natural to bio-based fibers, innovations in nonwoven, woven, braided and technical textiles, technologies for additives, bonding, coatings and polymers, and applications from apparel to hygiene to transportation, and more. Here we will post news stories relevant to textile fibers and their downstream applications on an ongoing basis. Please check back for regular updates. If you have news that you feel should be added to this summary report, please email it to Matt Migliore at mmigliore@inda.media.
Most recent update: August 31, 2021
US DoD, DHS award $6.5 M to US Cotton to boost polyester-tipped swab production
The Department of Defense (DOD), on behalf of and in coordination with the Department of Health and Human Services, awarded $6.5 million to U.S. Cotton, LLC, a subsidiary of Parkdale, Inc., to increase domestic production capacity of the polyester-tipped swabs used in COVID-19 home test kits and mass testing settings.
U.S. Cotton’s COVID-19 test swab is designed for hospital and laboratory settings and, when used at home, allows for an easier self-administered test. This industrial base expansion effort will allow U.S. Cotton to increase its production capacity from 92 million polyester swab tips per month to approximately 371 million polyester swab tips per month in Cleveland, Ohio, by May 2022 to support domestic COVID-19 testing.
The DOD’s Defense Assisted Acquisition Cell (DA2) led this effort in coordination with the Department of the Air Force’s Acquisition COVID-19 Task Force (DAF ACT). This effort was funded through the American Rescue Plan Act (ARPA) to enable and support domestic industrial base expansion for critical medical resources.
Source: defense.gov
British Textile Machinery Association names Jason Kent CEO
The British Textile Machinery Association (BTMA) announced Jason Kent has been appointed as Chief Executive Officer of the BTMA Group, which also includes subsidiaries nw texnet and The Textile Recorder (Machinery & Accessories) Exhibitions Ltd (TREX), effective from Monday 23rd August 2021.
Jason has been a non-executive member of the BTMA board for more than eight years and has spent 35 years working in the carpet tufting machinery industry.
As a time-served mechanical technician engineer, he ascended through a series of positions of greater responsibility with Cobble Blackburn until its acquisition in 2013 by the Vandewiele Group, where he undertook the role of Managing Director for the tufting machinery business.
He is also a Chartered Fellow of the Chartered Management Institute.
Founded in 1940, the British Textile Machinery Association actively promotes British textile machinery manufacturers and their products to the world. The non-profit organisation acts as a bridge between its members and the increasingly diverse industries within the textile manufacturing sector.
Source: btma.org.uk
Karl Mayer opens new headquarters in Obertshausen
The Karl Mayer Group opened its new headquarters in Obertshausen, Germany, with a building complex covering an area of 5,600 m². It is designed for 150 employees.
“We are looking forward to welcoming our international guests to a headquarters that, with its modern, transparent design and inspiring atmosphere, reflects the dynamics, cosmo-politanism and innovative strength of the Karl Mayer Group,” said its CFO Dr. Helmut Preßl.
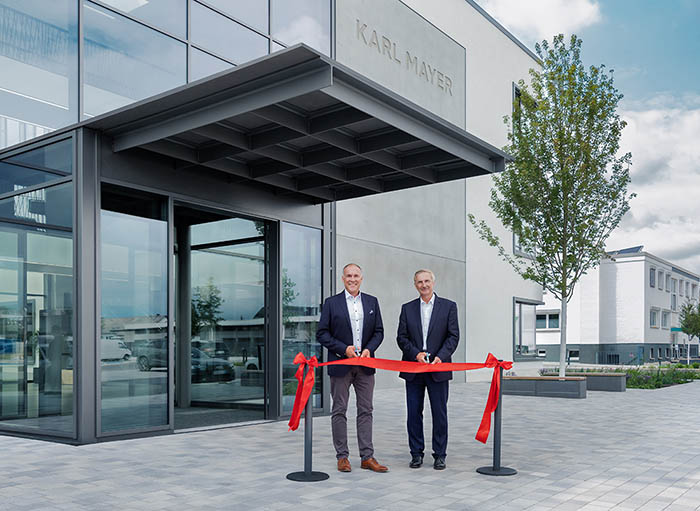
In the light-flooded foyer, a large media wall provides information on the latest news, and a showroom is dedicated to the company and family history. An Innovation Hub provides space and opportunities for new ideas and developments together with customers from all over the world.
Office areas, meeting rooms and places of retreat can be changed according to the situation by modifiable furnishing and seating arrangements. Open entrances, glazed walls and areas that can be used in a variety of ways promote communication “With our space and building concept, we want to promote a sense of togetherness and broaden horizons,” said Arno Gärtner, CEO of the Karl Mayer Group.
In addition to performance, the building has a low ecological footprint. Air-source heat pumps take care of the entire energy supply, economical, long-lasting LED technology reduces power consumption, and digitization means that work is paperless wherever legally possible. Recycled materials were used where practical and feasible. For example, the paving stones in the outdoor areas were already in use. Almost all roof surfaces are extensively greened, providing habitats for insects and retaining rainwater. In addition, all materials used meet the specifications for a healthy working climate, and all current legal requirements for thermal insulation are complied with.
Source: karlmayer.com
Beckmann Converting launches new website
Beckmann Converting, Inc, a laminator of textile composites specializing in ultrasonic bonding lamination, announced its newly redesigned website is now live at beckmannconverting.com.
“We believe that our new website, with leaner presentation and more effective navigation flows, will become an important resource for current and prospective customers,” said Ray Piascik, director of sales and marketing at Beckmann Converting. “Innovative modules including the ‘Buyer’s Journey’ and the ‘Virtual Swatchbook’ were created to give visitors direct access to critical information.”
A laminating program at Beckmann Converting could be driven by any one of three distinct groups of people in a customer’s organization, explained Piascik. The Buyer’s Journey provides three specially curated paths through the website – one for New Product Leaders, one for Manufacturing Capacity Leaders, and one for Supply Chain Leaders.
The Virtual Swatchbook provides descriptions and images of the roll patterns for ultrasonic laminating available at Beckmann Converting. Each roll pattern, with different shapes and spacing of weldpoints and bonded area as a percentage of total web area, has a downloadable and printable specification sheet accessible through the Swatchbook. A supplemental hard copy of textile samples showing the bond patterns can be requested from the company for use in conjunction with the online tool.
View the new site at: beckmannconverting.com (NOTE: If you’ve visited the site before, you may need to delete your web browser cache to load the new site.)
Dornbirn Global Fiber Congress releases program for 60th anniversary edition
Specialists in fiber and filament production for textiles and nonwovens will join academia in support of the 60th Dornbirn Global Fiber Congress, 15-17 September. The event will feature technical and scientific presentations, with 96 lectures over the course of three days in two virtual lecture halls.
The event will feature Robert van de Kerkhof, Lenzing AG, Uday Gil, Indorama, and a CEO Panel discussion on the first day.
Following lectures by Markus Mannström, Stora Enso, Eric le Lay, Huhtamaki, and Georg Stausberg, Oerlikon; Tobias Erikson, EFESO, will moderate the CEO Panel.
The Dornbirn GFC will also consider cross-sector innovation under the motto “Packaging Industry meets Fiber Industry,” as the two industries figure to play a large role in fostering sustainability and environmental stewardship in the years to come. In many cases both industries share the same/similar feedstock, production technologies, scope of applications and will face the same challenges when it comes to sustainability and circular economy.
A “Deep Dive Session“ – in cooperation with EDANA/Index and Dornbirn GFC – will offer four expert lectures in addition to the program on Friday. Results and opportunities for reuse and recycling of fibers from nonwovens will be presented and then discussed at a round table chaired by Pierre Wiertz, EDANA.
Ticket price for the Dornbirn GFC are 300 €. Expert lecture topics include:
-
- Fiber Innovation
- Sustainability and Circular Economy
- Apparel
- Surface Modification
- Nonwovens
- Machinery and Equipment
20 exhibitors will be available in the virtual exhibition hall.
View the full Dornbirn GFC program: https://www.dornbirn-gfc.com/fileadmin/documents/Programme/Programm_60th_Dornbirn_GFC_2021.pdf
Source: dornbirn-gfc.com
INDA releases World of Wipes 2021 conference content for on-demand viewing
INDA, the Association of the Nonwoven Fabrics Industry, announced “On-Demand” video access to presentations recorded from the 2021 World of Wipes (WOW) International Conference held July 12-15 in Atlanta. The program content includes sessions on: sustainability, market and consumer trends, industry policies and regulations, flushable wipes, and innovations in substrates, preservatives, and packaging. It also includes the product presentations and announcement of the World of Wipes Innovation Award and of the presentation of the INDA Lifetime Technical Achievement Award.
Each speaker’s presentation is approximately 30 minutes in length and includes Q&As recorded live following the session. The on-demand WOW program content is available for purchase and viewing for 90 days at https://www.pathlms.com/inda/courses.
“INDA’s 2021 World of Wipes ‘On-Demand’ video provides high-value business intel in a convenient, economical and efficient manner. Wipes industry participants worldwide can now experience the conference as if they were live in the front row,” said Dave Rousse, INDA’s president. “We are grateful for our 2021 World of Wipes Committee‘s leadership in developing this excellent program as it aligns with the INDA mission to address the key issues of the industry, stimulate innovation and recognize excellence,”
Professionals interested in advancing their knowledge of the multi-billion dollar wipes market sector may purchase the entire program containing 31 speaker presentations, or select among nine individual sessions here
Source: inda.org
* International Fiber Journal is owned by INDA, Association of the Nonwoven Fabrics Industry.
Oerlikon Manmade Fibers announces webinar series focused on services for manmade fiber systems
Oerlikon Group’s Manmade Fibers Solutions business unit will present a series of webinars focused on services for manmade fiber systems. Registration for the series is available at oerlikon.com/polymer-processing/en/about-us/events/. The series will focus on the following topics:
How ceramics within the yarn path improve the quality of your yarn
September 01, 2021: 2 – 2:45 p.m. CET
Catering to the ever-greater requirements in yarn quality and production speeds requires specially designed yarn guides made from new materials. They help optimize the yarn production process. Here, the yarn guide and yarn oiler become two of the most important components coming into contact with the yarn within spinning and texturing machines. Regional Service Sales Director Ingo Scholz and Technical Project Manager Michael Kochanek illuminate how the right selection of the ceramics used here can guarantee superlative yarn quality with maximum production speeds and outstanding durability.
myOerlikon – tailored digital services provide a comprehensive overview
September 13, 2021: 2 – 2:45 p.m. CET
Ingo Scholz, Regional Head of Service Sales at Oerlikon Barmag, and Oerlikon Neumag’s Regional Service Sales Manager Finn-Eric Jordt introduce the myOerlikon service portal and e-commerce platform. With this solution, Oerlikon customers across the globe have access to all machine and sales documents, drawings and operating instructions via the Web-based portal. The team of speakers from both brands will demonstrate how to quickly and easily order spare parts and how e-learning offerings, videos and machine-accompanying information can be accessed.
Always by your side – with Oerlikon Remote Services
September 22, 2021: 2 – 2:45 p.m. CET
Professional service is relevant in all phases of a system’s life. And it also plays a decisive role above all with regards to unforeseen events and incidents. Within the context of a presentation by Thomas Arnold, Head of Technical Services at Oerlikon Barmag, and Jan Pauer, Technical Service Manager for Modifications at Oerlikon Neumag, attendees will discover how yarn producers can utilize the Manmade Fibers Solutions business unit’s Remote Service to avoid longer downtimes.
Better safe than sorry – maximize productivity and minimize downtimes with regular machine check-ups
September 29, 2021: 2 – 2:45 p.m. CET
Superlative performance is the result of the interaction of numerous factors. Preventative equipment maintenance work is a simple way of avoiding unplanned machine downtimes. Oerlikon Neumag Expert for Industrial Services Christopher Hansen and Michael Schwarz, Technical Sales Manager for Modifications at Oerlikon Nonwoven, explain how services can be improved, future-proof system concepts developed and cost potentials tapped into.
Register now at: oerlikon.com/polymer-processing/en/about-us/events/
Source: oerlikon.com
Indorama Ventures agrees to buy Oxiteno
Indorama Venturas (IVL) has agreed to acquire Brazil-based Oxiteno S.A. Indústria e Comércio, a subsidiary of Ultrapar Participações S.A. IVL will purchase Oxiteno for $1.3 billion, with a deferred payment of $150 million in 2024. The transaction is subject to customary conditions to closing, including approval of relevant regulatory authorities. The transaction is expected to close in Q1 2022.
With 11 manufacturing plants, customers in four continents, and an experienced management team, Oxiteno will complement IOD’s footprint in the U.S and Latin America, while its five research and technology centers will add to IVL’s innovation credentials in green chemistry.
“This acquisition is a natural fit for us,” said Aloke Lohia, IVL Group CEO. “We have a solid track record of continuously driving value for shareholders through successfully integrating 50 acquisitions over the past 20 years. With Oxiteno, we are creating a global leader in surfactants. By bringing our companies together, we are strengthening our customer value proposition, our market reach, and our experienced team. Like us, Oxiteno grew as a family enterprise with an entrepreneurial mindset. The combination of our teams is unmatched in our industry, and we look forward welcoming them to our family.”
The acquisition gives IVL a portfolio in surfactants and extends its existing Integrated Oxides and Derivatives (IOD) business. IVL will gain customer relationships in Brazil, Uruguay and Mexico, as well as additional growth opportunities in end markets including the U.S. through a new facility in Pasadena, Texas.
IVL expects to realize synergies of $100 million by 2021 through portfolio adjustments, asset optimization and operational excellence.
Source: indoramaventures.com
VDMA WebTalk to focus on textile-reinforced concrete for sustainable building
Concrete is the most used construction material in building industry worldwide, but it is also a main driver for CO2 emissions. Textile concrete is clearly superior to classic reinforced concrete both economically and functionally. Textile concrete products are lighter and thinner, requiring up to 80% less concrete compared to classic reinforced concrete due to the corrosion-free nature of textile reinforcements.
On Sept. 2 at 2 p.m. CEST, VDMA will present its latest WebTalk, with a focus on the topic of textile-reinforced concrete. The program will feature the following sessions:
Production technologies for textile reinforced concrete – today and tomorrow
Typical production technologies and textile reinforcements will be shown as well as their dependencies on the intended application. An outlook on future production technologies, as 3D-printing of concrete and fiber reinforcements, will be given.
By Dr. Magdalena Kimm
ITA – Institut für Textiltechnik of RWTH Aachen University
Non-metallic reinforcement for sustainable concrete applications
By using carbon-, glass or basalt-reinforcements concrete structures can be designed much more slender, durable and ressource-saving than standard steel-reinforced constructions. The presentation shows what kind of reinforcements are on the market already, which are future possibilites as well as obstacles in todays building industry.
By Dr. Christian Kulas
Solidian
Eco-system for Textile Reinforced Concrete applications in the Building and Construction Sector in India and South East Asia
India and many South East Asian countries face serious challenges with corrosion of conventional reinforcement due to the tropical climate. Further on non-existance of proper building code for integration of textiles as reinforcements is an operational challenge. At Raina Industries, the constant endevour is to create an eco-system for the application of this new material in facades, street furniture, modular components and marine applications.
By Mohit Raina
Raina Industries
The sessions will be followed by a live Q&A.
Register for the WebTalk at: https://en.industryarena.com/vdma-textile-machinery/webinar/1373899363
Source: vdma.org
Hologenix named Inc. 5000 fastest-growing company for third year in a row
Hologenix, a developer of responsive-textile solutions and inventors of Celliant infrared textile technology, has been named to the Inc. 5000 list of America’s fastest-growing private companies for the third consecutive year. Hologenix’s profits grew 225% over the past three years and the company is ranked in the top half of the list this year.
“We are honored to be recognized for our continued growth and success as one of America’s fastest-growing companies by Inc.,” said Seth Casden, Hologenix Co-Founder and CEO. “We strive to develop new product solutions for the ever-changing marketplace and to broaden the uses of Celliant infrared technology and the health and wellness benefits it delivers. We are pleased Celliant is now a key ingredient in many brands across the globe, from clothing and bedding to furnishings and even space suits, with more applications on the horizon!”
Source: hologenixllc.com
Archroma announces CFO succession
Archroma announced that is has appointed Thomas Bucher as its new Chief Financial Officer (CFO) effective October 1, 2021, replacing Roland Waibel who will retire.
“I am very excited to join Archroma and a team who has shown amazing agility and market relevance in the recent years,” said Bucher, “transforming itself to operate ever more efficiently, profitably and sustainably.”
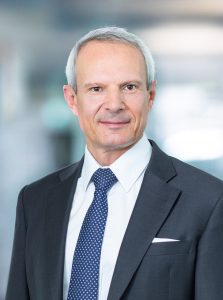
Thomas Bucher has held CFO roles with industrial and services companies as well as senior finance roles in the chemical sector. He joins Archroma from Alpiq Holding AG, where he has been Group CFO and a Member of the Executive Management Board since 2015. Prior to Alpiq, Bucher was Group CFO at Gategroup for 6 years, where he supported the company’s listing and subsequent strategic repositioning, and before that he held a number of senior finance roles at Ciba Specialty Chemicals over more than 12 years.
“We are very happy to have Thomas Bucher join us, and add his financial expertise to support our agenda towards confirming Archroma as an undisputed leader in innovative and sustainable specialty chemicals, supported by solid and profitable growth,” said Chief Executive Officer Heike van de Kerkhof.
Source: archroma.com
lululemon, Genomatica partner to create sustainable, bio-based nylon
lululemon athletica inc. announced a multi-year collaboration with sustainable materials provider Genomatica to bring renewably sourced, bio-based materials into lululemon’s products. This represents lululemon’s first-ever equity investment in a sustainable materials company and Genomatica’s largest partnership within the retail industry. Together, the two companies will aim to create a lower-impact, plant-based nylon to replace conventional nylon, which is the largest volume of synthetic material currently used to make lululemon products.
Genomatica uses biotechnology and fermentation to convert plant-based ingredients into widely used chemical building blocks, like those used to make nylon. These building blocks are converted to pellets and yarns, and the companies will be working closely with lululemon’s fabric supply chain to incorporate this material into future products. Through this collaboration, the companies seek to create positive change within the $22B global nylon market by building more sustainable supply chains.
In October 2020, lululemon released its first-ever Impact Agenda, outlining social and environmental goals and multi-year strategies toward a more equitable, sustainable, and healthy future. The collaboration with Genomatica is one of several ways lululemon is bringing new, sustainable innovation to its raw materials. Additional examples include the company’s partnership with Mylo, to use a mycelium-based leather, and LanzaTech, for polyester made using recycled carbon emissions.
Source: lululemon.com & genomatica.com
Rieter to acquire three businesses to support its ring and compact spinning systems
Rieter Holding Ltd. and Saurer Intelligent Technology Co. Ltd. signed an agreement by which Rieter will acquire three businesses from Saurer Netherlands Machinery Company B.V., Amsterdam/Netherlands, the parent company of Saurer Spinning Solutions GmbH & Co. KG, Uebach-Palenberg/Germany and Saurer Technologies GmbH & Co. KG, Krefeld/Germany.
With this acquisition, Rieter will complete the offering of ring- and compact spinning systems by acquiring the Schlafhorst automatic winder business. In addition, Rieter will invest in two component businesses: Accotex (elastomer components for spinning machines) and Temco (bearing solutions for filament machines).
In total, the three businesses had a combined turnover of EUR 142 million in 2020 (impacted by the COVID-19 pandemic). In 2019 and 2018, the total combined turnover was at a level of EUR 235 million and EUR 260 million, respectively.
The purchase price for the three businesses is EUR 300 million on a cash and debt free basis. Rieter has financed the purchase price by cash and available credit lines.
Rieter and Saurer expect to close the transaction during the month of August. In the first step of the transaction, Rieter will acquire 57% of the shares of Saurer Netherlands. The shares will be returned to Saurer after the implementation of the transaction in six to nine months.
In connection with the transaction, it is envisaged that Rieter will supply automatic winders to Saurer in the future.
In related news, Reiter announced Luc Tack and Stefaan Haspeslagh, two members of its board of directors, would be dismissed and have a criminal complaint filed against them for using confidential information during the course of the transaction to compete with Reiter.
Source: rieter.com
AATCC releases test method for measuring fiber shedding
AATCC TM212-2021, Test Method for Fiber Fragment Release During Home Laundering, provides a standardized method for quantifying fiber fragment shedding in the ongoing challenge to combat aquatic pollution. These fragments are sometimes referred to as “microfibers” or “microplastics.”
AATCC TM212 was developed to provide a means to determine the mass of fiber fragments released in an accelerated laundering setting.
AATCC TM212 defines standard nomenclature with the terms fiber fragment and microfiber, which address discrepancies that have long been a source of confusion for many who work to tackle pollution. Originally assumed to be a plastics problem, natural fibers are also appearing in marine life’s food cycle. AATCC TM212 is not limited to man-made fibers, as it can be used to determine the fiber shedding potential of natural fibers and blends.
The standard is the result of collaboration, not only within AATCC committee RA100 Global Sustainability, but among stakeholders from several organizations, including The Microfibre Consortium, headquartered in the UK, and the Cross Industry Agreement of European signatories. The outgoing Chair of RA100, Heather Elliot of Adidas, said, “Thank you to everyone who helped make this test method happen. It has been years in the making and would never have happened without the hands and minds of so many amazing people. We can’t thank you enough! Here’s to measuring our mess so we can figure out how to clean it up!”
The incoming Chair of RA100, Shulong Li of Milliken, said, “Small fiber fragments in the environment is an emerging and serious concern that raises heightened public attention. TM212-2021 results from extensive collaboration representing a broad range of stakeholders in the textile industry, public and private institutions, and technical experts in the Global Sustainability committee. This new standard method provides a common and useful tool for the textile industry to gain a better understanding of the issues.”
Although unofficial and proprietary methods have been in use, AATCC TM212 is the first global standard published to address the issue of quantifying fiber fragment release. The test method was developed and approved by consensus from a diverse group of experts from around the world and across related industries.
AATCC TM212-2021 Is now available for purchase through the AATCC website at: https://members.aatcc.org/store/tm212/3573/. It will also be included in the AATCC 2022 Manual of International Test Methods and Procedures released January 2022.
Source: aatcc.org
ASTM developing test method to aid in determining certain cotton fiber quality metrics
A proposed ASTM International standard test method will cover the determination of maturity, fineness, ribbon width, and specific surface area (micronaire) of cotton fibers.
Under development of ASTM International’s textiles committee, the test method focuses on cotton fibers from a loose, chemically untreated sample taken before harvest, during ginning, during mill processing, or unraveled from raw yarn or fabric.
“The cross-sectional properties of cotton fibers are important across the cotton supply chain from breeding through to textile production and fabric appearance,” said Stuart Gordon, team leader at CSIRO Agriculture and Food. “A standard such as this that provides direct and quick assessment of a cotton fiber sample’s properties has been a long-held ambition of the international cotton industry.”
According to Gordon, research laboratories, cotton merchants and spinners, and regulatory bodies will benefit from this proposed standard test method. Because the examination can be applied to fibers unraveled from yarn in a textile, the standard also has application in the forensic examination of textiles for quality assurance and identification purposes.
This effort directly relates to the United Nations Sustainable Development Goal #12 on responsible consumption and production.
Source: astm.org
KBR to provide chemical recycling technology for new TreeToTexile fiber plant in Sweden
KBR announced signed a technology contract for a sustainable textile fibers demonstration plant to be built by TreeToTextile AB in Nymölla, Sweden.
KBR will provide technology license, engineering, proprietary equipment, and commissioning services for the chemicals recovery unit of the project, which will enable TreeToTextile to efficiently and sustainably reuse chemicals through KBR’s Ecoplanning solutions.
“We are honored to support this exciting project by TreeToTextile for producing a highly sustainable low-cost textile fiber using renewable forest materials,” said Doug Kelly, KBR President, Technology. “KBR is committed to expanding its sustainable technologies portfolio to help our clients balance their business and ESG objectives.”
KBR Ecoplanning has over 50 years of experience in the design and supply of evaporation and crystallization technologies and has supplied over 200 plants globally across diverse applications and industry segments, including fertilizers, metallurgical, pulp and paper, chemicals, food, and others.
Source: kbr.com
NatureWorks passes final authorization milestone for Ingeo PLA manufacturing plant in Thailand
Continuing its global manufacturing expansion plan, NatureWorks, a leading manufacturer of low-carbon polylactic acid (PLA) biopolymers made from renewable resources, has obtained final authorization from parent companies, GC International Corporation Company Limited, a subsidiary of PTT Global Chemical Public Company Limited (GC) and Cargill Incorporated (Cargill), to build a new Ingeo PLA manufacturing complex in Thailand. NatureWorks plans to invest in excess of $600 million to construct the complex, which will include production sites for lactic acid, lactide, and polymer, making it the world’s first PLA facility designed to be fully integrated, according to the company.
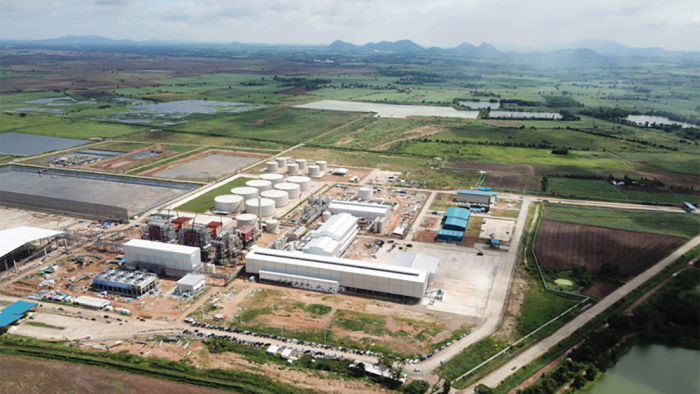
Construction of the new manufacturing complex to be located at the Nakhon Sawan Biocomplex (NBC) in Nakhon Sawan Province will begin in the second quarter of 2022. With an expected opening in 2024, the facility will have an annual capacity of 75,000 tons of Ingeo biopolymer and produce the full portfolio of Ingeo grades.
Following this shareholder approval, NatureWorks has also selected engineering partners for the next project phase. Jacobs previously provided the front-end engineering design for the new manufacturing site and will now complete final detailed engineering for the project. Additionally, IAG, has been chosen to partner with NatureWorks on engineering and construction, providing project management, project controls, and procurement services. Both companies were chosen due to their expertise in executing large global capital projects.
In 2002, NatureWorks became the first company to produce PLA biopolymers at commercial scale. In 2013, NatureWorks expanded its flagship Blair, Nebraska facility to an annual total capacity of 150,000 metric tons, making it the largest PLA manufacturing plant in the world. NatureWorks also announced a capacity expansion in 2020 at its Blair facility to further increase the availability of Ingeo biopolymers.
The expanded global production of Ingeo biopolymers will support growth in markets including 3D printing and hygiene as well as compostable coffee capsules, tea bags, flexible packaging, and food serviceware that demand sustainable, low-carbon materials and require the high-performance attributes that Ingeo is uniquely suited to deliver.
Source: natureworksllc.com
New book focuses on natural fiber composites for automotive components
The need to find a sustainable alternative to the man-made fibers used in reinforcing composites has led the automotive manufacturers and parts suppliers to shift to natural fiber reinforcements. Early versions of natural fiber composite (NFC) were only limited to non-structural parts; however, with ongoing intensive research, the idea to use NFC in more structural and exterior parts is rapidly expanding.
A new book, “Manufacturing Automotive Components from Sustainable Natural Fiber Composites,” published by Springer Nature, provides a comprehensive and integrated review on recent practices using natural fiber composites in automotive industry. The text is authored by Lobna A. ElSeify, a teaching and research assistant at the Faculty of Engineering and Materials Science at the German University in Cairo (GUC), Mohamad Midani, Ph.D., an assistant professor in the Materials Engineering Department, German University Cairo, and Adjunct Assistant Professor at Wilson College of Textiles, North Carolina State University, Prof. Ayman El-Badawy, Ph.D., a professor and department head of Mechatronics Engineering, and vice dean for Academic Affairs of the Faculty of Engineering and Materials Science, German University in Cairo, and Mohammad Jawaid, Ph.D., Highflyer Fellow (Professor) at Biocomposite Technology Laboratory, Institute of Tropical Forestry and Forest Products (INTROP), Universiti Putra Malaysia.
For more information: https://link.springer.com/book/10.1007/978-3-030-83025-0
NCTO welcomes Senate passage of U.S. infrastructure bill, funding to bolster domestic PPE supply
The National Council of Textile Organizations (NCTO), which represents U.S. textile manufacturers from fiber through finished products, issued a statement welcoming Senate passage of a bipartisan infrastructure bill that will provide billions of dollars in new spending with the aim of revitalizing the nation’s roads, bridges and railways and help reconstitute a domestic supply chain for personal protective equipment (PPE).
“We commend the Senate for passing the bipartisan infrastructure bill, which will provide critical resources for our nation’s aging infrastructure and at the same time help incentivize the reshoring of personal protective equipment (PPE) production, an important priority of the U.S. textile industry,” said NCTO president and CEO Kim Glas.
NCTO worked with congressional allies to include a version of the Make PPE in America Act, legislation co-sponsored by Senator Rob Portman (R-OH) and Senator Gary Peters (D-MI), in the infrastructure legislative package. The bill ensures all PPE purchased by the Departments of Homeland Security, Health and Human Services and Veterans Affairs are Berry Amendment-compliant; guarantees long-term contracts (a minimum of two years) to U.S. manufacturers; and creates a tiered preference for PPE made in the Western Hemisphere by our free trade partners using U.S. components, after domestic manufacturing capacity has been maximized.
“We sincerely thank Senator Portman and Senator Peters for working to include their Make PPE in America Act in the infrastructure bill,” Glas said. “This bill will help onshore critical production of personal protective equipment (PPE) by guaranteeing long-term contracts for domestically produced PPE and ensuring that taxpayer dollars are utilized to bolster the federal purchase of American-made PPE.”
Source: ncto.org
H.B. Fuller to build new facility in Egypt
H.B. Fuller announced an investment to build a new facility in Cairo, Egypt to support customers in Egypt, Turkey, the Middle East and Africa. The new factory will become a regional supply hub for adhesives serving various industries, including hygiene, packaging, labeling, paper converting and graphic arts.
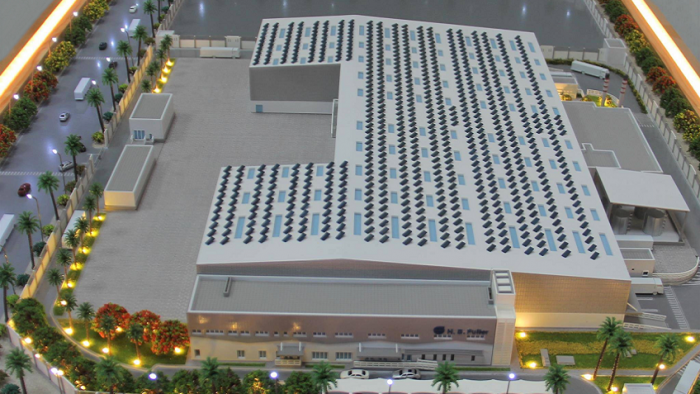
“Egypt has naturally become a main gateway to the region and with the new plant, we will extend our current leadership in Egypt and Turkey and grow our competitive position across the emerging markets of Middle East and Africa”, said Harsh Gupta, H.B. Fuller’s managing director for India, Middle East and Africa. “Our expanded presence in Cairo, with a high-tech site designed with future growth in mind allows us to double our production capacity and advance our technologies. This investment represents our commitment to better serving our customer base in close proximity to where they operate, for example in the markets for hygiene and packaging.”
The two-story, 37,000 m2 planned site will be built at the CPC Industrial Park in Cairo and will be designed to fulfill sustainability standards. Full production will commence in the last quarter of 2022.
Source: hbfuller.com
Indorama reports record results for Q2; expects continued growth through 2021-2022
Indorama Ventures Public Company Limited (IVL), a global chemical producer, announced its second quarter 2021 financial results, reporting a record Core EBITDA of US$477 million as major economies recovered from the COVID-19 pandemic and drove demand for products across IVL’s businesses. IVL is forecasting similar strong growth in the second half of 2021 and in 2022 as global vaccination programs spur positive sentiment.
Performance Summary
-
-
- Consolidated Revenue of US $3,559M, an increase of 10% QoQ and up 52% YoY
- EBITDA of US$ 552M and Core EBITDA of US$ 477M
- Net profit of THB 8,340M, a growth of 39% QoQ, and compared to THB 154M a year earlier
- Core ROCE of 12.9%, up 443 basis points (bps) QoQ and up 715 bps YoY
- Project Olympus, the company’s cost saving and business transformation project, yielded US$ 116M in efficiency gains in 1H21, on track to 2021 target of US$ 287M
- Acquisition of CarbonLite’s recycled PET asset in United States, making IVL the largest global producer of rPET resin
-
IVL delivered standout results in 2Q 2021 and a record Core EBITDA of US$477 million. The Americas and EMEA yielded record results in Q2, performing 59% higher Core EBITDA in first half 2021 compared to first half 2020, while Asia grew by 15%. In 2020, IVL’s businesses passed the test of resiliency, and this first half of 2021 has highlighted the value creation coming from our platform.
“Demand for our products remained robust across all segments and all regions,” said Aloke Lohia, group CEO of Indorama Ventures. “We achieved higher margins along our portfolio, leveraging on our integrated operating model and regional supply chain advantage offsetting headwinds in the ecosystem such as shortages of key raw materials and logistics constraints. In an environment of major disruption, IVL’s management has demonstrated agility in responsibly navigating the ecosystem and continuing to provide value to customers.”
The remainder of 2021 is expected to parallel the first half on the back of continued strong demand in our products from opening of travel with widespread vaccination and immunity.
Source: indoramaventures.com
Andritz to supply textile recycling line to Renaissance Textile
Andritz has received an order from Renaissance Textile to deliver a complete recycling line for its first recycling platform in Laval, France. Post-consumer waste fibers will be opened, mixed with virgin fibers and spun once again in order to produce new textiles.
“We were looking for a partner who is able to deliver tailor-made, sustainable solutions for our project,” Christophe Lambert, president of Renaissance Textiles, said. “We had already heard about the Andritz Laroche expertise, and that’s why we started running trials at their technical center. We quickly saw they were the right partner for us and that we could rely on the full support of their process experts.”
Renaissance Textile’s target is to become the first French recycling platform dedicated to end-of-line textiles and the company will soon open the new 12,000 sqm plant. Start-up of the line is scheduled for the end of Q2 2022.
Source: andritz.com
FET installs new meltspinning system at NIRI
Fiber Extrusion Technology Ltd (FET) has installed a new meltspinning system to upgrade research facilities at the Nonwovens Innovation & Research Institute Ltd (NIRI).
The installation comprises a FET-102 Series Laboratory Meltblown Spinning System and FET-103 Monofilament Meltspinning System. The equipment enhances NIRI’s pilot facilities and analytical laboratory, with the FET meltblown system to be utilized for R&D, pilot projects, and sampling.
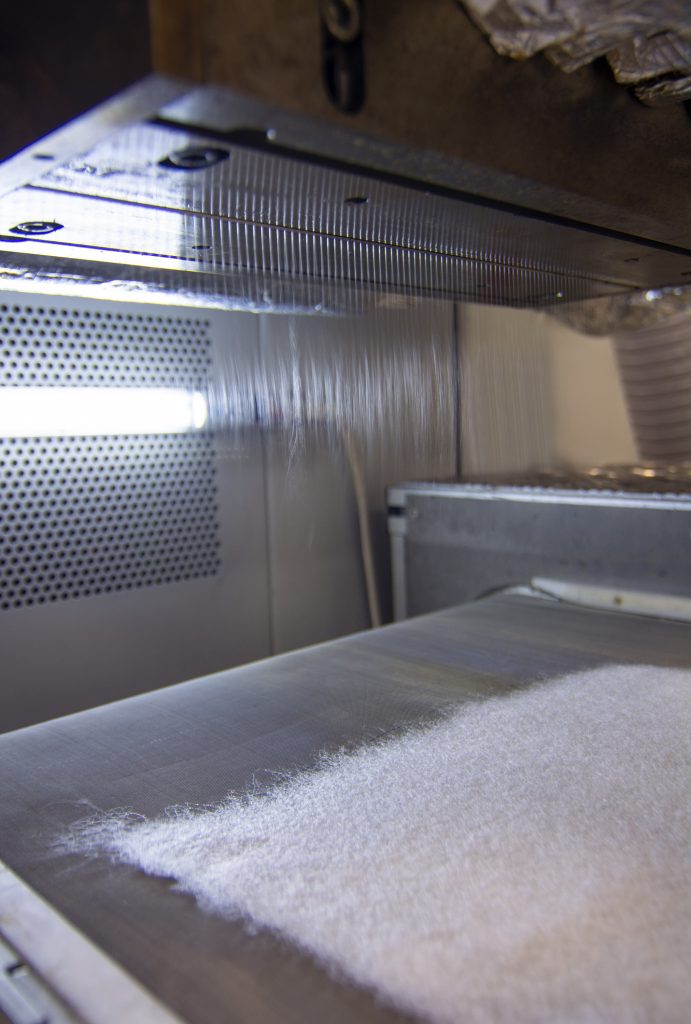
“We are absolutely delighted to secure this order with such a prestigious research organization as NIRI, a reflection of much hard work and a sign that FET is moving in the right direction in a fast-changing world of textile development,” said FET’s managing director Richard Slack. “In particular, NIRI had a requirement to invest in the most flexible and adaptable meltspinning technology available and FET was able to satisfy this priority.”
FET’s technologies and pilot system will allow NIRI to process a wide range of polymer types, including chemically recycled polymers and bio-polymers.
Source: fetuk.com
Glatfelter reports Q2 2021 results; gains driven by increases in Composite Fibers and Airlaid Materials businesses
Glatfelter Corporation, a global supplier of engineered materials, reported net income for the three months ended June 30, 2021 of $1.5 million, or $0.03 per diluted share, compared
with a loss of $2.3 million, or a loss of $0.05 per share, in the same period a year ago. The results include the acquisition of Georgia Pacific’s U.S. nonwovens business (“Mount Holly”) effective May 13, 2021.
Adjusted earnings from continuing operations for the three months ended June 30, 2021 and 2020, were $8.0 million, or $0.18 per share, compared with $9.9 million, or $0.22 per share, respectively. Adjusted earnings is a non-GAAP financial measure for which a reconciliation to the nearest GAAP-based measure is provided within this release. Consolidated net sales for the three months ended June 30, 2021 totaled $244.9 million, compared with $216.2 million for the same period in 2020. On a constant currency basis, net sales for Composite Fibers and Airlaid Materials (including Mount Holly) increased by 7.1% and 5.0%, respectively.
“Despite entering the second quarter expecting continued softer demand from customer destocking, Airlaid Materials recorded higher than expected volume growth driven by a rebound in tabletop products as in-person dining began to recover globally,” said Dante C. Parrini, chairman and CEO of Glatfelter. “The higher volumes, combined with increased production and a strong contribution from Mount Holly, propelled Glatfelter to deliver positive overall results compared to expectations.”
Parrini added, “In Composite Fibers, shipments were up slightly from the first quarter and our team continues to successfully implement the cost-related price increases we announced earlier this year. While our pricing actions only partially offset the rise in costs of raw materials, energy, and freight, we expect the benefit of our price increases to be more fully realized in the second half of 2021, further counteracting inflationary pressures in this segment. We remain disciplined in our approach toward managing costs throughout the entire supply chain while ensuring continued and timely delivery of high-quality products to our customers.”
“While we have been navigating the dynamic supply and demand environment stemming from the pandemic, our team remains committed to Glatfelter’s ongoing business transformation by making significant progress in executing our growth strategy. The newly-acquired Mount Holly facility made an immediate contribution to our Airlaid segment, and it strategically positions us to participate in the growing demand within health and hygiene categories. Of additional importance, on July 22, we announced the acquisition of Jacob Holm, a global leading manufacturer of premium quality spunlace nonwovens. This transaction will further diversify our end markets and technologies, enhance our overall innovation capabilities and add meaningful scale to the company.”
Source: glatfelter.com
Andritz signs cooperation agreement on textile recycling with Circ
Andritz has signed a cooperation agreement with Circ LLC to bundle resources in the field of textile recycling and to upscale Circ’s recycling technology for commercial use.
Circ has developed and patented textile recycling technology to separate and recover various raw materials used in most fabrics and in textile production. This process mainly focuses on the handling of mixed polymer streams, specifically any blend of polyester and cotton. As part of the agreement, Andritz will engineer, design, manufacture and start up the process equipment for the first demonstration plant and other commercial textile recycling facilities and provide support.
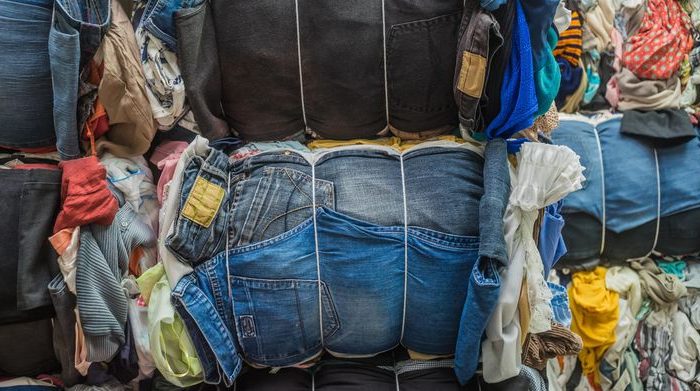
“Andritz has global reach, depth of expertise, and a solid reputation for executing world-class projects,” Dr. Julie Willoughby, Circ’s chief scientific officer, said. “The Andritz team is working shoulder-to-shoulder with Circ to implement our vision of a circular economy for textiles and other materials. We are delighted with the high competence of the Andritz staff, and we are more than excited about our next chapters together.”
The agreement comes after successful Circ processing trials in various Andritz research and development facilities.
“We have already been very active in the recycling of various waste streams for different industries,”says Wolfgang Lashofer, senior vice president and division manager of Paper, Fiber and Recycling. “We know about the importance of recovering raw materials in order to maintain value. The cooperation with Circ will enable us to further focus on the rapidly growing textile recycling sector.”
Source: andritz.com
Lenzing reports double-digit growth for Veocel in Asia, sees bright future for lyocell in the region
Lenzing reported its Veocel brand has recorded double-digit growth in Asia over the past year, compared to the pre-pandemic period. It is expected that the high demand for personal hygiene products in Asia will continue, even after the pandemic’s immediate impact lessens, whilst the beauty care segment is also forecasted for high growth.
In particular, the beauty care product trend has started to gain more prevalence in Southeast Asia, according to Lenzing. Strong growth potential is driven by the rise of environmental consciousness among younger consumers, and Veocel has been actively expanding its partner and customer networks in the region.
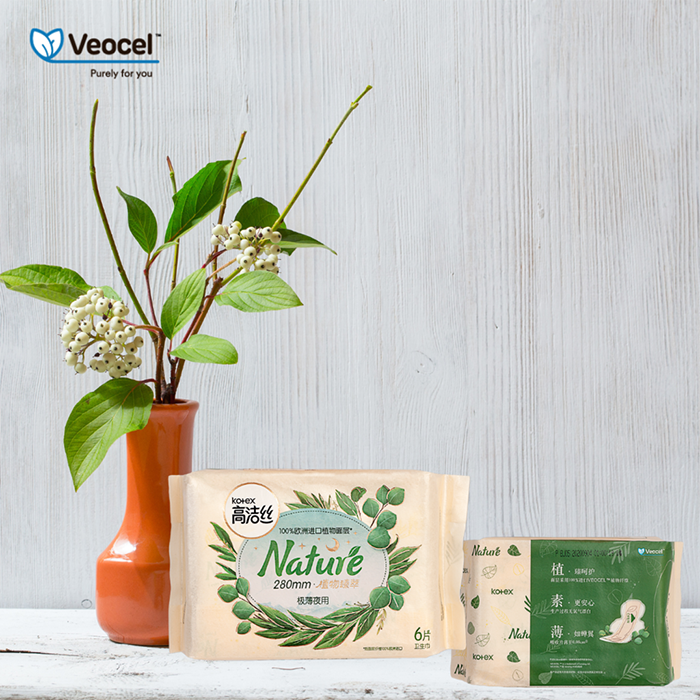
Steven Tsai, senior regional commercial director for Nonwovens Asia at Lenzing said, “We have observed a significant behavioral change in consumers since the beginning of the pandemic. As people spend more time at home, they are prioritizing self-care, causing them to invest in products which will improve their personal well-being. Globally, Veocel has three core segments – Personal Hygiene, Beauty Care, and Wipes. In Asia specifically, we are seeing high growth potential in the beauty care segment with an increased demand for facial sheet masks and facial cleansing wipes, as well as in the hygiene market where more consumers are prioritizing their health and cleanliness.”
Since the introduction of the Veocel certification criteria in July 2019, the Veocel brand logo has been featured on personal hygiene and beauty care products made from its cellulosic and biodegradable fiber materials.
Veocel branded lyocell fibers are currently used in Asian facial sheet mask brands like Annie’s Way, Sensatia Botanicals and Watsons’ HA facial sheet mask collection.
Feminine hygiene product brands such as Yejimiin Forest Story in Korea and Kotex Nature in China also use Veocel-branded lyocell fibers as the top sheet of their sanitary napkins.
With the European Commission’s recent Single-Use Plastics Directive (SUPD) confirming lyocell as a sustainable alternative to materials commonly used in single-use plastics, Lenzing expects Veocel to have new business opportunities in Asia.
“The EU SUPD has set a new industry standard which is expected to positively impact Asia as well. We hope the directive will encourage brands and business partners to re-evaluate global best practices and switch to more eco-friendly alternatives, such as Veocel-branded Lyocell fibers,” Tsai commented. “We believe the demand for sustainable non-plastic nonwovens from renewable sources will continue to increase. We are currently exploring the unlimited possibilities of eco-friendly nonwovens fiber to support the growing demand for sustainable materials in Asia.’
Source: lenzing.com
PolyQuest promotes Ryan Nettles, Brad Willingham to senior vice president roles
PolyQuest, a leading distributor of PET resins and manufacturer of recycled PET resins in North America, announces the promotion of Ryan Nettles and Brad Willingham to senior vice presidents.
Joining PolyQuest in 2006, Nettles has worked in the company’s manufacturing and warehousing operations. With his oversight, the company has grown its recycled production capacity to over 160 million pounds per year and has become the trusted provider of rPET flake, rPET resins, and toll processor of waste streams to our customers. In his new role as senior vice president for Operations & Recycle, Nettles will continue to lead PolyQuest’s operational and recycling efforts, contributing to strategic initiatives with business partners, enhancing product quality and performance while also driving continuous improvement across the company’s recycling division.
Brad Willingham joined PolyQuest in 2014, leading the development of new business for the company. During his tenure, Willingham has expanded PolyQuest’s footprint into the specialty PET, post-industrial rPET, polystyrene, and polypropylene markets. Willingham has generated incremental value for the business partners of PolyQuest. In his new role as senior vice president for Business Development, Brad will continue to drive growth into new products and markets for PolyQuest.
“Ryan and Brad have both exhibited outstanding leadership within our company,” said Tod Durst, president of PolyQuest. “Their consistent interface with customers, suppliers, and other business partners is consistent with our core values and a primary reason we have been able to successfully expand our business over the last decade. There is tremendous opportunity for PolyQuest to continue to grow in a variety of areas including the distribution of virgin polyethylene resins and enhancement of our well-established business in recycled PET with Ryan and Brad at the forefront of realizing our true growth potential.”
Source: polyquest.com
Orders up for Italian textile machinery suppliers; uncertainty persists
The index of orders intake for Italian textile machinery, as processed by ACIMIT, the Association of Italian Textile Machinery Manufacturers, for the period ranging from April-June 2021, was up 214% compared to the same 2020 period. The value of the index was attested at 150.7 points (basis: 2015 = 100), a result that was no doubt influenced by the comparison with a quarter, from April-June 2020, in which orders were at a minimum due to the Covid-19 pandemic.
An analysis of the index of orders intake for the first six months of 2021 confirms a clearly positive business dynamic for Italian manufacturers. An overall growth rate of 122% compared to the first half of 2020 regarded both the domestic and export markets.
Alessandro Zucchi, president of ACIMIT, said: “The data are certainly positive, bearing witness to a renewed climate of confidence.” On the domestic market, in addition to a physiological rebound following the collapse in 2020, the boost generated by Industry 4.0 incentives is being felt. “The push towards digitalization in the business sector is being perceived as creating a competitive edge for the entire textile industry, especially here in Italy,” added Zucchi.
In spite of these encouraging signals, a sense of uncertainty persists nonetheless on the actual solidity of this recovery. “There is no lack of obstacles facing our machinery producers during this phase,” said Zucchi. “The sharp rise in the price of raw materials does not seem to be stopping, to which we can add the limited availability of components, making it difficult for our manufacturers to fulfil the many orders they’ve received. Finally, the limitations imposed on the business travels of our staff persist, above all qualified assembly technicians.”
These are all issues that are expected to affect the sector’s order forecasts for the third quarter of 2021. To this end, ACIMIT’s survey have revealed a substantial stability compared to the previous three months for domestic orders (as expressed by 59% of companies), and a prevailing caution also abroad, where forecasts of stable or decreasing orders make up 74% of the answers provided by Italian companies in the sector.
Source: acimit.it
EDANA, INDA release updated Nonwovens Standard Procedures
EDANA and INDA, the associations representing the nonwovens industry in Europe and North America, respectively, announced the launch of the 2021 edition of standard procedures for the nonwovens and related industries.
The Nonwovens Standard Procedures are designed to help technically define the nonwovens industry, with specifiers for the properties, composition, and specifications of its products. Offering harmonized language for the industry across the U.S. and Europe, and recognized by many other individual markets, the procedures offer a way for the nonwovens industry to communicate both across the globe, and within the supply chain to ensure that product properties can be consistently described, produced and tested.
The harmonized methods contained in the Nonwovens Standard Procedures (NWSP) edition include 107 individual test procedures and guidance documents to support applications across the nonwovens and related industries, and are available on both www.inda.org and www.edana.org.
The 2021 edition includes updated or modified procedures with a numbering structure that makes the document intuitive to search and use. Additionally, each method also includes a page to summarize and track relevant changes made to the document. In an effort to make all methods more consistent, each one is now presented in a format building on the International Standards Organisation (ISO) template, facilitating any future possible submission to ISO in an effort to become a recognized international standard or technical specification.
As in previous editions, the table of contents for the Nonwoven Standard Procedures document includes references to existing related ISO standards, which makes it easier for technicians to choose the most relevant procedure or methods to apply to their product.
Source: inda.org and edana.org
* International Fiber Journal is owned by INDA, Association of the Nonwoven Fabrics Industry (inda.org).
Kimberly-Clark reports Q2 financial results
Executive summary
-
-
- Second quarter 2021 net sales of $4.7 billion increased 2% compared to the year-ago period, with an organic sales decline of 3%
- Diluted net income per share for the second quarter was $1.19 in 2021 compared to $1.99 in 2020.
- Second quarter adjusted earnings per share were $1.47 in 2021 compared to $2.20 in 2020.
- Diluted net income per share for 2021 is anticipated to be $6.00-$6.50.
- The company is now targeting full-year 2021 organic sales decline of 0-2% and adjusted earnings per share of $6.65-$6.90. The prior outlook was for organic sales growth of 0-1% and adjusted earnings per share of $7.30 to $7.55. The updated earnings outlook reflects significantly higher input cost inflation and lower sales volumes, partially offset by additional cost savings and reduced discretionary spending.
-
Chairman and CEO Mike Hsu said, “Our second quarter reflects continued pandemic-driven volatility. We are facing significantly higher input costs and a reversal in consumer tissue volumes from record growth in the year ago period as consumers and retailers in North America continued to reduce home and retail inventory. While we look forward to a return to a more normalized environment, we have moved decisively to take pricing actions to mitigate inflationary headwinds and continue to prudently manage costs. We remain confident in our strategy and in our fundamental brand performance. Our personal care business is performing well, and we continue to improve our market positions in key markets and realize robust growth across Developing and Emerging Markets.”
Hsu continued, “We will continue to execute K-C Strategy 2022. While our updated outlook reflects a more challenging near-term environment, we are taking appropriate actions and remain confident in our strategies to create long-term shareholder value.”
2021 outlook and key planning assumptions
The company updated the following key planning and guidance assumptions for full-year 2021:
-
-
-
- Net sales increase 1-4% (prior assumption 3-5%).
- Organic sales decline 0-2% (prior target 0-1% increase).
- Foreign currency exchange rates favorable between 1-2% (no change).
- Softex Indonesia acquisition expected to increase sales 2% while exited businesses in conjunction with the 2018 Global Restructuring Program anticipated to reduce sales slightly (no change).
- Adjusted operating profit expected to decline 11-14% year-on-year (prior assumption decline of 3-6%).
- Key cost inputs expected to increase $1,200 to $1,300 million (previous estimate $900 to $1,050 million). The increased estimate is driven by polymer-based materials and pulp.
- Cost savings of $520 to $560 million, including $400 to $420 million from the FORCE program and $120 to $140 million from the 2018 Global Restructuring Program. The prior estimate was for total savings of $460 to $520 million.
- Net income from equity companies similar, to down somewhat, year-on-year (prior outlook similar, to up somewhat).
- Adjusted earnings per share of $6.65 to $6.90 (prior outlook $7.30 to $7.55).
- Net sales increase 1-4% (prior assumption 3-5%).
-
-
- Capital spending of $1,100 to $1,200 million (prior outlook $1,200 to $1,300 million).
- Share repurchase of $400 to $450 million (prior outlook $650 to $750 million).
-
Source: investor.kimberly-clark.com