In the dynamic and global textile fiber industry with its various manufacturing processes and end-uses, news and information is breaking on a daily basis. International Fiber Journal is tracking stories relevant to our industry from manmade to natural to bio-based fibers, innovations in nonwoven, woven, braided and technical textiles, technologies for additives, bonding, coatings and polymers, and applications from apparel to hygiene to transportation, and more. Here we will post news stories relevant to textile fibers and their downstream applications on an ongoing basis. Please check back for regular updates. If you have news that you feel should be added to this summary report, please email it to Ken Norberg at ken@ifj.com.
Most recent update: February 24, 2023
Columbia Professors Develop Groundbreaking, Dirt-Based Textile
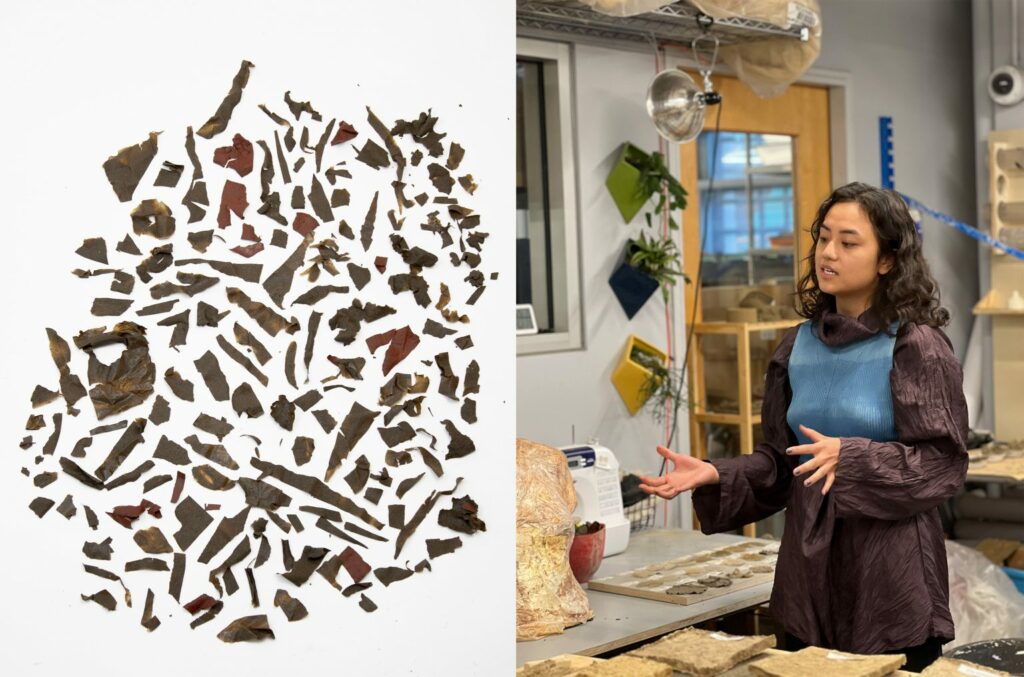
Professors at Columbia University have developed a textile that is 60% comprised of soil and suitable for making clothes. Named BioEarth, the material was co-designed by Penmai Chongtoua and Professor Lola Ben-Alon of the Natural Materials Lab at Columbia’s Graduate School of Architecture, Preservation, and Planning. It is thin and strong with a “leathery feel and a slight sandiness.”
The first generation of BioEarth was stiff, but later iterations gained flexibility when blended with bioplastics from corn starch, cellulose, and algae. “Finally, we found a recipe composition that has over 60% of soil—so the majority of the material is still soil-based,” said Chongtoua, “but it is a flexible, wearable, movable piece of fabric.”
The fabric is strong enough to be laser-cut, embroidered, and machine-sewed. The team hopes to continue advancing the strength and flexibility of BioEarth so that it can replace mainstream textiles like cotton.
Unifi publishes Sustainability Report
Unifi, Inc. – together with its consolidated subsidiaries – makers of REPREVE and one of the world’s leading innovators in recycled and synthetic yarns, recently released its Sustainability Report for fiscal 2022.
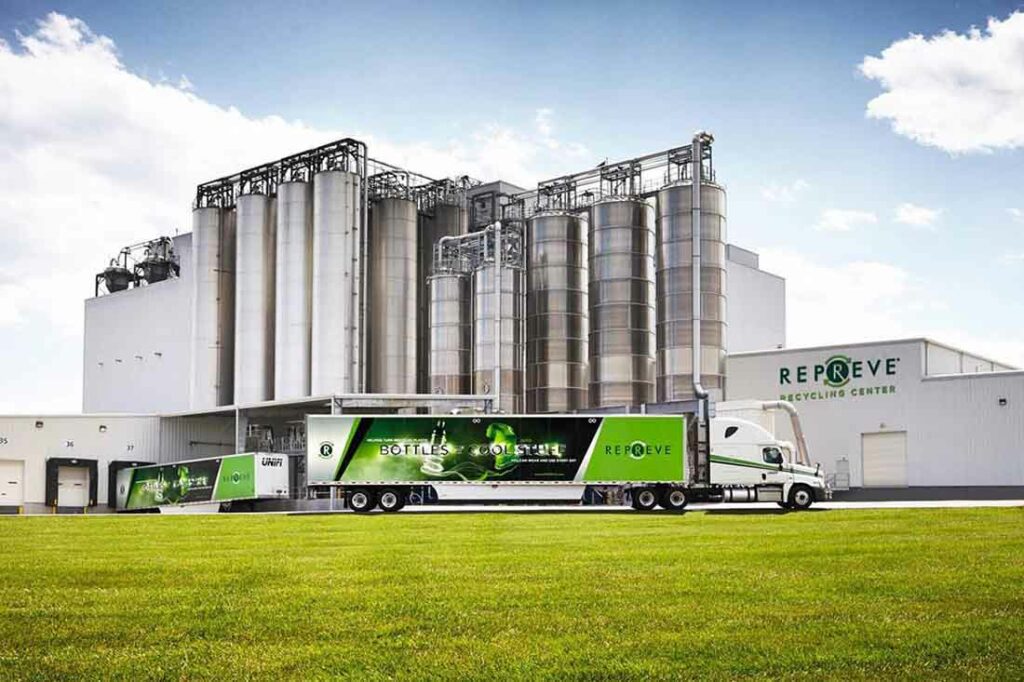
The report provides expanded insight into Unifi’s industry leading sustainability strategy and the company’s responsible approach to creating long-term value for its stakeholders. In tandem with the report’s release, Unifi reiterated its ambitious commitment to divert and transform 50 billion landfill-bound plastic bottles by 2025.
The report details progress on Unifi’s corporate and sustainability strategy organized under three pillars: people, planet, and product.
Milliken & Company’s Textile Business Eliminates PFAS
The Textile Business of Milliken & Company announced it has successfully eliminated all per- and polyfluoroalkyl substances, commonly referred to as PFAS, from its textile fibers and finishes portfolio, becoming the first U.S.-based multi-market textile manufacturer to remove PFAS.
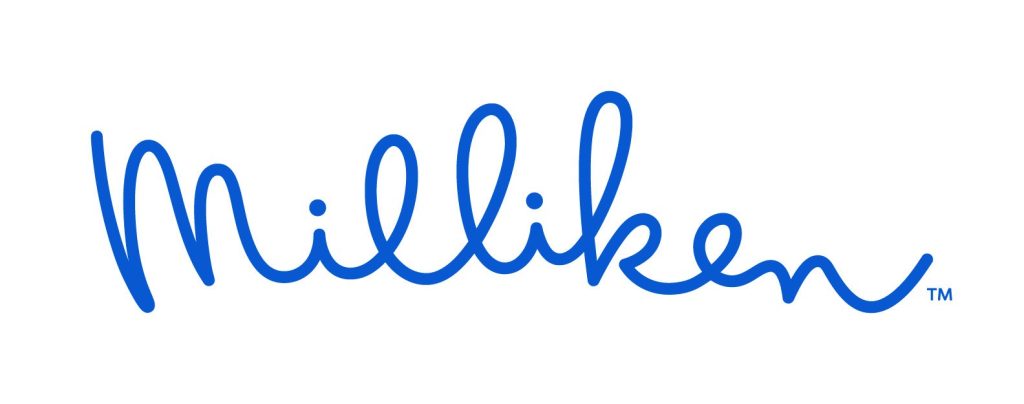
“This is a tremendous accomplishment and tribute to our team who worked around the clock to develop solutions that meet our customers’ performance requirements and reflect our purpose to positively impact the world for future generations,” said David Smith, executive vice president, Milliken & Company, and president, Milliken’s Textile Business.
The manufacturer announced in February 2022 an aggressive plan to eliminate PFAS as an ingredient in its textile portfolio by the end of the year. As of Dec. 31, 2022, the Textile Business at Milliken had removed PFAS-based finishes and fibers, which spans multiple industries including flame-resistant, military, uniform and decor fabrics.
Milliken’s Textile Business began evaluating its portfolio in 2020 and segmented its evaluation efforts between three areas of focus: durable water repellency (DWR), soil release and oil repellency. Alternative DWR solutions were readily available in the market through accredited organizations such as bluesign®. The Milliken research team assessed and implemented appropriate alternatives to maintain the performance and quality standards customers expect for DWR.
REI to Ban PFAS in Outdoor Clothing and Cookware
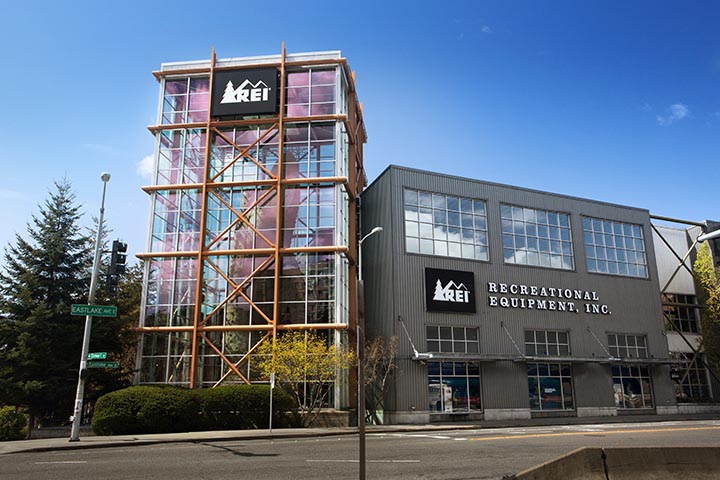
Outdoor retailer REI will ban the group of chemicals known as PFAS in all textile products and cookware from its suppliers starting in fall 2024, according to an announcement this week.
The announcement was an update to the company’s product impact standards for its more than 1,000 brands partners.
Exposure to PFAS, short for per- and polyfluoroalkyl substances, has been linked to multiple health problems including kidney and testicular cancer, liver and thyroid problems, reproductive problems, pregnancy-induced high blood pressure, low birthweight and increased risk of birth defects, among others. PFAS have also been linked to changes in cholesterol levels and in the timing of puberty.
Nassimi Completes Move To Establish A Fully PFAS-Free Portfolio
Nassimi – a leading textile manufacturer and pioneer in sustainable performance upholstery materials – is moving to eradicate Per- and Polyfluoroalkyl Substances (PFAS) from all new production.
Nassimi’s commitment to 100% removal of PFAS is bold, and it was the first textile company to produce phthalate-free faux leather in the early 2010s and remove flame-retardant chemicals from its upholstery materials in 2017. The company has reformulated the last of its textile lines containing PFAS, Resilience TX, to create a fully sustainable product portfolio that still delivers on performance.
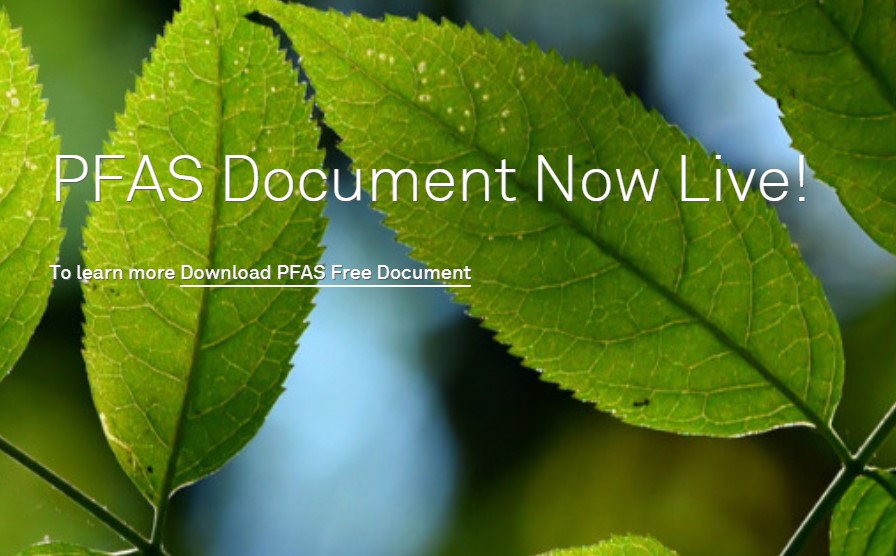
While conventionally used PFAS-free alternatives are often less effective in repelling stains, Nassimi’s state-of-the-art proprietary technology in the finishing process offers highly effective stain protection. As an example, Nassimi’s Supreen liquid barrier fabrics use a silicone-based stain repellent that is applied following a patented fabric-purification process. This allows for the silicone to fully embed itself into the textiles’ fiber to create an invisible layer of stain protection.
PFAS, often referred to as fluorocarbons, are a large, complex group of manufactured chemicals present in a variety of consumer products, including performance fabrics, that do not degrade easily in the environment and may be linked to harmful health effects in humans and animals. While many companies are just now beginning to develop PFAS-free alternatives as a response to current legislation in some states, Nassimi has been at the forefront of this, engineering its fabrics to be PFAS-free from the get-go.
Polartec® Introduces Technology That Reduces Fiber Fragmentation
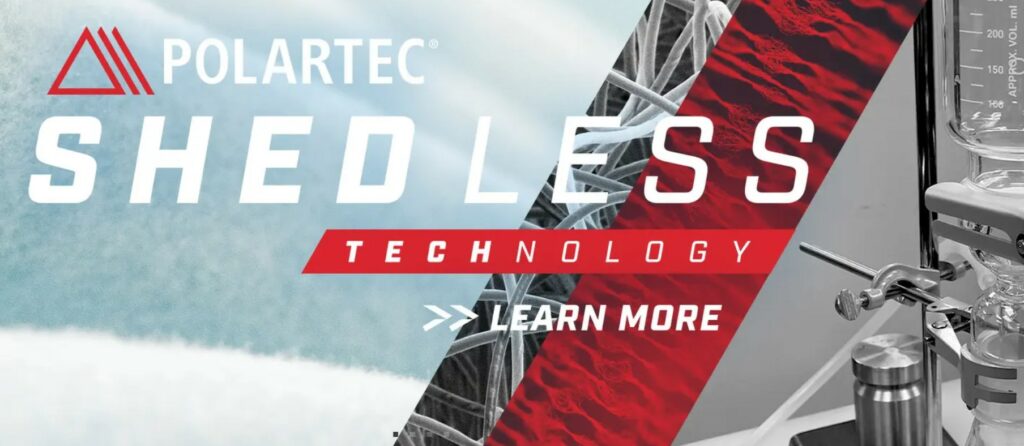
Polartec®, a Milliken & Company brand, recently announced Polartec® Shed Less Fleece, a new milestone in its industry-leading efforts to reduce textile fiber fragment shedding.
Shed Less is a process that combines yarn construction, knitting, chemistry and manufacturing to reduce home laundry fiber fragment shedding by an average of 85%. The first fabric to receive this new technology is the brand’s iconic Polartec® 200 Series Fleece, the modern version of the original PolarFleece® launched in 1981, and in 1993, the first performance fleece knit from yarn made from recycled plastic bottles.
The Shed Less process works by engineering the lofted fibers that give fleece its soft hand the ability to resist breaking and rubbing off during home laundering, cited as one contributing factor to the spread of fibers fragments (commonly referred to as microfibers). Polartec® Shed Less Fleece achieves this remarkable outcome while maintaining all of the attributes that continue to make Polartec fleece a staple of midlayer collections – lightweight, breathable and warm, with unmatched softness and hand feel.
U.S. producers to plant 17% less cotton than last year
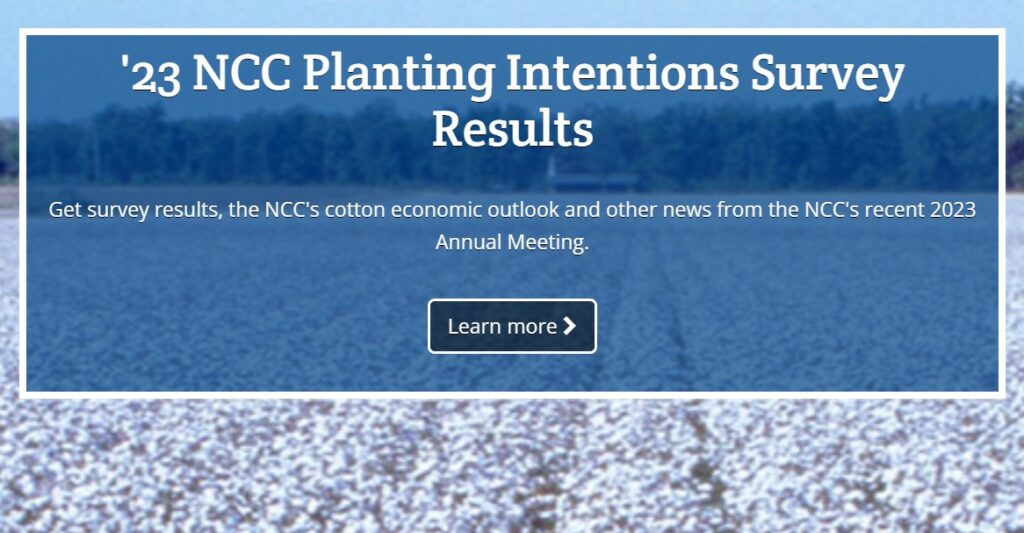
U.S. cotton producers intend to plant 11.4 million cotton acres this spring, down 17.0 percent from 2022, according to the National Cotton Council’s 42nd Annual Early Season Planting Intentions Survey.
Upland cotton intentions are 11.2 million acres, down 17.3 percent from 2022, while extra-long staple (ELS) intentions of 184,000 acres represent a 0.5 percent increase. The detailed survey results were announced today during the 2023 National Cotton Council Annual Meeting.
Dr. Jody Campiche, the NCC’s vice president, Economics & Policy Analysis, said, “Planted acreage is just one of the factors that will determine supplies of cotton and cottonseed. Ultimately, weather and agronomic conditions are among the factors that play a significant role in determining crop size.”
Using five-year average abandonment rates along with a few state-level adjustments to account for current dry conditions, Cotton Belt harvested area totals 8.8 million acres for 2023 with a U.S. abandonment rate of 22.6 percent. Using the five-year average state-level yield per harvested acre generates a cotton crop of 15.7 million bales, with 15.2 million upland bales and 466,000 ELS bales.
The NCC questionnaire, mailed in mid-December 2022 to producers across the 17-state Cotton Belt, asked producers for the number of acres devoted to cotton and other crops in 2022 and the acres planned for the coming season. Survey responses were collected through mid-January.
Archroma Expected to Close Acquisition of Huntsman Textile Effects
Archroma, a global leader in sustainable specialty chemicals and solutions for industries such as textiles, packaging & paper, paints and coatings, announced that it has secured all regulatory approvals required to complete the acquisition of the Textile Effects business from Huntsman Corporation.
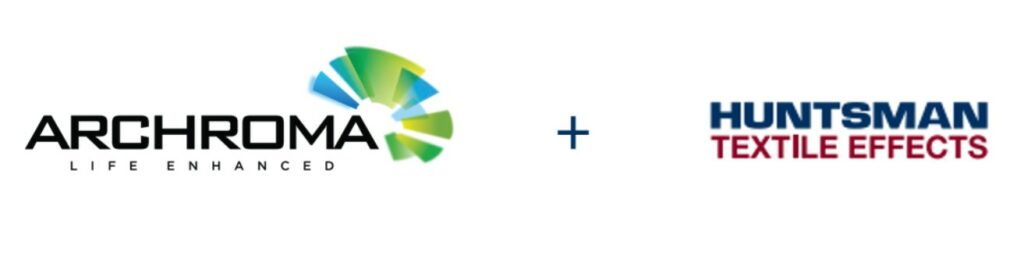
Both parties expect the transaction, which was first announced in August 2022, to close on February 28, 2023.
Archroma is a portfolio company of U.S.-based private investment firm SK Capital Partners. Since its formation in 2013, Archroma acquired and successfully integrated the global textile chemicals businesses of BASF as well as BASF’s stilbene-based OBA business for paper applications, and M. Dohmen, a specialist in coloration for automotive textiles.
Oerlikon Relocating, Expanding Service Offering for U.S. Customers
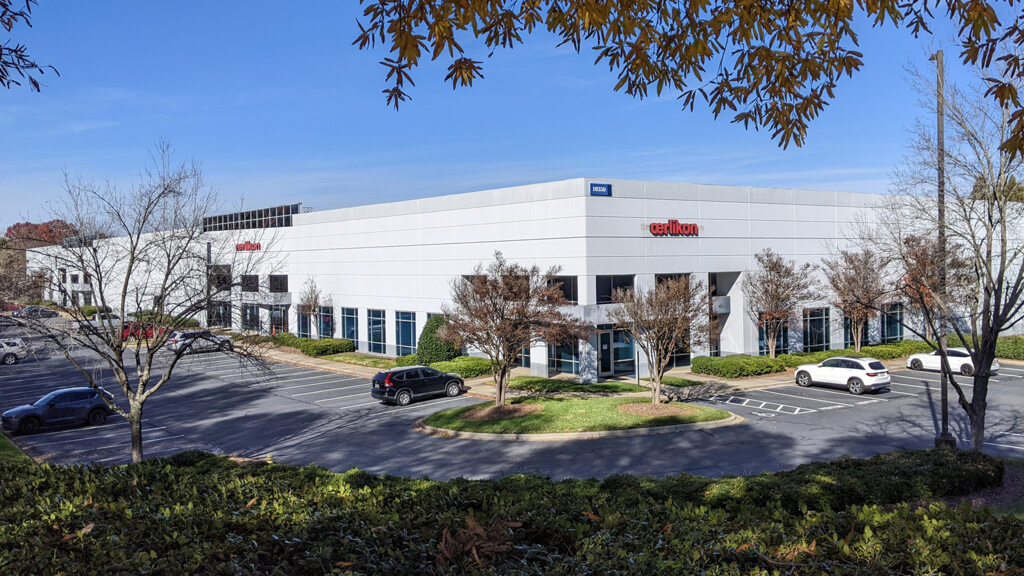
The American subsidiary of the Swiss Oerlikon Group, Oerlikon Textile Inc., is expanding and moving into new, modern premises tailored to future needs just a few miles away from its previous location in Charlotte, N.C.
A new service center for the polymer processing industry will be created latest by the middle of this year.
At the new address, 10350-A Nations Ford Road, Charlotte, N.C. 28273, synergy effects and resources can be used to a noticeably greater extent for the benefit of all Oerlikon customers in approximately 4500 m² of office and commercial space.
“We are the preferred technology partner in the field of manmade fiber production in the USA and not only want to remain so, but also to further expand our services for our customers. However, the previous premises no longer offered any opportunities for expansion,” said Chip Hartzog, president of Oerlikon Textile Inc., the logical step.
All processes were analyzed in advance and will now be optimized in the new buildings. Incoming goods, warehouse and dispatch will be merged, inventory control will be strengthened. On top, the range of services in the repair area will be expanded.
“In addition to our services in the area of filament and carpet yarn systems, we will also be able to offer our customers repair services for staple fiber components such as crimpers or nonwoven systems in the future,” Hartzog said.
This will further strengthen the market position for the Oerlikon Barmag, Oerlikon Neumag and Oerlikon Nonwoven brands.
Oerlikon Textile Inc. has been active in the manmade fibers business in the USA for over 55 years. In addition to the sale of Staple Fiber, BCF, IDY, POY, FDY and texturing plants, the product portfolio also includes upgrades and modernization of old plants, service and training offers as well as repair services and spare parts supplies.
Dovetail Workwear Partners With CiCLO® Sustainable Textile Technology
Built by, for, and with women, Dovetail Workwear announced a partnership with CiCLO® technology to reduce the environmental impact of fugitive synthetic microfiber pollution caused by textiles, the most prevalent form of microplastic found throughout the globe.
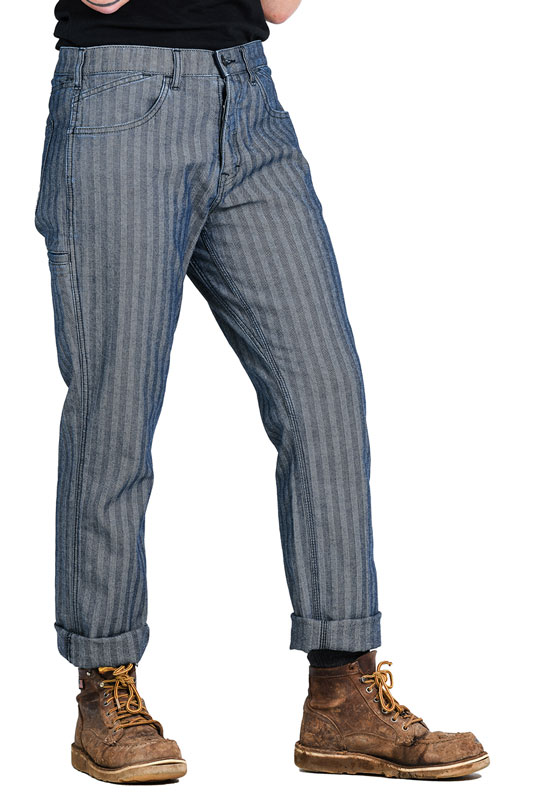
Debuting in the new Shop Pant for Spring 2023, Dovetail integrates CiCLO® nylon fibers woven into cotton to create a durable and long-lasting garment with materials that will reabsorb back into the environment post-consumer use.
The Shop Pant offers a stylish, higher waist design with ten pockets and panel-free leg face for women who prefer a pant without reinforced front panels. The durability and added strength of CiCLO-infused nylon in the warp yarns eliminates the need for panels and rivets, allowing mechanics and makers alike to not scratch or ding their handiwork. CiCLO® technology is non-toxic to marine life, fully traceable, and ECO Passport Certified by OEKO-TEX®.
Majocchi Achieves Exacting Textile Functionality with Baldwin’s Corona Treatment Technology
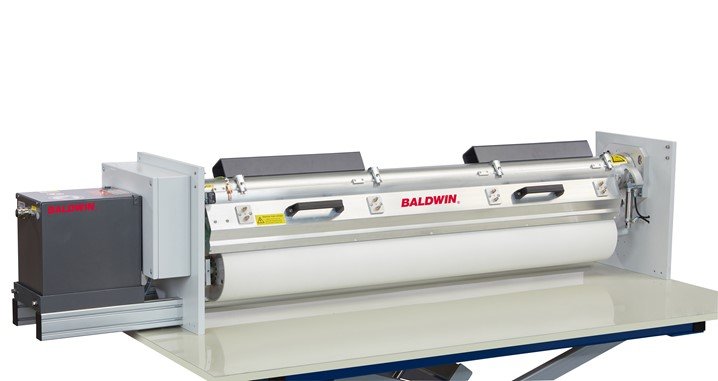
Majocchi, a leading Italian textile manufacturer, reports that it has achieved unprecedented functional and visual appeal with its key fabrics since installing Baldwin Technology Co. Inc.’s corona surface treatment technology.
Based in Tavernerio (Como), Majocchi has cemented itself as a leader in the global textile market by focusing extensively on applying the latest research and innovation within the field to achieve superior results.
Majocchi has a well-documented history of being a technological innovator in the textile industry. Within a decade of its conception in 1941, Majocchi became the leading global supplier of waterproof cotton for rainwear manufacturers. In the 1960s, the company began producing nylon and technical fabrics, which paved the way for it to become a leading provider of textiles for urban fashion, technical workwear and the military today.
Taking it to the next level, for over a year, Majocchi has partnered with U.S -based Baldwin Technology Co. to utilize its unrivaled corona surface-treatment technology to produce superior wettability and adhesion.
Corona treatment is a technique that temporarily modifies a substrate’s surface tension properties. The corona oxidation process improves the penetration and absorption of liquids on cellulosic and synthetic fabrics. Utilizing corona treatment before resin application on fabrics such as lycra and nylon facilitates superior adhesion and resin distribution. As a result, corona-treated fabrics provide exceptional color and tonal quality.
Majocchi uses Baldwin’s Corona Pure Model to apply polyurethane and acrylic-based coatings to its fabrics. The system allows Majocchi to administer a controllable, uniform coating to achieve the desired functionality and aesthetics.
The system is 2,000 millimeters wide with a discharging station and four ceramic electrodes designed for textile applications with the flexibility of customizing plasma dosage for a given fabric structure, width and process speed. The Corona Pure model allows for fabric treatment up to 300 gr/m² in thickness. The system is highly customizable, with single-sided and dual-sided treatment capabilities.
KARL MAYER Textile Specialists Develop Symmetrical Chantilly Lace
With clarity and balance in mind, KARL MAYER’s textile specialists have developed a lace last year that is characterized by an extremely precise and distinct appearance. The intricate look is created by a filigree pattern and the utmost symmetry of the design elements. Accordingly, the name of this innovation is Symm-Net.
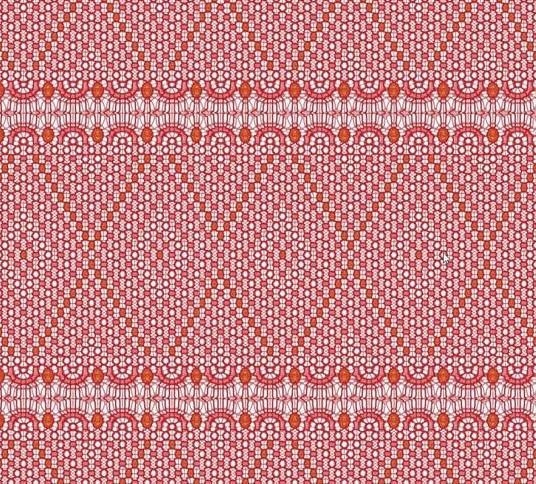
The new MJ 92/1 B multibar jacquard raschel machine is used to produce Symm-Net. Equipped with a split threaded jacquard bar, this newcomer can work both equal- and counter-lapped patterns, and also has two ground bars at the back operating counter-lapped to complete the symmetry. The possibilities of this set-up were exploited in initial samples last year, where Symm-Net was launched in an elastomeric galloon targeted at lingerie. Here a counter-lapping jacquard movement combined with the two counter-lapped elastane bars created a successful symmetry.
Several of the new machines have already been ordered to date.
Beste Incorporates HeiQ AeoniQ™ Into Circular Cellulosic Fiber
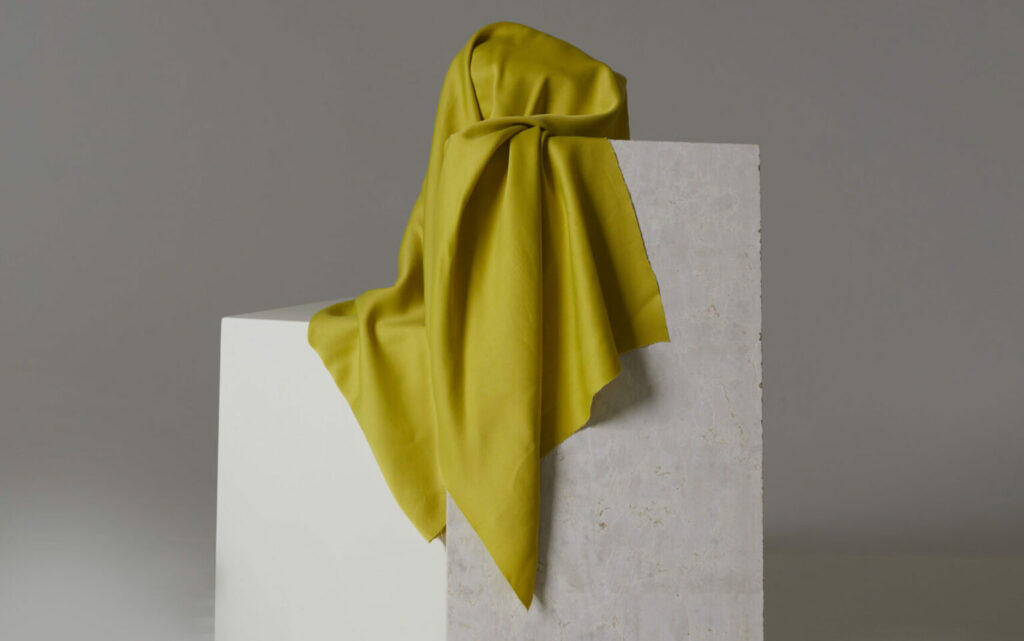
Italian premium textiles manufacturer Beste becomes the first partner in its field to incorporate HeiQ AeoniQ™ endlessly circular cellulosic fiber in its high-end fabric portfolio.
Beste and HeiQ AeoniQ™ announced their strategic partnership with the launch of a capsule in the CARPINI collection at Milano Unica. The fabrics including HeiQ AeoniQ™ are crafted by the Italian textiles manufacturer Beste, well known for supplying high-end fabrics for premium and luxury brands.
The innovative fabrics capsule collection for S/S 24 includes 12 articles made with 100% HeiQ AeoniQ™, linen, and HeiQ AeoniQ™ blends, and cotton and HeiQ AeoniQ™ blends in several different proportions.
The collection is named FLOW, as related to the movement of water and air to be in tune with Nature’s balance and rhythm, with a color range including hay, black, water, caramel, violet, dust, denim, lime, and cobalt.
With this initiative, Beste becomes the first partner to incorporate the HeiQ AeoniQ™ fiber into its active fabric portfolio, and also its Tessuteka, the library that keeps all the fabrics produced by the company since 1993.
Textile Technology Center to Host Textile Academy
The Textile Technology Center at Gaston College announced that it is holding Textile Academy, a six-week program that will run every Monday through Thursday from February 27th until April 6th from 1 p.m. to 5 p.m.
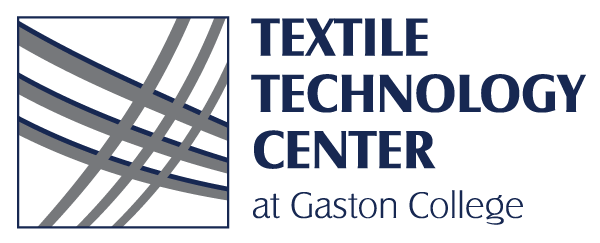
The Textile Academy will introduce participants to the basic concepts of textile technology and careers within the textile industry. Training is provided on core concepts such as textile fundamentals, textile manufacturing concepts, math and measurement, teamwork and communication, safety, lean manufacturing principles and problem solving.
Upon completion of the course, participants will receive their OSHA 10-hour certification and Basic Forklift certification, preparing them for employment in various sectors of the textile and apparel supply chain. These certificates and credentials will enable attendees who are currently employed to pursue advancements in their existing positions.