In the dynamic and global textile fiber industry with its various manufacturing processes and end-uses, news and information is breaking on a daily basis. International Fiber Journal is tracking stories relevant to our industry from manmade to natural to bio-based fibers, innovations in nonwoven, woven, braided and technical textiles, technologies for additives, bonding, coatings and polymers, and applications from apparel to hygiene to transportation, and more. Here we will post news stories relevant to textile fibers and their downstream applications on an ongoing basis. Please check back for regular updates. If you have news that you feel should be added to this summary report, please email it to Matt Migliore at mmigliore@inda.media.
Most recent update: May 26, 2021
Fibre Extrusion Technology begins construction on new R&D center
Fibre Extrusion Technology Ltd. (FET) of Leeds, UK has started construction on a new purpose-built research & development center to support its growth goals. The facility will be located adjacent to FET’s current site, providing state-of-the-art facilities, including a visitor center and enhanced Process Development Laboratory (PDL) for client testing and product development.
FET’s clients will be able to spend time on site participating in development trials and technical sales meetings, so the visitor center is designed to make their stay more efficient and comfortable. Sales, administration and design departments will also be housed in the new building.
The addition of the Visitor Centre will free up a considerable space for production and other facilities in FET’s existing premises. The refurbishment phase for the existing premises is scheduled for completion at the end of 2021. As a result, FET’s manufacturing capacity is expected to increase by more than 50% to meet customer demand.
FET reports substantial year-on-year growth has driven this initiative and FET’s current order book in excess of £10million has provided the opportunity for investment in infrastructure for the future. Sustainability has been at the forefront of FET’s growth, supporting customers in their development of sustainable textiles and this principle is reflected in the choice of building materials and products for the Visitor Centre wherever possible, according to the company. The expansion is expected to be complete and open in the first quarter of 2022.
Source: fetuk.com
Coterie introduces sustainable wipes made with VEOCEL lyocell fiber
Coterie launched its new wipe made from renewable and biodegradable wood sources. Designed in partnership with the VEOCEL brand, the Coterie Wipes, consisting of 99% water, are the most sustainable and the largest (up to 30% bigger) baby wipes on the U.S. market.
Following recent certification testing, the wipes proved to be fully compostable after just a few weeks vs. hundreds of years and decompose even under the toughest of conditions. By comparison, the acceptable standard for compostable products can take up to six months, and plastic-based products, like most competitive wipes, can take hundreds of years. According to Coterie, the new wipes are the first-ever across the nation to be certified by the Environmental Working Group (EWG) for chemical safety, the National Eczema Association for gentleness, and TÜV-OK Compost HOME for sustainability.
Features of VEOCEL Lyocell fibers include:
- Natural and renewable raw material sourced from sustainably managed forests with FSC (FSC-C041246) certification.
- A patented closed-loop production process offering precision and consistent quality combined with low environmental impact.
- Natural absorbency, liquid distribution, biodegradability, and versatility mean the fabrics show tremendous durability in both a dry and wet state.
- VEOCEL lyocell fibers have been certified as biodegradable and compostable under industrial, home, soil, freshwater and marine conditions, thus can fully revert back to nature.
Source: lenzing.com
Bostik launches ‘Attached to Hygiene’ podcast
Bostik, a supplier of adhesive solutions to manufacturers of absorbent hygiene articles, has launched a new podcast, “Attached to Hygiene.”
Every 2 weeks Bostik will be releasing a new ‘Attached to Hygiene’ episode in which Bostik and guest industry experts will provide valuable insight into consumer & market trends that are designed to support article producers in their efforts to stay abreast of market dynamics.
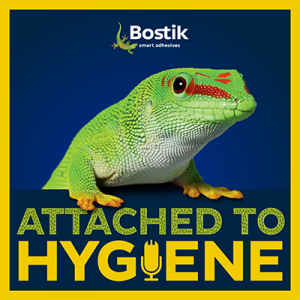
“For decades we’ve communicated through face-to-face meetings, emails, web content, videos, and webinars,” said Jack Hughes, Bostik’s global digital marketing manager and podcast host. “Given the rising popularity of podcasts, we thought this would be another great opportunity to share information and knowledge specific to the disposable hygiene industry in a way that is both easy to find and digest.”
Upcoming episodes of “Attached to Hygiene” take a detailed look at consumer needs and how they are driving trends in the disposable hygiene market. Bostik and our podcast guests discuss what they and the industry are doing to address these trends today and in the future; how choices in adhesives, materials, and substrates can differentiate article producers from their competition.
The first 2 ‘Attached to Hygiene’ podcasts and future episodes are available on Spotify, Apple Podcasts, Google Podcasts, Pandora, Tuneln, Stitcher, and iHeartRadio.
Source: bostik.com
Freudenberg Spunbond facility in Taiwan receives LEED sustainability certification
Freudenberg recently received the internationally recognized LEED certification for its resource-efficient, sustainable construction measures at the Tayuan Tao-Yuan site in Taiwan. LEED (Leadership in Energy and Environmental Design) recognizes the environmentally responsible construction of buildings.
The Freudenberg facility features modern lighting systems, air conditioning units and restroom facilities that utilize power and water from renewable resources are used efficiently. The energy consumption of compressed air and cooling equipment is optimized, with future plans for measuring equipment that will constantly monitor and control energy and water consumption at the facility.
Inside the production hall, low-emission paint and a sophisticated circulation system ensure air quality. Windows and transparent plastic materials have replaced some of the external cladding, so there is plenty of natural light in the hall’s interior.
Freudenberg uses recycled material made from post-consumer PET bottles to manufacture its spunlaid nonwovens at the Tayuan Tao-Yuan plant. In addition, an internal recycling system makes sure that production waste is returned to the production cycle.
Source: freudenberg-pm.com
NCTO testifies at Senate Homeland Security Hearing
NCTO President and CEO Kim Glas testified on “COVID-19 Part II: Evaluating the Medical Supply Chain and Pandemic Response Gaps” before the Senate Homeland Security and Governmental Affairs Committee.
Glas provided an overview of the U.S market prior to the pandemic and the root causes of America’s dependence on offshore sources of medical PPE, the response of the U.S. textile industry, the federal government’s response, and a series of policy recommendations in incentivizing the establishment of a permanent domestic PPE supply chain.
“The time is ripe for a revival of American PPE textile manufacturing. It has already begun, but we are at a pivotal point,” Glas said. “Without the necessary policy response and support, our recent progress will be undone just as quickly, and China’s stranglehold over global medical textile supply will be locked in for the foreseeable future with no reason to invest here. However, with the right policy framework, the domestic PPE supply chains built overnight can endure and grow, creating a level of self-sufficiency domestically that we have learned the hard way is essential to our national health and economic security.”
Glas detailed key policy recommendations designed to establish a permanent domestic PPE supply chain, including:
- Create strong domestic procurement rules for federal PPE purchases and other essential products–substantially similar to the Berry Amendment and the Kissell Amendment which require 100% US content from fiber production forward
- Implement forward-looking policies to shore up the Strategic National Stockpile and issue long-term contracts to incentivize investment in the domestic PPE manufacturing base
- Create federal incentives for private sector hospitals and large provider networks to purchase domestically-produced PPE
- Continue to deploy the Defense Production Act to shore up the textile industrial base from raw materials to end products for all essential products
Source: NCTO.org
Freudenberg shoe components certified to GRS
Freudenberg Performance Materials has completed the Global Recycled Standard (GRS) certification process for its shoe components manufactured in Asia. All Freudenberg Far Eastern Spunweb sites were certified by Control Union Certifications.
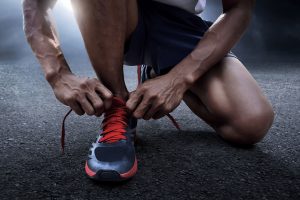
Freudenberg Far Eastern Spunweb’s materials are made from post-consumer and pre-consumer recycled polyester. The sustainable products include strobel insoles made of 100% recycled polyester with low waste from cutting, or 87% recycled and 13% conventional polyester, and its eyelet reinforcements. Freudenberg plans to exclusively produce materials made from 100% recycled raw materials by 2023.
Source: freudenberg-pm.com
Spinnova, Suzano announce annual production goal of 1 million tonnes of MFC fiber
Spinnova and Suzano launched a 22 million euro investment to build a joint facility in Finland. Located in Jyväskylä, the facility will produce Spinnova’s certified fiber with a goal of scaling production volume to one million tonnes annually by 2031.
“We have created a modular and flexible technology that is easy to scale and set up around the world. That’s why we can scale according to the pace of demand,” said Spinnova’s CEO and co-founder Janne Poranen.
Suzano will ensure the supply and quality of Spinnova’s raw material, micro-fibrillated cellulose (MFC), and increase volumes of MFC to Woodspin in line with these plans. Spinnova has selected Valmet to supply drying technology for the Spinnova production line.
“The first factory is a great start to realizing the vast, global opportunity of this innovation,” said Suzano’s New Business Executive Officer Vinícius Nonino. “We believe the Spinnova Technology will be highly scalable, and we support the ambition to ramp up the production in our joint venture to more than one million tons annual volume of Spinnova fiber within 10 years.”
Sources: spinnova.com | suzano.com | valmet.com
Danish Technological Institute leads the creation of ReSuit; aims to eliminate textile waste in Denmark
The Danish Technological Institute has gathered groups within fashion and textiles, raw material production, consumer behavior, and recycling technologies to form ReSuit (Recycling Technologies and Sustainable Textile Product Design), a Grand Solutions Project supported by Innovation Fund Denmark with DKK 13 million. This project will include: Bestseller, Elis, Design School Kolding, A/S Dansk Shell, Naboskab, Aarhus University, and Fraunhofer.
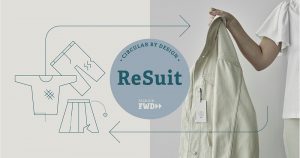
“Yearly, 100 billion textile units are produced worldwide, and they are to a great extent treated as disposable cutlery,” says Anders Lindhardt (PhD) from the Danish Technological Institute. “Materials worth 400 billion euros are lost as we lack infrastructure and solid recycling technologies on a very large scale. In this project, we are looking to get all textile waste in Denmark into a loop where it can become new textiles or raw materials for other products. If it succeeds, it can become a game changer.”
The consortium will address the textile problem from two angles:
- How can the textile industry get better at designing sustainably?
- Which technologies can ensure circularity for consumer textile waste?
For fashion, the focus is on sustainable textile products that are designed with recycling in mind. When it comes to textile waste, the project focuses on the enormous quantities of clothes and textiles that end up as garbage every year. In Denmark alone, this waste is 85,000 tonnes. Starting in 2022, Denmark will start sorting clothes separately, and in 2025, the rest of the European Union will follow.
“Polyester accounts for half of all clothes fibers in the world,” says Anders Lindhardt. “Therefore, we will further develop technology based on chemical recycling to recycle the polyester materials so that they can return to the textile industry.”
The remainder of the textile products must be degraded using so-called HTL technology (hydrothermal liquefaction). The process makes it possible, under the influence of water, heat and pressure, to convert the complex textile stream into oil products that can be used for the production of e.g., plastic, fuel or synthetic textile fibers.
Source: dti.dk
Registration open for virtual International Nonwovens Symposium
Registration is now open for EDANA’s International Nonwovens Symposium, a virtual event held June 9-10. The two-day program will explore the latest challenges and innovations from leading institutions including the European Commission, STFI, the Nonwovens Innovation & Research Institution (NIRI), the Universität Kaiserslautern, DKTE and the Indian Institute of Technology.
Presentations from DuPont, Andritz Laroche, Johns Manville, Sabic, Beaulieu, Covestro, Sandler, Freudenberg, Hassan and Walki, will explore topical themes including:
- New opportunities and technologies for meltblown nonwovens
- Innovations in automotive nonwovens
- New processes for the manufacturing of medical nonwovens
- Recycling and sustainability considerations in nonwoven design and production
Registration and sponsorship opportunities can be found at edana.org/nonwovens-symposium
Source: edana.org
Albarrie upgrades Morrow Road, Ontario, Canada, facility with new stenter frame
Albarrie replaced a 50-year-old machine on its factory floor with a new stenter frame, spanning 2,400 square feet. Operating at heats up to 450 F (232 C), the stenter frame will allow Albarrie to heat set and dry materials to produce denser and higher-quality fabrics than its predecessor. It will also cut production time for fabrics.
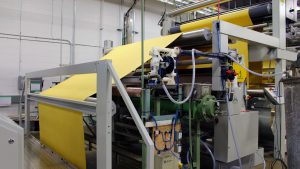
“This is an exciting time here at Albarrie,” said Kevin Horner, Director of Operations. “Pressing the on switch of this new technology means that we can continue to produce industry leading fabrics and have them out the door, on their way to customers, in a shorter amount of time, which will ultimately open new doors for this business.”
The stenter frame provides opportunities for seasoned employees to learn new skills in the operation of this technology, contributing to continued education and personal development.
Source: albarrie.com
Indorama Ventures reports first quarter 2021 financial results
Indorama Ventures (IVL) announced its first quarter 2021 financial results with a revenue of $3,240M, with its company-wide cost and business transformation, Project Olympus, yielding $67M. Project Olympus’ earnings were split evenly between business-led initiatives and cost transformation. The first quarter results have IVL on track to achieving its $287M efficiency gains in 2021. IVL also reported EBITDA of $483M coming from higher core EBITDA, positive contract adjustments and inventory gains.
IVL has been working toward strengthening data platforms and digital tools to improve company management. It has also reorganized leadership, with 16 business verticals within three business segments under one global CEO, creating a regionally integrated business model.
IVL has laid out a carbon neutral strategy to include recycling, renewable energy, ethical carbon offsets and adaption of new green technologies and initiatives. As a part of this strategy, IVL launches its first certified Carbon Neutral PET pellet through its Deja sustainable brand platform.
“Last quarter I stated that 2020 brought no structural damage to the industries IVL plays in and the first quarter of 2021 has further solidified this thesis,” said Aloke Lohia, CEO of Indorama Ventures. “Our advantaged portfolio and experienced management, supported by our transformation programs, will yield superior returns for shareholders in line with our 2023 targets. Our journey towards carbon neutrality will be a key guidepost for IVL’s actions going forward, in our quest to be a world class sustainable chemical company.”
Source: indorama.net
Suominen commits to 50% increase in sustainable product sales by 2025, launching at least 10 sustainable products per year
Suominen has announced sustainability goals, including increasing sales of sustainable products by 50% by 2025, compared to the base year 2019, and to launch at least 10 sustainable products per year. Its current sustainable product portfolio consists of products made of renewable, recycled and plastic-free raw materials, as well as compostable and totally dispersible nonwovens.
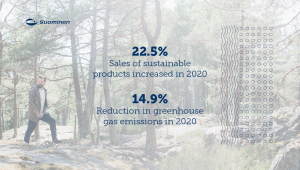
“Our customer insight together with our market & technology leadership provides the basis for creating sustainable products and product families,” said Lynda Kelly, SVP, Americas & Business Development.
Suominen’s New Fiber Center is home to its research and development, where it focuses on sustainability and customization in its products.
“Our fiber based technology platform, strong research and development team and our continuous work in new and innovative fibers means we are able to offer tailor-made solutions for customers’ different sustainability needs,” said Kelly.
Source: suominen.fi
INDA announces World of Wipes Innovation Award finalist
Nonwoven-based wipe products for sanitizing, cleaning and beauty applications from Kimberly-Clark Professional, Lenzing and SharkNinja are the finalists vying for this year’s World of Wipes Innovation Award that will be selected at the 15th edition of the 2021 World of Wipes (WOW) International Conference, July 12-15, in Atlanta, Georgia. These three leading companies will present their innovations live at WOW 2021 to the wipes professionals attending the in-person event.
The award finalists will make their presentations at the conference on July 13, and the winner will be announced on the morning of July 15, capping off the conference focused exclusively on wipes that will be held at the Atlanta Marriott Marquis.
The World of Wipes Innovation Award recognizes products or technology innovations within the entire wipes value chain that expands the use of nonwoven fabrics and demonstrate advancements in creativity, novelty of approach, uniqueness and technical sophistication.
Finalists for the World of Wipes Innovation Award are:
- Kimberly-Clark Professional – Scott 24 Hour Sanitizing Wipes are the first pre-saturated wipes to quickly disinfect and maintain surface sanitization for 24 hours, killing 99.9% of bacteria such as Staphylococcus aureus, Enterobacter aerogenes and Community-Associated Methicillin Resistant Staphylococcus Aureus Bacteria. The wipes patented formulation is found to be effective by the United States Environmental Protection Agency for disinfecting on hard, non-porous surfaces against numerous strains of bacteria and viruses, including SARS-COV-2 when used as directed. (It is not approved in California for use against SARS-CoV-2.)
- Lenzing – Lenzing Lyocell Skin fibers are designed with a patented technology that makes them translucent when impregnated with serum. Designed for the growing facial sheet mask market, these fibers are the basis for a premium facial sheet mask skincare routine that meets the expectations for translucency, smoothness, fineness and comfort. Lenzing Lyocell Skin fibers are an exquisite solution for consumer demands for more sustainable single-use masks made from natural cellulose and contributing to circularity.
- SharkNinja – The Shark VACMOP is a cordless hard floor cleaning system that utilizes suction and spray mopping for a more thorough clean. The disposable pad uses multiple nonwoven types allowing consumers to pick up and lock away dry debris, and also spray-mop to tackle the toughest messes. Shark VACMOP pads consist of two components – a dirt chamber that collects and locks away dirt and debris picked up by vacuum, and a fiber pad that mops up tough messes.
WOW 2021 sessions include wipes and the growing plastics debate, new directions in sustainability, the growth in cleaning products brought on by COVID-19, emerging markets, regulatory changes and more.
* International Fiber Journal is owned by INDA, Association of the Nonwoven Fabrics Industry (inda.org).
Source: inda.org
Aurora Specialty Textiles Group wins awards for operational excellence, innovation, and continual improvement
Aurora Specialty Textile Group has won awards for outstanding business and manufacturing practices from the Valley Industrial Association (VIA). The awards were announced at the annual VIA Spark Awards Benchmarking for Excellence celebration. VIA represents the manufacturing industry in the Fox Valley region of Illinois.
Aurora won the award for Operational Excellence for a company with 51-200 employees for the second year in a row. The award recognizes leadership in operational strategic planning and implementation.
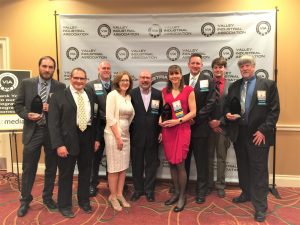
Aurora also won the awards for Innovation for a company of 51-200 employees and for Overall Most Improved. The Innovation Award recognizes companies that cultivate a culture of innovation and have an innovation process to engage employees, capture ideas, provide benefits for customers, as well as drive business initiatives. Overall Most Improved celebrates continual improvement year after year in the areas of safety, workforce development, innovation, culture, operational excellence and social responsibility.
“Even during a year of immense and unprecedented challenges, we managed to make improvements in Social Responsibility, Innovation, Operational Excellence, Safety, Culture and Workforce Development,” said Marcia Ayala, president of the company. “The awards speak to the great employees we have at Aurora and our continuous focus on improvement. The awards also demonstrate a consistent effort and focus throughout the Aurora organization. Thanks to all Aurora employees! I am very proud and appreciative.”
Source: auroratextile.com
Asahi Kasei renews membership in Business Call to Action
Asahi Kasei renewed its membership in the Business Call to Action (BCtA) program (UNDP), which aims to accelerate progress towards the Sustainable Development Goals (SDGs) by challenging companies to develop inclusive business models that engage people at the base of the economic pyramid (BoP).
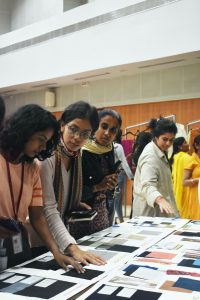
Since joining BCtA in 2016, the company’s support for stakeholders in the Bemberg value chain in India from raw material to garment as well as the collaboration with academia have been evaluated as a business model combining commercial activities and sustainable development.
Bemberg is a regenerated cellulose fiber made from cotton linter, the fuzz around cotton seeds. It is used in outerwear, inner wear, traditional garments, bedding, and sportswear. To support local manufacturers, Asahi Kasei lends equipment to remove linter from cotton seeds free of charge, and has its engineers provide the local workers with training and technical instructions for improving productivity. It also provides technical guidance on weaving and dyeing in the fabric production process in India.
Microza, a hollow-fiber membrane for filtration systems, is also part of Asahi Kasei’s BCtA initiative. Microza is used in a variety of applications from chemicals and high-precision electronics to potable water, wastewater, foods, pharmaceuticals, power plants, and environmental protection. Microza can also be used to treat wastewater from fabric dyeing, aiming for zero wastewater emissions from dyeing plants.
Source: asahi-kasei.com
Oerlikon Manmade Fibers explains its position on data security
Oerlikon Manmade Fibers business unit is emphasizing the importance of data security, with digital solutions such as Remote Service, AIM4DTY, Smart Maintenance Workshops, Plant Operation Center and the fully networked ‘smart’ factory necessitating a secure infrastructure.
Operating a yarn manufacturing system requires various components and solutions: everything is present – from the control level, the Human Machine Interface (HMI), the automation systems, the Plant Operation Center all the way through to cloud solutions. All this requires smart infrastructure, which – in addition to a reliable network – includes a high-performance edge computing solution that, coupled with a modern software platform (CSP) and a correspondingly high security level, safeguards the security and the quality of the end product. By nature, data security is also decisive for all downstream processes within the textile value chain that build on the collated data or for merchandise management systems that are directly connected to the smart factory.
Oerlikon’s services such as Remote Support and tools including the AIM4DTY training center necessitate data exchange. “Here, we draw on high standards for the purpose of encryption, customer separation and also minimizing data,” said Sebastian Helmer, who is responsible for Information Security at Oerlikon Manmade Fibers Solutions. “We basically distinguish between three categories of threat scenario: firstly, we have the unconscious actions of employees who unintentionally load malware onto a system without realizing this themselves. Then there are the attacks that have no concrete objective; here, perpetrators attempt to attack a company by means of SPAM or phishing. And, finally, there are attacks that focus concretely on a specific company. Here, perpetrators try to plant malware using targeted methods. This can extend all the way through to social engineering in order to exert influence over the relevant persons.”
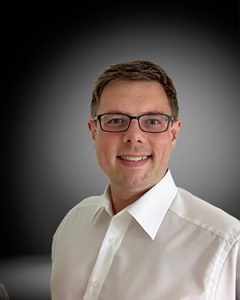
Helmer describes “Secure by Design” as the standard practice for establishing the necessary IT security in the product from the outset. “With our textile market expertise, intensive interaction with customers and our company-internal international experience, we have developed a picture of our customers’ requirements, which we are constantly expanding,” he said. “We also deploy common standards in the development of solutions – including ISO27001 and IEC62443, among others. Building on this, we develop our own smart factory security solutions, all the way through to customized solutions. We test new solutions by means of so-called pen tests – here, tests are carried out to hack the system in order to close potential security gaps in a targeted manner – in order to further improve them and check our environments with security architecture reviews.”
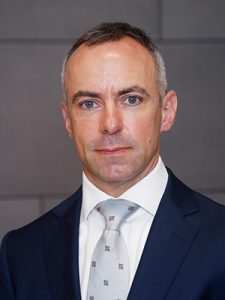
Oerlikon views the smart factory as a critical component between IT and innovation. “With the smart factory concept, we have developed from an operator into a consultant. On the one hand, IT enables innovation. At the same time, innovation is, however, also taking place in IT – culminating in new-generation digital products. Hence, both cross-fertilize each other,” said .
Source: oerlikon.com
Macron, RadiciGroup partner to develop line of sustainable technical sportswear
Macron and RadiciGroup have collaborated to develop and produce sustainable technical sportswear, such as sport socks made with Renycle. Renycle is a yarn manufactured by RadiciGroup from recycled nylon 6. Production scraps are recovered, recycled and reconverted into polymers to be spun into yarn comparable to yarn made of fossil-source materials. The Renycle yarn range reduces CO2 emissions by almost 90% and generates energy savings of more than 87% and water savings of 90%.

Macron has launched the Macron 4 the Planet project, which involves the construction of a new eco-sustainable headquarters, the production of sport jerseys made from 100% recycled polyester from PET bottles and the use of packaging made 100% from certified recyclate.
“RadiciGroup is a valuable partner in the green path undertaken by Macron,” Gianluca Pavanello, CEO of Macron, stated. “A shared vision and strategy on sustainability and environmental protection is essential. Macron’s objective is to create advanced technical sportswear for athletes of all levels, and our mission, which we pursue with great passion and commitment, is to study and develop materials that are more and more eco-friendly. Finding companies like RadiciGroup – a world leader in its sector, with whom we share values such as sustainability, recycling, use of renewable sources, corporate welfare and care for local communities – allows us to enhance our product offering and gain market acceptance by people who play sports at all levels. We hope our partnership will continue to develop over time.”
RadiciGroup has adopted a circular economy business model and directs all its efforts to optimizing raw material, energy and resource usage, perfecting processes, eliminating scraps and promoting designed-in end-of-life recycling of the materials it produces. The group’s goal is to reduce the environmental impact of its day-to-day activities by transparently and objectively measuring their effects at each stage.
“A circular economy cannot be achieved by acting alone,” stressed Angelo Radici, president of RadiciGroup. “As upstream players in the supply chain, we have always tried to share our knowledge of materials and deliver solutions featuring both better performance and respect for the environment. Furthermore, it is also crucial to find customers who are equally sensitive to these issues and can become strategic partners in the development of innovative and sustainable solutions. With Macron, we have worked as a team to create winning sports socks, because they are made from recycled materials, using all-Italian technologies, and are the result of a zero-kilometre, measured and traceable production and supply chain.”
Source: macron.com | radicigroup.com
INDA releases 2020 North American Nonwovens Supply Report
In 2020, North American nonwoven capacity increased to 5.552 million tonnes, a net increase of 0.7% (39 thousand tonnes) over 2019, according to the the eighth edition of the annual North American Nonwovens Supply Report by INDA, the Association of the Nonwovens Fabrics Industry.
Operating rates in 2020 were two sides of the same coin, as some end-use markets were completely shut-down for a few months, notably building and vehicle construction, and other end-uses were operating full-out. Producers were challenged by workforce and transportation issues. As a result, the overall operating rate only increased one-percentage-point over 2020. Additionally, as the operating rate is based upon tonnage, the increased demand for lighter-weight materials – medical apparel and fine-fiber meltblown – affected the total tonnage output, as some lines were running full-throughput of surface area, but not tonnage.
North American imports and exports, in tonnage, increased 51.2% and 14.2% respectively year-over-year. Imports were led by China (+97,200 tonnes, +121%) and India (+11,000 tonnes, +37 %). Even with the significant shifts in North American trade dynamics, nonwovens tend to stay where they are produced, with the net trade balance (imports less exports) accounting for less than 10% of the region’s capacity.
“This is a great time to be in nonwovens,” said Brad Kalil, Director of Market Intelligence & Economic Insights, INDA. “We are in a business that is expanding faster than the economy as production growth exceeded U.S. real GDP for the seventh consecutive year. Production growth also exceeded capacity growth for the fourth consecutive year. The overall operating rate for the industry also improved for the fourth consecutive year. Lastly – and most importantly – we are in a business that protects and improves people’s lives. This has been brought to the forefront recently with the benefits of protective medical apparel, respirators, face masks, and disinfecting wipes, now known by all. The nonwovens industry has responded to the pandemic and will continue to provide materials that keep the surfaces we touch clean, make safe the air we breathe, and provide a barrier to keep our bodies safe.”
The report is provided to INDA member companies and associates as part of their membership. The data gathered for this annual report serves as the foundation for the biannual North American Nonwovens Industry Outlook, which was published in December 2020.
* International Fiber Journal is owned by INDA, Association of the Nonwoven Fabrics Industry (inda.org).
Source: inda.org
Textile Technology Center aids student researcher in mission to turn plastic cups into fiber for sustainable textiles
In 2019, Lauren Choi, then a senior majoring in Material Science and Engineering at Johns Hopkins University started a project, The New Norm, to find a way to use plastic waste to produce sustainably made textiles. She began The New Norm after reading a Los Angeles Times article about China banning imported U.S. recyclables to search for a plastic product that was easily accessible and inexpensive.
Choi selected red Solo cups. The cups are made of polystyrene (#6 plastic). It is estimated that the approximately 7.4 billion Solo cups, lids and containers that are produced each year end up in landfills or oceans.
“At an early age, I had a strong interest and desire to work with sustainable products that would not damage but protect our planet. While in college my interest focused on creating sustainable textiles for the fashion industry. After reading this article, I saw it as an opportunity to step up and do something,” said Choi.
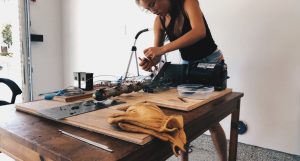
“Over time, I received grants and other funding to build a small extruder in my garage that enabled me to test the concept,” said Choi. “The long-term goal is to operate as a B2B wholesale fabric company, targeting higher-end womenswear brands, but I needed to first produce fiber and clothing on a larger scale.”
To inquire about blending the Solo cups into a suitable fiber-grade polymer, Choi contacted Gaston College’s Textile Technology Center (TTC) and the Catawba Valley Community College Manufacturing Solutions Center (MSC). Together, they worked with The Polymer Center of Excellence, a polymer lab in Charlotte, N.C. to conduct testing and determine the polymer blending and pellet extrusion process. Through this network of polymer engineers and textile specialists, Choi got in contact with Dart Container, the makers of Solo cups, and is now working in collaborative efforts with its recycling initiative.
In 2020, the TTC and the MSC formed a partnership creating the Manufacturing & Textile Innovation Network (MTIN), to work together to develop a regional workforce focused on advanced materials and textile testing development.
“When Lauren initially reached out to the Textile Technology Center for assistance with her research, I was extremely excited to help,” said Jasmine Cox, Process Coordinator at the Textile Technology Center at Gaston College. “Sustainability is such an important concept that directly impacts the textile and apparel industry. Being able to transform a common household item like a Solo cup into a garment is amazing. I knew that the TTC and partner organizations would be able to help The New Norm produce a great product,” said Cox.
The process included grinding recycled Solo cups into a pellet size suitable for the melt extrusion. Then the polymer pellets were melted through a combination of applied heat and friction, after which the molten polymer was forced under pressure through a small “shower head” opening, called a spinneret, on the TTC One Shot Extruder. This produced a prototype filament. The TTC Physical Testing laboratory then ran initial tensile, or tension, tests to determine ultimate strength and durability of a product.
Watching every stage of the testing process, Choi learned it was necessary to start small and work her way up to achieve successful fiber blends that could be turned into yarn and then a knit and woven fabric samples.
“Both the TTC and MSC have introduced me to experts in the industry,” said Choi. “I’m very grateful for this pool of advisors who helped me while working on this project. You need to seek advice and listen so that you can make the proper decisions. Stay on your feet but be flexible to change. Don’t give up and keep going.”
“These centers are wonderful tight knit facilities with good one-on-one communication,” Choi continued. “They were able to do multiple fiber tests and stay on budget until they could extrude a yarn successfully. You can’t create something so unique without building a relationship of trust. I don’t believe we would have accomplished these projects in the same timeline otherwise.”
Although Choi graduated from Johns Hopkins in 2020, she elected to pursue The New Norm for a year to continue with the project.
“Everything we’ve done so far would not have been possible without both centers. I’ve personally learned so much and as I look back to see what we’ve achieved in one year, I know we wouldn’t be here if it wasn’t for the centers,” said Choi.
Source: gaston.edu