Every year thousands of nonrecyclable/nondegradable composite parts end up in landfills, including gigantic parts like wind turbine blades, putting more pressure on composite manufacturers to reevaluate the sustainability of their products and their end-of-life options. This is why many of the industry players are interested in natural fiber composites (NFCs); however, a general unfamiliarity with this newcomer to the composite industry is preventing its widespread use. The purpose of this article is to bridge this gap and to provide a practical guide on the industrial utilization of NFCs.
Natural fiber composites can be defined as a composite in which the reinforcing phase is made up of natural fibers, while the matrix phase is either bio-based or synthetic polymer. But why should the industry consider natural fiber reinforcements?
- Sustainable – Natural fibers are obtained from renewable resources, carbon dioxide neutral and can reduce the CO² emissions of composite parts by 60-80% compared to glass fiber parts. In addition to being biodegradable, and recyclable at their end-of-life.
- Lightweight and safe – Natural fibers have almost half the density of glass fiber, they are safe in handling (don’t require any PPE), and they are nonabrasive to the machine parts during processing.
- High performance – Natural fibers have specific tensile properties equivalent to glass fiber, and they have higher thermal and acoustical insulation than glass and carbon fibers.
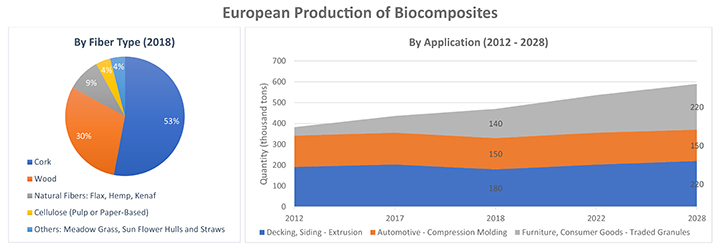
NFC market status
When we look at the market reports, we will often see market size reported as biocomposites. But it’s important to note here that biocomposites is a term that encompasses both wood plastic composites (WPCs) as well as NFCs. In 2018, the total biocomposites market size in Europe was 470,000 tons, and NFC market share was only 9% (42,000 tons), which is primarily used in automotive compression molding applications, as shown in Figure 1 (nova-Institut 2019).
The automotive sector is a major and one of the oldest markets for NFCs, dating back to Henry Ford’s hemp fiber car in the 1940s, as shown in Figure 2. The main parts that are commercially manufactured from NFC in the automotive industry are interior door panels, trunk liners, rear parcel shelves, headliners and instrument panels. But recently companies such as Porche and McLaren, in partnership with Bcomp, have been pushing the limits and started using NFCs in exterior body panels and structural parts, such as seat frames.
Furthermore, we are seeing enthusiastic researchers, engineers, architects and designers who are exploring new horizons for NFCs. For instance, recently an entire building façade in the Netherlands was made of hemp and biobased epoxy resin. Also, in the summer of 2021 two composite pavilions were built from NFCs in Germany. The first one is called Livmat, which was made from flax and biobased epoxy using a moldless filament winding process, and the second is the Biomat composite pavilion, which was made of flax and hemp pultruded rods. In addition, an interesting application by a Danish company called Projektkin, is making hardcase travel bags that can be bought from their online store for US$450. Another UK-based company called Jiva materials is trying to commercialize sustainable substrates for printed circuit boards from NFCs. Most notably, a German-based company called Greenboats famous for its iconic flax 27 daysailer, in summer 2021 installed the first NFC nacelle in the Netherlands, in a test program aiming at studying the performance of such new material in the wind industry.
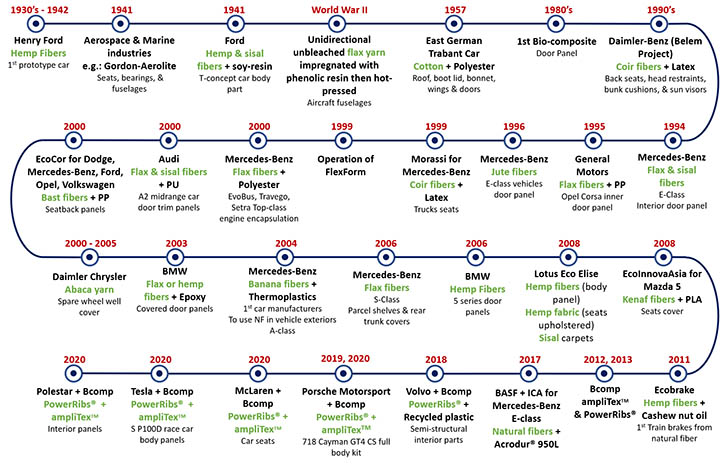
What’s holding NFCs back?
It’s a fact that natural fiber composites are still in their early adoption stages, despite their outstanding attributes. There are four major challenges facing NFCs, which are very important to understand to be able to define how to overcome them and to move forward.
- Lack of compatibility – Natural fibers are hydrophilic (they love water), and they are not perfectly compatible with most hydrophobic synthetic polymer matrix materials. Moreover, they have low thermal stability and cannot be heated beyond 200 C, so their use with thermoplastic polymers will be limited to low-melt polymers, such as polyolefins, including PP and PE. Further, they don’t bond well with the matrix because their surface functional groups do not react with functional groups of synthetic polymers. In addition, most of the natural fiber reinforcements have a coarse nature, so they are not easy to process into a textile form using conventional spinning and weaving methods of cotton.
- Complexity – Most natural fiber reinforcements are grown in developing countries, which don’t have much knowledge on composites, while most of the composite manufacturers are in developed countries, and they don’t have much knowledge on natural fibers. This is making it difficult to understand how to use such materials in new applications.
- Trialability – Most composite manufacturers are located in Western Europe, United States and Japan, and most of these countries do not grow natural fibers, with the exception of flax in France and Belgium. So, composite producers in these regions don’t have easy access to the wide range of possible natural fiber reinforcements for research and development.
- Communicability – This relates to how easy it is to communicate the benefits of this material. The most important benefits of using NFCs are indirect environmental benefits, including biodegradability or carbon footprint reduction. Unfortunately, in some cases such value proposition factors might not be convincing to customers who are more concerned about price, supply or performance.
Natural fiber reinforcements toolbox
Generally, natural fibers are classified into vegetable fibers from plant sources and animal fibers from animals and insects. However, we will find that most of the natural fiber reinforcements are vegetable fibers, specifically, bast, leaf and fruit fibers, as shown in Figure 3.
Examples of bast fibers include jute, which is the largest produced vegetable fiber after cotton primarily grown in Bangladesh and India. Also, flax is considered a bast fiber and it’s mostly grown in France, and archeological evidence confirm that flax was the first used fiber in human history. Another bast fiber is hemp, which belongs to the cannabis family and this association with Marijuana has led to a wide ban on cultivating it worldwide, but recently there has been an increasing interest in it, especially in the US. Other less popular examples of bast fibers are Ramie and Kenaf.
Furthermore, we are seeing enthusiastic researchers, engineers, architects and designers who are exploring new horizons for NFCs. For instance, recently an entire building façade in the Netherlands was made of hemp and biobased epoxy resin.
Examples of leaf fibers include sisal, which is a fiber extracted from a leaf of a cactus that belongs to the agave family native to South America, but it’s also grown in Kenya and other parts of Africa. Another amazing leaf fiber is the abaca, also known as the manila hemp, which is native to the Philippines and extracted from the leaves of a tree called Musa textilis, which is a close relative to the banana. Other types of leaf fibers include pineapple and banana fibers, which have been gaining popularity in recent years.
For the fruit fibers, the major type is the coir which is obtained from the husk surrounding the coconut fruit, and it’s mainly produced in India. Another less popular fruit fiber is the fiber obtained from the husk surrounding the oil palm fruit, but it hasn’t realized any commercial value up till now.
Bast fibers are designed by nature to be a reinforcement for the stem of the plant, so they tend to be finer and stiffer. Whereas leaf fibers are designed by nature to be pipelines inside the plant leaves and they are intended to transport moisture and nutrients, so the fibers tend be coarse and hollow and with higher failure strain and higher toughness as shown in Table 1.
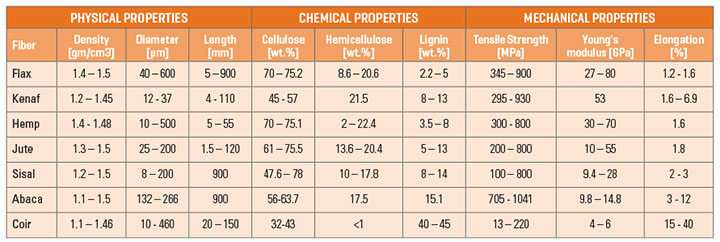
Processing of NFC
In order to use natural fiber reinforcements, they have to be converted into a textile preform with different possible structures similar to manmade reinforcements. The most popular structure is the nonwoven preform, which is usually blended (comingled) with 50% wt. polypropylene so that it can be directly compression molded for making automotive parts. Nonwovens provide the least performance due to the random fiber orientation and difficulty in achieving high fiber packing and consequently high fiber volume fraction. Yet, nonwoven reinforcements can be cost effective and can utilize hard fibers that are otherwise difficult to spin. Further, they provide a porous structure with up to 30% void content, which is important in achieving the desired levels of thermal insulation and vibration damping required in the automotive industry. The most important supplier to automotive tier 1 in the United State is FlexForm and in Europe is Ecotechnilin.
Other structures include woven twill preforms in different areal densities with higher performance and biaxial reinforcement in addition to a visually appealing pattern. Natural fiber preforms also include unidirectional tapes that come in width of 40 cm, which is made directly from sliver rather than yarns, with no twists and no interlacements, hence providing the maximum packing and maximum properties. Recently, several companies have been even offering unidirectional prepreg natural fibers, including Echotechnilin (France), BPreg (Turkey) and Composites Evolution (UK), in partnership with Bcomp, which also provides the highest performance, while still having good stability during handling due to the pre-impregnation.
While most of those preforms may be impregnated using commercial resins, there are certain companies that are making special formulations for natural fibers. Generally, polymeric matrix materials are divided into thermoplastics and thermosets. Thermoplastics are of higher interest to the automotive industry because of the short production cycles and recyclability. The most used thermoplastic is PP either in the form of fiber, powder or sheet. Yet, another important thermoplastic is PLA because it is biobased and can result in a fully biodegradable composite, but it is very expensive.
For the thermosetting resins common epoxy and polyester resins can be used, however there is increasing interest in biobased epoxy including formulations with plant oils such as soy, linseed and sunflower. The most popular supplier of biobased epoxy is Sicomin GreenPoxy, which provides formulations with up to 50% biobased content. But the best performance can be achieved with greenpoxy 33, which has 35 % biobased content.
NFC can be fabricated using most composite manufacturing techniques, but the processing parameters have to be optimized. The most important technique is compression molding, especially for natural fiber-PP composites that are used in automotive, as this is by far the technique most suitable for mass production. Another common technique is the vacuum assisted resin transfer molding (VARTM), which is more suited for larger structures that are produced in smaller quantities, including marine applications. Also, resin transfer molding (RTM) is a common technique for parts that require high surface finish on both sides, especially for smaller parts produced in larger quantities.
But before starting the fabrication process, a few points should be considered to achieve a good fiber matrix interfacial bonding. First, the fibers must be dry, because vegetable fibers can have up to 8% moisture content in normal conditions, which may result in at least 20% reduction in the composite performance. Also, if the fiber preform used is not initially developed for composite application it may contain spinning and processing lubricants, which may create a barrier layer between the fiber and the matrix. If this is the case, then the preform has to be washed or scoured and then thoroughly dried before using. Furthermore, for achieving the maximum performance, compatibilizers or coupling agents may be used to enhance the interfacial bonding. The most commonly used compatibilizer with PP matrix is maleic anhydride, and for thermosetting a matrix silane coupling agent is used.
Future trends
Nowadays, there is more interest in agriculture residues as feedstock for fiber extraction in order to achieve larger supply of natural fibers at affordable prices that can compete with manmade fibers. One of the recent innovations is PalmFil fiber, which is extracted from the frond and fruit stalks of date palms, which is a major agricultural crop in the Middle East and North Africa. And the fibers are said to have properties comparable to other high-performance vegetable fibers.
Natural fibers are emerging as a sustainable alternative to manmade reinforcements. The fibers have excellent environmental benefits, and their performance can be equivalent to glass fiber composites. And while there are certain barriers that are holding them back from diffusing into the mass market, there are companies and researchers who are pushing the limits and trying to overcome those barriers. Off-the-shelf reinforcements are available, offering similar performance to manmade preforms. Resin formulation are being specially developed for NFCs. And new natural fibers are being developed for composite applications. The future is green, and with the industry’s renewed interest in bio-based materials, natural fibers will prevail.
This article is based on a recent educational webinar by Dr. Mohamad Midani, as part of The Native Lab FREE course on Introduction to Composites. You can watch the recording on YouTube at https://www.youtube.com/watch?v=3Lt87LKaZUU and join the course for free at https://www.the nativelab.academy/courses/introduction-to-composites.
References
- Elseify LA, Midani M, El-Badawy A, Jawaid M (2021) “Manufacturing Automotive Components from Sustainable Natural Fiber Composites” Springer Nature.
- nova-Institut, (2021) “Solutions Made from Renewable Materials: Biocomposites”, Bioplastics Magazine [05/21] Vol. 16.