DREF spun polypropylene yarns are largely consumed in the manufacture of wound filters supplied to the domestic filtration sector. Suitability of alternative spinning systems can be explored to establish their use for water filtration application. This study compares the filtration performance of wound filters manufactured with DREF spun yarn and of that manufactured with roving (doubled) produced through the conventional route. Results show that the micron rating of filter wound with doubled roving yarn was better (@ 6 μm); the pressure drop experienced by it was higher (2.89 psi) which can influence its effective working life span. Practically the DREF spun yarn seems to be more suitable as an averaging effect is seen in terms of pressure drop (0.95 psi) and micron rating (90 μm) obtained.
Introduction
Though wound filters fall in the disposable type category; their performance greatly influences the life of final filter that is placed down the line in a water purification system. The prime requirement of filter media is that it should be porous or else the pressure drop experienced by it will be high which in turn can influence the particle retention efficiency. Literature available states that polypropylene (PP) yarns spun on DREF spun yarns are quite suitable and popular for being used as media for filtration purpose.[1] This is so, mainly due to its yarn characteristics like lower twist levels that result in its open structure. Twist level is indirectly reflected in the yarn diameter; higher twist results in greater compactness of yarn and lower diameter. If yarn contains higher level of twist then it will offer greater resistance to flow of water besides its ability to mechanically capture the suspended particles. In other words the porosity of yarn will be influenced due to the twist present in it and indirectly on the spinning system on which it is produced. Herein, we attempt to explore an alternative method to produce yarn for filtration application followed by comparing their respective performances.
Material and Methods
- Material
PP staple fibers having 51 mm length and 2.5 denier were used to produce yarn on the DREF spinning and the conventional spinning systems. - Methods
Yarn Manufacture
The purpose of the study was to analyze the influence of the spinning technique on the performance of the filter media in manufacture of wound filters. The ring spinning technique is referred to as the conventional method here while the usual method for producing the filter media is addressed as the DREF spun yarn using friction spinning technique. Slivers of known fineness were fed at a time to the DREF spinning machine that relies on aeromechanical principle[2] for yarn formation. The fibers were fed to the carding drum via the feed rollers from which they are conveyed to the nip of spinning drums and due to friction between them, fibers get twisted with yarn withdrawal occurring perpendicularly. The yarn was wound using a grooved drum to produce a cross-wound package.
Alternatively, similar kind of filter media can also be produced through the conventional (carded) route comprising of processing the staple fibers through the blow-room, card, draw-frame (one passage), simplex and the ring frame. But for the media produced in this trial, post draw frame, the sliver was given two additional passages (total three passages) followed by the final step of getting roving on Simplex. This roving was assembled to be used as feed package on two for one twister (TFO) to produce a cross wound package. The twist in the roving is very less so the structure is too porous. Earlier when DREF spinning machines were not available, the simplex roving were used as filter media but were produced with higher twist multiplier (twist); that could influence the porosity of yarn.
Yarn Characteristics
The DREF spun yarn and the doubled roving were checked for their characteristics in terms of count, yarn diameter, and twist as shown in Table 1 and Figure 1.
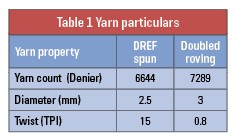
The yarn fineness was found by cutting and weighing method and the doubled roving was found to be coarser compared to the DREF spun yarn as is reflected by the difference in their respective diameters. The diameter of both the sample was found using Parco make traveling microscope. The value of yarn diameter was needed to calculate the wind ratio (equation 2) as well as to make an entry on the control panel of the winding machine. The diameter and twist are very closely related; in fact a yarn that has lower diameter would also contain higher turns[3]. But the means of twist insertion in both the yarn samples was different; hence a direct comparison is not suitable. Yet measurement was done to understand the yarn twist characteristics and its role in the performance of the wound filter. The twist in the doubled roving was found using twist contraction method at a gauge length of 10” while the twist in the DREF spun yarn was measured using twist to break method.
The photograph shown above in Figure 1 (a) is of the doubled roving and the twist binding the two rovings can also be clearly seen. The roving was cut and the individual strands were separated; seen in Figure 1 (b & c). The individual rovings contained minimal twist but that was not measured.
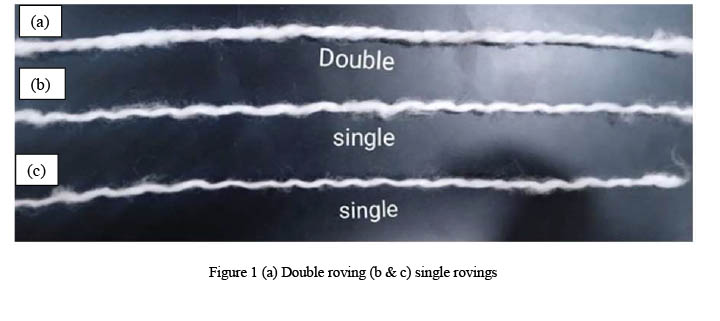
Wound Filter Manufacture
The wound filters were produced on specially designed filter winder[4] that can be operated, on flexi mode[5]. The packages were produced on precision winding mode for this study keeping an average tension of 55 g, package diameter of 65 mm and two circumferential diamonds. The winding calculations were done using equation 1 and equation 2 where the yarn diameter of DREF spun yarn and for doubled roving was taken as 2.5 mm and 3 mm respectively.
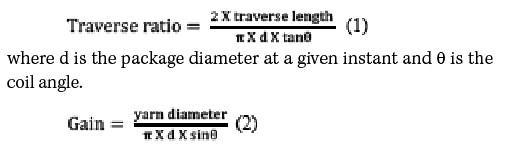
The packages were produced with almost similar wind ratios of 5.235 and 5.2321 respectively for DREF yarn and doubled roving so that, the characteristics could be maintained. Previous works have already discussed the winding calculations as well as the influence of winding parameters on the wound filter performance.[6, 7, 8, 9 & 10]
Wound Filter Testing
The wound filters were tested in-house[11] using ASTM F749 [12] test method under constant flow rate conditions. This is a destructive test method where duration of test trial was one hour with slurry concentration of 0.1 g/L. The pressure drop was noted after every 15 minutes while the micron rating was obtained from the microscopic analysis of particles present in the inlet and outlet water samples collected at the end of the test.
Results and Discussion
- Pressure Drop Characteristics
Figure 2 shows pressure characteristics of wound filter produced using DREF spun yarn.
It can be seen from Figure 2 that in the initial part of the test, (up to 20 minutes) there was hardly any change in the pressure drop. But after that a steady rise was observed till it reached approximately to 0.95 psi before terminating the test. Figure 3 shows pressure characteristics of wound filter produced using doubled roving.
It can be seen from Figure 3 that in the initial part of the test, (up to 20 minutes) there was hardly any change in the pressure drop. But after that a steady rise was observed in it till it reached approximately to 2.86 psi; when the test was terminated. Figure 4 shows the comparative results of pressure characteristics of wound filter produced from the DREF spun yarn and that produced from doubled roving.
The doubled roving showed higher pressure drop (2.86 psi) compared to its counterpart (0.95 psi). This indirectly implies that the wound filter produced using doubled roving yarn showed greater resistance to passage of water in spite of keeping similar winding parameters. The main reason behind this could be due to the use of doubled roving even though the twist was only nominal. Build-up of higher pressure drop is not favorable for the life of filter since it will essentially result in the need of early replacement.
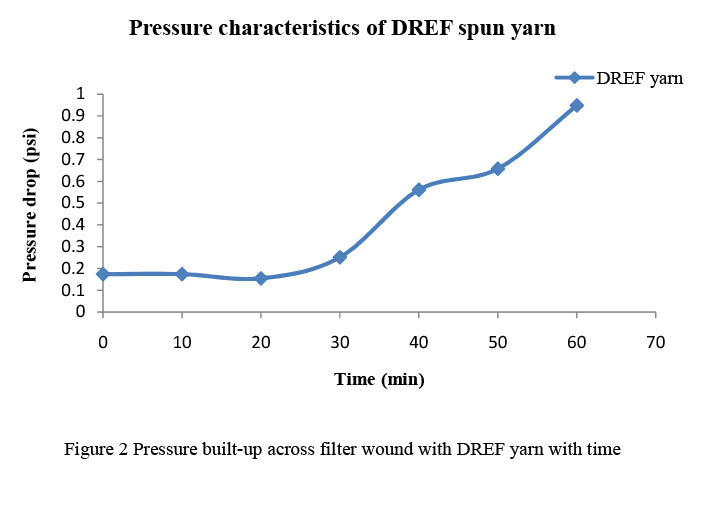
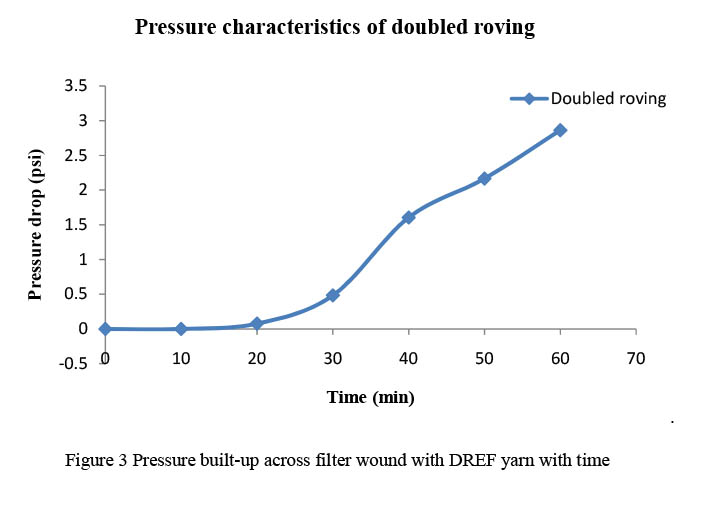
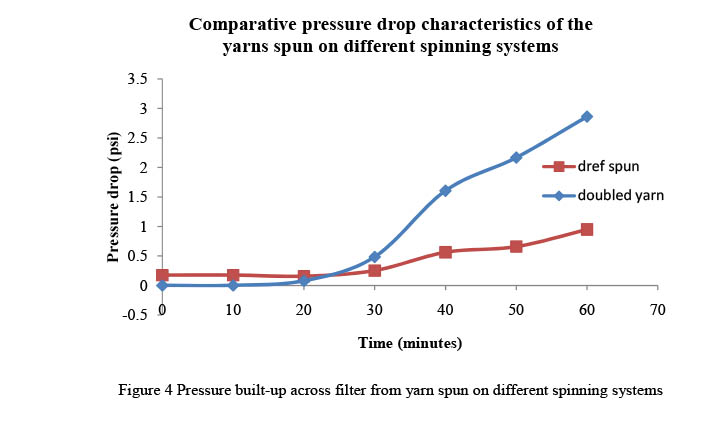
Retention Characteristics
Figure 5 shows the change in % frequency of particles present in the inlet and filtrate water samples of the wound filters manufactured from DREF yarn. It can be observed from Figure 5 that the % frequency of almost all particles in the outlet is less than the inlet except particles with an average size of 30 μm. It can be an indication of mechanical failure of the filter to trap the mentioned particle size and may need further test time to draw appropriate conclusion.
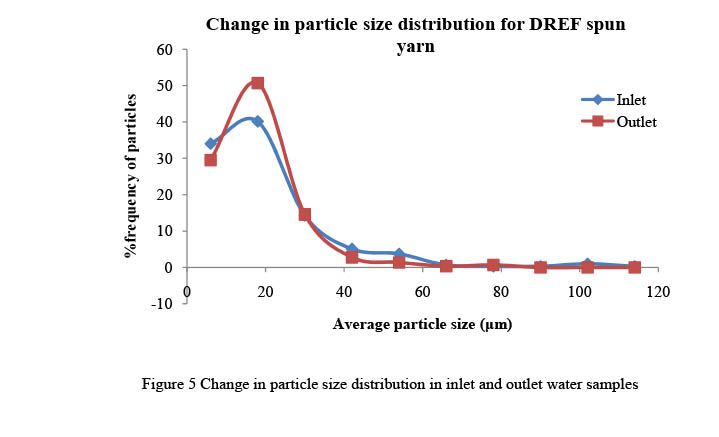
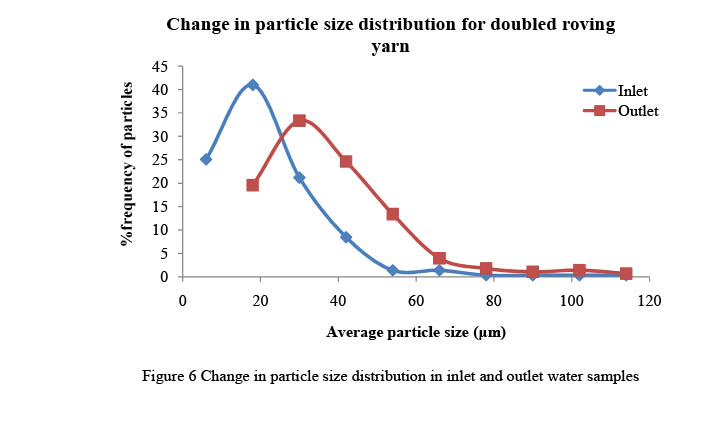
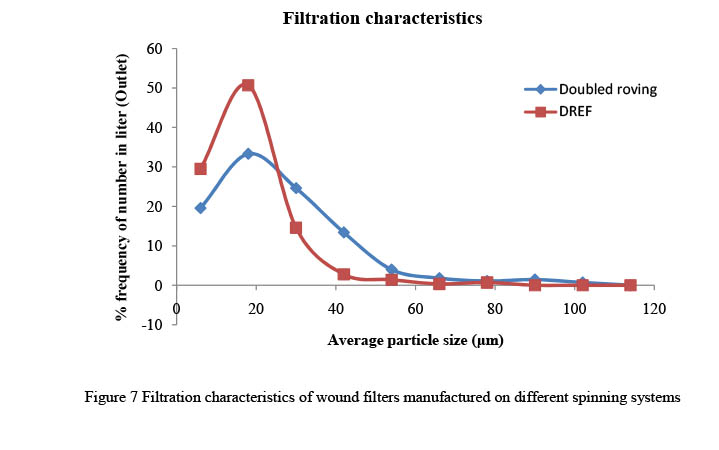
Figure 6 shows the change in % frequency of particles present in the inlet and filtrate water samples of the wound filters manufactured from doubled roving. It can be observed from
Figure 6 that the % frequency of all particles in the outlet is less than the inlet, however a shift in the distribution is also observed.
Figure 7 shows the comparative change in % frequency of particles present in the filtrate water samples of the wound filters manufactured from DREF yarn and doubled roving. It can be observed from Figure 7 that the % frequency of all particles is much less for filter wound with doubled roving than that produced with DREF spun yarn.
The micron rating of filters produced with DREF spun yarn and doubled roving was 90 μm and @ 6 μm respectively. Figure 8 shows the dirt holding capacities of different filters.
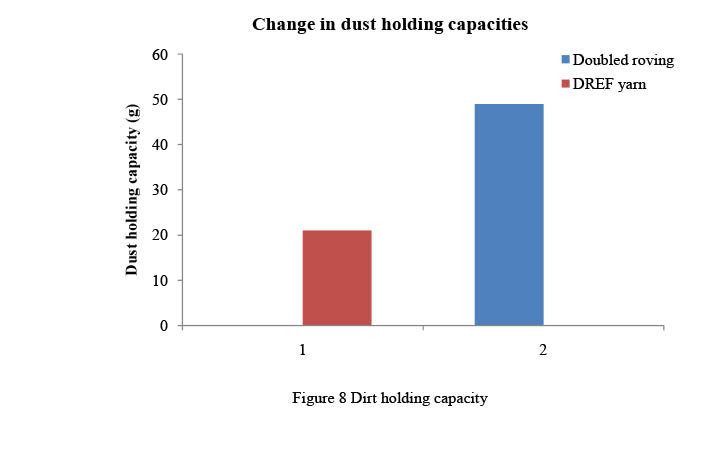
The results from Figure 8 show that doubled roving filter was able to hold greater quantity of dust that is mainly due to greater surface area available to the particles for getting deposited. This measurement was done after the filter test by allowing the filter to dry completely and then weighing it. As mentioned in the earlier part of the text, even though the apparent difference between the ratings of the two wound filters is large, yet as far as the performance of wound filter is concerned combined weightage is given to both, the pressure drop as well as the micron rating. A wound filter that exhibits higher pressure drop will get clogged sooner, requiring it to be replaced sooner. Thus life expectancy of filter wound with doubled roving yarn would be less though its filtration efficiency is higher. Thus as a disposable filter, wound filters produced from DREF spun yarn seem to be more suitable as pre-filter for removing coarser particles with longer life; resulting in filtering more quantity of water in the long run. The doubled roving yarn may be suitable in applications similar to the role of a final filter and need to be explored further with other variations in the winding parameters for drawing any solid conclusion regarding their use.
Conclusions
The idea of using an alternative technique to produce yarn for filtration purpose was successful. Pressure drop and micron rating in case of filter wound with doubled roving were 2.86 psi and @ 6 μm while the filter wound with the DREF spun yarn showed values of 0.95 psi and 90 μm respectively. Hence for practical applications DREF spun yarns seem to be a more suitable option than the doubled roving yarn. As far as the performance of wound filters produced with DREF spun yarns is concerned it can be improved further by choosing appropriate winding variables. However, the authors feel the necessity to carry out further trials so that better clarity can be achieved, nonetheless it’s a very promising alternative. The work can be extended further by carrying out similar experimental trials on the spinning systems and winding system to work out a suitable alternative.
The authors would like to express their gratitude to the Zenith fibers Pvt. Ltd. for providing the raw material and lab staff members of Textile Engineering Department, The Maharaja Sayajirao University of Baroda, for their help.
References:
- A J Sonagra, Bipasha Maiti, C R Prayag and Dr. S R Vengsarkar. Use of DREF technology for specific end uses in technical textiles – Case study. ATIRA commun. Textiles. 2007; 41 (3), 47.
- W Klein, (1998) 2nd ed., Vol. 6, pp 17-20, Text. Inst., United Kingdom.
- P S Kanade and S S Bhattacharya. Designing a cartridge winder with electronic controls. J. Eng. fibers and fabr. 2007; 9, 112.
- P S Kanade. Development of Flexi/Dual Winding System. J. Eng. fibers and fabr. 2015; 10 (4), 160.
- P S Kanade and S S Bhattacharya. Influence of winding parameters on the performance of string wound filter cartridges – part – I. The filtr. J. 2013; 13 (4), 222.
- P S Kanade and S S Bhattacharya. Influence of winding parameters on the performance of string wound filter cartridges – part – II. The filtr. J. 2014; 14 (3), 152.
- P S Kanade and T A Desai. How coil spacing affects graded filters. Filtr. & Sep. 2017; 54 (5), 39.
- P S Kanade and T A Desai. Improved design of wound filters for enhanced water filtration performance. J. Sci. Ind. Res. 2018; 77, 237.
- P S Kanade, M V Koranne and T A Desai. Analysis of wound filter performance from DREF yarn spun at different suction pressure. Alexandria Engg. J. 2017; 56 (9), 115.
- P S Kanade and S S Bhattacharya. Developing a test rig for string wound filter cartridges using water as the medium. Int J Adv Res Engg & Technol (IJARET). 2013; 4, 290.
- ASTM F 795 – 88. “Standard practice for determining the performance of a filter medium employing a single-pass, constant rate, liquid test”.1988 Dec.