Growing Avenues to Sustainability are What Took Center Stage in Nonwoven Advancements
The international nonwovens community came together in droves, excited to, once again, be in Geneva for April’s INDEX™23. The event showcases a massive global presence, with 610 exhibitors from 43 countries showcasing products throughout 50,000 m² of gross exhibition space. The number of attendees increased from 2,021 to 12,017 representing over 100 countries. The energy of the event was felt all over the two-tiered show floor.
“We are here to do business, but the nonwovens industry showed me that our supply chain is also one big family,” said Murat Dogru, EDANA’s General Manager. “It was a real pleasure to see the industry reunited once again in person to exchange, smile, negotiate, network, debate, and much more as we addressed challenges and discussed innovations.”
“It has been heartwarming to see so many representatives from the younger generations who feed the industry’s need in terms of new ideas, sustainable solutions, and business architecture,” added Pieter Meijer, Chairman of the INDEX™ Advisory Board.
Discussions with exhibitors uncovered the massive investments in green initiatives that will bring nonwoven producers more options in the future to meet sustainability goals being imposed on the industry – both internally and externally.
Medical Sector Discussion
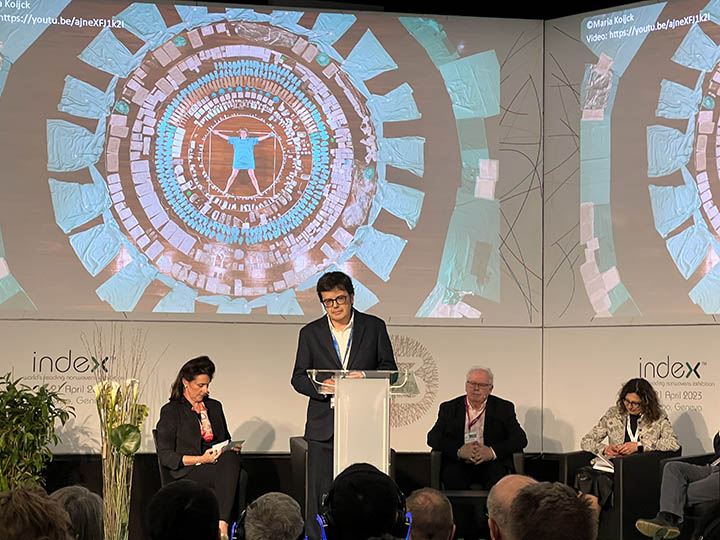
The most in-depth discussion centered around medical nonwovens, which was highlighted as a massive source of waste, with single use items the biggest culprit. Berry Global’s Robert Garcia, application and product development director, EMEIA hygiene and healthcare, defined the acute COVID-driven problem with statistics. Between 2019 and 2020, the overall increase in global import volume of nonwoven medical went from .86 M tons to 1.1 M tons. Berry Global identified that recycling solutions for medical waste were the best option to reduce CO2, based a six-month study of PPE products. For instance, they discovered that by using reusable gowns, CO2 could be reduced by 17%, and by recycling gowns, 35%. In the process of seeking recyclability in 2020, they encountered huge obstacles to green initiatives, including lack of infrastructure, legislative support and users’ behavior in efforts to recycle facemasks in 2020 within the company.
“Recycling is the way. We tried to recycle as producers, and we couldn’t. There were no solution providers. Only in the U.K. were we able to collect used facemasks,” Garcia said. “Another way must be possible. Survival of the planet and the industry is possible if we all get engaged and share a vision. Vision with passion moves the world forward.”
The company created collaborated on a project with Mölnlycke, a global medical solutions company with corporate headquarters in Gothenburg, Sweden, to collect and recycle scrubs. It was based on collection/melting, re-pelletization, and molding being the circular ambitions, and yielded positive results.
As of July 2023, Berry is now working with Deaconess Midtown Hospital and Nexus Circular to initiate circular collaboration that restores sterile, pre-surgery plastic packaging and unused fabrics to productive use. Deaconess Midtown Hospital’s Surgical Center is collecting around 500 pounds per week – 350 bags – of clean, used plastics from the hospital’s surgical suite, pharmaceutical, laboratory, and warehouse and are diverted from landfills.
Strategic sourcing manager Pontus Lindstedt at Mölnlycke discussed the company’s sustainability efforts. He noted that if healthcare was a country, it would be the fifth largest CO2 emitter, and said, “Our company is very dependent on this industry to decarbonize our business,” calling for sustainable healthcare options. “We want to see more supply chain transparency to get more data.”
SABIC’s Jelena Bozovic-Vukic, MDTS, market developer and technical service engineer, made a push for safer chemistry designed for recycling in polymer production. She highlighted circular renewable polymers– contributing to a bio-based economy, and certified circular polymers – contributing to waste management. Both options reduce fossil feedstock dependency and improve CO2 levels. SABIC’s
vision for the future is that plastic should never end up in the environment, landfill or oceans and instead is reused and remade into new products. TRUCIRCLE™ is SABIC’s vision that requires a total transformation of the value chain, with a closed loop for plastics using circular and renewable products, as well as mechanical recycling and ultimately design for recyclability.
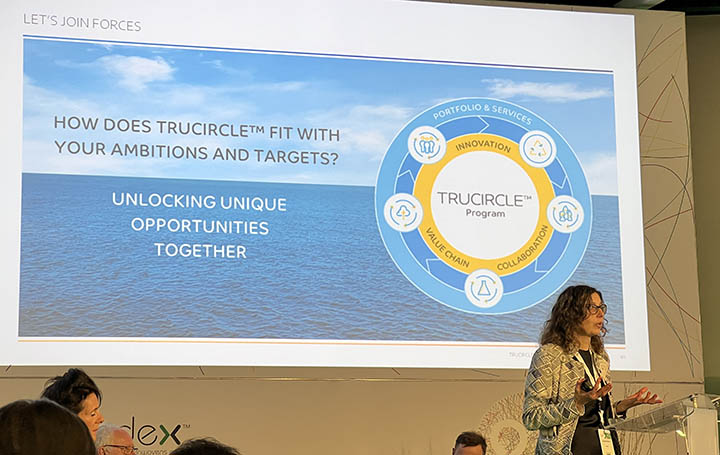
Rounding out the conversation, David Scheeres, director, Thermal Compaction Group Ltd. presented on Sterimelt. This mechanical process turns a disposal cost into a revenue, according to Scheeres. “Our innovative and sustainable technologies re-engineer single-use disposable non-woven (SMS) polypropylene products such as sterilization wrap, patient transfer sheets, scrubs, gowns, drapes and even face masks into a recovered resource, thus enabling what was a single use disposable plastic to become a multi-use plastic by reintroducing it back into the supply chain as new products, diverting single-use plastics away from incineration and or landfill.”
Green Exposition
Walking the Expo, one could witness the focus on green technology dominating the show floor. International Fiber Journal talked to some to see what they are offering to the marketplace.
Algaeing – Building upon their algae-based dye formulation that is 100% biodegradable and offers inherently stunning tones, the company is now in the fiber space with threads made from algae and cellulose, and hued with Algadye 3.0 dye. The company shows plants growing through textiles that simulated discarded waste, to illustrate the biodegradability of the product.
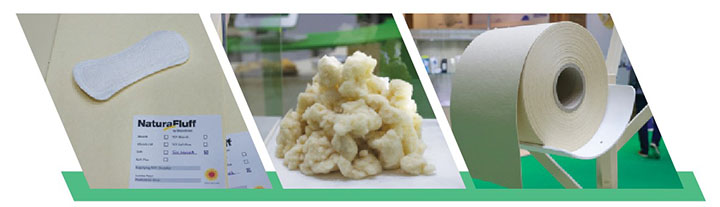
NatureWorks – The company touts their low-carbon alternative to petrochemical-based plastics and fibers, called Ingeo 6500D – a biopolymer, made from renewable bio-based feedstocks that makes the products we use every day safer and more sustainable. Ingeo 6500D has a wide range of applications including extrusion and thermoforming, injection molding, films and cards, fibers and nonwovens, and 3D printing. Delivering enhanced fluid management for hygiene applications, it boasts improved tensile strength and up to a 40% increase in softness that offers a better performing spunbond nonwoven that minimizes converting challenges while providing a 62% smaller carbon footprint.
“Building on our expertise in bio-based nonwovens, we developed a product that, based on our rigorous testing, can improve the softness of spunbound nonwovens by 40% over nonwovens made with generic PLA,” says Robert Green, vice president of performance polymers, at NatureWorks. “The tensile strength of the new Ingeo solution offers improved processing for converters while offering efficient low basis weight fabric production on the latest generation of spunbond equipment. We are looking forward to collaborating with the supply chain as we continue the development of this new Ingeo solution in nonwoven applications including diapers and wipes.”
Stora Enso – NaturaFluff Eco is a new product from the company that can be utilized in hygiene products like baby and feminine care, adult incontinence, and air-laid nonwovens. NaturaFluff Eco only differs from traditional fluff pulp in two ways: color and carbon footprint. It is an oxygen delignified fluff pulp. To produce it, there is bleaching of the pulp. Instead, it is treated with oxygen to remove the lignin. As a result, this fluff pulp is of a warm natural beige color and has a roughly 30% lower carbon footprint in comparison to traditional fluff pulp, but its performance isn’t altered. It also benefits from FSC® and PEFC™ chain-of-custody certified products from sustainably managed forests.
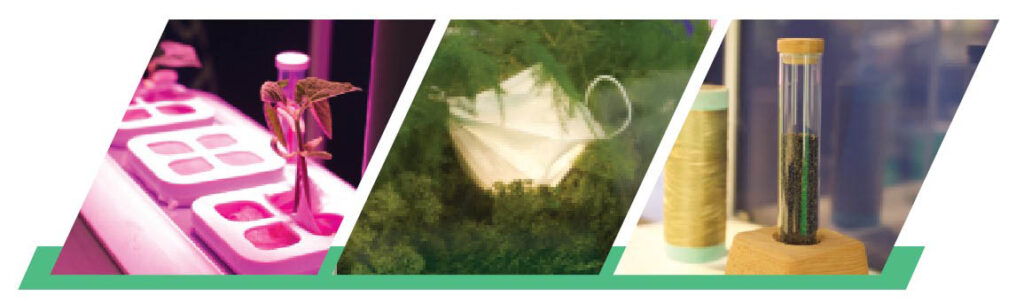
Fiberpartner® – The winner of an INDEX® Raw Materials or Components Innovation Award for BicoBio, a future proof biocomponent fibre which has a core sheath construction developed from sustainable materials with low carbon footprint. The component was designed to biodegrade in soil and water. The bio-based PE is produced from sugar cane, with a negative carbon footprint. The Recycled PET is GRS certified, and PrimaLoft® Bio™ is a cutting-edge technology that enables polyester and fabric fibres to biodegrade in the environment. BicoBio fibres can be processed in a variety of nonwoven technologies, such as airthrough, thermobonded, carded and airlaid. The core mission is to fix polyester, and the technology is a break-through innovation that has the potential to change the polyester industry.
To test production, ANDRITZ has tried the biodegradable* PET 1,4 den spunlace nonwoven fiber on their carded and Jetlace hydro-entanglement process. Production trials were done on the ANDRITZ Perfojet pilot line in Montbonnot, France. The company produced nonwoven spunlace fabrics from 35 to 50 gsm, with 100% PET PrimaLoft® Bio™ fiber. As a result, the fibers are confirmed processing by the ANDRITZ spunlace systems as other standard PET fibers.
Akinal – BioFlush® is the company’s multi-purpose hygiene cleaning product suitable for different uses. The company markets the 100% flushable and biodegradable nonwoven for use as baby wet wipes or wet toilet paper. It produces BioFlush® from 100% natural raw materials and uses no chemicals. It has CTP Laboratory Certification and meets the EDAN and INDA guidelines.
GP Cellulose – Golden Isles CO® Fluff Pulp for feminine care, baby diapers and adult incontinence products is how the company provides environmental benefits to nonwovens customers. The thinner product profiles allow manufacturers to compress cores to create higher density, thinner products without sacrificing softness and flexibility. Fiber is sourced from southern coastal pine forests that are responsibly managed and certified. Golden Isles CO® fluff pulps are made from a coarse, bulky, long fiber and are used in a variety of absorbent applications – offering optimum fluid retention, liquid distribution (wicking), and pad integrity. This is especially important with thinner products and with the use of super-absorbent polymers. Supply chain savings include smaller packages and the potential for increased package counts.
Sparkle – Making a splash for their biobased Sparkle sanitary pads, the company is now developing Sugar Fluff,™ a wood-free, sustainable, and cost-effective fluff designed for absorbent hygiene products, and made from bagasse fibers – dry pulpy fibrous material that remains after crushing sugarcane. The company says it is high performing, as well as circular, including the bonus that no extra land is required to grow bagasse fibers as fibers are readily available from the sugar industry.
OrganoClick – The nonwovens industry is dependent on binders used to improve the mechanical properties of nonwoven and technical textiles, and common binders are mainly made of fossil plastic polymers such as ethyl vinyl acetate (EVA) and acrylates. OrganoClick has developed the 100% biobased binder OC-BioBinder™ which is based on biopolymers from residual streams in the food industry such as orange peel, shrimp shells and wheat bran. With the help of these bio-binders, nonwoven and technical textiles can become 100% biodegradable, non-toxic and 100% compostable. The bio-based and biodegradable binders are adapted for several different nonwovens and specialty papers such as airlaid, wetlaid, spunlace, spunbond, carded, and drylaid. The binders are available in varying degrees of softness, (Tg), with different degrees of dry and wet strength, and that are hydrophilic or hydrophobic. They also offer binders that improve fire protection. They offer other bio-brands, such as the biocomposite OrganoComp – also 100% biodegradable, renewable, toxin-free and made from residual streams in the food industry.
Suzano – The company’s core product, Eucafluff® is the world’s first eucalyptus fluff and is a renewable-source raw material with a smaller carbon footprint, while simultaneously providing end consumers with a more efficient product that offers greater well-being. It is an innovative product designed for disposable sanitary absorbent products and other personal hygiene items, such as baby diapers, adult incontinence products, pet pads and for use in hospital supplies. As a sustainable solution from a renewable source, it offers companies the benefits of the lower carbon footprint.
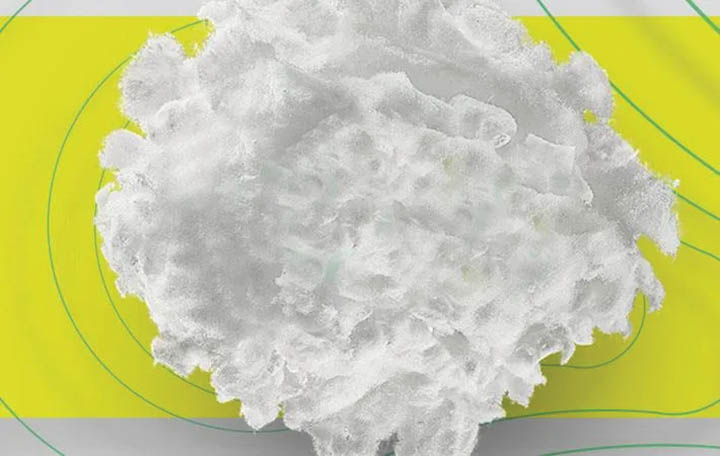
Bast Fibre Technologies Inc. – The natural hemp fibre sero™ is designed as Bast Fibre’s product that meets the rigorous technical standards required by commercial fabric manufacturing, including hygiene applications. It is a plug-and-play replacement for synthetic fibre, made from a highly efficient renewable agricultural crop that is one of the best natural sources of fibre. sero™ natural hemp fibre enables manufacturers to create consumer products with a circular, soil-to-soil lifecycle. Beyond plant based, sero™ is intact plant fibre, ideal for creating next-generation sustainable consumer products. It has the qualities of being natural, strong, clean and bright, soft and absorbent, with the environmental benefits of true sustainability, zero plastic, forest friendly, and 100% compostable.
UPM – Lignin is a 100% bio-based substance that can be found in the cell walls of all plants and especially trees. UPM BioPiva™ lignin is a versatile natural polymer, verifiably non-toxic and responsible sourced raw material. Lignin plays an important role in the natural carbon cycle by binding atmospheric carbon dioxide and serving as a long-term carbon storage. The goal is to transform the sustainability performance of products and help radically improve manufacturers CO₂ footprint. UPM BioPiva™ 100 is a purified, kraft softwood lignin that can be used in various applications. It is a non-toxic product from renewable sources. UPM BioPiva™ 100 can be used to replace and to reduce the usage of fossil-based materials without compromising the performance.
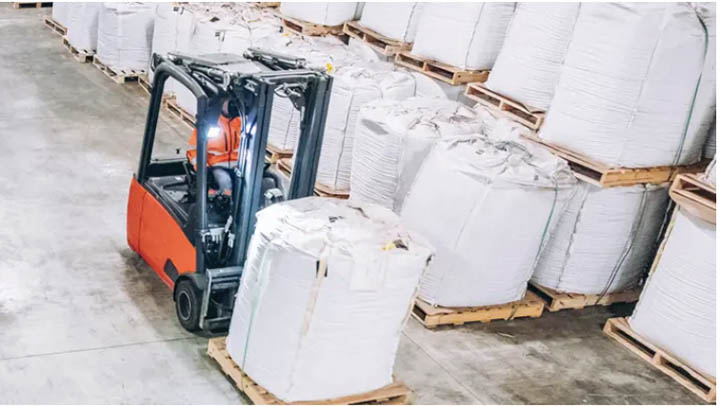
Lenzing — The environmentally-sound offerings from Lenzing are numerous, and under continual advancement. The company has dedicated its resources to making the most of wood-based fiber solutions, while also leading the way in corporate environmental sustainability measures. Tencel™, EcoVero™ and Veocel™ provide non-woven manufacturers with options. EcoVero™ viscose fibers have a lower environmental impact than generic viscose, according to Higg MSI. Veocel™ Lyocell fibers are the latest generation of fibers with botanic origin which combine advanced performance, comfort and sustainability for everyday consumer needs. Unique physical properties lead to their high-tenacity profile in both dry and wet states, efficient absorbency and gentleness to skin for multiple hygiene applications.
INDEX™ Awards: 2023 Winning Entries

Open to products that were made commercially available by January 31, 2023, and selected by a jury of experienced industry peers, EDANA’s INDEX™ Awards for “Excellence in the nonwovens and related industries” are the highest accolade for distinction in the nonwovens value chain. Here are the winners for 2023:
- Nonwoven roll goods
Winner: Suominen – HYDRASPUN® Circula Nonwoven
HYDRASPUN® Circula is one the first nonwovens on the market to be produced with recycled paper and virgin cellulosic fibres. It is challenging to use a waste source as a raw material in nonwovens due to high quality and hygiene requirements, which makes HYDRASPUN® Circula stand out as a successful example of innovation. - Finished products made from, or incorporating nonwovens
Winner: Henkel – Smart Adult Care
Smart Adult Care transforms a conventional diaper into a smart, connected medical device. This is a vital step into the future of patient-centered care and smart hygiene services. Equipped with a lightweight, flexible printed sensor and reusable pod, the diaper enables remote monitoring of moisture, movement, and temperature. It was developed in cooperation with Henkel’s IoT partner Smartz AG. - Raw materials or components (e.g., fibre, binder, polymer, tape), of special relevance to the nonwovens industry and related converted products
Winner: Fiberpartner – BicoBio
A future proof bicomponent fibre core sheath construction, developed from materials with a low carbon footprint, this component was designed to biodegrade in the environments where most plastics eventually find themselves: landfills and ocean water.
- The bio-based PE is produced from sugar cane and has a negative carbon footprint.
- The Recycled PET is GRS certified.
- PrimaLoft® Bio™ an additive technology that enables polyester and fabric fibres to biodegrade in the environment.
- Innovation in machinery of special relevance to the nonwovens industry
Winner: Curt G. Joa, Inc. – ESC-8™
JOA’s ESC-8™ Electronic Size Change unit offers a previously unavailable push-button product changeover technology. It uses numerous methods and processes that are truly unique to in-line product changeover and flexibility. As one example, each absorbent insert carriage within the ESC-8™ unit is controlled and cammed independently leading to unparalleled process flexibility and user control. - Sustainable Product
Winner: Sparkle Innovations – SugaFluff™
Made from bagasse fibers, SugaFluff™ offers a wood-free, sustainable, cost-effective, high performing and truly circular alternative source of fluff pulp for absorbent hygiene products. No extra land is required to grow bagasse fibres for SugaFluff,™ as sugarcane bagasse is an abundantly available by-product of the sugar industry.