Staple fiber represents nearly two-thirds (59%) of the resin and staple fiber used in the nonwovens industry. The consumption of staple fibers by drylaid, wetlaid, and airlaid short-fiber nonwovens production in 2018 was about 8.8 million tonnes, 35% more than five years before.
The worldwide production of nonwoven roll goods reached 14.9 million tonnes in 2018. The tonnage volume was equal to about 459 billion square meters in 2018. INDA and EDANA forecast that worldwide nonwovens production will continue to grow, and expect that in the period from 2018 through 2023, the industry will expand at an annual average rate of 4.8%, reaching a volume of at least 18.7 million tonnes
Staple fiber represents nearly two-thirds (59%) of the resin and staple fiber used in the nonwovens industry. The consumption of staple fibers by drylaid, wetlaid, and airlaid short-fiber nonwovens production in 2018 was about 8.8 million tonnes, 35% more than five years before. Fiber consumption is expected to continue to increase by 4.0% per year to 10.8 million tonnes in 2023.
Man-made fibers (shades of orange in the figure) account for two-thirds (62%) of the staple fiber consumption, with natural fibers (shades of blue) making up the remaining (38%).
Polyester staple, in both virgin and recycled, now accounts for more than half (58%) of the man-made fibers and 36% of the overall staple fiber consumed by nonwovens (see figure). While a large portion of the virgin polyester staple fiber can be attributed to the production of hydroentangled materials destined for the wipes industry, the vehicle sector (carpeting, trunk liners, and other noise, vibration, and harshness products) consumes large volumes of fiber for heavier weight needlepunch products made of recycled polyester fibers.
The consumption of polyester staple, both virgin and recycled, is expected to increase to 3.9 million tonnes by 2023, equivalent to 4.0% annual growth. Major single-use or disposable end markets for polyester staple are wipes, filtration, surgical packs and gowns (mostly produced by drylaid-hydroentangled technology). Important durable end markets include home & office furnishings, geosynthetics, interlinings, and transportation, all markets that are forecast to expand globally.
Polyester staple volume used in fiberfill — not produced in a nonwoven process — applications, such as bedding or apparel insulation, are not included in these figures. Worldwide, polyester used in fiberfill applications is roughly estimated to be at least 900,000 tonnes.
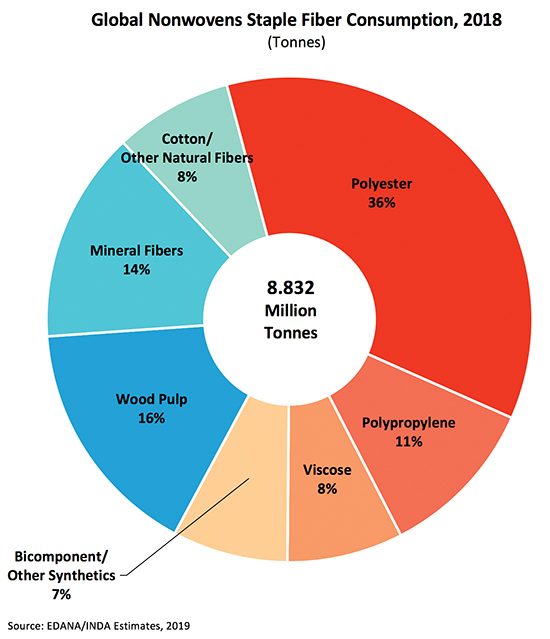
An estimated 952,000 tonnes of polypropylene staple fibers were consumed by the global nonwoven industry in 2018, accounting for 11% of all staple fiber consumed by nonwovens. While polypropylene staple fiber usage has declined in the disposable market, in particular the demand for drylaid thermal-bonded coverstock materials (only partly compensated by utilization of airlaid), this fiber continues to grow in supplying the durable nonwovens market. Most of the large durable end markets for polypropylene staple fibers are needlepunch durables. The major markets that consume needlepunch polypropylene include geotextiles, vehicle components, coating substrate, indoor/outdoor carpeting, blankets, upholstered furnishings and bedding. The worldwide forecast for 2023 polypropylene staple demand is 1.1 million tonnes.
Compared to the 2013 situation, it is estimated that 162,000 additional tonnes of viscose (rayon) staple were consumed by the global nonwovens industry in 2018, mainly driven by the wipes and medical products industries. The estimate for worldwide consumption of viscose in 2018 was 682,000 tonnes, and consumption of this fiber is forecast to grow to more than 821,000 tonnes by the end of 2023.
Nonetheless, the consumption of viscose in wipe applications is quite sensitive to viscose’s cost in relation to alternative fibers. Indeed, viscose is normally blended with polyester to produce hydroentangled wipes substrate. The blend for wipes is typically a 50/50 or 60/40 ratio. Viscose used to be the higher percentage of the mix due to its softness and hydrophilic properties. However, viscose staple can be more expensive than polyester. Therefore, the blend ratio can change so that less viscose and more polyester is used as a cost reduction measure. Any significant further rise of viscose’s price above polyester could lead to increased substitution and lower viscose’s volume outlook.
Bicomponent and other synthetic fibers consumed in 2018 were approximately 680,000 tonnes. Bicomponent fibers are increasingly important in nonwovens. There are several types of bicomponent fibers: (a) binder fibers used generally in fiberfill and airlaid short-fiber production; (b) splittable bicomponent fibers that can be divided into micro denier by the hydroentangle process and (c) self-crimping fibers generally consumed by needlepunch production.
The main markets for bicomponent fibers include the acquisition/distribution layers of diapers and feminine sanitary products, airlaid nonwoven binder fiber, needlepunch and fiberfill. All of these end markets are growing and will drive bicomponent fiber consumption. This market is forecast to rise to 827,000 tonnes by 2023.
Wood pulp consumed by airlaid short-fiber, drylaid hydroentangle, spunlaid coform, and wetlaid processes totaled about 1,417,000 tonnes in 2018. Wood pulp consumption is expected to rise to 1,725,000 tonnes by 2023. The gain is a result of the expectation that airlaid short-fiber nonwoven will continue to replace line-formed absorbent cores on the adult diapers and feminine sanitary production lines. This increased volume does not translate into an increasing pulp demand, rather, a replacement of existing volume. The swing to using airlaid short-fiber in North American feminine napkins is almost complete, and there is high consumption by adult diapers.
Mineral fibers — including carbon, ceramic, carbon and metal fibers — are extensively used in North America. According to INDA figures, of the 1,245,000 tonnes used by the global nonwovens industry in 2018, the North American industry, alone, consumed 643,000 tonnes, of which 87% was consumed in the wetlaid process. Glass fiber is made from extremely fine fibers of glass. It is a lightweight, extremely strong, and robust material. Glass fibers have applications in filtration, transportation, construction, electronics, wind energy, industrial, and others. Mineral fibers are often used in the production of wetlaid nonwovens; however, they are also used in airlaid short-fiber and drylaid needlepunch processes.
While worldwide consumption of cotton fiber by nonwoven productions in 2018 was still relatively small, the use of other natural fibers such as jute, flax or hemp is increasing. Both cotton and natural fibers, together, accounted for not more than 3% of the fibers consumed in nonwovens. Cotton is also used in many other domestic and personal care products, such as medical sponges, pharmaceutical coil, disposable wipes, tampons, cosmetic pads, beauty coils, jeweler padding and several other miscellaneous products. Although produced from a garnet or carding system, these uses are not generally counted as nonwovens production.
The content of this article is based on data from the “A Worldwide Outlook of the Nonwovens Industry 2018-2023 Base” report by INDA and EDANA. For more information on this report, visit inda.org.
* International Fiber Journal is owned by INDA, Association of the Nonwoven Fabrics Industry.