Selecting the Textile Construction Method That Ensures End Item Performance
Woven narrow fabrics can serve as structure or substrate for components in critical customer applications that require superior properties. End product designers and engineers should understand weaving technology and how it differs from other textile production so they can correctly select a textile construction method that ensures end item performance.
Weaving of Narrow Fabrics – The Basics
Weaving is a method of creating a structural textile by interlacing fibers and yarns in a way that maximizes specific fiber properties. Weaving yarns are interlaced in a perpendicular manner, with both longitudinal yarns (x-direction), and horizontal yarns (y-direction). Known respectively as warp and weft or filling yarns, they are oriented at 90 degrees to each other.
Weaving produces a stable construction in both the x and y directions. In fact, of all the available methods used to create textile material, weaving provides the most stable and versatile construct. Key properties include high strength, elongation, energy absorption, optimum strength to weight ratios, flexibility, and sewability.
Narrow fabrics are generally divided into two types: webbing and tape. Webbing, narrow fabrics 12 inches wide or less, refers to fabric with a longitudinal strength equal to or greater than 1000 pounds per inch of width. Tape refers to narrow fabrics with a longitudinal strength of less than 1000 pounds per inch of width.

Both shuttle looms and needle looms are used to manufacture both structural webbing and tape. The needle loom is designed for speed and is the best option for large runs of production material. A shuttle loom enables more weave design versatility and provides structural, uniform, and woven edges that results in more even loading across the webbing’s width. This method is preferred for applications requiring maximum weave design flexibility. Flat woven, tubular material and 3-D fabrics can all be produced with perfect symmetry on both edges of the woven substrate. This provides uniform edge loading during, for example, high-speed deployment of parachutes.
Weaving is a method of creating a structural textile by interlacing fibers and yarns in a way that maximizes specific fiber properties.
Weave Design Options
Several weave designs are available to meet specific application requirements.
- Plain weave is the simplest form of weaving. The filling/weft is inserted up and down every other warp yarn. Edge binding and reinforcement tapes utilize plain weave designs due to their need for high structural stability and minimum surface abrasion.
- Twill weave involves passing the filling/weft yarn over or under two more warp yarns. It is generally softer and more pliable than a plain weave and has increased tensile and decreased elongation properties. Twill constructions are used to bind edges with complex curves and tight corners and for high strength applications that require maximum strength of the woven warp yarns.
- Tubular weave joins two sets of warps yarns at the edges. When woven on a shuttle loom, the fabric created is completely seamless, resulting in a fabric with a uniform water porosity and air permeability property. Often designed into filtration and other medical device applications, tubular webbings are also utilized for their hoop strength in inflatable vessel constructions.
- Stuffer yarn constructions are those with a tubular weave to which a stuffer yarn and a binder yarn is added to multilayer woven fabrics to add strength. One example is industrial belting applications that use woven thermoplastic fibers around aramid stuffer yarns used for its high tensile properties. The method is also used in parachute harness webbing to improve webbing strength and stiffness. The binder yarns act as woven sewing type stitches that help to stabilize the weave and lock in the jacket fibers with the stuffer yarns.
Many variables affect the success of a specific webbing. Questions to consider during the design process include:
• What performance properties will be required in the final weave design?
• What is the stiffness requirement? How should it feel when held?
• What type of hardware will be required?
• What termination method will be used?
• Does the end-use application require specific consideration?
• For composite applications, what are the specific properties of different fibers required?
Fiber Size and Strength
Weaving yarns are composed of bundles of individual filaments of a specified number. When these filaments have long continuous lengths, it gives the yarn optimum strength and tensile resistance.
All types of manmade fibers are specified for size. Comparisons are made among fibers by referring to their denier, which equals the mass in grams of 9000 meters of weaving yarn. For example, a 220 denier nylon is composed of a smaller bundle of continuous filament fibers and has less mass than a 440 denier nylon, so it is less strong. The strength to mass ratio is in direct proportion; for example, 440 denier nylon 6.6 has two-times the strength as 220 denier nylon 6.6 from the same batch of fiber.
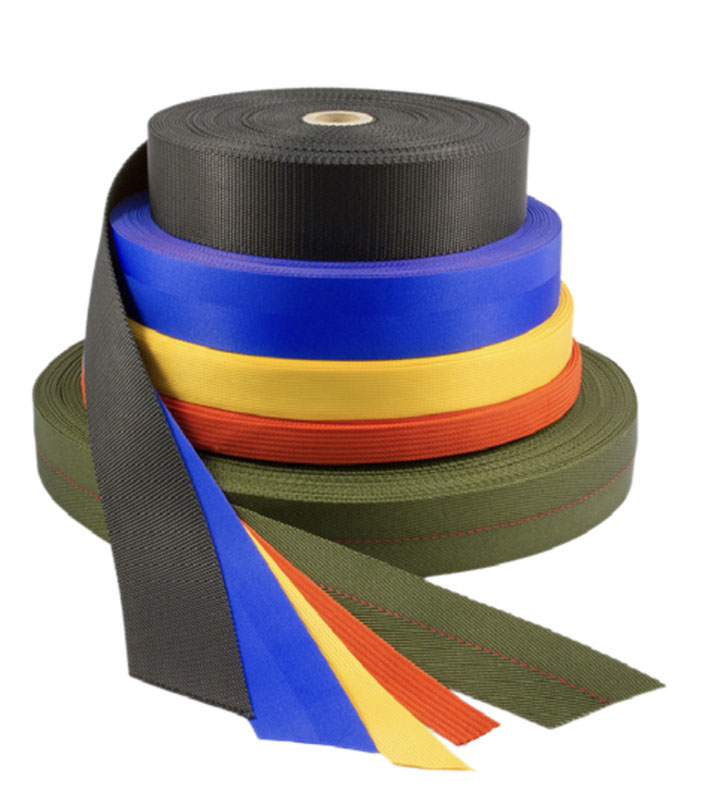
Fiber producers publish tenacity values that can be valuable for comparison purposes, but actual tensile strength yields of woven fabrics will be less than these published numbers. This is due to a concept known as translational strength, defined as a comparison of the properties of a fabric to that of the input base fiber. Due to many weaving process variables, translational tensile strength yields are typically 20-40 percent less than published fiber tensile strengths. It is critical to understand the many trade-offs needed to achieve performance characteristics and the relationship between variables and performance.
Fiber Selection
Fiber selection is an important aspect of woven fabric design. Available options include natural fibers, standard man-made fibers, and high-performance advanced fibers.
Natural Fibers
Cotton is the most typical natural fiber used in webbings, especially for packing material for mechanical bearings and flame wick applications. Preferred for next-to-skin contact, cotton is not used for most industrial applications.
It is difficult to produce structural cotton webbings using U.S. cottons that meet United States Military Standard (MIL-SPEC) specifications for thickness, strength, and weight. However, the Berry Amendment requires that fibers be grown in the U.S. for U.S. DOD contracts. This can present challenges when using cotton webbing for technical applications and may require that end users consider nylon or polyester webbing as an alternative.
Man-Made Fibers
Man-made fibers include such standard options as nylon, polyester, polypropylene, and rayon. Nylon is used on many webbing applications because of its toughness, strength, durability, and dyeability. Nylon will elongate under load, which absorbs energy, making it a good choice for parachutes and PPE/fall protection applications. Nylon is also hygroscopic, meaning it absorbs moisture. While all fabrics will wick moisture, the nylon fiber itself will gain moisture content.
Polyester is another common standard manmade fiber used in webbing construction. With a strength similar to nylon, polyester has a lower elongation property, making it a good option for automotive and aircraft seatbelts. Polyester is hydrophobic, so it has minimal moisture regain and can be used for applications at or around fresh and salt water. Polyester is dyeable but must be dyed at a higher temperature and pressure than nylon.
High Performance/Advanced Fibers
Polymer chemistries advancements have given high-tech fibers desirable inherent properties, for example, greater strength to weight ratios, high temperature resistance, chemical resistance, and minimized elongation properties. Key examples include aramids, UHMWPE (ultra-high molecular weight polyethylene), PPS (polyphenylene sulfide), and PBO (polybenzoxazole).
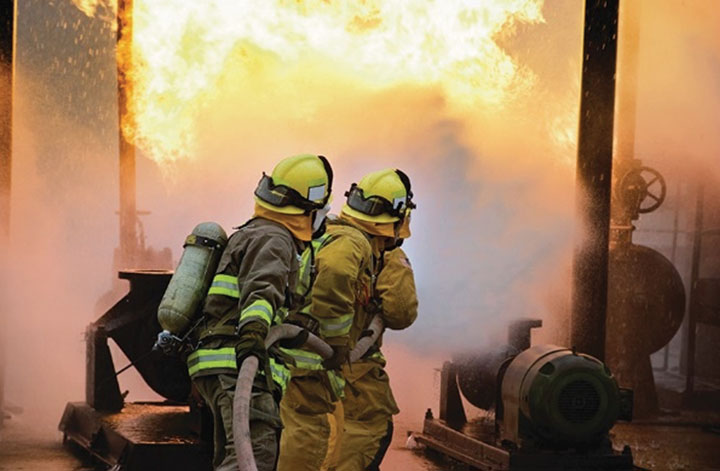
Webbing Used in Critical Applications Requiring Superior Properties
BRM designs, engineers, and manufactures woven materials that serve as structure or substrate for components in critical customer applications that require superior properties, including:
- Strength: specific, interlaminar shear, enduring
- Resistance: impact, abrasion, chemical, environmental
- Light weight, reclaimable
- Conducting, sensing
- Shapes: 2D, 3D
For example, polytetrafluoroethylene (PTFE) fiber chemistry makes fibers resistant to specific chemical exposure and gives them a natural lubricity. BRM uses this type of fiber on the webbing surface to impart a wear-surface.
One successful application is as a wear surface for structural components of highway bridges. The other fibers used in this proprietary construction are high strength aramid, which gives the fabric the strength needed to survive the tensile and compression forces on concrete and steel bridge structures from high-weight vehicle travel and thermal expansion and contraction.
Another example is PPS, used in industrial filtration and air cleaning, where high concentrations of sulfuric acid must be removed from effluent air from power plants and other industrial processes.
A final example is a woven composite belting/narrow fabric being utilized in a proprietary application as a drive/control belt in a machinery process. The customer pursued the use of DuPont™ Kevlar® aramid, whose high strength and low elongation seemed ideal. However, Kevlar tends to degrade from bending fatigue. To counteract this negative property, BRM added polypropylene fibers to the outer jacket of the woven material to provide some protection. The final item is heated to approximately 300 degrees F, at which point the polypropylene melts around and through the Kevlar fibers, completely encapsulating the aramid fiber and providing a wear surface and protection from flexural fatigue.
Understanding the Art and Science of Weaving
Weaving is both an art and a science. Many variables affect the success of a specific webbing, irrespective of predictions based on bench top design. With its years of experience, BRM understands how to control many of these variables, but such knowledge does not necessarily always improve strength yields. That is why BRM always runs rigorous trials at the loom to test properties and understand the trade-offs that must be made to ensure fabric performance. Using a careful iterative process to create innovative new fabric prototypes, BRM designs solutions with fabrics that meet a wide range of property requirements for highly engineered applications. After all, we have material on the planet Mars!