This is a great time to be in nonwovens and will continue to be so, as demand and, correspondingly, localized supply, to meet that demand, continues to increase. The nonwovens industry has responded to the pandemic and will continue to provide materials that keep the surfaces we touch clean, protect the air we breathe, and provide a barrier to keep our bodies safe.
Annually, INDA produces the North American Nonwovens Supply report based on extensive research, producer surveys and interviews with industry leaders, the report provides an overall view of North American supply, including the key metrics of capacity, production, and operating rates, in addition to regional trade, through the year 2021.
Based on that data, North American capacity continues to increase with the investments being made across all the processes and for a variety of end-uses. Production output exceeded that of new capacity, resulting in the industry’s nameplate capacity utilization increasing year-over-year, for the fourth consecutive year.
Production by raw material usage
In 2021, the production of nonwovens in North America reached 4.790 million tonnes, 2.7% growth over the previous year. In 2021, the production growth outpaced that of capacity growth, resulting in the overall operating rate edging up to 87%. The figure below (Figure 1) displays the share of resin and staple fiber used in the North American nonwovens production, whether in the form of resins or fibers. Staple fiber represented 70% of the material usage in 2021. This is not surprising given that staple fiber represents 70% of the installed base of drylaid (carded), wetlaid, and airlaid short-fiber capacity.
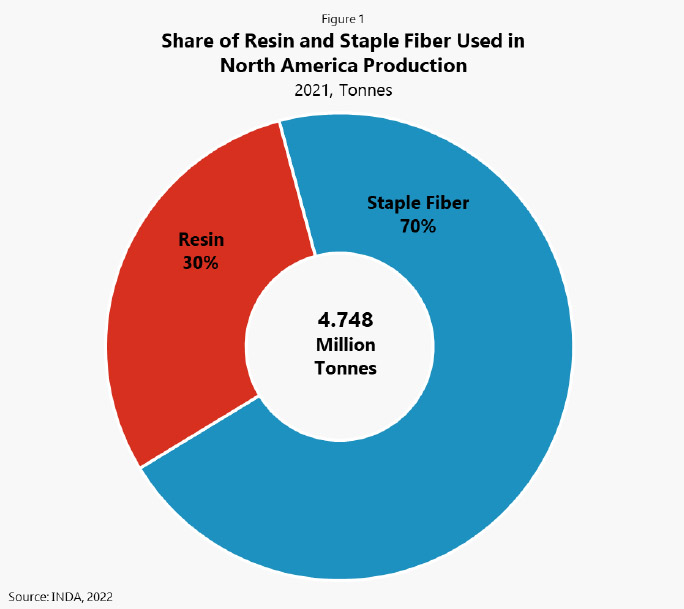
The shares remained constant from 2020 to 2021. However, the share of the use of resin increased from 27% in 2019 to 30% in 2020, as the spunlaid production increased 8.4%. The production of the three web-forming processes using staple fiber declined 2.0% year-over-year.
The raw materials used in the nonwoven production process can also be classified synthetic-based or natural. In 2021, the synthetic share was two-thirds (69%) of the overall raw materials used in production. The next figure (Figure 2) displays the share of synthetic polymers used in the nonwovens industry, whether in the form of resins or fibers. Polyester is the most common synthetic polymer (45%), followed by polypropylene (35%). Polyester (PET) tends to be more used in the durable categories, and polypropylene (PP) in the disposable categories. With the rebound in material production for some of the durable end-use categories, PET increased two-percentage- points, while PP and Nylon/Rayon/Other both declined one percentage point.

Spunlaid resins
Resin consumption in the North American spunlaid processes was 1.402 million tonnes in 2021 (Figure 3). Polypropylene (PP) resin is the most widely used resin in spunlaid applications, accounting for two-thirds (66%) of the North American spunlaid market in 2021. Polypropylene has several advantages over other resins, and those advantages continue to drive its growth in new markets and maintain its dominant share position against other resins. Polypropylene has a specific gravity of less than one, lower than competing polymers; therefore, producers attain a higher yield per tonne using PP rather than competing resins. The PP melt-spinning process tends to have a wider process operating window than other polymers, resulting in easier processing. In addition, polypropylene has pleasant aesthetics of softness and pliability, and thus is used widely as coverstock in diapers, feminine hygiene, and disposable apparel. Polypropylene is also the predominate resin in the meltblown process.

The next most widely used resins are the polyester resins (PET ‒ polyethylene terephthalate and PBT ‒ polybutylene terephthalate) at 15%, a decline of one-percentage point from 2020 (Figure 3). Polyester is primarily used in spunbond materials, but a small volume of this resin is consumed in meltblown production. Durables are the principal end markets for spunbond polyester, with the exception of fine denier spunbond polyester for fabric softener sheets. Polyesters are also used in applications requiring higher temperature resistance, since polyester resins have a melt temperature in the 230 to 260-degree Celsius range.
Staple fiber
The North American consumption of staple fibers by the drylaid, wetlaid, and airlaid short-fiber nonwovens production was 3.331 million tonnes in 2021. The synthetic fibers (in shades of orange) accounted for slightly more than half (56%) of the staple fiber used (Figure 4). This was the same share as the previous two-years.
Polyester staple fiber accounted for 37% of fiber utilized by nonwoven producers in 2021 (Figure 4). In North America, the recycled share of polyester staple fiber consumption was 27% in 2021, up from 24% in 2019. While a large portion of the virgin polyester staple fiber can be attributed to the production of hydroentangled materials destined for the wipes industry, the transportation end use (e.g., carpeting, trunk liners, wheelhouse liners, underbody systems) consumes large volumes of fiber for heavier weight needlepunch products made of recycled polyester fibers.

Polypropylene staple fibers accounted for 7% of the staple fibers used in 2021 (Figure 4). While PP staple fiber usage has declined in the disposable market, in particular drylaid thermal bonded coverstock materials (only partly compensated by utilization of airlaid), this fiber continues to grow in supplying the durable nonwovens market. Most of the large durable end markets for PP staple fibers are needlepunch durables. The major markets that consume needlepunch PP include geosynthetics, vehicle components, and home/office furnishings (primarily indoor/outdoor carpeting, blankets, upholstered furnishings, and bedding).
Viscose (rayon) staple fiber, including those of the lyocell process, accounted for 5%, mainly driven by the wipes and medical products industries.
Mineral fibers – including carbon, ceramic, carbon, glass, and metal fibers – extensively used in North America, primarily in the wetlaid process, accounted – in weight – for 19% of the staple fiber consumption in 2021. Glass fiber is made from extremely fine fibers of glass. It is a lightweight, extremely strong, and robust material. Glass fibers have applications in filtration, transportation, construction, electronics, wind energy, and other industrial uses. A small amount of mineral fibers are also used in airlaid short-fiber and drylaid needlepunch processes.
Wood pulp, primarily that of southern bleached softwood kraft (SBSK) fluff pulp – consumed by airlaid short-fiber, drylaid hydroentangle, spunbond, spunlaid coform, and wetlaid processes – accounted for 18% of the staple fiber production in 2021, a decline of one-percentage point. Surprisingly, wood pulp is used in all the web-forming processes; approximately 51% of wood pulp is used in the wetlaid process (primarily for wipes and filter media), 26% in airlaid short fiber, 16% in spunlaid (primarily Kimberly-Clark’s coform and Berry Global’s Spinlace® products) and 7% in drylaid hydroentangle.
Both cotton and natural fibers (such as jute, flax or hemp), together accounted for 7% of the staple fibers consumed in 2021 nonwovens production, an increase in one-percentage point. Cotton is also used in many other domestic and personal care products, such as medical sponges, pharmaceutical coil, disposable wipes, tampons, cosmetic pads, beauty coils, jeweler padding and several other miscellaneous products. Although produced from a garnet or carding system, these uses are not counted as nonwovens production.
The next most widely used resins are the polyester resins (PET – polyethylene terephthalate and PBT – polybutylene terephthalate) at 15%, a decline of one-percentage point from 2020. Polyester is primarily used in spunbond materials, but a small volume of this resin is consumed in meltblown production.
Looking forward
While the North American economic and population forecasts are the basic building blocks of the North American nonwovens demand, like all aspects of life, the coronavirus pandemic has significantly impacted the nonwovens markets, in the short-term and, most likely, forever.
The industry has responded by investing in new assets to ensure the steady flow of these needed materials. Across the two-year period, 2020 and 2021, the nonwovens industry has publicly announced investments of $203 million. For this year and next for the industry has announced capacity investments of $686 million starting up in North America. These investments will increase the fiber demand in North America.
Once again, it is a great time to be in nonwovens and will continue to be so through the next few years as demand and, correspondingly, supply to meet that demand continue to increase, and nonwovens continue to protect and improve our lives.
The North American Nonwovens Supply report is one of three INDA member-publications produced by INDA’s Market Intelligence and Economic Insights Group. For additional information on these publications and other INDA member benefits, please visit www.inda.org/indamembers/index.html or contact Morris Collins, INDA’s Director of Member Relations at mcollins@inda.org.
International Fiber Journal is owned by INDA, Association of the Nonwoven Fabrics Industry (inda.org).