Passenger compartment becoming a key decision factor in car purchasing
Electric vehicles (EVs) are propelling the automotive industry toward a more sustainable future, while autonomous driving will alter just about everything regarding vehicles – mega-changes that will amount to the biggest leap forward since cars replaced horses.
Almost all the attention concerning autonomous vehicles is currently focused on the self-driving aspects, particularly safety. However, the functions and features of the vehicle interior will also need to work autonomously for improved occupant comfort and convenience.
The new exterior
For many decades, the exterior design was the decisive emotional factor in the cur purchase. But with changing behavior in public and private transportation and the growing autonomy of vehicles hugely impacting the driving experience, interior features are fast becoming become the main differentiating element influencing buying decisions, according to a 2019 survey conducted by Asahi Kasei Europe.
This will also drive developments toward premium, hygienic and sound-absorbing surfaces, as well as a greater desire for sustainable materials – 57% of survey respondents said sustainable materials for seat covers and interior surfaces will become increasingly important over the next 5-10 years, while the need for real leather materials will fall drastically.
Alexander Schieke, global market manager mobility at Netherlands-based Stahl, a supplier of chemistry for coatings, processing and treatments of various materials, believes that all the main substrates – leather, synthetics and fabrics – will have a role to play in the automotive interior of the future – despite the growing trend to veganism, which is starting to impact the leather sector, particularly in the premium segment.
Sustainable alternatives
Emerging interior trends regarding lifecycle and sustainability include climate change, limited fossil-based resources such as oil, concerns about waste plastic in the environment and a reduction in the use of plastic.
This will lead to alternatives to petroleum-based chemical products, such as plant-based feedstocks, and the use of recycled plastics and other materials.
In the luxury segment, Jaguar Land Rover (JLR) is working with Econyl polyamide (PA) to develop automotive interiors made from ocean and landfill waste.
Next-generation Jaguar and Land Rover models will feature floor mats and trims made with Econyl fiber from recycled industrial plastic, fabric offcuts from clothing manufacturers, nets from the fish farming industry and fishing nets abandoned in the ocean (so-called “ghost nets”).
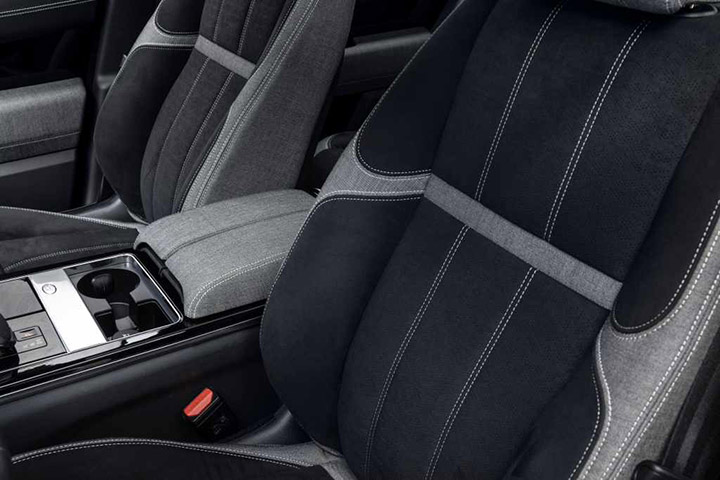
Econyl regenerated PA, created by Italy-based synthetic fiber maker Aquafil, has already been used by high-end fashion, sportswear and luxury watch brands to create handbags, backpacks, swimwear and watch straps.
In a single year, the company can recycle up to 40,000 tonnes of waste sourced globally, with the recycling process reducing the global warming impact of PA by 90% compared with the material produced from oil.
And for every 10,000 tonnes of Econyl raw material produced, 70,000 barrels of crude oil are saved and 65,100 tonnes of carbon dioxide (CO2) equivalent are avoided, it is claimed.
In state-of-the-art treatment centers the waste is analyzed, treated and prepared, and fed into a chemical plant, where the PA waste is broken down using a depolymerization process to its original raw material, which is then used to make Econyl yarn.
Throughout the process, other by-products such as non-PA, metallic materials and copper sulfate, which is used for preventing seagrass growing on fishing nets, are removed and sent to alternative industries for recycling.
The resulting Econyl regenerated PA polymer is said to have the same chemical and performance characteristics as raw fossil material, allowing it to be processed into a fiber for carpet flooring and textiles.
This yarn will be used to manufacture floor mats for future JLR models. Land Rover offers a premium Eucalyptus textile interior on the Range Rover Evoque, while the Evoque, Range Rover and Jaguar’s all-electric I-PACE offer the Kvadrat option, which combines wool with a suede fabric made from recycled plastic bottles.
Mechanical recycling
Most post-consumer textiles are either sent to landfill, burned or processed to make low-quality nonwovens. The main problem with textile recycling is the different components of the textile, which are mostly made from fiber blends.
Previous approaches to recycling have usually followed chemical processing routes, which are not entirely sustainable. However, engineering service provider Imat-uve is now working with a German-Dutch project consortium on the mechanical recycling of used clothing made from mixed fibers, with the recycled yarns and woven fabrics primarily intended for use in the automotive industry.
By optimizing the mechanical recycling process, the blended fibers can be finely torn and processed into a particularly soft, uniform card sliver by new spinning preparation technologies. The resulting yarns (Nm 15 and Nm 28) can be further processed for different requirements, depending on the polyester content.
The raw material for yarn production consisted of sorted used workwear (60% polyester/40% cotton) and old clothing (made of unknown fiber blends), as well as raw polyester.
From the resulting recycled yarns, Imat-uve created various fabric samples, with the weaving process showing an excellent result: even yarn made of 100% mixed fibers could be woven commercially without complications, with no thread breaks and hardly any fiber abrasion during weaving.
In trials with several yarns and fabrics, standard tests for the automotive industry, where high demands are placed on the durability and comfort of the textiles, were passed, such as the Martindale test for resilience and abrasion behavior, modified Martindale tests for internal and external pilling, and hot-light ageing.
Tufted carpet
Autoneum, a supplier of acoustic and thermal solutions for the automotive industry, has launched a tufted carpet with the yarns manufactured from recycled polyethylene terephthalate (PET) bottles.
Compared with standard carpets, Relive-1 carpets are more robust owing to significantly higher abrasion resistance and are easy to clean due to the vertical alignment of the filaments and the water repellency of polyester, said the Switzerland-based company.
As a result, small particles such as wood splinters, dust or pebbles, as well as liquids, can be removed easily with no residual traces – a key benefit for recreational vehicles such as sport utility vehicles.
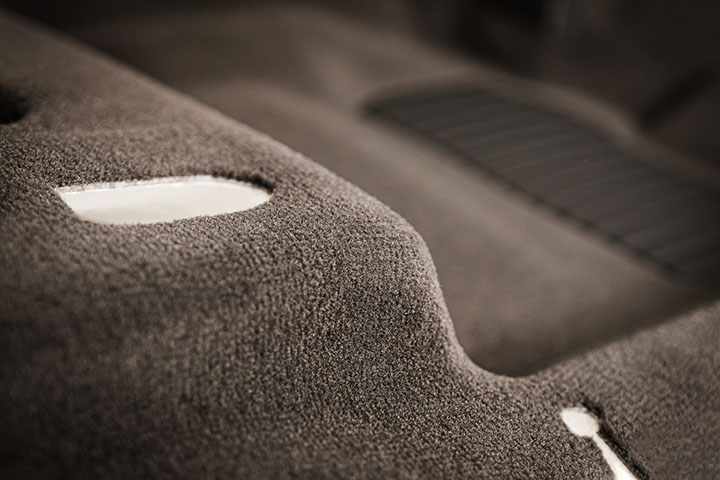
Autoneum has also developed a “frunk” (front trunk) made of Ultra-Silent, its lightweight, noise-reducing and sustainable technology initially designed for EV underbodies.
The multifunctional component offers more storage space and is said to be particularly light owing to its textile fiber composition, replacing the heavier plastic solutions consisting of several individual components that are common in current EVs. The frunk is made entirely of PET and contains up to 70% recycled material.
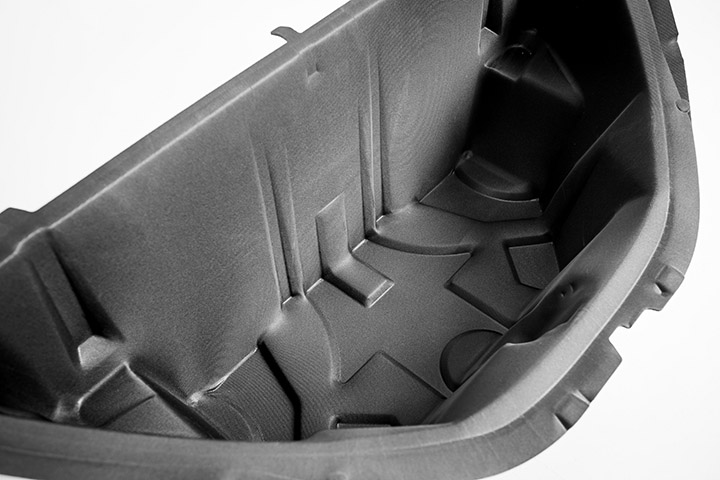
Recyclable microfibers
Sustainable and recyclable microfiber suedes, such as Dinamica, produced by Miko of Italy, a subsidiary of U.S.-based Sage Automotive Interiors, have been supporting automotive original equipment manufacturers to achieve their environmental goals.
The recycled polyester contained in the microfiber derives from polyester fibers, such as T-shirts and other clothing, and PET bottles and packaging materials.
Dinamica is mostly used to cover automotive seats and headrests, headliners, door panels and steering wheels, with recent introduction in the Mercedes-Benz AVTR concept car, the Volkswagen ID.3 and the new Audi Q2.
Recycling automotive textiles
Currently, more than 25 kg of textiles are used in the average new vehicle. With the onset of EVs, this will increase to 35 kg and possibly more, which represents both a future waste product and a potential source of raw material in the processing of end-of-life vehicles.
Most automotive textiles are made from synthetic fibers, often a combination of several textile materials or with other non-textile materials to create composite fabrics, which makes recycling using conventional technologies virtually impossible.
PR Krajné, based in Slovakia, has developed the patented Stered technology to reprocess composite automotive textile waste into an insulation product that can be used on conventional, purpose-built areas, such as roofs of homes, office buildings, and production and storage facilities.
These surfaces are converted into so-called “climatic, energy-active areas” that are characterized by their repeated ability to retain rainwater and allow it to evaporate. The surfaces become “energy-active” – i.e., the energy from the environment is consumed to evaporate the water, thereby cooling the buildings.
Another novel use of end-of-life automotive textiles is a limited-edition sports shoe made with repurposed airbags by sportswear brand Reebok together with South Korean label Kanghyuk. The Reebok x Kanghyuk Zig Kinetica collection was produced in an exclusive run of just 50 pairs that were sold in London, UK.
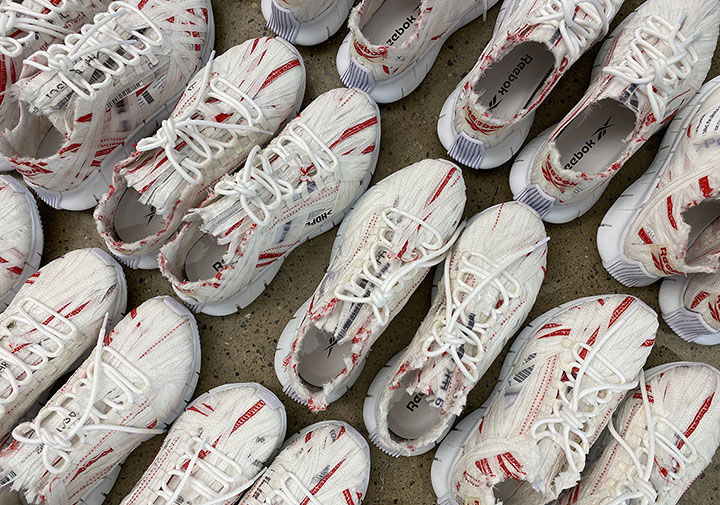
Natural fibers
Automakers have been using natural fibers for various components for decades, including the incorporation of hemp, sisal and wood into materials for insulation, interior paneling and internal engine covers for luxury vehicles.
Other plant-derived natural fibers, such as kenaf, flax and jute, are also increasingly being used as automotive components, according to Dr. George Kellie, director of UK-based Kellie Solutions.
For example, thermoplastic and thermoset natural fiber composites are now used for door panels, seatbacks, headliners, package trays, dashboards and trunk liners.
Comingled polypropylene-based composites that include plant-based fibers are also emerging, using such technologies as compression molding, thermoforming, and extruded sheets and mats, as part of nonwoven composite structures, he said.
Composite materials
The interior of the Precept concept vehicle, which is being put into series production in China by Polestar (a battery EV brand founded by Volvo and Geely), will see a mix of sustainable materials, including recycled PET bottles, PA 6 from reclaimed fishing nets and cork from the wine industry.
It will also feature composite materials from Swiss supplier Bcomp, which specializes in natural fiber-based materials.
For interior applications, Bcomp’s production process enables the use of a visual surface layer to be applied to its materials, such as leather, Alcantara or textiles, with the composite structure below consisting of flax fibers, and, where necessary, reinforcing ribs to improve stiffness.
The flax-based composite is featured in Precept’s interior doors, floorboards, dashboard and seatbacks, as well as some exterior components.

UK-based McLaren has developed a natural fiber racing seat considered to be the first Formula One car part to be made of renewable textile fibers.
Developed in conjunction with Bcomp, the novel racing seat is said to optimize the mechanical properties of flax fibers through fabric architecture, developing a seat with the required strength and stiffness, but with a 75% lower CO2 footprint compared with its carbon fiber counterpart.
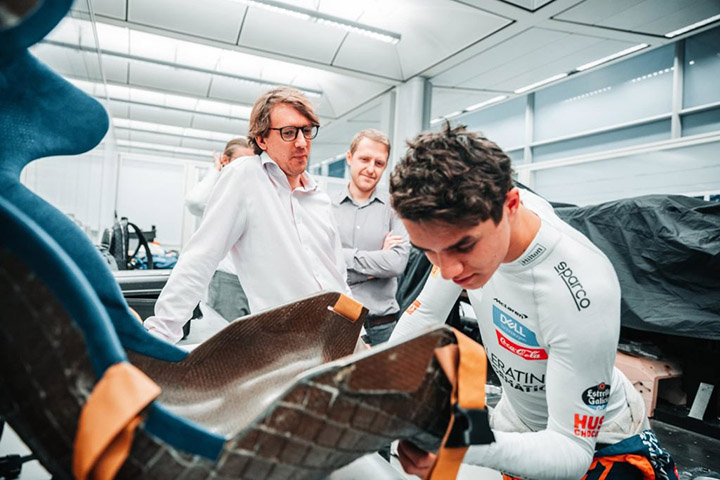
Delivery vehicles
Bcomp’s flax fiber composite is also being used for EVs designed for inner-city freight deliveries by Swedish start-up Volta Trucks.
The 16-tonne Volta Zero features body panels made with flax fibers and a biodegradable, bio-based resin – claimed to be a world first in a composite body panel construction.
Body panels for the EV are being made using Bcomp’s ampliTex flax-based technical fabrics reinforced with powerRibs, which comprise flax fiber woven in a grid structure.
The use of flax-based fabrics in body panels is said to enable significant weight savings as well as up to 75% lower CO2 emissions compared with carbon fiber reinforced plastics.
Volta Trucks also uses a novel bio-based and biodegradable resin derived from rapeseed oil to further reduce the carbon footprint of the vehicle.
At the end of life, parts made from flax fibers can become a CO2-neutral energy source when incinerated via a standard waste management system for heat recovery, without residual waste, which compares with traditional composite materials that often end up in landfill.
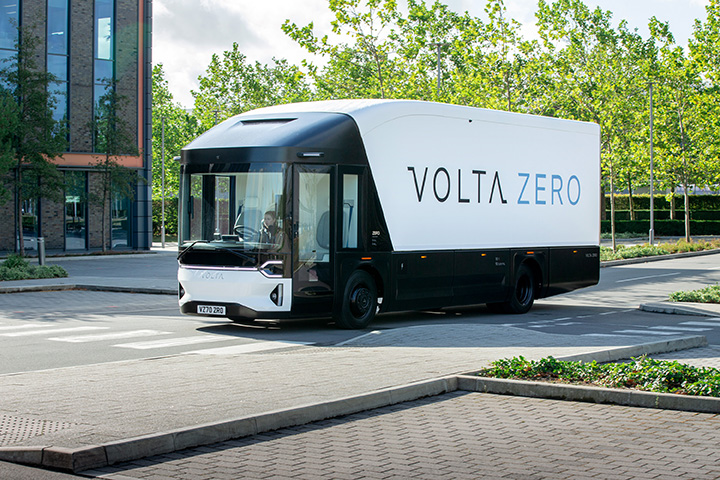
Global research
Natural fiber composites are renewable, low cost and low density, and they have high specific strength and stiffness, while the manufacturing processes are relatively safe. Their use in automotive applications continues to be the subject of intense research worldwide.
For example, researchers from the University of Johannesburg have demonstrated that plantain, a starchy type of banana, is a promising source for automotive composite materials.
Treated plantain fibers can be combined with carbon nanotubes and epoxy resin to form a natural fiber reinforced polymer hybrid nanocomposite material that is much stronger and stiffer than epoxy resin on its own.
Meanwhile, a consortium of Egyptian researchers has developed high-performance long fibers and reinforcements extracted from the by-products of the pruning of date palms, such as frond and fruit stalks.
The sustainable PalmFil fiber is 100% biodegradable and compostable and is claimed to have specific tensile strength five times higher than that of structural steel and equal to that of flax, hemp and sisal.
Further, its vibration damping and acoustic insulation is higher than that of glass and carbon, it has a thermal insulation higher than that of carbon, and it can be easily blended with other long fibers, such as flax, sisal and abaca, or chopped and blended with hemp, kenaf and jute.
Potential applications in the automotive sector include door panels, parcel shelves, engine encapsulation, rear trunk covers, seatbacks and acoustic insulation.
Aircraft fabric
UK-based textile manufacturer John Horsfall has developed a sustainable fabric to replace traditional polypropylene (PP) nonwovens used in aircraft cabins, as well as in coaches and trains.
Ideal for headrests, pillow covers, tray mats and other single-use items, BioFibre is 100% regenerated cellulosic fiber made from reclaimed waste wood using a clean, chemical-free hydroentanglement process.
Compared with a PP headrest, which can take more than 50 years to break down to micro-plastic particles in landfill, BioFibre takes less than 12 months to fully biodegrade, without the need for any special processing.
