Faced with unprecedented levels of disruption and innovation, technological advances are impacting all segments of the vehicle industry, particularly interiors.
Despite ongoing setbacks due to the impact of the coronavirus pandemic, a shortage of semiconductors and higher raw material, energy and transport costs, automakers have continued to develop their visions of the future – and automotive interiors are beginning to take center stage.
According to German car maker Audi, new technologies are changing people and the way they move, via the transition to e-mobility, the potential for autonomous driving, all-encompassing digitization, and with it the networking of car and world.
Inside the vehicle, language and gesture control, as well as touch-sensitive surfaces, will replace traditional switch panels and rotary wheels. There will be more free space where passengers can relax during car journeys, particularly when they are no longer needed as drivers.
The vehicle interior of the future will set new standards for the integration of technology, spaciousness and feel-good ambience, says Audi. As a result, the interior will set the pace for vehicle design overall.
Chip crisis
In 2021, nearly 10 million vehicles less than initially forecast were produced worldwide, owing to the semiconductor chip crisis, which affected global supply chains and caused global vehicle production to fall by 19% in the third quarter.
As a result, the total recovery in the automotive sector, in the wake of the crisis in 2020 caused by the onset of COVID-19, now looks like it’s taking longer than expected.
But when the industry situation returns to “normal” in the coming months, the high global demand for vehicles should produce sustained growth in sales over the medium term, according to many industry analysts.
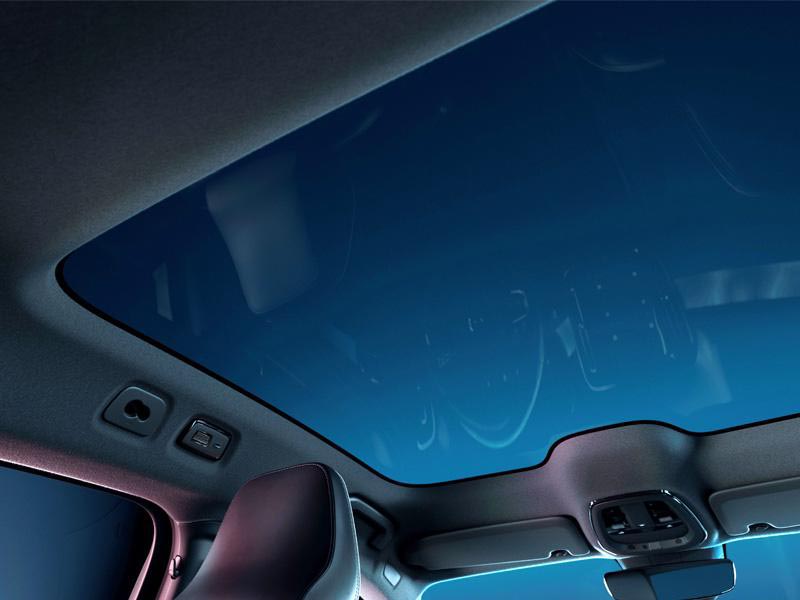
Electrification and digitization
Wemzer Industries managing director Amin Uz Zaman has identified additive manufacturing, re-manufacturing, e-commerce, hybrid/electric drive trains and mobility as a service as the new drivers for the automotive sector.
The automotive aftermarket in particular is undergoing major disruption, he said during the recent Automechanika Dubai trade show. “With electrification and digitization driving change, we are reshaping the way customers, automotive suppliers and industry stakeholders think of cars and driving and how business in the automotive aftermarket is conducted and value is created.
“The massive penetration of internet connections and smartphones has driven the customer’s expectation for a seamless, comfortable and, most importantly, a transparent shopping experience,” said Uz Zaman.
“The automotive industry was probably delayed in embracing this transformation, but the pandemic accelerated the process and now we are witnessing a massive digitization of the industry.”
‘Greener’ headliners
While the pandemic has thrown the global automotive industry off balance, vehicle and parts manufacturers are becoming increasingly aware about the need to contribute to a “greener” future.
For example, Tier 1 automotive supplier Grupo Antolin has developed what it claims to be the first car headliner substrate produced by thermoforming a polyurethane foam with materials made from urban and post-consumer plastic waste, as well as end-of-life tires.
The new headliner is said to look and perform exactly the same as the company’s established headliners and has been made possible by a chemical recycling process developed by BASF, which Antolin has introduced in a recently launched, fully electric European premium car.
Approximately 50% of the headliner weight is recycled and 100% of the textiles, 70% of the core foam and 70% of the plastic sunroof reinforcement frame were obtained from waste that could not be recycled in any other way, the Spain-based company reports.
Foam alternative
Autoneum, a supplier of acoustic and thermal management solutions for the automotive industry, has introduced a new felt-based technology that, owing to a blend of recycled cotton and functional fibers, reduces product weight and allows for accurate adaptation – even to complex shapes.
The Switzerland-headquartered company says its Flexi-Loft technology provides a versatile and more sustainable alternative to foam for interior components, such as inner dashes or carpets, as it is significantly lighter, more flexible and more adaptable than standard felts.
Flexi-Loft consists of at least 50% recycled cotton fibers, and off-cuts generated during the manufacturing process are reclaimed, processed and then reused in the production of new felt blanks. Further, the material is fully recyclable.
Autoneum is already using Flexi-Loft as an insulator for various carpets, inner dashes and other acoustic components based on its Prime-Light technology, while the application of the material as a decoupler in inner dashes made of Hybrid-Acoustics will be launched on the European market in 2023.
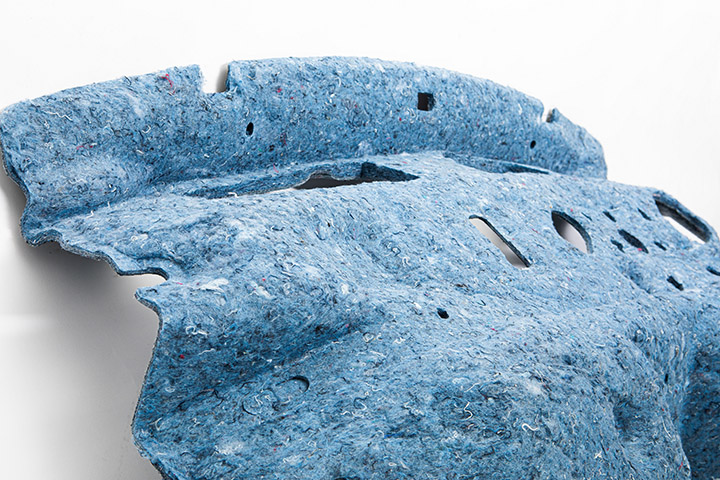
Leather-free interiors
By 2025, Volvo is aiming for 25% of the material in its new cars to consist of recycled and bio-based content, as it looks to become a fully circular business by 2040. The company says it is actively working to find high-quality and sustainable sources for many materials currently used in the automotive industry.
As part of this transition, the Swedish vehicle maker has announced that all its new, fully electric models will feature entirely leather-free interiors, starting with the new C40 Recharge.
The interior design of the Concept Recharge utilizes a range of sustainable materials, both natural and recycled, such as responsibly sourced Swedish wool, environmentally friendly textiles and lightweight composites created from natural sources.
Wool is used in the seat backrest and instrument panel top, while the floor and lower doors are also covered by a rich carpet of 100% wool. The seat cushions and touch surfaces on the door are made from a material that contains Tencel lyocell fibers.
The seatbacks and headrests, as well as part of the steering wheel, use a new material created by Volvo called Nordico. This is a soft material made from recycled material such as polyethylene terephthalate (PET) bottles, bio-attributed material from sustainable forests in Sweden and Finland, and corks recycled from the wine industry.
Elsewhere in the interior, including in the lower storage areas, back of the headrest and the footrest, the Concept Recharge uses a flax composite developed by Volvo in collaboration with suppliers. This is based on fibers from the linseed plant, which are used in composites to provide a strong and lightweight, yet attractive and natural, aesthetic material.
Volvo will, meanwhile, continue to offer wool-blend options from suppliers that are certified to source responsibly, as the company looks to ensure full traceability and animal welfare in its wool supply chain.
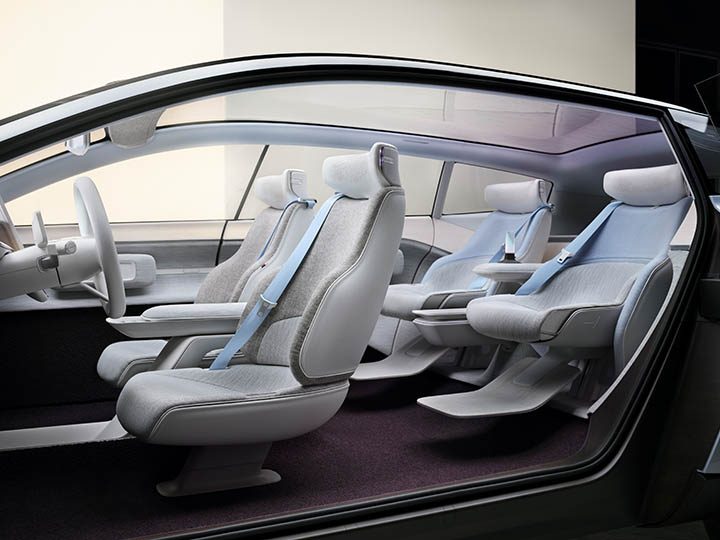
Sustainable processes
Škoda Auto has developed a sustainable raw material with the Technical University of Liberec that could be used in the interior of future Škoda vehicles. Produced using sugar beet pulp, the material can be used for door trim or decorative dashboard inlays and is dyed using a process to produce design accents.
The Czech automaker is also researching other sustainable and ecological materials such as one based on miscanthus in which the fibers from the reed plant can be processed and turned into a material suitable for application to interior panels.
Škoda says the organic residues from production make excellent ecological raw materials as these can be processed further without the need for additional resources.
Door panels and pillars in the Škoda Octavia have been finished with miscanthus-based fabric, and sugar beet shavings have been utilized for the door panels and dashboard.
The automaker has also applied sustainable processes to other interiors across its vehicle portfolio. For example, 30% of the seat covers in the design selection for the Škoda Enyaq iV are made using 100% new wool, certified in accordance with the Woolmark Company, while the other 70% is made using polyester from recycled PET bottles.
Surface trends
Although the future of mobility – a hot topic even well before the pandemic – remains a constantly evolving vision, most in the automotive industry agree that autonomous driving represents the long-term future, which in turn is driving interior surface trends.
At November’s Automotive Interiors Expo in Stuttgart, Germany, automotive supplier Continental showed a converted VW T2 Bulli named AMBIENC3 to highlight smooth, uncluttered surfaces in bright natural colors, including seats, couch, tables, floors, doors and headliner, that together provide an interior space that combines the areas of driving, working and relaxing.
The concept vehicle is made primarily from sustainable, natural and renewable raw materials. Lightweight surfaces use recycled materials or materials from upcycling, as well as low-emission and low-pollution materials.

space concept of Continental
combines the areas of driving,
working and relaxing. Photo courtesy of Continental
Third living space
Asahi Kasei showed its prototype vehicle interior of the future – AKXY POD – for the first time outside of Japan at January’s CES 2022 technology industry trade show in Las Vegas, Nevada, USA.
The Japanese chemicals and materials producer believes the automotive interiors of tomorrow will be molded by a wide range of technologies. For example, textiles and engineering plastics can significantly dampen sounds while reducing the vehicle’s overall weight to create a cabin atmosphere with optimized comfort. In addition, automotive interiors will need to be safe and clean.
Between luxury and nature
Also, on show at CES was Mercedes-Benz latest concept for electric mobility, the Vision EQXX. With a range of more than 1,000 km on a single battery charge, the concept vehicle’s minimalistic yet high-tech interior features a large number of sustainable, lightweight materials sourced without using animal products, from mushrooms to bamboo, cactus and vegan silk.
The door pulls, for example, are made from AMsilk’s Biosteel fiber, a high-strength, certified-vegan, silk-like material that is said to be 100% biodegradable, recyclable, renewable and zero-waste.
A sustainable material used in the seating is Mylo, a vegan leather alternative made from mycelium (the underground rootlike structure of mushrooms), while the floor carpets are made from 100% bamboo fiber.
Another animal-free leather alternative used in the Vision EQXX seats is a sustainable cactus-based biomaterial called Deserttex, which is made from pulverized cactus fibers combined with a sustainable bio-based polyurethane matrix.
Elsewhere, the Vision EQXX makes extensive use of recycled waste materials, such as PET bottles that are used in a textile to enhance the floor area and door trim.
The interior also features UBQ material, a sustainable plastic substitute made from household and municipal landfill waste, while the doors of the concept car are made from a hybrid of carbon fiber and glass fiber-reinforced plastic components with aluminum reinforcements.
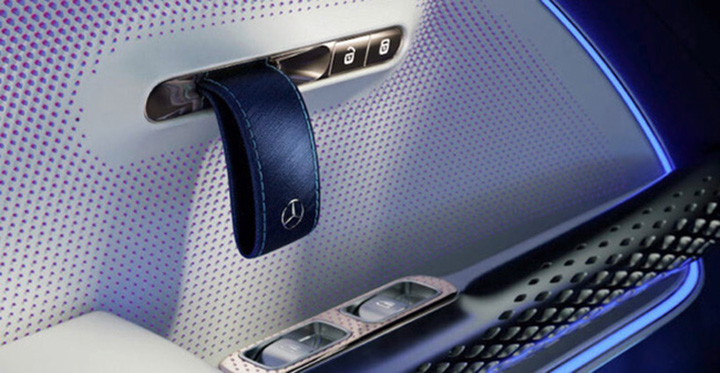
Luxurious ambience
Meanwhile, BMW’s new concept plug-in hybrid electric vehicle, the first in its M class to get an electric motor, has been designed with a new form of luxury and sense of space for the interior. The BMW Concept XM interior is half cockpit and half lounge – the front is fully driver-focused while the rear offers extravagant comfort.
A bold trim element offers clear, visual separation between the driver’s area and the other sections of the interior, together with a decorative surface made from carbon fiber with interwoven copper thread that provides a base for displays, air vents and control/operating elements.
The luxurious lounge-like ambience in the rear is decked out in “petrol blue,” together with deep-pile carpet with a diamond pattern. Only the diamond-shaped area of the head restraints is leather trimmed, while the lower sections of the seats offer high comfort and an exclusive couch character with luxurious velvet upholstery and diamond quilting.
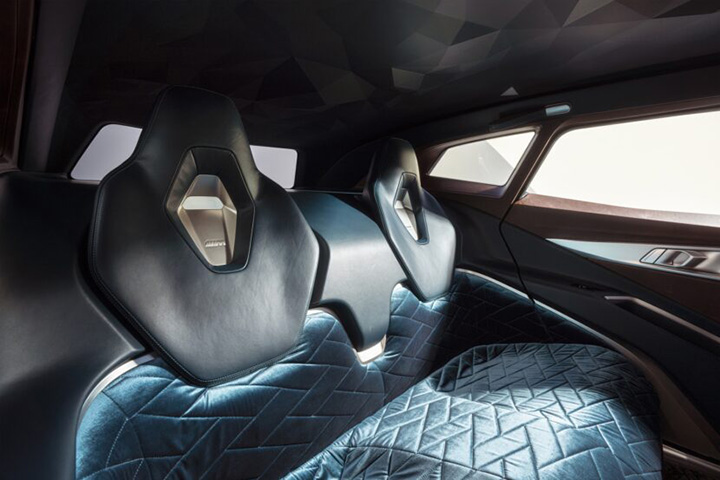
Family space
South Korean car maker Hyundai recently unveiled its Seven autonomous vehicle concept that maximizes interior space. When the usual driver’s equipment is not in use, the cockpit and integrated screens create a lounge-like experience, with swiveling lounge chairs and a curved bench seat.
The seat arrangement can also be customized depending on driver-controlled or autonomous driving modes. When the smart hub and front seats combine with the rear chaise-lounge seating, the interior becomes a communal, family living space.
Beyond the use of recycled materials throughout the interior, such as mineral plaster, bamboo wood and carpet, the bio-resin and interior paint are also based on renewable sources. The use of copper and hygienically treated fabric with antibacterial functions ensure all surfaces inside the car remain clean at all times.
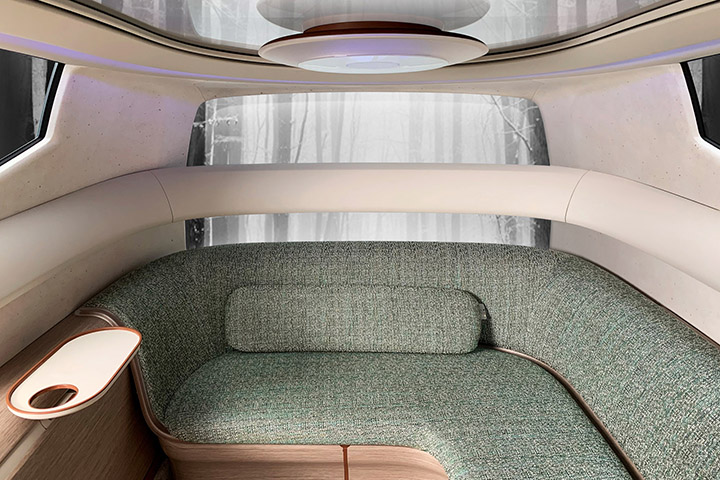
Hygienic surfaces
One of the impacts of the pandemic has been the concept of car sharing losing ground to personally owned and driven vehicles, which are seen as offering a significantly greater margin of safety.
“While the sharing trend is currently on hiatus, it will pick up again once the pandemic is over,” according to Ralf Imbery, head of surface material innovation, transformation and design at Continental. “The pandemic has led to much greater attention being placed on surface materials offering special hygienic properties.”
Continental believes future car-sharing concepts will require interior surfaces and fabrics that are antimicrobial, rugged, durable, resistant to soiling and easy to clean, and disinfectant-resistant.
Germ-repelling seat covers
This is equally the case for aircraft interiors, where airlines are attempting to ease the infection control concerns of both passengers and employees.
A recent report from Bloomberg indicates that demand is booming for aircraft seat coverings designed to repel bacteria, viruses and other pathogens, which when properly applied can reduce the presence of pathogens on seats, thereby reducing the frequency of cleaning tasks in between flights while ensuring the same level of safety.
According to France-based Safran Seats, one airline carrier has been able to successfully reduce daily rotations on seat disinfecting from eight to six with the use of these seat coverings, although the International Air Transport Association continues to recommend other standard cleaning procedures for aircraft seats, including vacuuming of loose particles, belt buckle disinfection and visible stain removal.
Leather fiber composite
Fabric and moquette seating upholstery has been widely used throughout public transport sectors, including inter-city bus and national and international rail applications, mainly due to the low up-front acquisition costs of such materials.
However, passengers on public transport are becoming more aware of fabric seating upholstery’s retentive properties of dirt, dust and potential bacteria and pathogens, according to UK-based engineered leather producer ELeather.
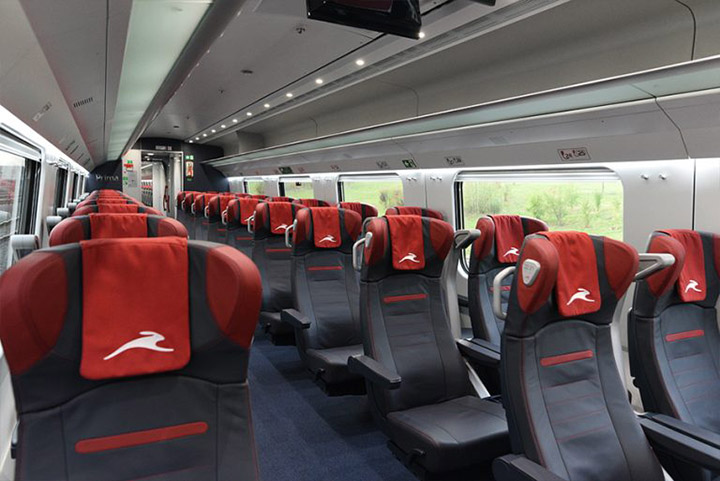
Further, expectations regarding comfort and cleanliness are now greater than ever and touchpoints, particularly seating upholstery material, that passengers engage with throughout a single journey are being analyzed and re-evaluated to ensure a positive passenger experience.
ELeather says that although the patterns of moquette and fabric seating upholstery are designed to hide the numerous stains and dirt lodged in the fabric itself, the material is harder to clean and often requires specialist equipment to do so.
The company adds that easy-to-clean, hard-wearing materials such as leather fiber composite offer a more hygienic upholstery solution compared with fabric and moquettes, while also having greater design variation potential, such as embossing, stitching and printing.