With the global automotive industry facing unprecedented change over the next few decades, suppliers of automotive textiles, including nonwovens and composites, are being challenged to realign their strategies as these major market transformations unfold.
As well as advances in electrification, one of the key drivers is the effort to commercialize self-driving vehicles – it is anticipated that by 2035 around half of all new vehicles could be fully autonomous.
Other disruptive technologies include artificial intelligence, virtual and augmented reality, fuel cell and battery advances, the Internet of Things, sensors and digital technologies. Major trends that will have an impact on the automotive industry include car-sharing in urban cities, end-of-life recycling, sustainability and the need for lightweight materials based on increasingly stringent carbon dioxide (CO2) emission regulations for new vehicles.
Increasing demand
Automotive textiles encompass a wide variety of products ranging from upholstery, flooring and headliners, to filters, tire cords and passive safety. Most are used for interior trim, such as seat covers, carpets, headliners and door panels, with the remainder used to reinforce tires, belts, hoses, seatbelts and airbags, and for filters and insulation.
The value of textile materials going into the 91.5m cars and light vehicles manufactured globally in 2018 was estimated at US$86bn, according to a new market report, Automotive Textiles: Preparing for total transformation.
Meanwhile, the amount of textiles used in new vehicles continues to increase as automakers seek further means of lightweighting to reduce emissions and improve fuel consumption, as well as higher demand for increased comfort and improved safety.
The use of textile materials has increased from 20 kg in a mid-size car in 2000 to 35 kg (around 45 m2 in terms of surface area) today, most notably from the adoption of textile and composite underbodies as replacements for metal.
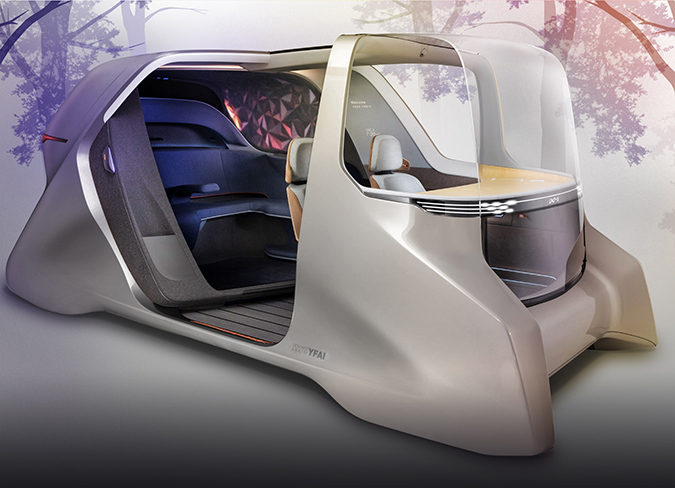
Early vehicles
The first commercialized car designed in 1885 by Karl Benz featured steel tubing and a driver “compartment” created using wood panels. The earliest vehicles had no interiors as such, and comprised only a wooden board seat covered with a scrap of leather, a fabric remnant or a horse blanket.
As vehicles became more sophisticated, emulating horse-drawn carriages with passenger and then driver compartments, later models employed a range of natural fiber materials, such as flat woven wool, cotton broadcloth and woven mohair pile fabrics; natural leather continued to be employed.
Leather and wood interiors continued up to the 1950s along with the introduction of plastic moldings, while the post-war years ushered in the age of synthetic fibers with automotive interiors beginning to resemble the luxurious, tailored, upholstered furniture of upmarket living rooms. Synthetic leathers and coated fabrics such as vinyl were also introduced, particularly to improve durability and cleanability.
Now, with the drive towards lowering weight for reducing both fuel consumption and CO2 emissions, many current developments are including new uses for fabrics and other fiber-based materials.
Customization
Autonomous vehicles, electric vehicles and car sharing will soon redefine vehicle use as the car becomes a multifunctional, mobile living and working space.
Self-driving vehicles will be customizable in a number of different modes – traditional, working/meeting, relaxed/lounge, family – with the seat becoming a multifunctional interior component providing safety, comfort and entertainment.
These changes present major opportunities – and challenges – for suppliers of materials for vehicle interiors.
Technology is enabling vehicle designers to come up with new uses for “old” materials, making fabrics and surfaces “smart,” and enabling customization. This will include the use of smart fabrics, antimicrobial surfaces, active glass, attractive finishes and sustainable materials, as well as personalized lighting and multi-sensor infotainment systems with more screens and fewer switches and buttons.

Recycling
Despite initiatives such as the End of Life Vehicles Directive in Europe, there is still a significant volume of automotive plastic that is not currently recycled and is destined for landfill or incineration.
In fact, the direct recycling of fiber-based materials, such as textile fabrics and nonwovens, used in vehicles is insignificant and is likely to remain so in the near to mid-term future.
With textiles accounting for only around 30 kg of the average car weight of 1.5 tonnes, there is little incentive for any attempts at recycling fiber-based automotive materials compared with efforts to recover metals and plastics – even with the minimum 95% recycling target as stipulated under the ELV Directive.
For the time being it is likely that textiles from end-of-life vehicles will continue to end up as landfill or be incinerated, apart from synthetic fibers such as polypropylene (PP) that are more easily recovered through mechanical recycling processes, although there is relatively little PP currently used in fiber-based automotive materials.
However, regulations such as the ELV Directive do have implications for reducing the use of hazardous substances when designing vehicles, including automotive textiles, and for the design and production of vehicles that facilitate the dismantling, reuse, recovery and recycling at end of life.
Car buyer priorities
But while there is likely to be an increase in the use of recycled textiles in vehicle manufacture, the use of such materials can increase the final vehicle cost – and the purchaser has to be interested in having recycled/sustainable materials. Recent research has shown there is high interest for this in North America, but less in Europe.
There is new evidence that car buyers are increasingly looking at the total cost of vehicle ownership, including fuel consumption, life cycle assessment and environmental impact, and original equipment manufacturers (OEMs) are trying to incorporate this in their new designs.
For example, French car maker Renault has co-developed a fabric made from 100% recycled materials for the new Zoé subcompact vehicle. The fabric is made from seatbelts, textile scraps from the automotive industry and polyester fibers from recycled polyethylene terephthalate (PET) bottles, and is used in the manufacture of seat covers, dashboard coverings, gear lever brackets and door fittings.
Meanwhile, Autoneum has developed Hybrid-Acoustics PET, a lightweight textile made from PET fibers, largely obtained from recycled fibers, which can both insulate and absorb sound waves for use in automotive engine bays. The Switzerland-based supplier of acoustic and thermal management solutions for vehicles has adapted its Hybrid-Acoustics textile interior technology to enclose electric motors, thereby contributing to lighter, quieter and more environmentally friendly vehicles.
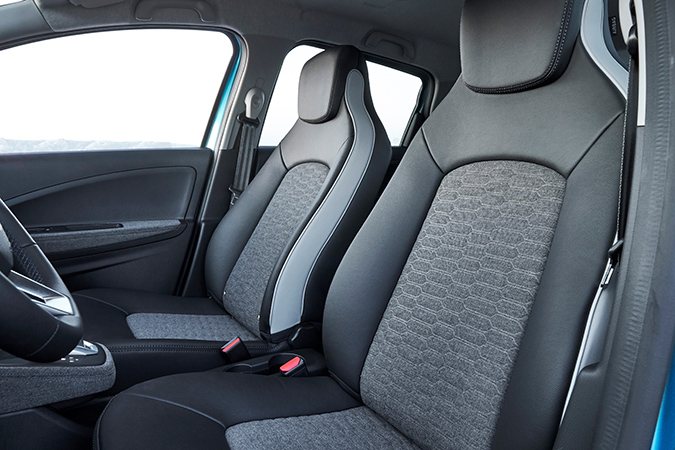
Natural-fiber composites
With increasing consumer environmental awareness and sustainability regulations over the past decade, the automotive industry is under increasing pressure to fulfill environmental and performance demands as well as higher fuel efficiency at competitive costs.
Automakers are now recognizing the potential of bio-composites – natural fiber-reinforced polymer composites – providing these materials offer the same performance as traditional composites, but with lower weight.
From the early days of automotive production, steel has been the preferred option for structural components requiring high strength. Initially, the vehicle bodywork was wooden, which required a time-consuming and expensive varnishing process; the first all-steel car was fabricated in the United States in 1912.
Then in 1941, Henry Ford unveiled a prototype, plastic-bodied “soybean car” that weighed around a third less than an equivalent steel-bodied vehicle. It is thought the body panels and fenders were made from a soy-based bioplastic reinforced with natural fibers, although no one is quite sure of the exact make-up of this early version of a bio-composite (besides soybeans, other ingredients were possibly wheat, hemp, flax and ramie).
However, when the U.S. entered the Second World War at the end of 1941, all Ford vehicle production was suspended and the soybean car project was abandoned; the prototype was apparently destroyed.
Bio-composites
More recently, the U.S. car maker has used kenaf fibers in the door trim of the first-generation Mondeo, which began production in 1993 – the door trim in all Ford cars is now made from a mix of at least 50% natural fibers and plastic. Current Ford vehicles contain on average 9–18 kg of bio-based or renewable materials, mostly as fiber-reinforced plastics.
Automotive supplier International Automotive Components Group (IAC) believes vehicle interiors, such as map boxes, trunk trim, rear seat liners and door components, are where most car manufacturers will use bio-composites in future.
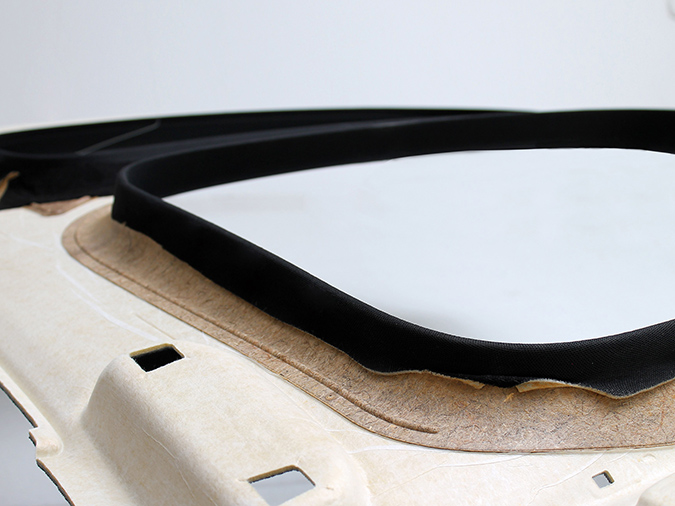
In 2017, IAC launched the first natural fiber composite sunroof frame, which is made from 70% hemp and kenaf fiber and weighs 50% less than a metal sunroof frame. The part is now used on all Mercedes-Benz E-Class and A-Class cars.
The next step could be semi-structural applications, such as front and rear bumpers made from flax fiber composites. A team at the University of Portsmouth in the UK is close to producing a flax fiber material that will meet the mechanical requirements that most vehicle manufacturers specify for engine covers, although they admit that the manufacturing techniques for semi-structural bio-composites will need to be more efficient than they are at present.
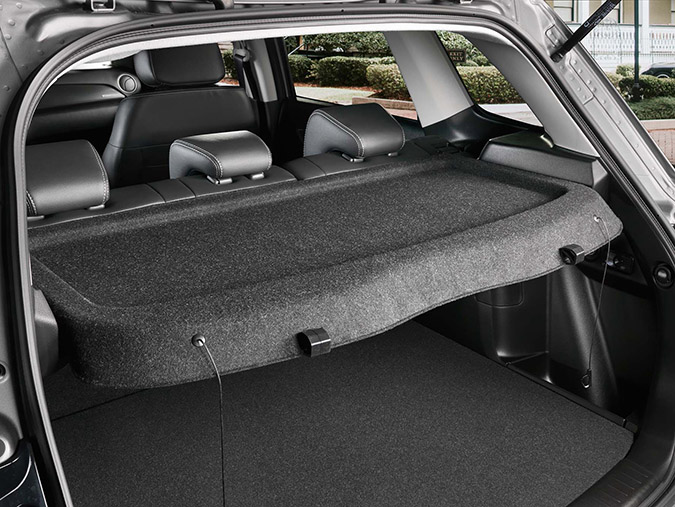
Natural benefits
Compared with many manmade fibers, natural fibers can have benefits in terms of reduced waste disposal, reduction of greenhouse gas emissions and lifecycle considerations.
Natural fibers are also less energy intensive to produce than synthetic fibers. According to the Nova-Institute of Germany, the production of one tonne of glass fibers produces 1.7–2.2 tonnes of CO2 equivalent, while four natural fibers – flax, hemp, jute and kenaf – have an impact of 0.5–0.7 tonnes CO2-equivalent per tonne of fiber produced.
Manmade fibers
The age of synthetic fibers took off after the Second World War, although interestingly Duroplast, a cotton-fiber composite thermoset plastic, was used to make bodies for the East German Trabant car from 1957–1991.
Polyester, which has good ultraviolet lightfastness properties, is now used extensively in automotive interior textiles. Textiles for door coverings and seat fabrics are commonly made from polyester false-twist textured yarns on circular knitting machines, polyester headliners can be manufactured on warp knitting machines, while air-jet textured polyester yarns tend to be used in woven fabrics for car seats, where their good abrasion properties are advantageous.
Meanwhile, Austria-based cellulosic fiber producer Lenzing is pushing its lyocell and modal fibers produced from renewable wood sources as alternative materials for car seats, floorcoverings and other vehicle interior applications. These fibers are said to combine natural softness and efficient moisture management, providing enhanced breathability, while driver and passenger comfort additionally benefit from their minimal static charge.
Carbon fiber
Carbon fiber is increasingly being used in the aerospace industry, having grown from around 10% of the weight of an aircraft body 20 years ago to more than 50% in the latest models, such as the Airbus A350 and Boeing 787 Dreamliner.
Previously the preserve of limited-edition luxury sports cars and racing cars, many major vehicle makers have been driving the use of carbon fiber-reinforced plastic (CFRP), forming partnerships with carbon fiber manufacturers to secure raw material supply and share know-how.

Global production of carbon fiber for all applications was estimated at 78,500 tonnes in 2018, which is forecast to grow to more than 150,000 tonnes by 2025. The market for carbon fiber in automotive applications was estimated at over 7,000 tonnes in 2017, with more than 100 models currently specifying CFRP for OEM components. This market is projected to grow to almost 11,000 tonnes by 2025.
Carbon fiber has comparable properties to steel, but is only one-fifth the weight. However, the barriers to increased use of carbon fiber in mainstream automotive applications include its cost and the limited supply, as well as time-consuming production technologies. There are now a large number of collaborative projects aiming to develop high-volume carbon fiber-reinforced composites manufacturing processes for automotive end-uses.