When I first entered the smart textiles industry, there was little knowledge of electronic textiles (e-textiles). People had this skeptical kind of curiosity, like they were something out of a science fiction movie. Or, more popularly, that they are just another fashion trend. Over the last nine years, I have been working hard to prove that e-textiles are not just a thing of the runway, but an impactful “ingredient” that can provide a range of useful functionality to cars, medical devices, and other essential items. To put it simply: E-textiles are a foundational technology that allows us to merge soft goods and electronics. And I believe they will one day be the basis for human-machine interfaces and devices.
While many view e-textiles as lab technology, our team at Loomia views e-textiles as a solution for engineers and designers who need the right blend of electrical and mechanical properties for their products. Current solutions on the market today are not flexible enough and/or have poor electrical performance. Engineers and designers needed something with a higher bend radius limitation, less pesky wires, and that could be easily integrated into several materials. Many e-textiles, like the Loomia Electronic Layer (LEL), can achieve this in a cost-effective and scalable manner.
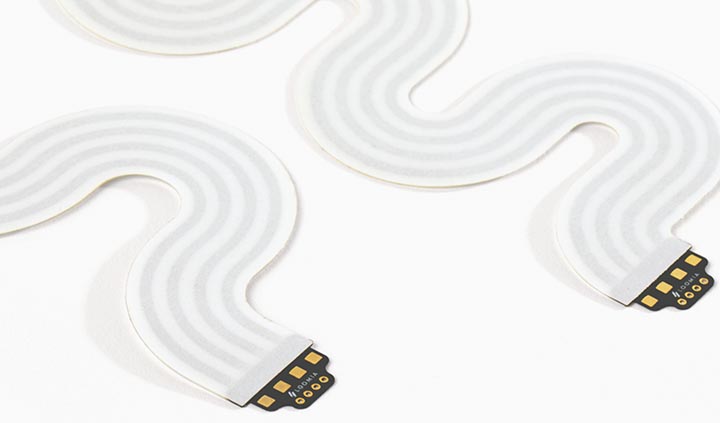
E-textiles are useful for many other reasons, as well. They are not only lightweight (due to reduced conductor weight) and robust, but they offer a clean finish and there is less manual work needed in manufacturing. E-textiles may sound complicated, but the idea is simple – e-textiles make integration easier for soft goods that require electrical function. A t-shirt that requires charging for power is one example of a project we worked on with Analog Devices. (You can learn more about the Stitch garment on their website.)
Many people inside and outside of the industry have asked me, “Well, if we’re not talking about using e-textiles in fashionable frocks, what can they be used for?” My response is that the use cases for e-textiles are broader than you could imagine. This technology can be used in a wide variety of application areas: automotive interiors, robotics, and medical wearables, to name a few. They can be used to provide heating, lighting, and sensing capabilities to so many products; the list would be too exhaustive for this article. For example, in automotive and airplane interiors, e-textiles could be implemented for seat heating, human-machine interfaces (such as backlit buttons) and soft sensors.
E-textiles are a foundational technology that allows us to merge soft goods and electronics. And I believe they will one day be the basis for human-machine interfaces and devices.
Projects That Prove Concept
To cite a couple of projects, we have worked with Covestro, Hyundai and Festo on various projects.
For Covestro and Hyundai we were tasked to create solutions for automotive interiors. For the Covestro project, the project was to design a heating and lighting system that was thin enough to be integrated into a roll-up top shade for a sunroof. Prior to working with the company, they were on the hunt for technology that could add function to their films and bring heating and lighting capabilities to the car interior, specifically for an electric vehicle. It was determined that our LEL technology was both flexible enough and possessed the features needed.
Prior to our work with Covestro, we were approached by Hyundai to provide their door panels with heating and lighting. They were seeking innovative concepts for a spec vehicle and wanted to implement smart surfaces. The LEL was integrated directly under the door trim and created a smart surface with minimal tooling. These two case studies are an example of how e-textiles can bring dimension to something we use every day.
Robotics are a whole other area that can incorporate e-textiles – something we did not even realize until we began experimenting and researching possible use cases. In robotics, e-textile technology is typically used for sensing, industrial climate control, and data and power cables for wearables. They are mechanically designed for an elevated level of performance, so they are ideal for an application that requires a lot of seamless motion – like robotics.
We worked with Festo, a leader in robotics, to develop a 113-point pressure matrix, glove design, backlit logo, and PCB integration for a robotic arm. The Bionic Mobile Assistant moves autonomously in three directions, can independently detect objects, adapt its grip depending on the object, and work collaboratively with humans. While some people may be afraid of the increase in robotics, this is an example of one that can improve human lives by making tasks easier.
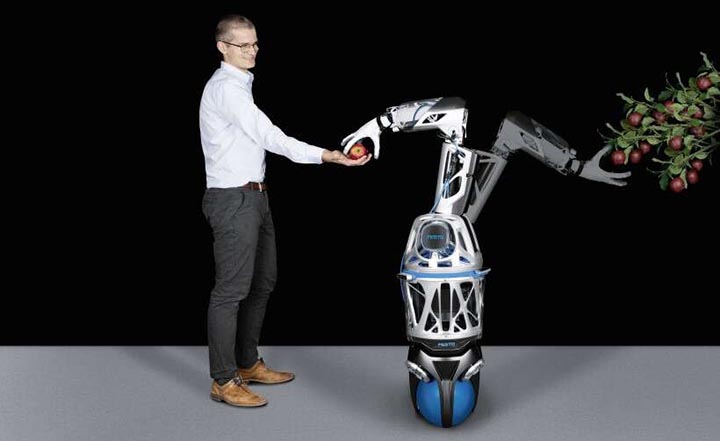
Charting the Way
Working in a new field always involves some uncharted territory and challenges. Some of our biggest challenges and hiccups have come from a lack of testing and standards in the industry. For many developments, we have run into roadblocks where we just simply don’t know how to evaluate something and we often have to grab from other industries in order to create our own standards. I think that having a hybrid design and engineering mindset is critical – sometimes the solution comes from the design field and sometimes it comes from the engineering field. Our biggest learning is that it’s important to be empirical and to be persistent and somewhere between those two, we’ll find a solution.
We are always thinking up new ideas for our technology, and we like to develop ideas that solve real problems. For example, those who have dementia: We concepted a blanket with our e-textile pressure sensor prototyping parts and heating units. This blanket can be used for both patient monitoring and patient comfort. Keeping dementia patients safe and warm are two big pain points, and we felt this could be an easy way to solve both.
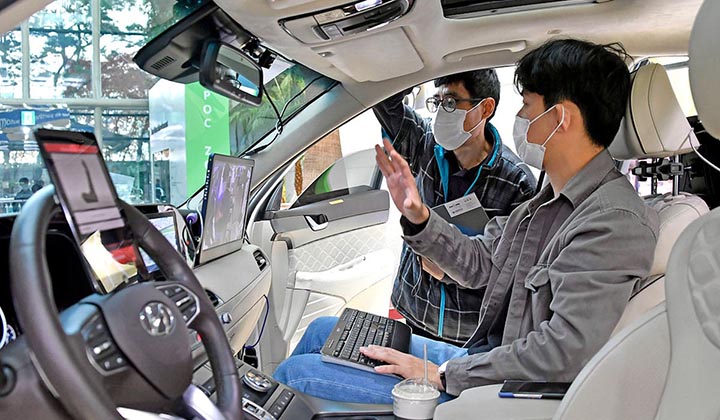
Like most designers and engineers, we were antsy during the pandemic and eager to create new things. As we were tinkering around at home, we brainstormed some ways the LEL could potentially kill the coronavirus on high touchpoint services – such as in medical and home settings. The LEL technology would either be integrated into a glove or a mat. One of our key findings while developing this concept was that the temperature needed to kill the virus could be met by our technology. Additionally, our technology can be easily integrated into any textile-based products – making it the ideal solution for personal protective equipment. While we have not finished developing this idea, we do have the groundwork laid and data points ready to go should another mass pandemic strike again.
IDTechEx says we are in touch with textiles 97% of our lives, so what if these textiles did more than just drape our body?
E-textiles are more than just a fashion statement, and if the industry is going to grow, we need to look beyond light up pants. This technology has the potential to solve large, real-world problems and make lives easier. And it can do so with more ease than the current technological solutions we use now.
While a lack of industry standardization and a clear-cut commercialization plan might be preventing this technology from being widely utilized; that is more incentive for us to develop these standards, so it is easier to bring the technology to market. This is the true next step. My call to the industry is: Let’s make more next-generation products possible with the help of electronic textiles.