Expanding Sustainability Includes Exploring Fiber Advancements in China for the Growth of Their Green Economy
At the 29th China International Manmade Fiber Conference (CIMFC), September 26-27 in Jilin City, Jilin Province, China, experts and executives spoke about challenges and opportunities, advanced materials, manufacturing technologies, and sustainability relevant to the manmade fiber industry.
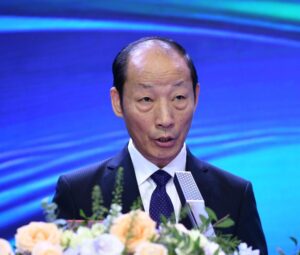
More than 30 speakers and approximate 400 fiber professionals attended the conferences for two days of programming. Speakers and attendees were primarily from mainland China, with representatives from the Europe, Japan, South Korea, Thailand, Taiwan, and Thailand also in attendance.
The conference was organized by the China National Textile & Apparel Council (CNTAC), the Jilin Municipal Government, the China Chemical Fibers Association (CCFA), the China Textile International Exchange Center (CTIEC), and Jilin Chemical Fiber Group (JCFG), the world’s second largest carbon fiber producer, which is headquartered in Jilin City. A combined conference, the 10th China Carbon Valley Carbon Fiber Industry Conference (CCVCFIC), was also held simultaneously with the CIMFC, making carbon fiber a main focus of the events.
Ambition for Carbon Fibers
Jilin Province is where China started its dream for carbon fibers. In 1962, the Changchun Institute of Applied Chemistry (CIAC), a Chinese Academy of Sciences (CAS) branch located in Changchun City, the capital of Jilin Province, began the research and development for carbon fibers. But commercialization hadn’t been achieved until in the 2000s when JCFG and several other Chinese companies launched their carbon fiber lines.
JCFG, founded in 1959 as one of China’s oldest manmade fiber producers, started to manufacture carbon fibers in 2007. Today it has capacity of 49,000 metric tons per year, ranking No. 2 in the world, only after Toray. In addition, it has annual capacity of 160,000 metric tons of carbon fiber precursor, and 20,000 metric tons of carbon fiber composites.
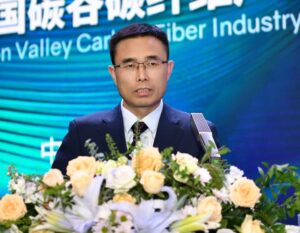
JCFG has an even bigger plan. Currently, it is building several new plants, aiming to expand its capacity to exceed 400,000 metric tons per year in the near future. The goal includes 100,000 metric tons of carbon fibers, 330,000 metric tons of carbon fiber precursors, and 65,000 metric tons of carbon fiber composites.
JCFG’s ambitious expansion is based on China’s fast-growing carbon fiber demand. In 2022, China’s apparent consumption for carbon fibers reached 70,300 metric tons, up 21.98% from 57,600 metric tons in the previous year. Homegrown producers only met part of the demand, with 29,300 metric tons of carbon fibers and their related products imported in 2022. The fast growth and the gap between supply and demand attract Chinese companies to invest a lot more to expand their capacity rapidly.
Carbon Reduction Boosts Carbon Fibers
The booming demand for carbon fibers is mostly boosted by China’s efforts for a green economy. In September 2020, China proposed its “double carbon goal” of reaching peak carbon emissions by 2030 and achieving carbon neutrality by 2060. For this goal, China will largely increase its renewable energy output to replace conventional energy, and wind energy is one such solution. Wind power generation emits zero greenhouse gases, and carbon fibers are the main materials for making turbine blades of wind power plants.
Compared to its main competitor fiberglass, carbon fiber helps reduce the blade weight by approximate 30% due to its light weight and high strength properties. The weight reduction would allow the production of longer blades, which have higher energy efficiency than their shorter counterparts. As a result, carbon fiber has been gradually replacing fiberglass, becoming a primary material for making wind power blades.
China installed over 37.63 million kilowatts of wind power capacity in 2022, increasing its total wind power capacity to 365 million kilowatts. The installation of wind power in 2022 consumed 23.5% of China’s carbon fibers, or 16,520 metric tons, according to ATA Carbon Fiber Tech Guangzhou Co Ltd (ATA), a Chinese consultancy. At the same time, China has a goal for wind power of exceeding 581 million kilowatts by 2025, which means the country will install at least another 216 million kilowatts of wind power capacity in the following three years, creating a demand for another 95,000 metric tons of carbon fibers from 2023 to 2025.
Car Weight Reduction
China’s double carbon goal also relies on emission reduction from other industries such as automobile and aerospace through using advanced materials such as carbon fiber reinforced polymers (CFRPs). For automobiles, CFRPs are often used to make the bodies, chassis, and suspension system components, reducing 20% to 50% weight compared to their metal counterparts. When an automobile reduces 10% weight, it typically reduces 6% to 8% energy consumption. As transportation accounts for around 10% of China’s total greenhouse gas emissions, the use of CFRPs will help China reduce a substantial amount of greenhouse gas emissions.
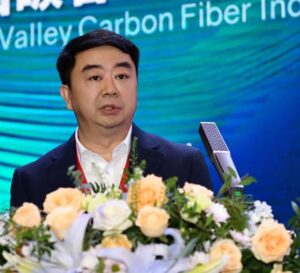
Mr. Ye Fuheng, senior engineer and researcher of China FAW Group Co Ltd (FAW), one of China’s oldest and largest automakers, spoke about carbon fibers’ use for FAW automobiles in the 29th CIMFC. He said that FAW had been developing carbon fiber-based components since 2012, and the company’s flagship model, Hongqi, has used carbon fibers for making engine hook, wrap frame, and other structural components. According to ATA, Chinese automakers took 2.56% of the country’s carbon fiber consumption in 2021, or a total of 1,475 metric tons. Automobiles’ carbon fiber consumption is expected to have a double-digit annual growth rate in the following decade.
Low Manufacturing Cost, Recycling and Bio-Based Route
Although having all the advantages and benefits, carbon fibers are expensive to manufacture, impacting their adoption. Currently, the prices of carbon fibers mostly range from $13 to $35 per kilograms, depending on grades, manufacturers, and specific deals. As a result, experts are looking for new solutions to lower the manufacturing costs for market expansion.
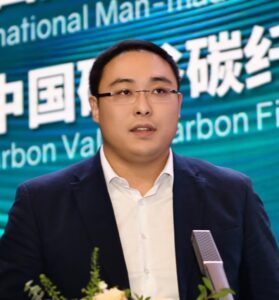
Mr. Ziwen Liu, research assistant at Institut für Textiltechnik of RWTH Aachen University (ITA), introduced a method to shorten the stabilization time by 20% by using potassium permanganate (KMnO4), or nitrogen (N2), under atmospheric pressure as pretreatment media. Today, about 96% of the world’s carbon fibers are produced by spinning polyacrylonitrile (PAN) co-polymer to form PAN fibers, and then thermally converting the PAN fibers to carbon fibers. The thermal conversion process includes multiple steps such as stabilization and carbonization. Stabilization usually accounts for 15%-18% of the total cost of making carbon fibers. Mr. Liu said that the method not only reduces the stabilization time, but also lowers the stabilization temperature. The reduced time and lower temperature would result in energy reduction and cost saving.
Recycling is another solution for lowering carbon fiber cost, and also makes carbon fiber’s lifecycle more environmentally friendly. However, most of the recycling methods currently available in the market would produce short fibers and cause fiber damage, thus decreasing the quality and values of recycled carbon fibers.
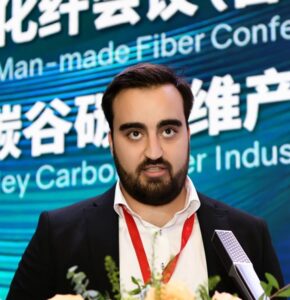
Mr. Deniz Yesilyurt, research assistant at ITA, introduced a new method to reduce the fiber damage by optimizing surface treatment and sizing. He said in the conferences that this method would make multiple recycling for continuous carbon fibers a possible solution.
On the other hand, although carbon fibers help reduce weight and emissions, their production still emits a substantial amount of greenhouse gases as they mostly made from fossil-based PAN.
Mr. Stefan Schonauer, another research assistant at ITA, said in the conferences that making acrylonitrile (ACN), the raw material of PAN, from bio-based glycerin is a promising solution. He said the glycerin used for making ACN is a waste in biodiesel production, which is significantly cheaper than crude oil. As a result, the glycerin route is both greener and more economic than the fossil routes.