For the past few years now, Industry 4.0 concepts have been introduced by the leading European suppliers of technologies for the production of synthetic fibers and nonwovens.
In 2020, some of these new ideas have been tested to the full.
Most notably, remote support services to customers have not just been in demand, but proved vital in respect of many new installations, with travel between countries – and even within them – having not been possible for extended periods.
Unprecedented demand
Reifenhaüser Reicofil, headquartered in Trosidorf, Germany, was thrown into the middle of a maelstrom between February and May, as the demand for its meltblown technology for the production of facemask filters reached unprecedented levels.
It initially reacted by reducing the delivery time for one of its new meltblown lines from nine months to three, but was overwhelmed by demand.
Reicofil has subsequently recorded a backlog that puts delivery of a meltblown line ordered today to 14-15 months in the future, but at the same time is pulling out all the stops to expand its existing capacity to meet demand as quickly as possible.
The engineering behind such a line is extremely complex, according to sales director Markus Müller.
“It’s a challenge to build a line where every fiber is smaller than one micron,” he explained. “This requires extremely precise machinery and control of the process. It starts with the dosing, and the temperature controlled extruders. It is important to achieve equal distribution in the coathanger die and equal heating and/or cooling of the die, as well as perfect quenching of the meltblown air.”
It is reported that some of the over 100 meltblown installations made by Chinese technology suppliers during the COVID-19 crisis period subsequently ran into problems due to being unable to meet these exacting engineering standards.
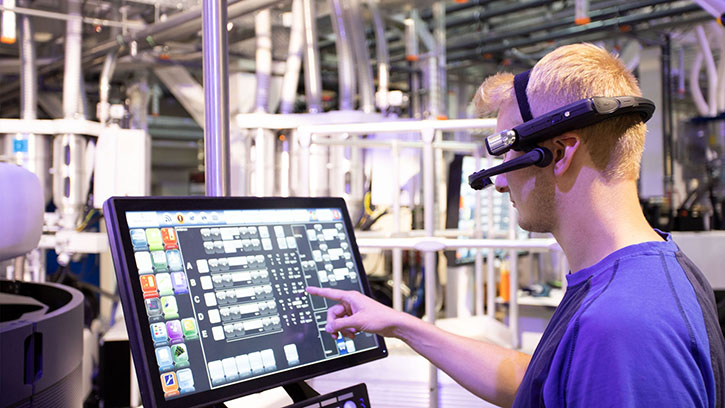
Visual assistance
When it came to remote support services, Reicofil was able to benefit from the proven Industry 4.0 progress made in plastics extrusion by the Reifenhaüser group, notably in the supply of blown-film lines.
The group has already used its Visual Assistance services to start up blown-film lines all over the world and is now adopting these techniques for meltblown installation.
Among these IoT tools, a customer’s assembly team can send on-site assembly activity live by smart glasses to the Reifenhäuser Visual Assistance Cockpit in Troisdorf. Experts assigned to the project there guide the customer’s team step by step, using remote communication and based on specific instructions and checklists. The experts also provide the technician with all the necessary information on an integrated display. All of this is part of a software platform that instructs the technician with exactly what needs to be done in a specific situation at the right time.
Support using smart glasses is just one of many solutions in the package to make Reifenhäuser’s service portfolio available in digitized form. In 2020 these services have been extended to meltblown installations.
Most notably, remote support services to customers have not just been in demand, but proved vital in respect of many new installations, with travel between countries – and even within them – having not been possible for extended periods.
Backlog
Fellow German company Oerlikon also reports very high demand for its meltblown technology.
“At the start of this year we changed all of our processes in order to shorten our delivery times from nine-to twelve months, down to five,” said business development manager Ingo Mählmann. “We are now in a backlog situation, so realistically it is six months from signing a contract to start-up of a line. We continue to sell lines to China, but there has been strong demand from Europe and North America, with customers taking advantage of various funding programs that have been introduced.”
During 2019, Oerlikon began the process of fully digitizing all of its technologies for the conversion of polymers into filaments, yarns and nonwovens. This includes operations such as automatic labelling, yarn packaging and fiber and nonwoven bale logistics which to date have been covered by third-party solutions.
In addition to process monitoring on smart phones and tablets via an online service app, remote maintenance can now be carried out on Oerlikon’s plant equipment by Microsoft HoloLens.
HoloLens is a holographic computer built into a headset which allows the technician to see, hear, and remotely interact with holograms. Microsoft has built the headset to operate independently, without the need to be wirelessly connected to a PC, and it employs high-definition lenses and spatial sound technology to create an immersive, interactive holographic experience.
Robustness
Autefa Solutions, of Friedberg, Germany, has provided remote services for the commissioning and troubleshooting of its machines for staple fiber nonwovens for many years, with 24-hour availability.
“Because our machines and lines are very robust and reliable, only customers with production lines older than 15-20 years – with no remote access – faced some problems,” said the company’s CMO Marco Fano. “At the beginning of the crisis and with the first lock downs, we were able to respond to many requests for retrofits to those older production lines to enable remote access.”
He added that due to measures implemented at its own manufacturing plants, Autefa has been able to deliver machines on time since the beginning of the crisis.
“As worldwide travel is still restricted there have been some additional complications with the erection of machines and production, but we have well established service people located in key areas around the world and in addition, with long term contracts with reliable sub-suppliers, our spare parts service has not been disrupted at all.”
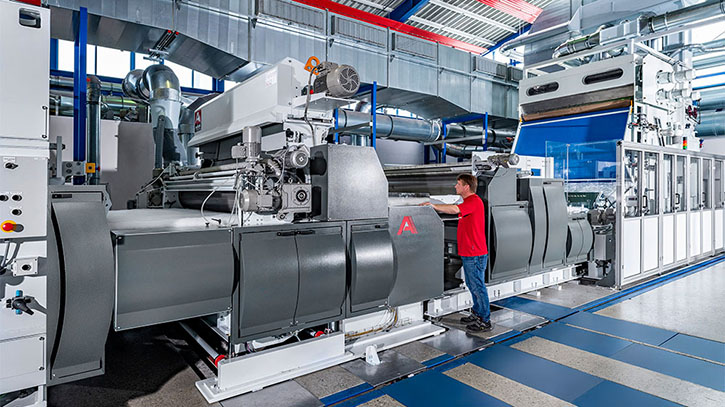
Metris
Andritz Nonwoven has meanwhile been able to field test components of its Metris Industry 4.0 system.
The Andritz Group’s digitalization drive began over a decade ago, initially with pulp and paper mills where millions of tons are being produced daily, so the benefits of optimization are very immediate.
Andritz Nonwoven adopted these now proven tools and started to implement programs to push the digitalization of nonwoven technologies two years ago and this January opened the first Metris Performance Centre dedicated to the industry in Montbonnot, France.
Two key components of the Andritz Metris system have proved particularly useful when travel was not possible – the Metris Remote Assistance System and Metris Predictive Maintenance.
Following its acquisition of Italian converting machinery group Diatec in 2018, Andritz has not only been able to rapidly develop an advanced facemask converting machine in record time, but also test the Metris system to the full.
“Just prior to the lockdown in Italy, we had delivered a new diaper line from Italy to a company in the Ukraine,” said director of business development Alexandre Butte. “We were then unable to send technicians to install the machine, but with the Metris Remote Assistance System we managed to talk the customer through all the initial stages of its testing and operator requirements, so that it could start on time. It is now fully operational.”
He added that the company has also seen a big surge in demand for the Metris Predictive Maintenance service.
“Everybody is now beginning to see the benefit of this. For globalized companies, the data allows automatic reporting graphs from all plants to be generated and shared internally between companies of the same group anywhere in the world. This is allowing the efficiency of a group’s entire global operations to be increased and decisions to be taken. These are the two major areas where we have seen digitalization ramped up a lot in the last six months.
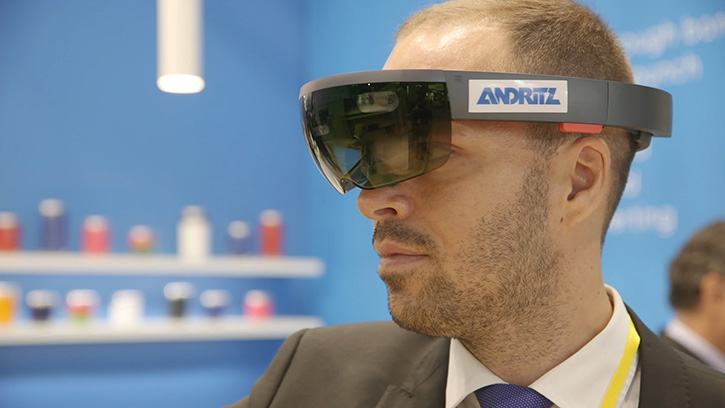