For most of the 20th Century, Eastman Kodak held a dominant position in photographic film – back in 1976 it had an 89% market share of all U.S. photographic film sales.
The company began to struggle financially in the late 1990s as a result of the decline in sales of film and also its slowness in shifting to digital – despite having invented the core technology used in current digital cameras, as well as having amassed a vast portfolio of some 10,000 patents.
By that time, however, Eastman Chemical – the Kodak subsidiary founded by George Eastman in 1920 to supply Kodak’s chemical needs – had already been spun off as a separate corporation and now stands as a leading Fortune 500 company in its own right, with 14,500 employees globally and annual sales of around $8.5 billion.
Plastic-to-plastic
In January this year, Eastman announced plans to build one of the world’s largest plastic-to-plastic molecular recycling facilities at its huge complex in Kingsport, Tennessee, with completion expected in 2022. Through methanolysis, this world-scale facility will convert over 100,000 metric tons of plastic waste that cannot be recycled by current mechanical methods annually into new specialty plastics.
At INDA’s RISE (Research, Innovation & Science for Engineered Fabrics) conference, which took place from September 28-30, Jon Woods, Eastman’s general manager for textiles and nonwovens, outlined the extent of the waste plastic problem and his company’s development of a number of solutions in response to it.
“Plastics are still crucial to solving a lot of the world’s problems, but the waste issue must be solved,” he said, adding that of the 300 million tons of plastics produced annually, 40% is landfilled, 25% is incinerated and alarmingly, 19% escapes into the environment.

“Only 16% of what is produced is collected for recycling and only 12% actually gets collected, so it’s not hard to see we have a problem,” Woods said. “A combination of both mechanical and molecular recycling will be required. Mechanical recycling has its limitations in requiring a pure input stream, typically single polymer products, but molecular recycling is about taking products back to their molecular building blocks to be reassembled into new products, with the potential to enable infinite value to be created.”
CRT is an integrated, molecular recycling technology that breaks down waste plastics, such as post-consumer carpet fiber and plastic packaging materials, into basic molecular building blocks for the manufacture of new products including textile fibers.
Methanolysis
Eastman is investing approximately $250 million in the Kingsport methanolysis facility, and Woods said the company’s process using plastic waste as the main feedstock is a true material-to-material solution and will not only reduce the company’s use of fossil feedstocks, but also reduce its greenhouse gas emissions by 20-30% relative to fossil feedstocks.
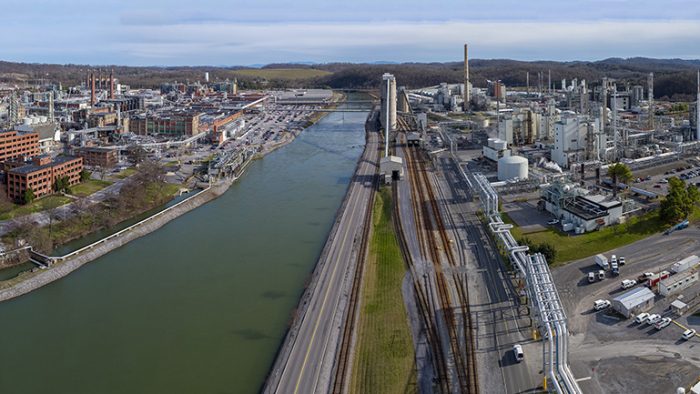
Eastman has pioneered methanolysis technology at commercial scale and has more than three decades of expertise in this recycling process.
The company’s existing advanced circular recycling technologies also include carbon renewal technology (CRT) and polyester renewal by glycolysis.
CRT is an integrated, molecular recycling technology that breaks down waste plastics, such as post-consumer carpet fiber and plastic packaging materials, into basic molecular building blocks for the manufacture of new products including textile fibers.
Naia Renew
In 2020, Eastman introduced its Naia Renew fiber, based on CRT and combining 40% recycled waste plastics with 60% wood pulp.
The fiber is traceable, with certified biodegradability that captures the value of hard-to-recycle materials that would otherwise be destined for landfills. Importantly, it can be produced at scale.
Available as both a filament yarn and a staple fiber, Naia Renew offers clear advantages over other materials. As a filament, it results in fabrics with a silky hand, rich luster and fluid drape and is being used to create fashionable womenswear garments. In staple fiber form, fabrics produced are inherently soft and quick drying, with reduced pilling properties, making them ideal for everyday casual wear.
Fully circular, Naia Renew is produced with a low carbon footprint in a closed-loop process where solvents are safely recycled back into the system for reuse.
Recycling plan
Polyester renewal, however, is an especially impactful solution, as low-quality polyester waste that cannot be mechanically recycled would typically be diverted to landfills, incineration or end up in the environment.
With methanolysis, this waste can instead be recycled into high-quality polyesters suitable for use in a variety of end-use applications.
The Kingsport plant will be complete by the end of 2022 and is a major part of a comprehensive plan by the company to recycle more than 250,000 tons of plastic waste annually by 2030 via molecular recycling technologies. The company has committed to recycling more than 125,000 tons by 2025 and now has an agreement with Procter & Gamble – one of the largest users of nonwoven fabrics in its absorbent hygiene products (AHPs) – to further accelerate the transformation of plastic packaging and collaborate on circular recycling solutions.
These efforts will complement the current recycling streams in the United States and enable additional recycling options for consumers eager to help solve the plastic waste problem. The two companies will work to expand the collection of hard-to-recycle plastics which will be used to create new materials via Eastman’s molecular recycling technologies.
Co-located
“Our feedstock strategy is very much focused on the plastic waste that is not being addressed today and we have the unique advantage of having co-located technologies that together can recycle many types of plastic waste,” Woods said. “We will buy waste streams, including PET strapping used in packaging, fines and dust waste from recyclers and chunk PET waste from both plastics producers and recyclers.
“We will partner to provide outlets for difficult to recycle waste such as carpets and create new feedstock streams of other mixed and colored PET not fit for mechanical recycling. We are already making solid progress in securing multiple sources of feedstock for the new methanolysis facility.”