There are important considerations relative to fiber characteristics and how they impact the converting processes chosen for the manufacture of personal care products. Discussing examples specific to diaper, feminine hygiene and adult incontinence products, the following will focus on converting practices to boost throughput, improve efficiency and enhance brand image. Trends in the industry relative to sustainability will also be addressed.
Formatting processes, such as large-format spooling and wide-web flexographic printing, must be performed with precision to maintain the functionality and unique characteristics of each nonwoven material’s fiber content and construction.
The converting process
Converting is the process of changing a raw material or other product inputs into a format that can be used more efficiently downstream in the manufacturing chain. Converting often involves taking large-format materials and transforming them into a smaller format required for high-speed manufacture of the final product.
One example is slitting and spooling large raw material master rolls into narrower widths. Printing is also a type of converting.
Converting is important to hygiene and personal care product manufacturing because it enables end-product manufacturers to optimize efficiencies within their operations, save costs and speed time to market. If a diaper manufacturer had to perform the steps in-house to get raw materials into a usable format, it would require a lot of specialized equipment, facilities space, resources and time. But if a converter can deliver material that has been printed, slit and spooled precisely to run through that manufacturer’s automatic diaper-making machinery, the diaper OEM can hit the ground running with production.
Trends in converting for hygiene and personal care
Hygiene and personal care businesses are focused on efficiencies, cost savings, product differentiation and sustainability. As a result, they need converting partners who can help them with these priorities.
Regarding efficiency, large-format spooling (LFS), or traverse winding, as explained in more detail below, is a converting trend that dramatically increases uninterrupted run time while reducing labor and scrap. When it comes to product differentiation, multicolor printing is a major converting advantage. Brands, private label owners and institutional buyers all face a very competitive landscape, and they need to differentiate their products to respond to evolving consumer demands. One way they are making their products stand out is through colorful prints. In particular, the baby diaper and adult incontinence product markets are releasing attractive new multicolor print designs. In fact, the latest adult incontinence products look and feel a lot like cloth underwear, from the material’s cloth-like feel to a more tailored fit to a wide variety of colors and patterns. Finally, with respect to sustainability, there is growing interest in renewable fiber content for hygiene and personal care products. There also is a focus on reducing waste, emissions and energy throughout the product lifecycle. Here again, manufacturers need converting partners who have expertise in working with all types of materials and offer efficient processes such as wide-web printing and LFS to help them meet sustainability goals.
Considering fiber characteristics
The converter must have deep knowledge of a material’s fiber characteristics and overall construction because these factors affect how the material can be handled and successfully formatted. The inherent attributes of the material, whether that’s moisture management or softness or elasticity, must not be impacted during converting.
For example, too much or too little tension during slitting, spooling and printing can damage the material’s innate performance characteristics or its ability to run smoothly through end-product manufacturing equipment.
As mentioned above, precise tension control is an essential converting best practice to maintain fiber performance characteristics. Expert converters should be able to customize the tension for successful processing of a wide variety of materials, from thin, extensible materials to thick, high-loft materials. Just the right tension must be maintained throughout the material web as it is converted, whether that involves unwinding, slitting, spooling, printing, laminating or other processes. Related to printing, another best practice is to have 100% vision inspection and pre-print web cleaning. This helps to ensure a clean print, regardless of the substrate’s fiber content.
The importance of formatting processes
Formatting processes must be compatible with a nonwoven material’s fiber content and construction. If they are not compatible, then it opens the door for quality problems.
Material suppliers build a great deal of value into their products, and it’s up to the converter to preserve all those properties so that the end-product manufacturer captures that value in the finished product.
For example, if a nonwoven is lightweight and thin, the converter must take these properties into account when printing in order to avoid ink strikethrough. This occurs when ink penetrates too far, from one side of the material to the other. Likewise, if there is too much tension or packing force on the material roll as it runs through various web-based processes, the material characteristics can be compromised.
For example, some diaper materials have a 3D construction, with tiny cone-shaped ridges built into the material web to deliver greater breathability and moisture management. The tension and packing force must be precise when slitting and spooling these materials, or else the cones can be crushed or inverted, impacting their intended performance.
The importance of large-format spooling
LFS is an efficiency-boosting take on traditional unwinding, slitting and rewinding.
First, a large master roll of material is received by the converter. With Web Industries’ proprietary LFS solution, these master rolls can be up to 120 inches (304.8 cm) wide and have an outer diameter of 60 inches (152.4 cm), or with extra-large format spooling (XLFS), these master rolls can be up to 120 inches (304.8 cm) wide and have an outer diameter of 72 inches (182.2 cm).
Next, the converter unwinds the material onto slitting machinery, slices the material into narrower widths and then rewinds, or spools, it into multiple rolls, ready to be used by the end-product manufacturer. These rolls can hold material strips cut into slit widths as narrow as 1 inch (2.5 cm) to 4 inches (10.2 cm). The slit materials are spooled onto rolls that are a width convenient for the end-product manufacturer.
With its LFS technology, Web Industries can take incoming master rolls of up to 118 inches (299.7 cm) wide and 60 inches (152.4 cm) outer diameter and slit and traverse wind them into rolls of up to 48 inches (121.9 cm) wide and 60 inches (152.4 cm) outer diameter. With its Extra-Large Format Spooling (XLFS) solution, Web Industries can take incoming master rolls of up to 120 inches (304.8 cm) wide and 72 inches (182.8 cm) outer diameter and slit and traverse wind them into rolls up to 50 inches (127 cm) wide and 60 inches (152.4 cm) outer diameter. (Figure 1). The slit width of the material on these XLFS can be up to 12 inches (30.5 cm).
At the end of the day, LFS is important because it enables manufacturing partners to leverage many economies of scale and efficiencies, such as:
- Processing large orders quickly;
- Fewer material changeovers and longer uninterrupted run time (Figure 2);
- Less packaging material; and
- Greater utilization of trucks and containers.

Wide-web flexographic printing
Wide-web flexographic printing is a high-speed printing method ideal for printing on nonwoven diaper top-sheet material, acquisition distribution layer (ADL) materials, label indicators, diaper tabs and other personal care and hygiene materials.
High-quality flexographic printing, especially multicolor printing, is important for building brand awareness. The more colorful the product design, the more attractive the product and the better able the brand will be at engaging the consumer.
Wide-format printing is also important today given the growth of the adult incontinence product market. These products require wider format materials than baby diaper products. Also, when it comes to the printing processes used in their supply chain, customers want the freedom to choose between water- or solvent-based inks. Some may want to use both and need their converter to offer a customized printing solution. With its multiple wide-web flexographic presses from Windmöller & Hölscher, Web Industries offers this flexibility.
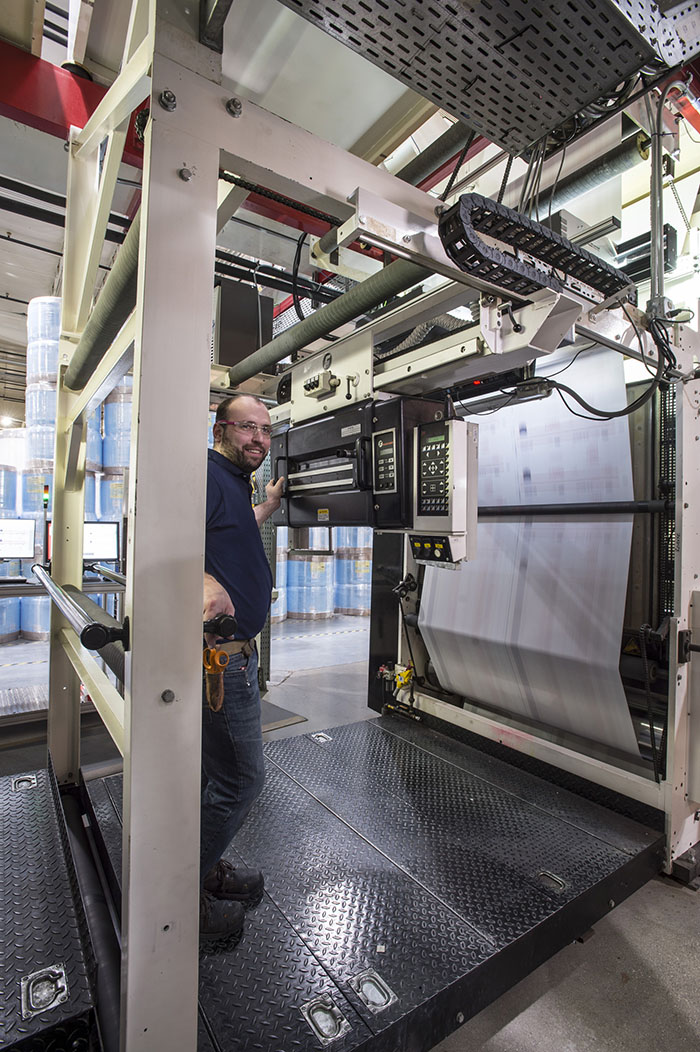
Photo courtesy of Web Industries Inc.
Sustainability
The converting industry, like many others, is extremely focused on sustainability. In the personal care and hygiene markets, end consumers are increasingly interested in sustainably sourced products and desire greater transparency into the supply chains of the brands they buy.
Efficient converting practices such as LFS reduce packaging, material waste, fuel consumption and emissions due to the ability to leverage larger raw material rolls and consolidate shipments of larger slit spools into single truck or container loads. There also is less end-product waste because there are fewer splices in the formatted material roll. Therefore, there are fewer instances when a visible splice could end up in a finished diaper. Some manufacturers will scrap products containing splices.
Leading converters also have implemented recycling programs throughout their operations for packaging and waste, and some return scrap material to suppliers for recycling.
The future
Going forward, there will continue to be a lot of emphasis on sustainability. Fiber and material suppliers, manufacturers and their converting partners will need to collaborate on the optimal materials and processing paths to conserve energy and reduce emissions, waste and overall consumption of chemicals and natural resources.
Product innovation ultimately is the main driver of success in the fast-paced consumer products markets, including personal and home care. There is a very real competitive advantage to rapidly and cost-effectively bring differentiated, exciting and useful products to consumers.
When efficient converting processes and practices like multicolor printing, high-speed slitting and LFS are all under the same roof, converters can provide fast, scalable service to manufacturers and help them get their latest products in front of today’s consumers before the competition.