Smartex is Engaging AI in Quality Control, Creating a Convergence of Technology, Mathematics and Production in the Modern Textile Factory
In a presentation at ITMA Milan 2023, Gilberto Loureiro, CEO and founder of Smartex, laid out a vision of possibilities for the modern textile factory. Legacy manual methods for quality control and production plague the industry with inefficiencies and waste. But, what if some of that manual labor and machinery was modified by technology? In an industry still relying on old school production methods, Smartex’s CEO presented a case for such a change, and it was compelling.
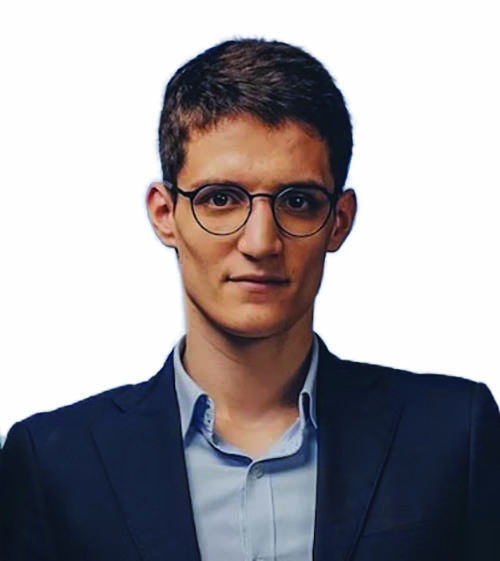
Smartex technology empowers textile factories and brands towards a more efficient, sustainable future – decreasing textile waste, saving natural resources, troubleshooting quality control, and minimizing financial impacts surrounding customer complaints. Smartex offers three technology products: CORE, FACT and LOOP.
CORE addresses production line quality control, inspecting every inch of fabric with precision and speed using artificial intelligence and machine learning. FACT is a real-time production tool where managers gain full control and visibility of textile operations. This is achieved through pre-determined metrics employed from production to inspection, which is accessible from a mobile or desktop device. LOOP works to resolve customers’ problems with tagging of textile rolls with QR codes during production to allow historical data to be accessed months later from the actual production time frame.
The company has gained support of well-known technology investors and is recognized by the European Union for its efforts. International Fiber Journal caught up with Loureiro to see where the company is today, and how Smartex can revolutionize textile production.
International Fiber Journal: What made you aware of the problem Smartex aims to solve?
Gilberto Loureiro: We are at the intersection of technology, physics, computer science and mathematics with textiles, and these places don’t overlap too often. Because of that, there are not many startups or technologies in this industry.
In my family, everyone works in textile and fashion industry factories. When I was a teenager, I worked with my family in their employer’s factory for extra money, and I hated it. My job was fabric inspection on the production line – an exhausting, manual job.
Looking back, it was fantastic to work in knitting mills, the garment manufacturers, and dye houses to see the whole process. I realized, well, this industry is massive; it moves billions and billions of items, and largely affects many lives. There are so many inefficiencies in quality, such as fabric inspection, internally and externally, which causes disruption and disagreements between suppliers and customers, and it is all still mainly documented with pen and paper. I saw that this was stressful and inefficient.
With no desire to follow my family into textile work, I was very lucky to go to college – the first one in my family – to studying physics and finance. It was here I met co-founders Antonio Rocha, CTO and Head of Product and Paulo Ribeiro, VP of Engineering. Antonio was the electronics hardware guy and Paulo was the computer science guy. As we discussed my frustrations with the textile industry, ideas to bring technology to it became “aha” moments for us to pursue the idea to connect the tech and textile worlds.
We looked at cameras, UV lights and infrared lights – technologies that we were studying in physics – to potentially apply to textile machines. That was how our ideas evolved. We decided early on to only address the quality control issues – detecting defects that could stop machines and production, including ways to avoid waste.
We are at the intersection of technology, physics, computer science and mathematics with textiles, and these places don’t overlap too often.
Today, we are always stumbling into larger problems to solve. For instance, the traceability issue and the digital product passport are the new hurdles. With our ongoing discoveries, Smartex continues to store knowledge to tackle issues. Currently, we are doing research and development on the digital product passport, helping factories to produce efficiency metrics, and the use of televisions and gamification for employees, and things like that.
IFJ: You’re just out of college, and you all decided that you could solve this legacy textile industry problem. What gave you the confidence to move forward that you thought you could do it?
Loureiro: Sometimes being a bit naive and ignorant helps some of these moves. We were talking with so many factories about the problems, everybody confirmed, ‘Oh yeah, that’s a big problem. We lose millions on that.’ Quality control, massive problem. Dyeing, huge problem. The textile industry is the largest in the world yet remains largely untouched by the internet. Before Smartex, most of our clients relied on pen and paper systems, and analog applications at best.
In 2018-19, we had other jobs while developing our idea for Smartex. Then, we all decided to leave our jobs, leave Portugal and move to China because it was a hub place of activity, and in some ways still is, to build robots, hardware, cameras, drones, and electronics. We were super lucky to have our first investor, the HAX program with offices in San Francisco, New York, London, and Shenzhen, China. They invite fund-backed companies to work in Shenzhen with their massive team of engineers – to help naive guys like us to build robots and hardware systems. So, that was the first step.
In development, we came up against the real hindrances of the textile industry. For example, many of our clients don’t have internet at all, not even connectivity in the areas. So, we created a cloud-based solution, and so on. Many of our clients have very old machines that cannot incorporate technology solutions. Some don’t even have electric connections near their mechanical machines. These are the challenges.
We are more experienced after five years and scaling worldwide. We are now in India, Bangladesh, Pakistan, Turkey, Brazil, Portugal, and other countries. (we are present in 13 countries). Maybe if we knew the whole story back then, we wouldn’t have jumped in so fast. Thank God we did.
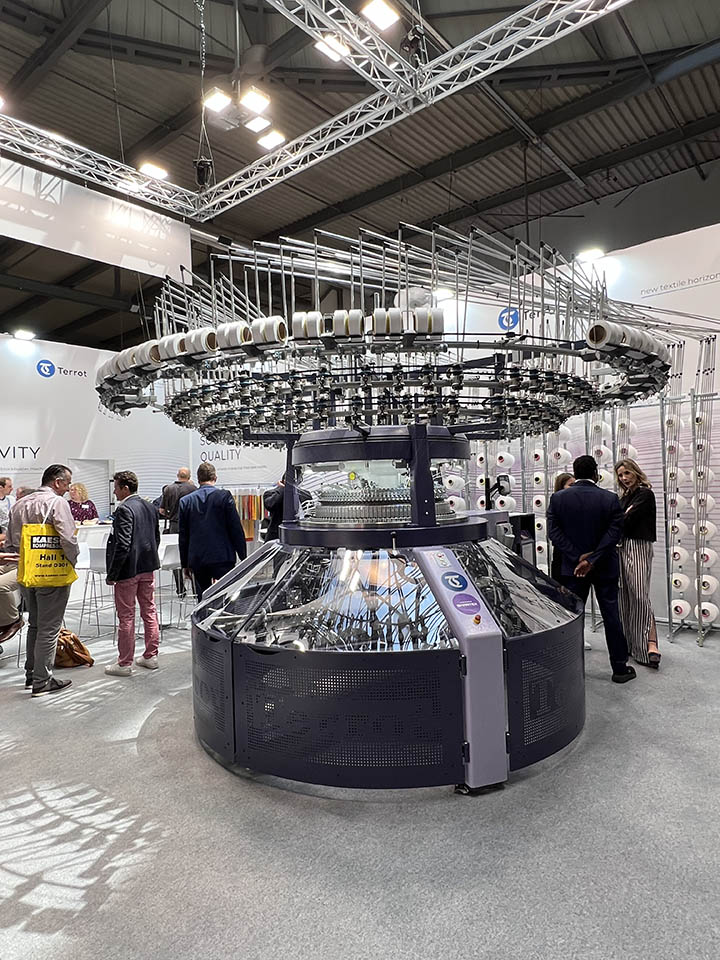
IFJ: You were first backed by the San Francisco fund. Did you have other investors?
Loureiro: Yes. We always have been humble. I guess that’s one of our superpowers. We know that we don’t know a bunch of things. So, we are constantly chasing experts who do. We have investors from the textile world. Some fashion brands have invested in us through Fashion for Good’s investment fund.
Brands like Adidas, H&M, Indy Tags, and PVH Corp. invest in this fund to help startups. We have also the robotics hardware investors from Silicon Valley, and the machine learning and deep technology investors, also from Silicon Valley, and investors from Europe. Lightspeed Venture Partners, one of the largest VCs in the world, are investors. Anthony (Tony) Fadell, father of the iPod and iPhone, is a force multiplier as one of our largest shareholders. He is also one of my personal mentors.
With input from these smart people, we fail less, but we still fail a lot. We are continuously looking for new investors because we know that if someone will change this industry, it will not be alone. We want to partner with machinery builders in Switzerland, Germany, Italy, and Japan, and with legislators and certification companies. We are open to collaboration. Being a very complex industry with a vast global supply chain, no one can solve this alone. Members at various ends of the supply chain do not often know each other. It is really something that makes this industry special, but also why I believe this industry will be probably the last one to be fully automated.
And that’s one of our missions.
IFJ: Tell us specifically about your company product offerings.
Loureiro: We started the impossible; and it’s still not perfect. Yet, I believe if we started this company 10 years ago, it wouldn’t be possible at all. The first building block that is essential for Smartex tools to be effective is internet connectivity. We install routers, access points, cables, cameras and sensors, etc.
Smartex CORE addresses the pain of defects and waste. It is technology that makes machinery “smart,” to combine the production and inspection processes, traditionally separate steps.
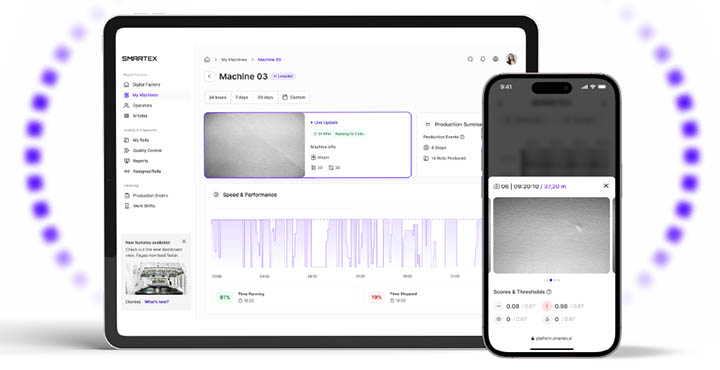
Smartex FACT addresses the ability to go back in time once a product is shipped. If complaints come in after something has been received by a customer, there was no way to verify the problem existed in production. We create a set of computer screen platforms that record a machine’s productivity or worker performance in a previous time frame. We used to say, “your factory in your pocket.” The production manager wants to check who is the best worker, why is that machine stopped, why is that thing not being well-produced, why is there so much waste. This tool allows the production manager to get the answers through a computer screen.
Our product Smartex LOOP communicates to the client the quality of the product that he receives. A LOOP QR code as a label on a textile roll – a super roll – is like quality control insurance. Anyone can scan it to see if the roll was fully inspected, with no surprises.
Many times, the dye houses receive client calls about defects in shipped materials, causing fabric waste and credit notes, sometimes for millions of dollars. For many, one complaint means they need to work the next three months without any faults to cover that cost.
IFJ: How long did it take to get a working model of Smartex CORE, FACT or LOOP?
Loureiro: It took a few years to monetize, but we had working model installations in the first few months of the company, then continuous refinement. Still today, we cannot say that everything we have done is perfect. Like other technologies, there is a constant evolution. We invested already more than $20 million in research and development in patents, discovery, and engineering, and we need to invest much more. We have five years of company life, 150 people, mostly software engineers, and still so much to be done.
We focused on the main mission which was detecting defects in textile production. While others ask us to apply this technology to other parts of the industry, we prefer to be where we are, and make sure we kill it here.
IFJ: Tell me about how you test your products and work with a client to install Smartex.
Loureiro: Whenever we do product upgrades or new product tests, we have an abundance of spinning and weaving mill partners here in Portugal. We have some partners for development, where we can test out new things in a working model. Then, we start monetizing it and charging the partners for it. We have now over 100 clients already using the initial CORE product.
Istanbul is another great place for talent, software, and textiles. We acquired a company there last year; now we have 10 engineers there. We now have Turkish development partners, too.
We collaborate with a company, with trial and error, when installing Smartex; then, as soon as we feel that we are creating value, we monetize it. That’s what differentiates us from a research center. We have R&D expenses, but it is monetizable at the end of that process, scaling to commercialization as the goal.
IFJ: Your mission is to empower textile factories to be fully traceable, with zero waste. You also produced the “Modern Textile Factory Report,” found on your website. Tell us about this.
Loureiro: Everyone talks about sustainability, traceability, and digital product passports. From our perspective, what we need to do is involve the factory in the discussion. Eighty percent of the impact of this industry happens in factories, especially in dyeing, and in all the other stages, in terms of water, chemicals, energy usage, etc. For the average fashion brand, 98% of their environmental impact is in their supply chain. We must move the conversation about traceability and sustainability to include the “98%” of where problems are found. Some brands are aware of this and are building infrastructures in manufacturing to support the whole supply chain.
I feel that we are in the right place at the right time. Legislation, smart factories, and awareness are at the forefront of real change. Yet, factories still don’t have the necessary technology to maneuver change. Part of the mission of the Modern Textile Factory Report is general education – we cannot get to the collective goal of sustainability and circularity without information.
In the traditional factory, no one knows the source of imperfections, but everybody has an opinion about it. An investment in technology gets to the real source of an issue.
IFJ: Can you give us details on current and future development?
Loureiro: We cracked a problem that was never cracked before; no one has ever spent so much money and time focusing on textile defects and quality control. We have 150 engineers looking at specific problems.
If you are not going fully vertical on textiles, you are not going to break the mold. Many that have tried tech in the past – like computer vision – complain about two things. First, the tech is not at the human level, to understand the nuances in textiles. A defect for you is not a defect for me; there are many materials, colors, wrinkles, fluffs. Second, the ROI is so tight that every cent matters. These two things – tech and ROI – need to be perfectly aligned.
Solving these two issues, Smartex is at the “human level,” at an affordable price with one- or two-years payback period. In two years, we sold more than 1,000 devices. If you look at any other supplier of computer vision camera inspection, they sell a few times per year. That’s a signal that we are on the right track.
Now looking at the future, we are thinking where we can expand. An obvious place is going vertically – textile factories have other machines. So, our plan is to eventually connect the dots.
IFJ: What is your realistic view for automating the textile industry over the next 10 to 15 years?
Loureiro: I think the direction might be 10 years or a little bit longer for full automation. The main issue is textile production is driven by geographical factors.
One factor is sewing. It is very manual and always pushes this industry to cheap-labor countries. Then, one country raises prices, and everybody is looking to another country, right? Sewing is an inflection point that I am really interested and is the reason textiles are constantly being pushed to cheap labor countries, which often lack connectivity.
In theory, you could have the whole industry in mainstream countries or cities, with super automated factories that do it right – with less waste and energy, and more efficiency and profit. We could have centralized factories closer to consumers, minimizing the environmental footprint that long-range shipping creates.
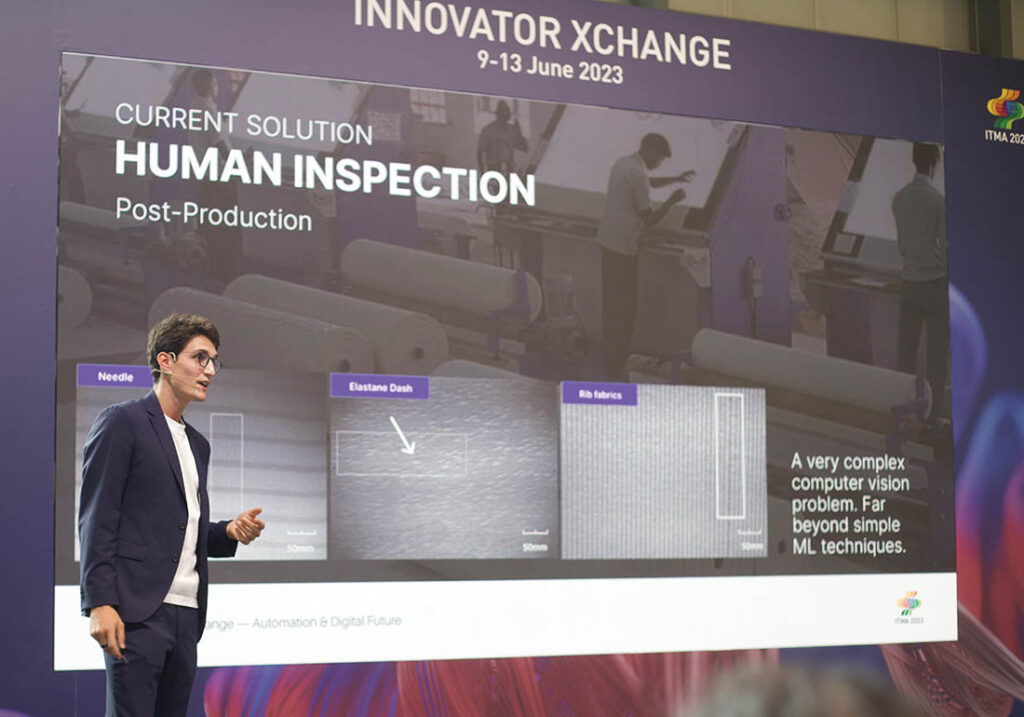
Origin of the materials is the second factor; we can’t control where the cotton grows, for instance. It is normal to see textile factories located in these places to be fully vertical there.
These two things are very limiting for other innovations to occur.
In 10 years, I can still see factories and textile production in these low economy locations, but this trend will gradually decrease with more automation options, which offsets the labor factor, and with
increasing environmental legislation.
I was talking with you a few minutes ago about tech and price. Legislation is the new wave for compliance and cost. Depending on how hard the rules become, it could be a push for decentralization, where factories move to places with first-world access to resources that enable green initiatives, and less concentration in China or in Bangladesh that lack traceable accountability measures.
We might expect production to be more expensive because of compliance with these factors. But we should not expect a decrease in consumption from consumers or for them to pay for them. Consumers won’t pay for sustainable materials, even if they may say they want them. The “say-do” gap is huge on the consumer side. We shouldn’t ignore these massive problems because of cost.
IFJ: What is your advice to up-and-coming textile entrepreneurs?
Loureiro: I divide textiles innovators into three categories. One is material types like alternative leathers or yarns. The second one is process technology or automation. The third one is in the retail and consumer arena. My general advice is to focus on a niche pain point in one segment that everybody agrees is an issue. Then, expand the alternatives and make sure that you kill it in that category – go deep on that.
And then expand it, because you will have much more market knowledge as a team – and eventually, funding. We raised $40 million with investors, but we also had $10 million in sales. You need to have the initial spark to have the initial flame and then have the initial fire. All these need to be in a specific order.
There is a vast range of things to improve upon; we need more entrepreneurs in this industry. That’s one of my missions, attract more talent to fill this industry.
IFJ: Do you have final thoughts to share?
Loureiro: 2024 is the best year ever to be working in technology, because of all AI and machine learning advancements. The textile industry’s environmental impact numbers are massive. This gives us a special energy at Smartex. We believe technology is best to solve these problems.