According to a report by Textile Media Services, the value of the global composites market was around $96 billion in 2019, and while components reinforced with carbon fibers generally gain all the attention through their association with Formula One motor racing and the aerospace industry, glass fibers account for well over 90% of the market by volume and over 75% of its value.
Other fibers employed in niche applications include para-aramids, UHMWPE (ultra-high molecular weight polyethylene) and basalt, while there is a growing interest in flax and other natural fibers as composite reinforcements.
Glass fibers
Continuous filament glass fibers can contain silica sand, soda ash, limestone, kaolin and dolomite all blended and then melted in a furnace at approximately 1,500 C to form molten glass with a uniform controlled viscosity. The molten glass is then drawn through a multi-hole heat resistant bushing, which has multiple precisely drilled openings through which the glass flows to form thin filaments.
The filament diameters range from 5 to 30µm, and they are treated by various sizing processes, which help to protect them during weaving or braiding. Sizing also determines the adherence of the glass fiber to different resins, and therefore the quality and properties of the end-use application, depending on their further processing.
The leading manufacturers of continuous filament glass fibers include Owens Corning, China Jushi Group, Chongqing Polycom International Corporation (CPIC), Johns Manville, Nippon Electric Glass (NEG), Şişecam Group and Taishan Glass Fiber.
There have been significant new capacity expansions made in glass fiber over the past two years, with Owens Corning, for example, expanding in France and India, Jushi and Johns Manville both adding plants in the U.S., Şişecam Group installing a new plant in Turkey and Taishan investing in India.
Transportation, construction, and pipes and tanks are the biggest end-use markets for glass fiber, and glass fibers are also the most common reinforcement in wind energy applications.
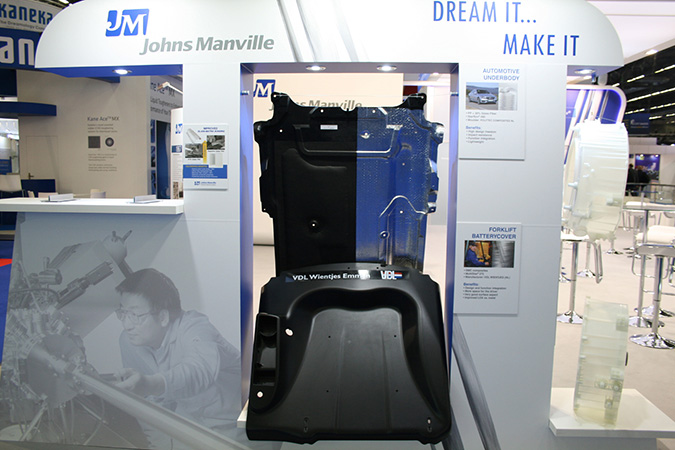
Wind turbines
In the wind industry, glass fiber is used in various textile formats in blades, spars, shear webs and shells, as well as in additional components like nacelles.
“Glass fiber weighs more than carbon fiber, and is not as stiff, but it is more impact-resistant and has a greater elongation-to-break,” explains Peter George, senior consultant for the UK-based Future Materials Group (FMG), which has assisted a number of technical textile manufacturers to successfully enter the composites industry. “Depending on the glass type, filament diameter, coating chemistry and fiber form, a wide range of properties and performance levels can be achieved.”
A wind turbine’s size and efficiency grows with increased blade length, he adds.
“Blades must at all times remain stiff enough not to hit their own support tower and this is achieved by design with thicker blades and materials such as carbon rather than glass, and material morphologies such as multi-axial rather than woven fabrics. Each development, particularly the use of expensive carbon, has to be cost effective since the ultimate aim is lower cost performance.”
Aerospace demands
Only the advanced performance of highly engineered and extremely expensive carbon-based structures will suffice for applications such as the wings and fuselage of the latest Airbus and Boeing planes.
Carbon fiber is a material consisting of extremely thin fibers of around 0.005-0.010mm in diameter and composed mostly of carbon atoms. The atoms are bonded together in microscopic crystals that are more or less aligned parallel to the long axis of the fiber. This crystal alignment makes the fiber very strong for its size.
Carbon fiber has been defined as containing at least 90% carbon, obtained by controlled pyrolysis – the thermochemical decomposition of organic material at elevated temperatures in the absence of oxygen
The term graphite fiber is used to describe fibers that have carbon in excess of 99%.
Carbon fiber is a non-isotope material, which means that all fibers have to point in the same direction as the force-lines through the material. If this is not the case, there will be an opposite effect in terms of effectiveness. Wood, for example, is also not isotope, while aluminum and copper certainly are.
Carbon fiber’s specific strength is considerably higher than silicon carbide (SiC), aramids, aluminum alloys or steel and its density is also much lower than that of steel, making it ideal for applications requiring low weight, which has ensured its continuing success in aerospace applications.
“The stringent requirements of the aerospace industry demand high strength-to-weight ratios for all materials used,” says Peter George. “Depending on the anisotropic (directional) strength needs, unidirectional or multiaxial fabrics with straight uncrimped fibers are used to maximize the effectiveness of expensive fibers such as carbon and aramids. Fabrics are engineered to meet and exceed the crucial requirements for core strength, durability, fire and fatigue resistance.
“A financially significant benefit of composites in aerospace, beyond strength to weight, is the reduced need for expensive maintenance compared to traditional materials, due to higher overall durability.”
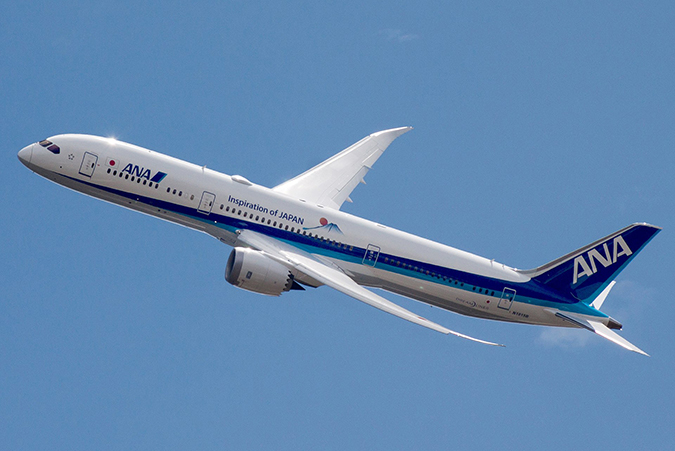
Carbon capacity
According to a recent report from the German industry association Carbon Composites, the theoretical global carbon fiber capacity in 2019 was 159,000 tons, with the top ten manufacturers accounting for almost 90% of it.
By far out in front with almost 50,000 tons of capacity is Japan’s Toray, which in addition to incremental capacity increases, significantly added to its size through the acquisition of Zoltek in 2014. The second largest manufacturer in 2019 is SGL Carbon with 15,000 tons, followed by Mitsubishi Chemical, Teijin (Toho Tenax), Hexcel, Formosa Plastics, Solvay (Cytec), Zhongfu-Shenying, Jiangsu Hengshen and DowAska.
Expansions
Despite the major investment required in adding carbon fiber capacity, an additional 44,100 tons is currently being planned by a range of players. Toray continues to make incremental expansions to its existing plants while looking to forward integrate by acquiring carbon composite manufacturers. Of the other leaders, Teijin, Hexcel and Zhongfu-Shenying have also announced capacity expansions.
Of new entrants, DowAksa is creating a new 13,400-ton capacity plant in Turkey involving an investment of US$545 million, to become operational in 2023. South Korea’s Hyosung has meanwhile announced a long-term investment of $828 million which will provide it with 24,000 tons of carbon fiber capacity by 2028. The key driver for Hyosung is the growing demand for hydrogen and natural gas transportation and storage containers made from carbon fiber composites. Hyosung’s first manufacturing line is due to become operational in 2020.
By far the most ambitious plan, however, has come from China, with Kangde Group announcing an enormous investment of $7.3 billion to create a carbon fiber complex with an annual 66,000 tons of capacity.
This would correspond to approximately 44% of today’s global market at a single location and would significantly exceed the current position of the world market leader Toray.
As part of the first stage, two carbon fiber lines and numerous infrastructure buildings are currently in parallel construction with a timeline for completion earmarked for 2023.
“Initial activities indicated a very rapid build-up by Kangde, but this has been increasingly overshadowed by financial irregularities at its parent company, as well as initial financing problems and legal disputes,” says Michael Sauer, author of the Carbon Composites report. “Against the background of these irregularities, the timeline and probably also the total volume of the project appears increasingly unrealistic.”

Photo by Adrian Wilson
Natural fibers
Finally, the European Confederation of Flax and Hemp (CELC) – the agro-industrial organization bringing together some 10,000 companies at all stages of the production and transformation of these natural fibers – reports that natural fibers continue to make inroads into the composites market.
CELC points out that the use of flax and hemp as reinforcements for composites can exploit a range of useful properties, including impact response, fatigue behavior and biodegradability.
They also have a higher specific stiffness than glass fiber and better vibration damping and insulation properties than either carbon or glass fiber.
Added to this is the case for the cultivation of such natural fibers. The production of flax in Europe results in the capture of some 250,000 tons of CO2 each year – equivalent to the CO2 emissions generated by a medium-sized saloon car driving around the world 62,000 times.