Benefits at Both Ends of the Scale
NatureWorks is continuously expanding its portfolio of Ingeo polylactic acid (PLA) materials which includes well-established grades for fibers and nonwovens, extrusion and injection molding, and increasingly those for 3D printing.
Monofilaments made with Ingeo PLA have notable 3D printing characteristics such as precise detail, good adhesion to build plates with no heating needed, less warping or curling and low odor. This makes them suitable for many different types of printers and for a broad range of printing applications.
A special composite grade of Ingeo was required, however, for a somewhat ambitious project undertaken by the University of Maine Advanced Structures and Composites Center (ASCC) last year – the first 3D-printed house made entirely with bio-based materials.
BioHome3D
BioHome3D was developed with funding from the U.S. Department of Energy’s Hub and Spoke program between UMaine and Oak Ridge National Laboratory.
The 600-square-foot prototype features 3D-printed floors, walls and roof which are fully recyclable and highly insulated with 100% wood insulation and customizable R-values. Construction waste was nearly eliminated due to the precision of the printing process.
“Many technologies are being developed to 3D print homes, but unlike BioHome3D, most are printed using concrete,” said ASCC director Habib Dagher.
“However, only the concrete walls are printed on top of a conventionally cast concrete foundation. Traditional wood framing or wood trusses are used to complete the roof. Unlike the existing technologies, the entire BioHome3D was printed, including the floors, walls and roof. The biomaterials used are 100% recyclable, so our great-grandchildren can fully recycle BioHome3D.”
Composites
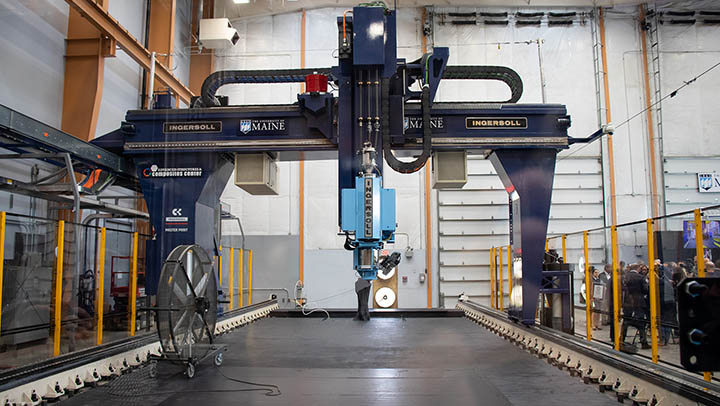
“Our interest was in making 3D printing greener and using more renewable materials to decrease the carbon footprint and we were introduced to NatureWorks through our partners who have previously used PLA in a demonstration project for the printing of a pavilion,” explained Susan MacKay, ASCC senior R&D program manager. “PLA is known to print really well and it’s used worldwide in desktop printing in filament form, but when you get to large-scale additive manufacturing there are some issues.
“While we liked the renewability of PLA we incorporated wood fillers wood flour, nanocellulose and pulp with the PLA to create new types of composite materials to improve the impact and tensile strength. We were struggling with the traditional PLA because it’s semicrystalline, which causes a lot of shrinkage and some distortion.”
“The testing we did showed that compared to the normal semicrystalline PLA, this material worked similarly in terms of mechanical properties but printed better at such a scale,” added Doug Gardner of the Advanced Engineered Wood Composites Center at UMaine. “Having an amorphous polymer lends itself to processing by large scale 3D printing, with less dimensional stress during the laying down of the part and the cooling that occurs during this manufacturing. Most significantly we have used a totally 100% sustainable material that also sequesters carbon.”
Housing Crisis
The U.S. is experiencing a crisis-level shortage of affordable housing. The National Low Income Housing Coalition reports that nationally, there is a need for more than seven million affordable housing units. In Maine alone, the deficit is 20,000 housing units and growing each year, according to the Maine Affordable Housing Coalition. Nearly 60% of low-income renters in Maine spend more than half of their income on housing.
The BioHome3D technology is designed to address these issues and less time is required for on-site building and fitting up the home due to the use of automated manufacturing and off-site production. Printing using abundant, renewable, locally sourced wood fiber feedstock reduces dependence on a constrained supply chain.
Faster
Using the advanced manufacturing processes and materials developed at UMaine, future low-income homes can be customized to meet a homeowner’s space, energy efficiency and aesthetic preferences. Importantly, as the manufacturing technology and materials production are scaled up, homebuyers can expect faster delivery schedules.
The prototype home is currently sited on a foundation outside ASCC, equipped with sensors for thermal, environmental and structural monitoring to test how BioHome3D performs. Researchers expect to use the data collected to improve future designs.
BioHome3D was printed in four modules, then moved to the site and assembled in half a day. Electricity was running within two hours with only one electrician needed on site.
UMaine is no stranger to such large-scale projects – in 2019 it received no less than three Guinness World Records for the world’s largest prototype polymer 3D printer, the largest solid 3D-printed object, and the largest 3D-printed boat.
Peugeot’s Inception
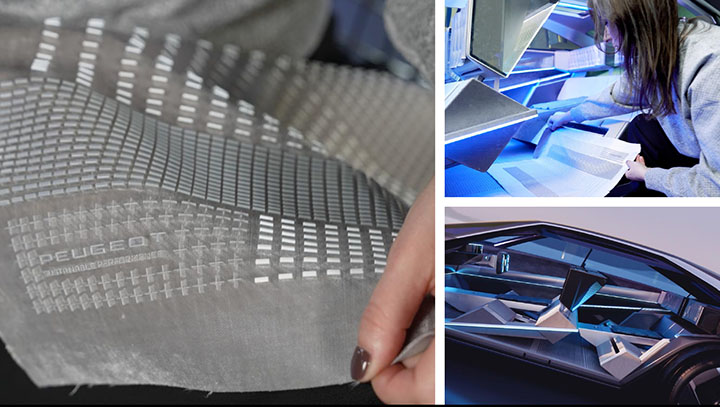
From the macro to the micro – advanced materials produced using Stratasys J850 TechStyle 3D printers feature in the interior of the new Peugeot Inception concept electric vehicle – achieving a level of resolution that would not have been possible with traditional embellishment methods.
The Inception has a minimalistic cockpit devised by design director Matthias Hossann to support the car’s aim of reinventing the driver experience. Immersive seats covered with a velvet made from 100% recycled polyester extend to the floor and feature 3D patterns created with the Stratasys 3D printing technology.
“At Peugeot, we always like to combine function with aesthetics,” said Maud Rondot, of the Advanced Design team at Peugeot. “Our objective with the Inception’s seating area was to modernize the velvet material used and compartmentalize the design by extending it to also serve as a visually impactful floor mat.”
Micro-architectures
Where the floor area space would typically need to be treated with a protective overlay, the Inception concept leverages direct-to-textile 3D printing to deliver a unique combination of functionality, texture and aesthetics which would not have been achievable with other technologies.
“Although we have access to relatively flat designs with current embellishment methods, it is not possible to build thickness and height,” said Rondot. “It is thanks to 3DFashion technology that we could 3D print directly onto the flexible material. Often, there is a delta between what we imagine and what we can obtain, so it was quite magical to see our idea arrive precisely as envisaged and with a remarkable quality of execution.”
The team selected a metallic shade for the velvet, which is designed to play with light before using the printer to create the semi-transparent ‘micro-architectures’.
“Instead of covering the whole stretch of material, it was really advantageous that we could leave the velvet visible,” Rondot said. “3D printing allowed us to modify and reprint the files very easily, but also important is its durability and efficiency – as a technology it doesn’t require molds, which is revolutionary in terms of industrialization.”