In the dynamic and global textile fiber industry with its various manufacturing processes and end-uses, news and information is breaking on a daily basis. International Fiber Journal is tracking stories relevant to our industry from manmade to natural to bio-based fibers, innovations in nonwoven, woven, braided and technical textiles, technologies for additives, bonding, coatings and polymers, and applications from apparel to hygiene to transportation, and more. Here we will post news stories relevant to textile fibers and their downstream applications on an ongoing basis. Please check back for regular updates. If you have news that you feel should be added to this summary report, please email it to Matt Migliore at mmigliore@inda.media.
Most recent update: February 28, 2022
Indorama Ventures reports record FY2021 performance, as global recovery drove volumes
Indorama Ventures Public Company Limited (IVL), a global chemical company with significant interests in the fiber industry, reported a record FY2021 performance as the economic recovery drove demand across the company’s global footprint. The company also committed to being an industry leader in sustainability under its new ‘Vision 2030’ strategy.
In 2021, IVL delivered Core EBITDA of US$1,743 million (up 55% YoY) on production volumes of 14.72 MMT (up 7% YoY). Consolidated Revenue increased 38% YoY to US$14,629 million as consumer confidence rebounded and the company benefited from rising inflation, energy price hikes and supply chain advantages.
Macroeconomic tailwinds supported IVL’s performance, including government stimulus packages. In premium western markets, higher freight rates improved the company’s local import parity pricing advantage. In the fourth quarter, the introduction of China’s dual control policy widened polyester margins.
IVL’s Fibers segment delivered a 37% increase in Core EBITDA of US$268 million as volumes rose 11%. Margins widened due to tighter markets and a favorable product mix, with setbacks coming from energy and commodity price increases, while the ongoing semiconductor shortage impacted the Mobility vertical.
IVL’s largest Combined PET segment posted a 39% increase in Core EBITDA to US$1,103 million in the context of strong demand and low inventories. The resetting of PET contracts in 2022 is expected to capture higher freight rates and the consequent beneficial impact on import parity. The segment is expected to enjoy improved margins in 2022.
Integrated Oxides & Derivatives (IOD) recorded a Core EBITDA of US$377 million, up 228% from a year earlier. With higher oil prices expected to continue into 2022, the segment will continue to benefit from shale gas economics, improving MEG spreads, and upside from Lake Charles (IVOL) ethylene cracker, which resumed operations in late 2021. The Oxiteno acquisition, expected to close in H1 2022, will bring complementary products, green energy innovation, and geographical diversification to the IOD segment, according to IVL.
At IVL’s annual Capital Markets Day on 10 February 2022, the company announced its three-year business plan to leverage its global footprint, ongoing transformation initiatives, and high levels of integration across the company’s three business segments to drive earnings growth, extract efficiencies, and lift productivity.
IVL said it will continue to invest in its platform, its people, and strengthen systems to unlock its full potential to contribute to EBITDA growth and deliver our aspirational 15%+ ROCE by 2024.
Project Olympus, the company’s efficiencies and business transformation project, is tracking ahead of 2023 budget, and the company raised its expectation to more than US$650 million in annual recurring EBITDA gains by 2024.
IVL also outlined its “Vision 2030” ambition to grow organically with sustainability as its priority, guided by its new purpose statement: Reimagining Chemistry Together to Create a Better World. Vision 2030 is designed to guide IVL’s journey towards “net zero.”
Under Vision 2030, IVL plans to invest in technology to capture carbon from its operations, increase renewable energy consumption, and phase out coal. It will invest more in PET recycling and introduce bio-based feedstock in about a third of its polyester-based value chain.
Source: indoramaventures.com
Kimberly-Clark acquires majority stake in reusable period and incontinence products provider Thinx
Kimberly-Clark Corporation has completed its acquisition of a majority stake in Thinx, Inc., a provider of reusable period and incontinence products. The company made an initial minority investment in Thinx in 2019.
Terms of the transaction were not disclosed.
“Our investment in the success of Thinx represents a compelling strategic fit as we build our portfolio of period and light bladder leakage solutions, and we are excited for the opportunity this expanded partnership will provide to both Kimberly-Clark and Thinx,” said Russ Torres, group president of Kimberly-Clark’s North American Consumer business. “The investment in Thinx paves the road for collaboration and allows us to work together to drive category growth with our retail partners while continuing to support Thinx in direct-to-consumer channels.”
Thinx continues to be a leader in the reusable period and incontinence underwear category. With the continued advancement of hybrid environments, more consumers are staying and working from home, and they are demonstrating increased awareness and consideration for the category, according to Kimberly-Clark. Market trends also confirm consumers are seeking these additional solutions for their period and bladder leak needs.
Source: kimberly-clark.com
Neenah announces 25M euro investment in meltblown line for its filtration manufacturing facility in Germany
Neenah, Inc., a global manufacturer of specialty materials for filtration media, specialty coatings, engineered materials, and imaging & packaging, announced a 25 million euro investment in new meltblown capacity in its German filtration facility. The new meltblown line is expected to be online in mid-2024.
Neenah is committed to accelerating growth in life science and industrial filtration markets, and this investment reflects that aim. Neenah’s portfolio of meltblown products is designed to promote higher filtration efficiency and lower energy usage, with the company’s electrostatically charged NeenahPure media solutions supporting HVAC, air pollution control, and air purification systems, delivering market leading efficiencies >99.9%.
“Clean air and water are critical to our communities and environment. Meltblown technology effectively removes harmful particles from the air we breathe and the water we drink. This new meltblown line intensifies our innovation efforts and allows us to continue to grow with our customers,” said president and CEO Julie Schertell.
Source: neenah.com
Bast Fibre Technologies completes acquisition of Georgia Pacific fiber manufacturing facility, eyes significant capacity increases
Bast Fibre Technologies Inc. (BFT), a manufacturer of premium natural fibers, has completed its purchase of Georgia-Pacific’s Lumberton Cellulose LLC. The Lumberton, North Carolina, site provides BFT with a highly automated state-of-the-art manufacturing facility with approximately 25 employees that will now operate under the new name, BFT Lumberton.
With this acquisition, BFT plans to significantly expand capacity to over 30,000 tonnes per year, establishing BFT Lumberton as one of the largest fully integrated natural fiber processing plants in North America, according to the company.
In addition to the planned capacity increase, the acquisition of the Lumberton facility diversifies BFT’s natural fiber offerings, allowing entry into complementary product categories for cosmetic cotton, filtration, hygiene, and other nonwoven applications.
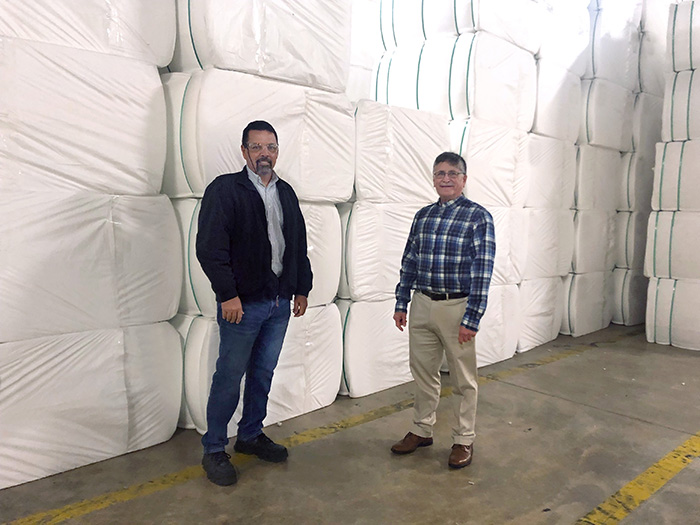
“As changes in consumer preferences and single-use plastics legislation drive demand for alternatives to synthetic fibers, consumer brand companies are seeking to manufacture products using fiber with minimal ecological impacts,” says BFT president, Jim Posa. “The BFT Lumberton plant will produce all-natural, clean, soft, compostable fibers that are capable of displacing synthetics fibers in many nonwoven and textile applications and will bring valuable cleantech sector jobs to the local community.”
Source: bastfibretech.com
Koshiro Kudo named president of Asahi Kasei
Asahi Kasei announced at the end of January 2022 a change in the company’s management. In line with this change, Asahi Kasei has appointed Koshiro Kudo to the role of president and representative director, with current president, Hideki Kobori, becoming chairman of the company. The change will become effective in April 2022.
Koshiro Kudo takes over as president with the company in a robust business setting, as results for the most recently reported quarter show earnings per share of 35.59 JPY (0.27 EUR) with full-year 2021 earnings per share of 23.93 JPY (0.18 EUR). Compared to the same period the previous year, Asahi Kasei achieved an increase in sales of 17.6% in the past quarter. Sales amounted to 643.70 billion JPY (4.86 billion EUR) compared to 547.30 billion JPY (4.17 billion EUR) during the same quarter the previous year. Asahi Kasei’s full-year forecast announced in November 2021 remains unchanged, with expected 2,453.0 billion JPY (18.72 billion EUR).
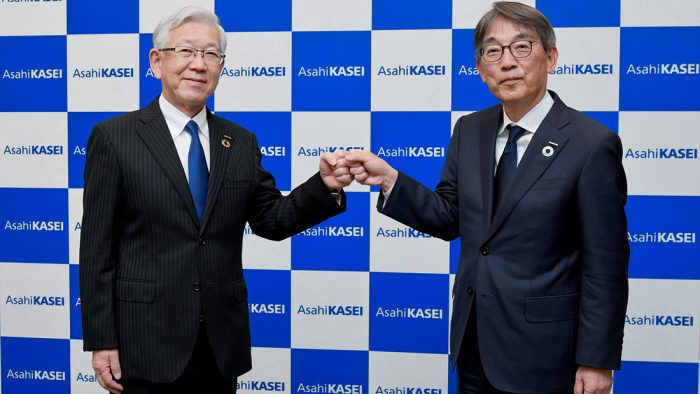
Koshiro Kudo is a graduate of Keio University in Tokyo in March 1982, and he began working at Asahi Kasei that same year. After holding various positions, Kudo became head of the ROICA business unit in May 2008, producing premium stretch fibers from elastic polyurethane filament. In 2017, he became president of Asahi Kasei’s Fibers & Textiles Strategic Business Unit (SBU), based in Osaka. Kudo has also served as president of the Performance Products SBU, with responsibility for engineered plastics, synthetic rubber, elastomers, as well as household and packaging materials. He was also involved in the establishment of a new department for mobility materials, launched in April 2020, to focus on products for the automotive sector.
During his presidency, Hideki Kobori expanded Asahi Kasei’s global presence. One key achievement was the establishment and development of Asahi Kasei’s Europe business in April 2016. He also oversaw business development activities, including capacity expansions for battery separators, filaments for airbags, synthetic rubber and virus filtration. This includes strategic positioning in the automotive and medical sectors, with acquisitions including Sage Automotive Interiors in the U.S., the Swedish sensor company, Senseair, as well as Veloxis Pharmaceuticals, Inc., a U.S.-based company focused on the commercialization of immunosuppression medications.
Source: asahi-kasei.com
Indorama takes 85% equity stake in UCY Polymers; sets sights on 1.12B annual increase in PET plastic bottle recycling in Czech Republic
Indorama Ventures Public Company Limited (IVL) completed a deal for an 85% equity stake in Czech Republic-based polyethylene terephthalate (PET) plastic recycler UCY Polymers CZ s.r.o. (UCY).
As a result of the investment, IVL said it will recycle about 1.12 billion additional post-consumer (PET) plastic bottles in the Czech Republic every year by 2025, increasing the total bottles recycled by UCY across the Czech Republic, Germany and Central Europe to 1.6 billion bottles per year.
UCY will work with IVL’s existing PET flake production facilities in the region. These provide the washed and shredded post-consumer bottles as PET flake feedstock to produce recycled PET resin that is suitable for food contact use. PET is fully recyclable and the most collected and recycled plastic packaging in Europe. Currently, UCY can produce 40,000 tonnes of recycled PET flake per year.

“We look forward to adding our robust supply of post-consumer bottles, well-established technology and proven management team to IVL,” said Maximilian Josef Söllner, CEO at UCY. “Expanding our capacity by 2025 means an extra 896 million more bottles will be recycled in our facilities compared with today.”
“IVL will use our know-how to grow capacity and recycle more and more bottles,” said D K Agarwal, CEO and CFO at IVL. “As part of our commitment to sustainability and the circular economy, we are building the recycling infrastructure needed to divert PET waste from the environment. By recycling post-consumer PET bottles into new bottles, we give waste an economic value. This drives improvements in waste collection systems, meaning less waste and a cleaner environment.”
IVL is investing $1.5 billion globally to expand recycling facilities and sustainable production, including boosting its recycling capacity to 750,000 tons per year by 2025.
Source: indoramaventures.com
INDA names Jen Greenamoyer as its new director of government affairs
INDA, The Association of the Nonwoven Fabrics Industry, has named Jennifer “Jen” Greenamoyer as its new director of government affairs with the aim of raising the association’s profile in Washington, D.C. She brings 25 years of experience at associations, the U.S. Environmental Protection Agency (EPA) and on Capitol Hill to the position.
Most recently, Greenamoyer served as senior government relations liaison and the principal lobbyist at the American Institute of Physics (AIP) for 15 years, where she represented the association to Congress and lobbied for appropriations. She has strong expertise in science policy and education that is expected to enhance her role as an information resource for INDA members, staff and others on government-related matters affecting the nonwovens industry.
At INDA, Greenamoyer will serve as the liaison between the nonwovens industry and government legislative and regulatory bodies by preparing formal submissions to the federal government articulating industry positions, and representing INDA on the Industry Trade Advisory Committee for Textiles and Apparel (ITAC 13), among other responsibilities.
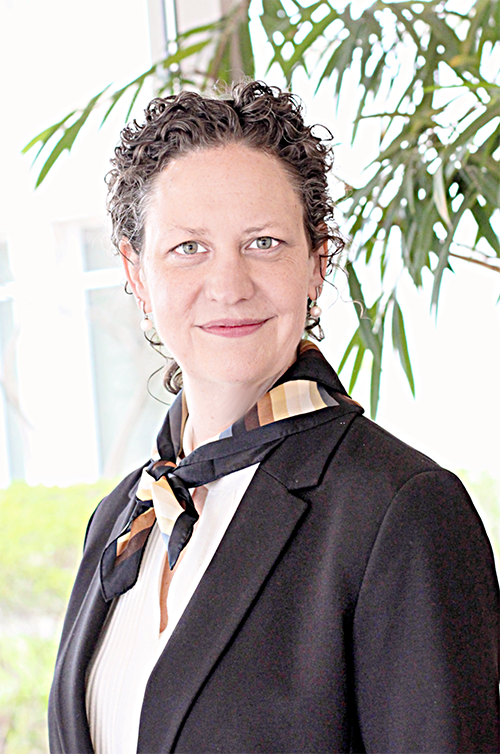
“With her excellent experience and capabilities, Jen will be a great asset to INDA’s members by advocating on issues that directly impact our members and raising INDA’s profile with policymakers and government and business organizations in Washington, D.C.,” said Dave Rousse, INDA president. “She will play a critical role in supporting INDA’s new strategic plan that includes advocating for the nonwovens industry in public policy forums and achieving industry relevance among key stakeholders.”
“I am excited about this new opportunity to join INDA to be part of bolder and more strategic advocacy efforts for the nonwovens industry,” Greenamoyer said.
Greenamoyer holds master’s degrees in Marine Affairs and Oceanography, both from the University of Rhode Island, and a Bachelor’s in degree Marine Science from Stockton College of New Jersey. She begins her role Feb. 22 and looks forward and will be meeting industry professionals at INDA’s upcoming IDEA and FiltXPO events, March 28-31, at the Miami Beach Convention Center. Greenamoyer succeeds Jessica Franken in this role.
Source: inda.org
Canalair names Gottfried Abrell, former CEO of Luwa, to management team
Canalair is happy to announce that Gottfried Abrell, former CEO of Luwa, has joined the management team of Canalair Service S.r.l. as chief business development officer. This follows the company’s expansion of R&D activities as part of the innovation district of Kilometro Rosso and further extends the company’s commitment to growth going forward.
With 29 years of experience in air engineering for textile and nonwoven applications, Abrell brings valuable inputs to the planned business expansion of Canalair. He has worked in several management positions in Germany, Switzerland, Singapore, Mexico and India. During the past 11 years he has served as CEO of the Luwa Group in Switzerland.
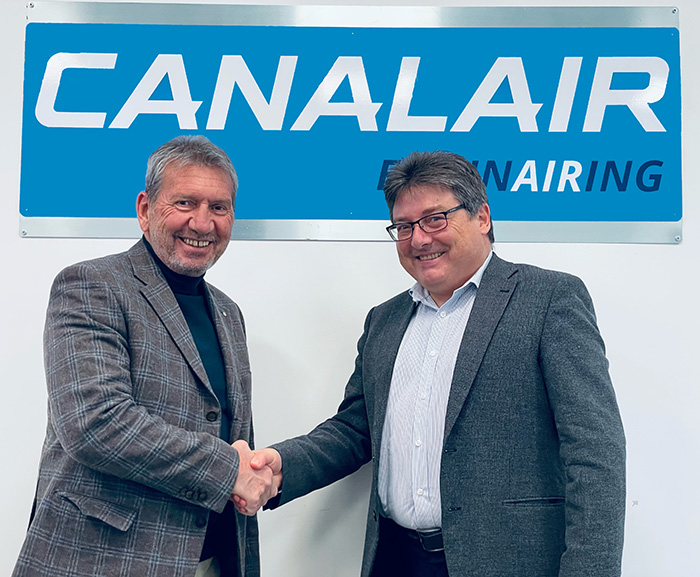
Maurizio Braga, global sales director and co-owner of Canalair said, “We are very proud to announce the joining of the new chief business development officer of Canalair, an important person for the future of our company. The entry of Mr. Abrell in the management team will help us through his experience and his knowledge of the air treatment market to achieve all the goals in the field of technological innovation, sustainability and digitalization. This is a great opportunity to grow all together.”
Canalair Service S.r.l has served the nonwovens and textiles industries for 30 years, providing process technologies in the areas of air conditioning/engineering and fire protection.
Source: canalair.com
Leigh Fibers to add thermal-bonded airlay line, targeting fiber development for non-automotive nonwoven applications
Leigh Fibers is currently installing a multi-million dollar thermal-bonded airlay line at its Wellford, South Carolina facility. The line is intended to open up new non-automotive markets for the company and its customers. Leigh Fibers plans to leverage the line to help expedite fiber development and foster a better understanding of the fiber’s value in a finished product. The line is currently being installed, with commercialization expected on April 22.
According to Daniel Mason, president of Leigh Fibers, the line will aid customers who are struggling to meet demand for nonwoven products due to limited installed capacity and staffing challenges. Also, the line is intended to support Leigh Fibers in R&D and validation of new fiber solutions.
As Leigh Fibers’ customers have been struggling with capacity issues for a variety of reason, Mason said this has impacted his company’s access to lines to support its own research on new fiber blends. By having its own in-house line, Mason said Leigh Fibers can now test and validate new fiber blends without having to go externally to run trials.
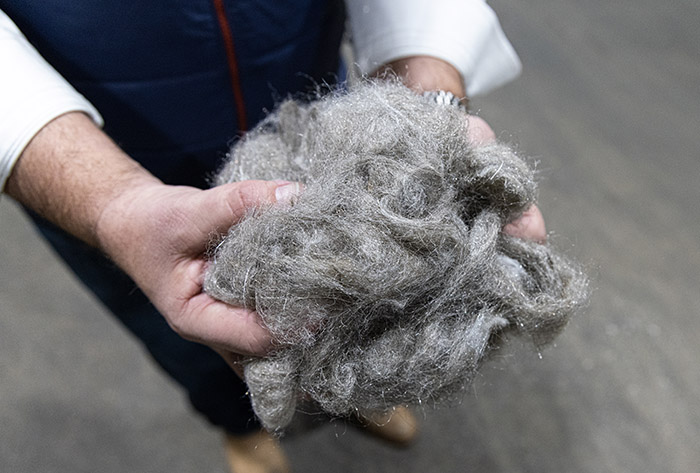
“We see that this line will allow us to do better product development on the fiber side of our business by allowing Leigh to get our engineered fiber blends into pads quickly with the goal of understanding the value-adding characteristics of these fiber blends,” said Mason. “With test data in hand we can then better communicate the value prop of the engineered blends to our customers/partners. In addition to this, we hope these efforts allow Leigh to develop new markets for recycled fibers – this will be good for everyone since so little textile waste is recycled today in the U.S.”
Leigh’s ultimate goal in introducing this new equipment, which is being recognized as part of the company’s 100-year anniversary, is to prove to long-time partners and prospective customers that the company is dedicated to the development of new processes that will benefit them for the next 100 years to come.
“We are exploring a wide range of markets that have shown interest in sustainable-based high-loft nonwovens that deliver acoustic and/or thermal properties,” said Mason. “We will be a unique high loft airlay manufacturer in that we are experts in sustainable/recycled fibers. The line is very versatile and can produce a wide range of GSM weights.”
“The line is designed to run any range of fibers from 100% synthetics to 100% natural fibers, but with our background in technical/value-adding fiber blends, we anticipate running a mix of fibers,” said Mason.
In announcing the new line, Mason said it was important to ensure the company’s existing partners understand that this new technology will not compete with them in the market, but rather support them in a tight labor and supply-chain environment. This is why Leigh Fibers has designated the line for R&D and validation of fibers for non-automotive nonwoven applications.
Leigh Fibers is an international manufacturer of engineered fiber solutions and is recognized as one of North America’s oldest family owned textile recycling and trading companies. Leigh’s expertise spans across several markets, including automotive, bedding, caskets, furniture, apparel, acoustic insulation, sporting equipment, specialty fibers, etc.
Source: leighfibers.com
Lenzing announces Young Scientist Award to recognize outstanding research in the field of fibers and textiles
The Lenzing Group, a leading provider of wood-based specialty fibers, will present the Young Scientist Award for outstanding research in the field of fibers and textiles for the first time in 2022. The award will be presented at The Dornbirn Global Fiber Congress in Dornbirn Austria, September 14 to 16, 2022.
Nominations are encouraged from bachelor’s and master’s degree students in the categories of fashion and the circular economy, textile recycling and the innovative use of bio-based fibers. Nominees will be evaluated by a jury of industry experts, including Karla Magruder (Founder of Acceleration Circularity), Friedericke von Wedel-Parlow (Beneficial Design Institute Berlin) and Dieter Eichinger (Head of Standardization and Innovation, Secretary- General of BISFA). The winning project will receive a prize of EUR 5,000. The aim of the program is to promote the students’ work and create a platform for networking within the textile and fiber industry.
“As one of the leading innovators in improving fibers and wovens for decades, Lenzing is best positioned to make a real difference and create a more sustainable future. Driving research and development forward and supporting young scientists in developing their ideas at all times is not just a matter that is close to our heart. We are convinced that innovation and technological progress are vital to our success in tackling the pressing environmental challenges we face,” said Robert van de Kerkhof, member of the managing board at Lenzing Group and president of the Austrian Fibers Institute.
The Austrian Fibers Institute is the organizer of the 61st Dornbirn Global Fiber Congress on a not-for-profit basis. The Austrian Fibers Institute, which is headquartered in Vienna, was founded in 1960 by fiber producers and the Austrian textile industry to promote the market launch of fibers and fiber products. The institute also offers opportunities to exchange information and experience relating to fibers and supports engagement with educational institutions. The GFC aims to encourage the international exchange of experience in close liaison with Brussels-based representative body.
Applicants for the Young Scientist Award can submit their work (final-year projects, papers, etc.) in English between February 01, 2022 and June 15, 2022 to YSA2022@lenzing.com.
Source: lenzing.com
BASF launches RegXcellence with an eye on helping the plastics and polymer value chain navigate regulatory and compliance issues
BASF launched a new service offering, RegXcellence, for its plastic additives customers, which provides targeted access to a range of global regulatory support. RegXcellence is designed to provide digital solutions and simplify regulatory issue management with advisory support in an environment where the regulatory landscape is constantly changing.
As this service expands, plastic additives customers will have access to a digital solution to access regulatory documents. A global community of regulatory experts also evaluates relevant environmental, health and safety data. These experts will be available to support customers from registration services to process and substance consulting. In addition, specific regulatory trainings are offered.
BASF already offers RegXcellence services to the customers of its fuel and lubricant solutions, plasticizers, pharma solutions and human nutrition businesses.
RegXcellence for plastic additives is part of BASF’s VALERAS plastic additive portfolio. With VALERAS, BASF aims to increase the sustainability of plastics along the entire polymer value chain with innovative solutions and offerings from its plastic additives business.
“As a leading global producer of plastic additives, we leverage our extensive experience in the plastic industry and strong knowledge of product stewardship and chemical legislation to stay ahead of the evolving regulatory trends,” said Dr. Thomas Kloster, president of Performance Chemicals for BASF. “We proactively support our customers to ensure responsible and appropriate use of our additive solutions. With the extension of the successful RegXcellence service to include plastic additives, we now enable our customers to benefit from our extensive regulatory service and expertise. Together, we can mitigate business risks, accelerate innovation, and achieve sustainable growth through regulatory compliance.”
Source: basf.com
HUGO BOSS, LYCRA make significant investments in HeiQ AeoniQ sustainable filament yarn technology
HUGO BOSS has committed a US$5 million equity investment in HeiQ AeoniQ LLC and an additional contingent US$4 million based on performance milestone arrangements. The LYCRA Company has also become the exclusive distributor for HeiQ AeoniQ yarn by making a significant, undisclosed investment and by committing to develop the technology for broad application in textiles.
As part of its “CLAIM 5” growth strategy, HUGO BOSS executed its first sustainability-linked investment for a US$5 million shareholding in HeiQ AeoniQ LLC, a fully owned subsidiary of London-listed HeiQ Plc. The HUGO BOSS investment is supplemented by an additional US$4M arrangement, which is subject to the achievement of agreed goals. The strategic partnership is expected to help HUGO BOSS meet its ambitious sustainability targets, which include the aim for climate neutrality within its own area of responsibility by 2030. Over the mid-to-long-term, HUGO BOSS is focused on the potential to materially complement and substitute polyester and nylon fibers with the cellulosic HeiQ AeoniQ fibers.
HeiQ AeoniQ (Aeon: striving for eternal circularity) is a continuous cellulosic filament yarn with the potential to compete with polyester and nylon fibers. According to HeiQ, it constitutes a revolutionary, first-to-market and scalable proprietary apparel technology, which will allow the manufacturing of a sustainable, cellulosic yarn designed for circularity and closed-loop recycling that could ultimately substitute for oil-based fibers.
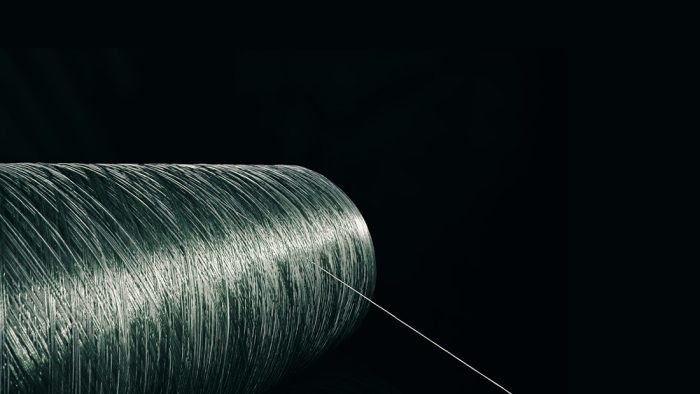
HeiQ AeoniQ yarns are made out of cellulosic biopolymers that during growth bind carbon from the atmosphere. HeiQ AeoniQ yarn is designed to substitute for existing oil-based filament yarns, such as environmentally persistent polyester and nylon, which constitute over 60% of global annual textile output of 111 million metric tons. The global polyester and nylon fiber market is worth an estimated US$135 billion USD with a CAGR of >3.5% over the next decade (Statista). For every ton of polyester & nylon substituted by HeiQ AeoniQ, potentially up to 5 tons of CO2 can be reduced, according to the company.
When compared to conventional polyester, nylon, cotton and conventional regenerated cellulosic products, the production of HeiQ AeoniQ yarns has the potential to transform the environmental impact of fiber production, as it is designed to be circular, uses 100% renewable energy for manufacturing, features a closed-loop recycling of more than 99.5% of productive factors, uses no toxic chemicals, and does not draw on arable land, pesticides or fertilizers for its feedstock.
The primary use of the raised proceeds would be to scale up and commercialize the HeiQ AeoniQ technology. HeiQ AeoniQ LLC will build its first commercial giga factory in Central Europe by end of 2024, and is currently scaling-up its pilot commercialization plant for fiber production, scheduled for Q2 2022.
Source: heiq.com
Klopman publishes latest Sustainability Report, touting recycled polyester fabrics made from 8.5M plastic bottles
Klopman, a European manufacturer of workwear fabrics, issued the sixth edition of its Sustainability Report highlighting several successes: over 8.5 million plastic bottles recycled into sustainable textiles, a total of over 3.5 million meters; a reduction in C02 emissions; and total savings of over 3,000,000 Kw/h of electricity and over 40,000 M3 of water.
In 2021, Klopman launched three new fabrics made from sustainable materials: Vitalys, a fabric made from wood pulp and cotton waste; Luminex C50 RPES, a high-visibility fabric made from recycled polyester; and Hydrogreen, a water-repellent treatment made without perfluorinated chemicals. The company has also launched the Zero Waste project to reduce waste and encourage correct waste disposal inside the plant.
Klopman also noted the achievment of the highest level of STeP by Oeko-Tex certification for its Jakarta plant, which guarantees the use of environmentally friendly technologies and products, efficient use of resources, and working conditions in line with the highest international standards. STeP certification, which stands for Sustainable Textile & Leather Production, is further evidence of Klopman’s ongoing commitment to sustainability and guarantees its customers the same standards of quality and social responsibility worldwide.
“Corporate Social Responsibility is in Klopman’s DNA, and we are very proud to be able to show the results we have achieved in a challenging global period that has presented us with limitations but also many opportunities that we have tried to make the most of,” said Amaury Sartorius, the company’s managing director. “The results summarized in our Sustainability Report indicate once more that we are going in the right direction and that our choices continue to bring concrete results both for our customers and the society around us. As European leaders in the sector, we cannot forget how important our impact can be not only for us but for society.”
Source: klopman.com
INDA announces IDEA trade show will shift from three-year to two-year cycle, with FiltXPO returning to 18 months
INDA, the Association of the Nonwoven Fabrics Industry, announced its IDEA (ideashow.org) trade show for the nonwovens & engineered fabrics industry will be held every two years instead of three starting in 2024.
The upcoming dates for IDEA under the new schedule will be March 28-31, 2022, as currently scheduled, and then April 23-25, 2024. Both will be held as live, in-person events at the Miami Beach Convention Center in Florida.
“INDA has three key reasons for making this change in event frequency,” said Dave Rousse, INDA’s president. “First, the nonwovens industry has been a vibrant, innovative sector with new products, processes and materials every year, so providing an opportunity to showcase more frequently these new developments better serves the industry. Second, one of the major nonwoven events in Asia has declared they will run each and every year, impacting the past three-year cycle of major shows in the nonwovens industry. Third, coming out of the COVID pandemic, market research predicts for the near future that regional events are expected to be better supported than global events.”
INDA expects the 2022 edition March 28-31 to attract several thousand senior-level buyers and attendees from over 60 countries and several hundred exhibitors from industry sectors, including absorbent hygiene, wipes, filtration, medical and surgical products, personal protective equipment, home and office furnishings, transportation, geosynthetics and building construction.
FiltXPO (filtxpo.com), INDA’s exposition and technical conference dedicated to the filtration and separation industry, will be co-located with IDEA in Miami Beach this March 29-31 to avoid conflicting with other filtration events that were originally planned in 2021. FiltXPO then returns to an 18-month schedule and will next take place October 10-12, 2023, at Navy Pier, Chicago, Ill.
Source: inda.org
Spinnova, adidas unveil first commercial product made of SPINNOVA sustainable fiber
Spinnova and adidas announced the release of TERREX HS[1], the first adidas product made with the sustainable SPINNOVA fiber. Composed of a minimum of 25% wood-based fibers and organic cotton, the adidas TERREX HS1 is a mid-layer knit for hikers. Working with the material’s natural color, the hoodie is made without dyeing or bleaching chemicals.
SPINNOVA is a circular textile fiber made of sustainably sourced wood, without harmful chemicals. It produces 65% less CO2 emissions and uses 99% less water than cotton production and contains zero microplastics, according to Spinnova.
Spinnova’s first commercial-scale factory is expected to be completed in Finland at the end of this year. Spinnova, and its Woodspin joint venture partner Suzano, have a scaling target of a million tonnes of global fiber production capacity annually within the next 10-12 years.
A limited number of the TERREX HS1 will be made commercially available on adidas.com and in other selected retail outlets, with global reach from July, marking a significant milestone in Spinnova’s market entry.
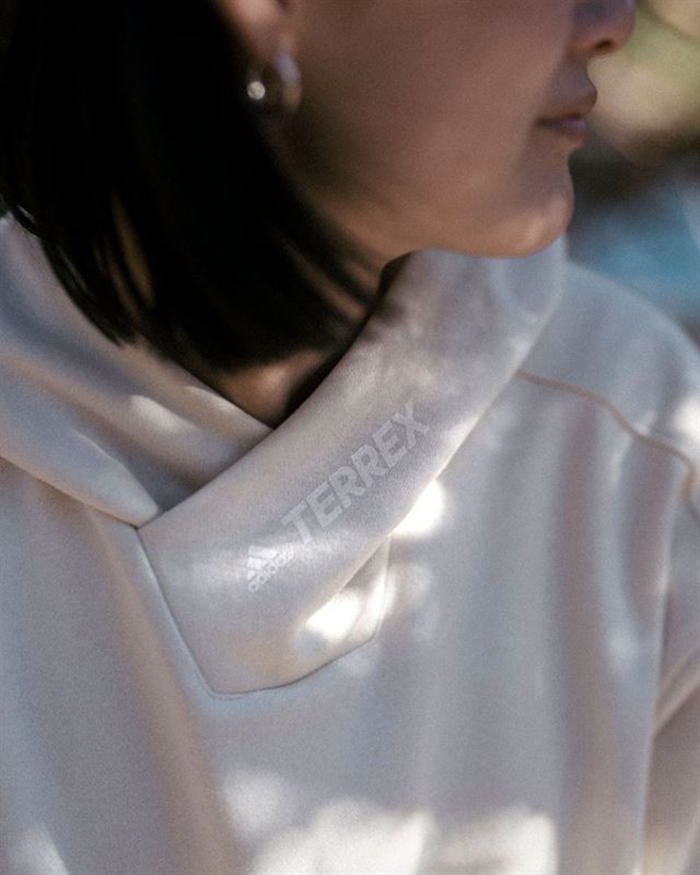
As part of ensuring access to future volumes of SPINNOVA, adidas became a cornerstone investor in Spinnova’s initial public offering last June.
SPINNOVA fibers are expected to allow adidas to make high-performance apparel while reducing the CO2 emissions, water consumption and waste usually required to create such products. The TERREX HS1 is described as a major step on adidas’s journey to create nine out of 10 articles with a sustainable technology, materials, design or manufacturing method by 2025.
Although significant in terms of Spinnova’s commercialization, this launch is not expected to have a material impact on Spinnova’s financial performance in 2022, when the majority of revenues are expected to come from technology sales to its joint ventures, according to the company.
Source: spinnova.com
BB Engineering GmbH delivers melt filter for PET recycling to Indorama Polyester
BB Engineering GmbH (Germany) reports the deliver of a melt filter for recycling PET flakes to polyester manufacturer Indorama Polyester Industries (Thailand). Indorama will use the type NSF38 filter in its recently assembled recycling system to produce rPET granulate from flake PET bottle waste.
The NSF38 filter enables continual filtering – in other words, the system switches from one filter to the other during the process without the need for conversion shut-downs. The filter allows the processing of consumer waste for example, in the form of shredded PET bottles into new, high-quality rPET granulate. This granulate is subsequently processed into manmade fibers in spinning systems.
The NSF38 is a switchable filter with a filter surface area of approx. 16 m2 on each side, with throughputs of between 1,000 and 1,900 kg/h. The filter inserts each contain 19 pleated filter candles (60 x 1,000mm Ø). The filter medium comprises a sintered metal fiber nonwoven with a filtration fineness of 25 μm. This ensures that the melt remains free of contaminants and gel particles, which in turn enables the production of high-quality end products, according to BB Engineering.
Source: bbengrs.com
Mitsui Chemicals expands meltblown capacity; targets demand for industrial-use applications
Mitsui Chemicals announced plans to expand its production facilities for meltblown nonwovens at its subsidiary Sunrex Industry Co. Ltd. The move comes in an effort to respond to growing demand for industrial-use meltblown nonwovens, and it will drive a 30% increase in the company’s overall production capacity for meltblown nonwovens.
As part of its new VISION 2030 Long-Term Business Plan, Mitsui Chemicals will be positioning nonwovens as a growth business under its Life & Healthcare Solutions unit. Mitsui Chemicals is looking to supply nonwovens not only as sanitary materials for applications such as disposable diapers, but also as industrial materials for a variety of applications.
Products targeted toward this end will include TAFNEL, which can be used as an oil-adsorbing material, a structural material for automotive seats and a civil engineering material; SYNTEX, a structural material for filters and masks; and other such high-quality nonwovens. In particular, SYNTEX nano – a brand consisting of superfine fibers – is expected to meet with use in products such as highly advanced precision filters.
Mitsui Chemicals plans to further bolster and grow its nonwovens business going forward, with the newly announced facility expansion coming as one such move.
Source: jp.mitsuichemicals.com
Kelheim Fibres recognized in ‘Cellulose Fibre Innovation of the Year’ program
Specialty viscose fiber manufacturer, Kelheim Fibres, was awarded third place in the “Cellulose Fibre Innovation of the Year,” awarded during the International Conference on Cellulose Fibres 2022, held Feb. 2-3 in Cologne, Germany. The award was issued based on the concept for sustainable menstrual underwear made from Kelheim’s functionalized specialty fibers.
Natalie Wunder, who presented the concept from Kelheim at the International Conference on Cellulose Fibres, said, “We have been able to use our experience as a long-established supplier for the tampon industry to develop further sustainable solutions in the feminine hygiene sector, in this case reusable menstrual underwear. As an innovation pioneer, we are thus helping to break the taboos that surround the topic of menstruation. We offer women the choice between different environmentally friendly products which also offer high levels of performance – depending on what fits their lifestyle.”
For the next step, the commercialization of the concept, Dr. Marina Crnoja-Cosic, director of new business development at Kelheim Fibres, said, “We want to bring partners from the entire value chain together. By bringing in our joint expertise, we can significantly accelerate the path from idea to finished product in the market. At the same time, through open dialogue, we ensure that the concept works seamlessly from fiber through processing to the final product.”
Source: kelheim-fibres.com
German Institutes of Textile and Fibre Research Denkendorf wins 2022 Cellulose Fibre Innovation Award
With research results on the production of carbon fibers from wood, the German Institutes of Textile and Fibre Research Denkendorf (DITF) earned first prize in the “Cellulose Fibre Innovation of the Year,” awarded during the International Conference on Cellulose Fibres 2022, held 2 to 3 February in Cologne, Germany.
For the second time, the nova Institute for Ecology and Innovation honored outstanding scientific research that provides sustainable solutions for the cellulose fiber value chain at the “International Conference on Cellulose Fibres 2022.” With the topic “Carbon Fibres from Wood,” the DITF Denkendorf presented its solution for resource-saving alternatives to fossil-based fibers.
The Competence Centre Biopolymer Materials at DITF Denkendorf received first place with its presentation of carbon fibers, which are obtained from the raw material wood in a novel and sustainable process. The HighPerCellCarbon technology describes a patented process that has been further developed under the leadership of Dr. Frank Hermanutz. As a result, carbon fibers based on biopolymers can be produced in a sustainable and particularly environmentally friendly process.
The HighPerCellCarbon process involves the wet spinning of cellulose fibers using ionic liquids (IL) as direct solvents. The filament spinning process is the central technical part. It takes place in an environmentally friendly and closed system where the solvent (IL) is completely recycled. The cellulose fibers produced in this way are converted directly into carbon fibers in a further development step by a low-pressure stabilization process, followed by a suitable carbonization process. No waste gases or toxic by-products are produced during the entire process sequence.
The HighPerCellCarbon process is convincing in terms of sustainability in several respects: 1. in addition to the recyclability of the solvent used, the use of wood as a raw material in particular represents a natural and potentially sustainable source; 2. petroleum-based raw materials, which are usually used in the industrial production of carbon fibers, are substituted by renewable biopolymers.
Carbon fibres are used in many lightweight construction applications. Global demand has been growing for years. An environmentally friendly production process like HighPerCellCarbon is elementary for the sustainable management of an important industrial sector, according to DITF.
Source: ditf.de
Essity acquires wiping and cleaning company
Hygiene and health company, Essity, has acquired the U.S. professional wiping and cleaning company Legacy Converting, Inc. The company offers products within the categories of sanitizing and disinfecting wet-wipes, chemical-ready wipes and dry wipes. The purchase price amounts to USD 40M (approximately SEK 370M) with a potential additional earnout amount of USD 10M (approximately SEK 90M) on a cash and debt-free basis. Essity is the world’s largest supplier of products and services in the market for professional hygiene with its leading Tork brand.
Legacy Converting was founded in 2004 and manufactures the Everwipe brand of roll and folded wipes in a variety of formats, including pop-up canister, bucket and resealable packs. Customers are mainly found in the Industrial and Office Supply, Public Interest, Commercial and Healthcare market segments. Legacy Converting is located in New Jersey.
For the first nine months of 2021, Legacy Converting reported net sales of USD 15.1M (SEK 140M) with an adjusted EBITDA of USD 2.5M (SEK 24M), an adjusted EBITA of USD 1.8M (SEK 16M), equivalent to an adjusted EBITA margin of 11.7%. Sales growth for the first nine months of 2021 amounted to -49%, following extraordinary sales growth in 2020 as a result of COVID-19-driven demand. In 2020, the company reported net sales of USD 39M (SEK 362M), an adjusted EBITDA of USD 12.1M (SEK 112M) and adjusted EBITA of USD 11.8M (SEK 109M) equivalent to an adjusted EBITA margin of 30%. Sales growth in 2020 amounted to 183%.
“As a leading global hygiene and health company, we are committed to offering innovative sustainable hygiene products and services. With the acquisition of Legacy Converting, we will expand our wiping and cleaning product offering and further strengthen our presence in key customer segments in the North American market,” says Don Lewis, president of the Professional Hygiene unit at Essity.
Essity’s Professional Hygiene business comprises complete hygiene solutions, including toilet paper, paper hand towels, napkins, hand soap, hand lotion, hand sanitizers, dispensers, wiping and cleaning products as well as service and maintenance under the globally leading Tork brand. Essity also offers digital solutions, such as Internet of Things sensor technology, enabling data-driven cleaning. Customers consist of companies and office buildings, universities, healthcare facilities, industries, restaurants, hotels, stadiums and other public venues. Distribution channels for the products consist of distributors and online.
Source: essity.com
PFNonwovens, Smart Plastic Technologies enter development agreement around PP, PE bio-assimilation technology
PFNonwovens and Smart Plastic Technologies have signed an exclusive joint development agreement for the use of Smart Plastic’s patent-pending SPTek ECLIPSE technology in PFNonwovens’ hygiene and medical nonwoven products.
Smart Plastic’s SPTek ECLIPSE enables the bio-assimilation of polypropylene and polyethylene polymers at the end of a product’s guaranteed life span in terrestrial, marine, and landfill environments. The ECLIPSE bio-assimilation technology steadily reduces and modifies the polymer chains to enable the assimilation of these molecules by microorganisms, transforming the material into biomass, CO2, and water. The technology is FDA approved, 100% recyclable, and has already been commercialized by Smart Plastic Technologies in various industries.
Tonny de Beer, chief product, technology and sustainability officer for PFNonwovens said, “We are very excited for this joint development partnership with Smart Plastic Technologies. Our initial work together has already shown that we can use the ECLIPSE bio-assimilation technology on pilot-scale equipment. Now, our focus is to optimize the formulation for nonwovens to ensure performance and meet end-of-life goals.”
Jay Tapp, president & COO of Smart Plastic, added, “Smart Plastic and PFNonwovens are aligned on developing environmentally-responsible solutions as we transition to a more sustainable economy. SPTek ECLIPSE bio-assimilation is a proven technology that has been used commercially across several industries both in the USA and around the world to significantly reduce the impact plastic has on the environment. Our strategic partnership with PFNonwovens represents an important step in Smart Plastic’s mission to reduce plastic waste and help prevent further damage to the environment.”
Source: pfnonwovens.com
Huntsman Textile Effects employs RO filtration system to save 76 kiloliters of water per day at Baroda, India facility
Huntsman Textile Effects, a global leader environmentally sustainable dyes, chemicals, and digital inks, has successfully implemented a water conservation process to improve water efficiency and reduce net water usage at its Baroda facility, which is located in the western region of India. The initiative undertaken at the plant aims to save around 76 kiloliters of reverse-osmosis water per day by modifying the phase sequence in the pH measurement program.
Water is used extensively throughout textile processing operations. The amount of water used varies widely in the industry, depending on specific processes operated at the plant, equipment used, and policies concerning water use. This conservation project at the Baroda Plant will have a potential savings of Rs 10 crore, or US$146,000 a year for the organization.
“At Huntsman, we recognize the important role we play in creating a more sustainable future and are committed to the well-being of the communities where we operate, and the protection of the environment. We are continually looking for ways to improve the environmental footprint of our manufacturing sites and have been implementing numerous projects in recent years to reduce our water usage,” said Mark Devaney, vice president of Manufacturing and Operations Excellence at Huntsman Textile Effects.
“The team has done a detailed assessment of the pH analysis process in dye vessels, mapping the existing water usage and potential conservation method. After a brief study and several brainstorming sessions, we were able to adjust the phase sequence, resulting in conservation of reverse osmosis water by almost 76 kiloliters of water per day,” said Kavishwar Kalambe, site director for Huntsman Textile Effects. “This project directly contributes to Huntsman’s Horizon 2025 goals to reduce net water usage at facilities in water-stressed regions.”
Source: huntsman.com
Stoll offers next series of online courses for k.innovation Create Design
Stoll is slated to continue its online course series for k.innovation Create Design, its new software for digital knitwear development. Dates for the trainings are:
- March 8 and 9 (February 8 application deadline)
- April 27 and 28 (March 30 application deadline)
- July 5 and 6 (June 7 application deadline)
The k.innovation Create Design software combines knitwear with 3D product development and knitting production to increase efficiency for the flat knitting industry. The online courses explain these features and show how they can be used. The target groups are primarily knitwear designers and creatives.
“The digital transformation is indispensable for the future,” said Vasilios Fasois, founder of AthensKnitLab. “Small high-end productions, bespoke knitwear and digital patterns will reduce lead times and make knitting a part of the digital ecosystem of the future. Sustainable production and reduced waste are the added value of this workflow. This software bridges the generation gap. It gives designers and technicians skills to enter the market of the future.”
Registration can be completed by emailing training@stoll.com
Source: karlmayer.com
Sam’s Club and Huggies partner to donate up to one million diapers
For each pack of Huggies purchased at Sam’s Club during the month of February, Huggies will donate a day’s worth of diapers to the National Diaper Bank Network, up to one million diapers total. The National Diaper Bank Network is a national nonprofit dedicated to providing basic necessities required to build the strong foundations for children, families and individuals.
“Working to help end diaper need and raise awareness of this critical issue in America is something incredibly important to the Huggies brand,” said Robert Raines, vice president of Huggies North America. “We’ve been a long-time partner of the National Diaper Bank Network, and together with the support of Sam’s Club, we’ll be able to help thousands of families across America and help babies thrive.”
The National Diaper Bank Network has over 225 member diaper banks across the United States. Since 2011, Huggies has donated more than 300 million diapers and wipes to the National Diaper Bank Network.
Sources: huggies.com | samsclub.com | nationaldiaperbanknetwork.com
Hologenix’s Celliant pure white infrared fiber technology earns Top Ten in ISPO Textrends Fall/Winter 2023/24
Materials science leader Hologenix announced its newest innovation – pure white Celliant – is a Top Ten winner in the Fibers & Insulation Category of ISPO Textrends Fall/Winter 2023/24. Twice a year, ISPO recognizes innovative fabrics and components that are used to manufacture sports apparel. It’s no surprise that this innovation, whereby Celliant infrared technology can be embedded in fibers and for those fibers to be pure white, has achieved this honor. Pure white expands the potential applications of Celliant to crisp white performance and athleisure apparel, athletic uniforms and jerseys, towels, bedding, baby clothes, medical apparel, etc., while maintaining its well-known wellness benefits. Pure white is the foundation that makes delicate pastel fabrics, as well as any color, possible.
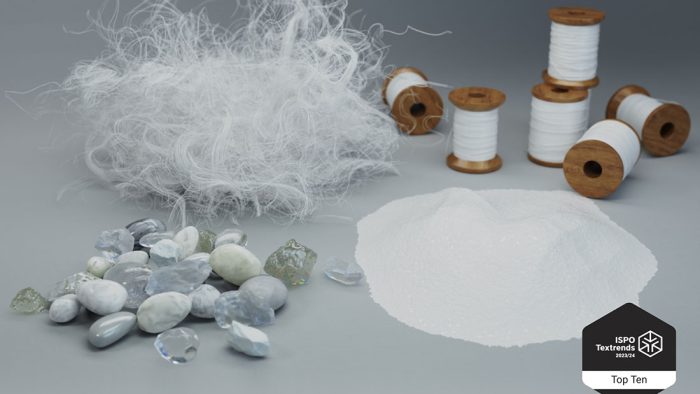
Pure white Celliant still captures and converts body heat into infrared energy, increasing local circulation, aiding in temperature regulation and promoting stronger performance, faster recovery and better sleep. Pure white Celliant is also still made from ethically sourced minerals from the earth and is available in nylon, polyester and recycled polyester fibers, while retaining the natural characteristics of the polymer.
This award follows on the heels of the 2022/23 ISPO Textrends Awards finalist selection of Celliant viscose in the Fibers and Insulations category, which features Celliant embedded into plant-based fibers. “We are honored to achieve this recognition from ISPO for our pure white CELLIANT,” said Courtney OKeefe, chief supply chain officer for Hologenix. “This new formulation took years of work to achieve and is a testament to the dedication and talent of our global research team. We are also very proud to be able to state that we now have two ISPO-recognized fibers.”
Source: celliant.com
Zünd, Airborne sign distribution agreement
Swiss cutting system manufacturer Zünd Systemtechnik and Dutch composite automation company Airborne have expanded their collaboration, signing a new distribution agreement to jointly sell and support digital production solutions for automated processing of composite materials.
Both companies are technology leaders offering solutions for composites manufacturing and processing – Zünd develops and manufactures digital flatbed cutting systems capable of processing reinforced fiber materials such as CFRP or GRP. Airborne, based in Den Haag in the Netherlands, provides fully integrated automation solutions for composites processing.
The goal of this partnership is to make it easier for customers to access digital cutting and automation solutions. The partnership provides a full portfolio of automated cutting, preforming, offloading, and sorting technology.
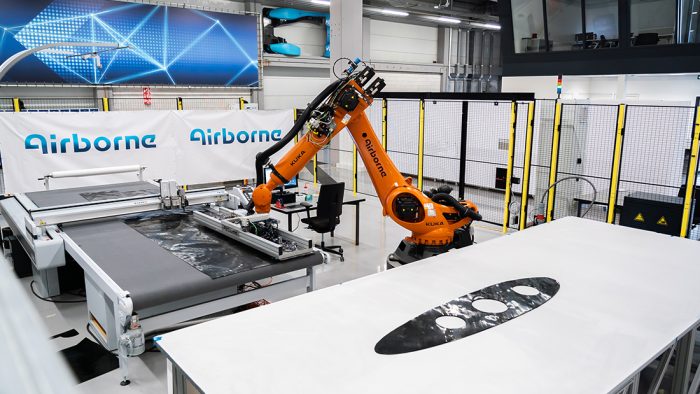
Airborne’s automated kitting solutions reduce operating costs by maximizing material yield through optimized nesting. At the same time, they resolve the challenges inherent in sorting and grouping cut parts from complex nested layouts into laminate-ready kits with minimal operator intervention. Airborne offers a portfolio of solutions tailored to meet individual customer needs, from affordable, entry-level semi-automated products to fully integrated high-productivity systems. All systems are “plug and play” and require no additional special programming. Airborne’s software generates the required robotics code directly from information derived from the nesting data and permits static or dynamic nesting and a sorting solutions that adapts “on the fly”.
Zünd has been designing, manufacturing, and marketing digital cutting systems for more than 30 years. Zünd’s high-performance modular cutters are in use all over the world. The Swiss family owned company, now in its second generation, has established a global network of Zünd sales and service organizations under the leadership of Oliver Zünd. “This is a situation where two strong partners complement each other in much the same way as in strong partnerships we have established in other industries. It is a continuation of a long-standing company strategy. Airborne has excellent know-how in developing and manufacturing automated solutions for processing composites. Together we can offer our customers state-of-the-art technology and provide a technological answer to the growing demand for high-performance, innovative production systems in the composites market,” he said.
Joe Summers, commercial director for Airborne, said, “Our partnership with Zünd brings a great deal of added value to our customers. Zünd shares our goal of creating greater cutting-room productivity. The Zünd cutter is key to converting materials with the greatest possible efficiency and maximum material usage.”