In the dynamic and global textile fiber industry with its various manufacturing processes and end-uses, news and information is breaking on a daily basis. International Fiber Journal is tracking stories relevant to our industry from manmade to natural to bio-based fibers, innovations in nonwoven, woven, braided and technical textiles, technologies for additives, bonding, coatings and polymers, and applications from apparel to hygiene to transportation, and more. Here we will post news stories relevant to textile fibers and their downstream applications on an ongoing basis. Please check back for regular updates. If you have news that you feel should be added to this summary report, please email it to Ken Norberg at ken@ifj.com.
Most recent update: June 30, 2022
LYCRA has new ownership
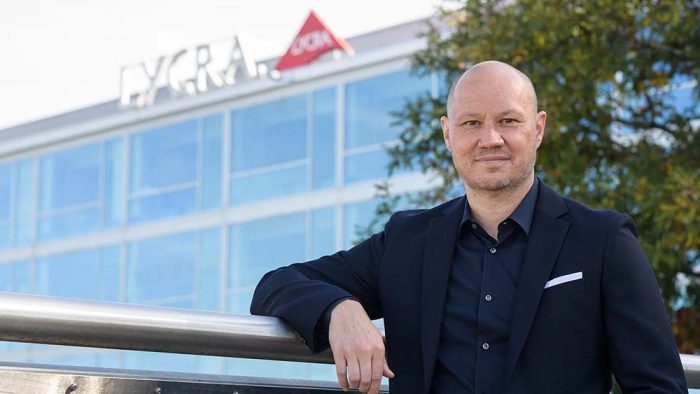
The LYCRA Company, a global leader in developing innovative fiber and technology solutions for the apparel and personal care industries, announced that a group of financial institutions, comprising Lindeman Asia, Lindeman Partners Asset Management, Tor Investment Management, and China Everbright Limited (“New Shareholders”), have gained full equity control of the Company.
The change of equity control follows the conclusion of the receivership process that started in February when the New Shareholders initiated an enforcement action against Ruyi Textile and Fashion International Group Limited, the former parent of The LYCRA Company, for loan defaults associated with its purchase of The LYCRA Company in January 2019.
The LYCRA Company has grown into one of the most powerful global franchises in the textile industry with its world-class brands, including LYCRA®, COOLMAX®, and THERMOLITE®, unique marketing services, and wide network of partners across the global value chain. In addition, The LYCRA Company’s diverse and broad innovation capabilities and robust intellectual property estate of over 800 patents have helped it build long-standing strategic relationships with most leading producers, brands, and retailers.
Source: thelycracompany.com
Lanxess adds new sustainable variants to Tepex
Specialty chemicals company Lanxess in Germany has added new sustainable product variants to its Tepex thermoplastic composites range, including the launch of a fully bio-based composite material based on flax and polylactic acid.
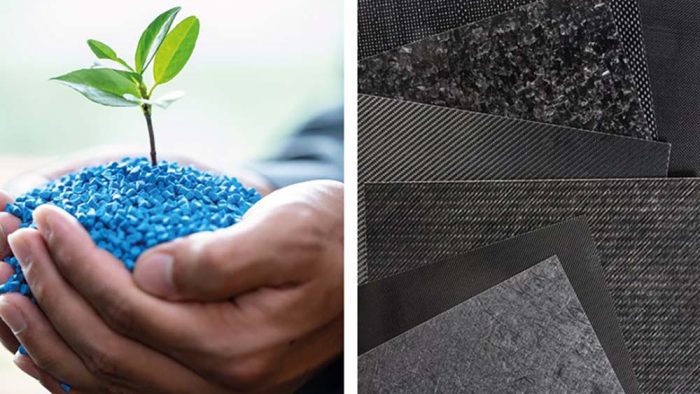
Lanxess said the development is about to be completed on a matrix plastic based on polyamide 6 (PA6) for Tepex dynalite. The material, produced from “green” cyclohexane, is comprised of more than 80% sustainable raw materials, meeting the requirements Lanxess has set for its Scopeblue range. When the matrix for the new Tepex dynalite material is reinforced with continuous fiber fabrics, the resulting semi-finished products are said to exhibit the same optimized properties as comparable, equivalent products that are purely fossil-based. The semi-finished products are suitable for applications in structural lightweight design that are typical for Tepex dynalite — such as front-end carriers, seat shells or battery consoles.
Source: lanxess.com
Trützschler partners with Texnology
Trützschler Nonwovens & Man-Made Fibers GmbH has embarked on a joint venture with Italian textile machinery manufacturer Texnology S.r.l. to offer complete production lines for needlepunched nonwovens under a new brand called T-SUPREMA.
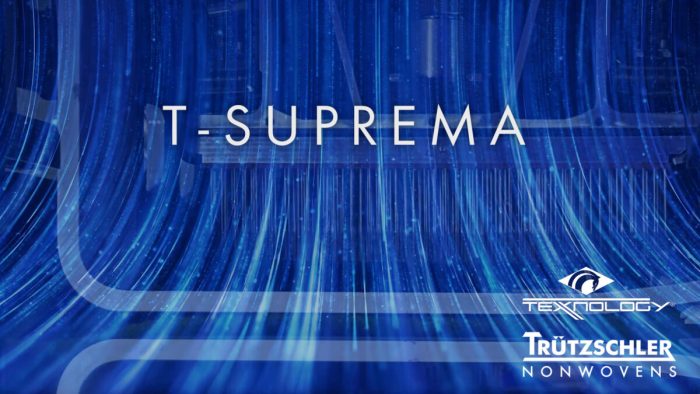
Web bonding with steel needles represents the largest production process in the drylaid nonwovens segment. The areas of application are predominantly of a technical nature, with the largest applications being durable geotextiles, automotive textiles and filter media.
The high adaptability of the needling and finishing processes as well as the broad material base result in a large number of different end products. Needle-punching is suitable for a wide range of manmade and natural fibers including mineral and high-performance fibers.
Trützschler Nonwovens is contributing years of experience in fiber preparation and web forming to the venture, while Texnology will mainly be responsible for the needlepunching process.
Source: truetzschler.com
Huntsman Textile Effects Introduces New PFC-free Durable Water Repellent in Performance Breakthrough

Huntsman Textile Effects has released PHOBOTEX® R-ACE, a breakthrough PFC-free durable water repellent (DWR) that makes it possible for mills and brands to deliver high-performance outdoor and extreme sports apparel and everyday wear while meeting stringent environmental standards and optimizing production flow.
PHOBOTEX® R-ACE delivers excellent water repellence on all types of fibers. In addition to its outstanding performance on synthetic fibers and blends, PHOBOTEX® R-ACE offers excellent compatibility with resin finishing to ensure even application with unmatchable performance on cellulosic fibers. It offers outstanding rain and splash protection for garments that are water repellent and windproof, even under the toughest conditions. Additionally, it repels everyday stains, such as mud, coffee, ketchup and juice, so that garments stay cleaner for longer. Textiles treated with PHOBOTEX® R-ACE are breathable, retain their soft handle and continue to look good and perform well through repeated laundering and drying.
The robust chemistry of PHOBOTEX® R-ACE achieves high repellency with significantly less chemicals added on to the fabric as compared to the typical PFC-free DWRs in the market. This helps mills minimize unwanted consequences like chalk marks, seam slippage issues and harsh handle. The breakthrough DWR also offers best-in-class runability, for faster trouble-free production and good reproducibility. Its excellent compatibility with resin finishing ensures even application with unmatchable performance on cellulosic fibers.
Source: www.huntsman.com
Kraig Biocraft Laboratories takes next step in launching Spydasilk™ apparel brand
Kraig Biocraft Laboratories, Inc., the biotechnology company focused on the development and commercialization of spider silk, announced that, in collaboration with its joint venture partner, Kings Group, the Company has selected a high-quality garment manufacturer to produce Spydasilk’s™ first apparel line.
Over the course of multiple meetings between Kraig Labs, Kings Group, and the garment manufacturer, conducted while the Company’s COO was in Vietnam this month, the Company finalized its manufacturer choice for the first apparel launch under the Spydasilk™ brand.
The manufacturer selected has demonstrated its capacity and technical ability to deliver on Spydasilk’s vision for apparel that blends performance and elegance with its exclusive spider silk materials. With more than 20 years in business and its strong ties to Vietnam’s entire textile supply chain, this producer can leverage the capabilities of the best mills to bring the Spydasilk brand to life.
In partnership with Kings Group, the Company has already delivered its recombinant spider silk yarn and a non-spider silk fabric swatch for use in developing a brand new fabric built upon the performance and feel of the Company’s spider silk.
Source: www.KraigLabs.com
Renewcell and HeiQ partner up to replace polyester
The ambition to replace environmentally polluting polyester in textiles has led to Renewcell AB of Sweden and Swiss company HeiQ to form a strategic partnership to manufacture circular HeiQ AeoniQ cellulose filament yarn from Circulose® pulp supplied by Renewcell. This partnership enables the incorporation of recycled raw materials in the most modern and environmentally friendly yarn production process that facilitates 100% circularity in the textile industry.
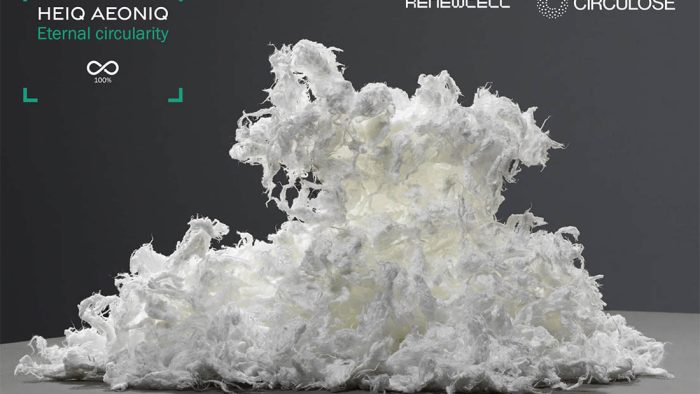
Capitalizing on their shared vision of a circular and bio-based textile industry, HeiQ and Renewcell have joined forces to commercialize 100% circular and biobased high-tenacity filament yarns as a viable replacement for fossil-based fibers like nylon and polyester at scale. Promising results in initial tests using Circulose® as a feedstock for production of HeiQ AeoniQ yarn create an opportunity for collaboration between the partners in their effort to lead the current textile industry transformation, positioning both companies and Europe as a pioneer region incorporating recycled raw materials in the most modern and environmentally friendly yarn production processes that allow true circularity in the textile industry.
Circulose® is a branded dissolving pulp product that Renewcell makes from 100% textile waste, such as worn-out jeans and production scraps. Dissolving pulp cellulose is what the textile industry uses to make viscose, lyocell, modal, acetate other types of regenerated fibers (also called ‘manmade cellulosic fibers’). The only difference with Circulose® is that it’s made from textile waste instead of wood. Cellulose is the most abundant organic polymer in the world. It’s what makes up the cell walls of most plants and trees. The purest cellulose found in nature is cotton.
HeiQ AeoniQ yarns are made out of cellulosic biopolymers that during growth bind carbon from the atmosphere while generating oxygen. This high-performance yarn is positioned to potentially substitute synthetic filament yarns which constitute over 60% of global annual textile output of 108 million metric tons. Further, when compared to conventional cellulosic products, HeiQ AeoniQ yarns do not draw on arable land, pesticides or fertilizer in their production. HeiQ AeoniQ yarns are designed for cradle-to-cradle circularity and can be recycled repeatedly while maintaining consistent fiber quality. The manufacturing process is expected to consume 99% less water than cotton yarns and HeiQ AeoniQ is designed to offer comparable performance properties to polyester, nylon and conventional regenerated cellulose yarns.
Source: www.renewcell.com
Wilson College of Textiles, Baldwin, Partner for Sustainable Finishing
Zeis Textiles Extension (ZTE) at North Carolina State University’s Wilson College of Textiles is announced its new working relationship with Baldwin Technology Co. Inc., utilizing its precision spray technology for chemical applications, TexCoat G4™, in the dyeing and finishing lab. This mutually beneficial relationship will enhance sustainability in the textile industry by reducing energy, water, chemicals and processing time with innovative spray technology.
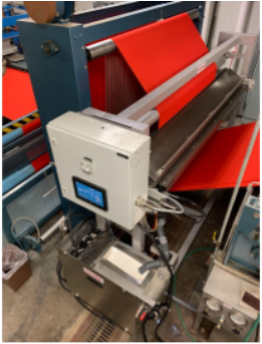
In addition to equipment partnerships such as this, companies within the textile industry can partner with ZTE to utilize the pilot lab for the opportunity to test new processes and products at an industry scale, exposing them to new technologies and possibilities without interrupting their manufacturing timelines. The labs within ZTE employ student workers and are available for use in their capstone and research projects.
Non-contact precision spray technology such as in the TexCoatG4™ allows for even application of a wide range of low-viscosity water-based chemicals to one or both sides of the fabric. Compared to traditional pad applications, the system enhances productivity, efficiency and sustainability by:
- Reducing water use by up to 50%.
- Reducing drying time and energy up to 50%.
- Recycling 100% of chemistry used.
- Reducing downtime for changing or cleaning baths between fabrics.
- Reducing water and chemical waste.
This partnership promotes Baldwin Technology and keeps the Wilson College at the cutting edge of advancements in the textile industry, allowing both students and companies to gain access to this eco-friendly finishing equipment.
Source: baldwintech.com
Archroma and Baldwin to collaborate on finishing
Archroma, a global leader in specialty chemicals towards sustainable solutions, and Baldwin, a leading global manufacturer and supplier of precision spray systems and technology for sustainable textile manufacturing, announce a new collaboration to optimize performance and resource saving in the finishing department.
The two companies aim to support textile manufacturers in their development projects, targeting to improve their product safety, performance and functionality, while at the same time maximizing the productivity and resource utilization of the finishing application process.
Archroma and Baldwin are collaborating in multiple projects that combine Archroma’s most sustainable product innovations with Baldwin’s Texcoat G4™.
TexCoat G4 is a non-contact spray technology for textile finishing and remoistening, designed to allow a controlled and optimal coverage of the exact amount of finish chemistry for reaching specific characteristics of the fabric. The system can be used to reduce water consumption by as much as 50% compared to traditional padding application processes.
Archroma and Baldwin are currently testing Archroma’s finishing products and systems, such as the soon-to-be-launched PFC-free* Smartrepel® Hydro SR for water-based soil repellence, as well as metal and inorganic particle-free antimicrobial technologies like Sanitized T 20-19 and TH 15-14, which will be launched at the upcoming Techtextil 2022.
Source: baldwintech.com
Lenzing aims for $1 billion EBITDA by 2027
Lenzing AG and its leadership team have carried out a comprehensive review of corporate strategy to maximize the use of growth opportunities and enhance the company’s position in sustainability and circularity. The result for the company is sharpened corporate focus, prioritizing projects that best serve its customers’ needs, while contributing positively to society and the environment. The core outcome of the corporate strategy has led to higher financial targets for 2027. These include earnings before interest, taxes, depreciation and amortization (EBITDA) above 1 billion euros ($1.06 billion) versus 363 million euros ($383.54 million) in 2021, return on capital employed (ROCE) above 12 percent compared to 8.1 percent in 2021, and net financial debt/EBITDA below 2.5x versus 2.7x as of the end of 2021.
Source: www.lenzing.com
Nominations open for prestigious RISE® Innovation Award
INDA, the Association of the Nonwoven Fabrics Industry, has announced the nomination process is now open for the annual RISE® Innovation Award. The prestigious award will be presented at the RISE® (Research, Innovation & Science for Engineered Fabrics) Conference – September 27-28, 2022, at North Carolina State University, Raleigh, NC. RISE® 2022 is a two-day conference presenting insightful research and science that propels product development.
Companies, academic institutions, research centers, and individuals are invited to nominate their advances in nonwovens and engineered materials at https://www.riseconf.net/award-submission.html until the July 15, 2022 deadline.
The RISE® Innovation Award recognizes innovation within and on the periphery of the nonwovens industry that uses revolutionary science and engineering principles to solve current and future industry needs. Raw material advances, advances in process or manufacturing technologies including web forming and converting, new product or application development, and other areas that may extend or enhance the use of nonwovens will be considered for nominations.
Industry professionals involved with product development, material science, and disruptive enabling technologies for both consumer and industrial products are encouraged to nominate their product(s) for the RISE® Innovation Award.
Technical experts serving on the INDA Technical Advisory Board will review nominations and select three finalists who exemplify the use of cutting-edge science and engineering principles to advance the field of nonwovens. Finalists will present their innovations to technology scouts, scientists, researchers, and next level industry professionals at the RISE® Conference on Tuesday, Sept. 27, 2022.
Last year’s RISE® Innovation Award was presented to Canopy for their fully mechanical, non-electrostatic, Canopy Respirator featuring a filter designed for superior breathability while offering the wearer facial transparency.
Criteria and eligibility, nomination process timing, and prior award recipient information is available online: https://www.riseconf.net/award-submission.html
Source: www.inda.org
Junior engineers with focus on sustainability
Chairman of VDMA’s Walter Reiners-Stiftung Foundation, Peter D. Dornier, awarded prizes to seven successful young engineers at the Techtextil Frankfurt event in June. For the first time, the Foundation awarded two Sustainability Awards. They were awarded to academic works in which, for example, solutions for resource-saving products and technologies are developed.
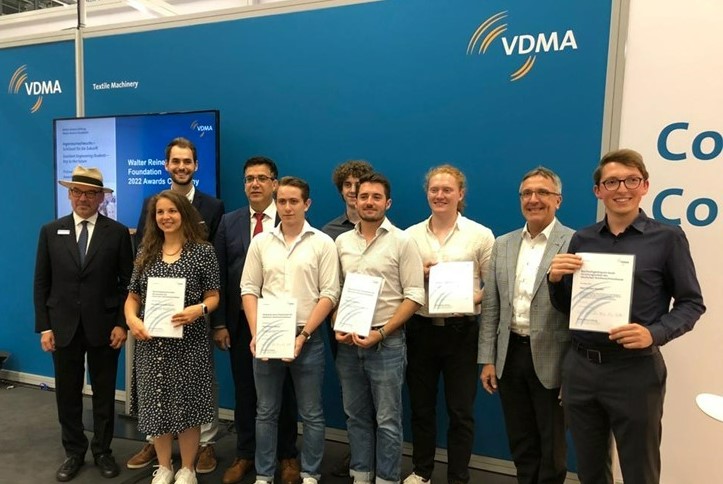
A Sustainability Prize in the category Project Work, endowed with 3.000 euros was awarded to Simon Hoebel, TU Dresden, for his thesis on recycled thermoplastic fibres for composite components.
Marina Michel, TU Dresden, received a Sustainability Award in the category Master, worth 3.500 euros. The topic of her master thesis was the functionalization of yarns for the filtration of micro- and nanoplastics from water.
A Promotion Prize in the category Project Work, endowed with 4.000 euros, was awarded to a student group from RWTH Aachen. The teamwork of Luis Gleissner, Leopold Habersbrunner, Frederic Olbrich and Frederik Schicks was the construction of a test rig for tests on oil-adsorbing textiles.
Felix Zerbes, RWTH Aachen, was awarded a Promotion Prize of 3.500 euros in the category Master. He developed a technical solution for air jet weaving to improve the quality of woven fabric.
Source: VDMA.org
Manuel Merkt appointed president of Zund America
Zund America, Inc., announced the appointment of Manuel Merkt as President of Zünd’s Milwaukee-based North American operations. As a German native, Manuel Merkt began his career in industrial engineering with an apprenticeship program through Hermle AG, a manufacturer of high-end machine tools. After acquiring degrees in engineering from both the University of Applied Science in Constance, Germany, and from Coventry University in the UK, Manuel moved to Wisconsin in 2010 to support the Hermle USA team in various sales and business management functions and ultimately took on a leadership role as President and COO in 2017.
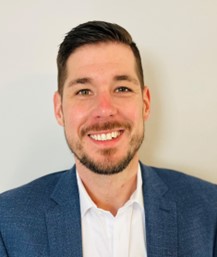
In his 11 years with Hermle USA, Manuel developed exceptional leadership skills which are reflected in the company’s steady growth. His intimate knowledge of both European and North American culture and business practices makes him an ideal candidate for stepping into the leadership position at Zund America. He intends to continue building on the company’s remarkable growth with smart recruiting practices and ongoing workforce development. Ultimately, Manuel’s goal is to continue moving Zund America forward with long-term business development strategies, marketing initiatives, and best practices in sales and support services consistent with those Zünd pursues globally. Taking full advantage of Zund America’s state-of-the-art HQ in Wisconsin, Manuel will push to further improve the Zünd customer experience in sales, training, and support.
Source: zund.com
Retech to present godet roll at Techtextil
Retech will address demand for technical yarns with maximum strength with a newly launched godet roll at Techtextil, Germany later this month. The roll has an ideal length of 420 mm to process 8-12 threads at a time. Its extended diameter of 250 mm allows a significantly increased speed with the same dwell time. Additionally, the higher motor torque guarantees the very best results in yarn tenacity. Further technical parameters are speeds that can be ramped up to 6500 m/min and the temperature reaches 250°C with an excellent temperature profile of +/- 1.5 °C.
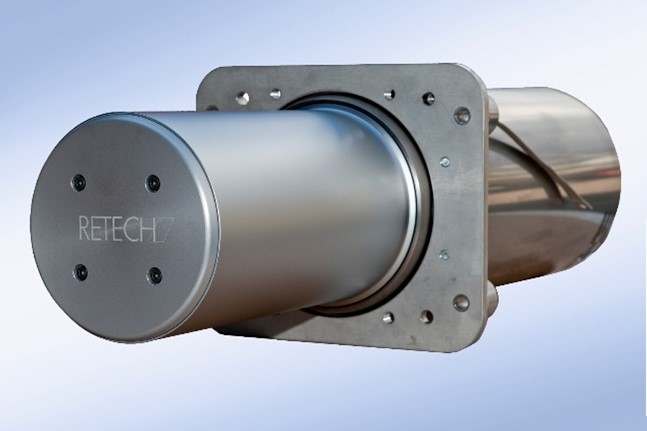
High-temperature godet rolls are used for high-performance fibers. High-performance fibers require temperature at extremely high levels, since fibers such as para-aramids have high glass transition temperatures nearing 370 °C. Retech high-temperature godet rolls have a heating power of up to 400 °C. They also offer outstanding performance in terms of precision within 0.5°C – guaranteed by the established Retech temperature controller – and repeat accuracy from 1 to 100 godets.
Source: Retech
Trützschler to present new nonwoven solutions at Techtextil
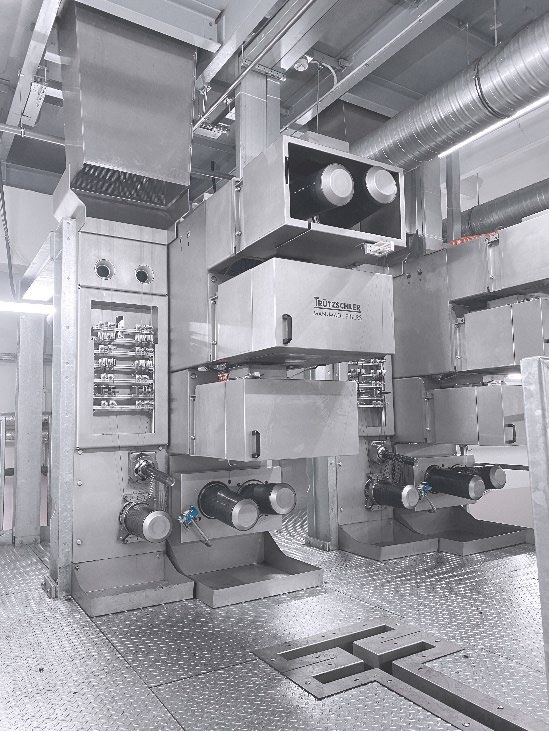
Trützschler Nonwovens, Trützschler Card Clothing and Trützschler Man-Made Fibers will present various new and proven solutions for the nonwoven, card clothing and man-made fiber sectors at Techtextil in Germany this month.
Trützschler Nonwovens will show solutions for using sustainable fibers such as hemp, linen, nettle and pineapple fiber, among others. The company will also showcase software solutions for manufacturing, nonwovens for automotive sector, and processing of manmade material.
Source: Truetzschler
DiloGroup to incorporate sustainability
German machinery maker DiloGroup will showcase its machinery and equipment tailored for sustainability at Techtextil, Germany this month. Savings in energy and materials have become crucial for the industry, and the company will show off its latest developments in this area.
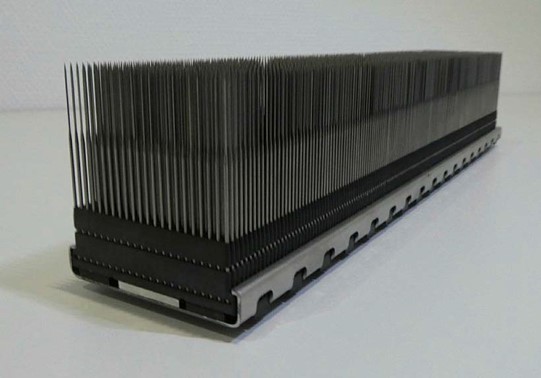
Among the developments are Needling, producing nonwoven by “intense needling” instead of water entangling, which can reduce cost to between one third and one fifth per annum; Fiber Pulp Recycling, where fibrous material in nonwoven and used clothes can be recycled; Additive Nonwoven Production, the additive production method of the 3D-Lofter that is suited for automotive parts, and an added potential for use in apparel and shoe production; IsoFeed Card Feeding, a method that offers great potential for a more homogenous card feeding.
Source: DILO
New fiber from Swedish company
Swedish company TTT – TreeToTextile, owned by H&M Group, Inter IKEA Group, Stora Enso, and LSCS Invest, have developed a technology for producing a new fiber for textile applications. It is a regenerated cellulosic fiber, produced from renewable and sustainably sourced raw materials from the forest. The properties and touch of the fiber are of a natural fiber, with similarities to both cotton and viscose.
The technology of TreeToTextile is subject to several patents. The spinnerets for this special process were produced by SOSSNA- Spinnerets®, Sossna GmbH, Dorsten/Germany.
Source: www.treetotextile.com www.sossna.de
Recover receives $100 million investment
Recover™, a leading materials science company and producer of sustainable, premium recycled cotton fiber and cotton fiber blends, announced that it has closed a new $100 million minority equity capital investment led by the Sustainable Investing business within Goldman Sachs Asset Management (Goldman Sachs). Goldman Sachs is investing alongside majority shareholder STORY3 Capital Partners.
Recover will use the investment to accelerate its global expansion and production capacity, allowing more rapid adoption of sustainability initiatives by leading brands and retailers. Recover serves some of the largest and most recognizable retailers, brands and vendors in the world, including, among others, Primark, Inditex, C&A, Revolve and Lands’ End.
Recover’s proprietary recycled cotton fiber reduces the carbon and water intensity of the apparel supply chain, addressing the apparel sector’s contribution to one of the world’s largest sources of environmental degradation. Recover estimates that the new investment places Recover on a path to increase its production to over 350,000 metric tons of recycled cotton fiber per year by 2026, saving up to 5 trillion liters of water annually—equivalent to the drinking water consumed by over 4.5 billion people each year—and allowing for significant reductions of carbon emissions, energy and land use relative to conventional cotton fiber, based on industry research.
Source: Recover Fiber
NIRI Accelerator – agile collaboration for rapid product development
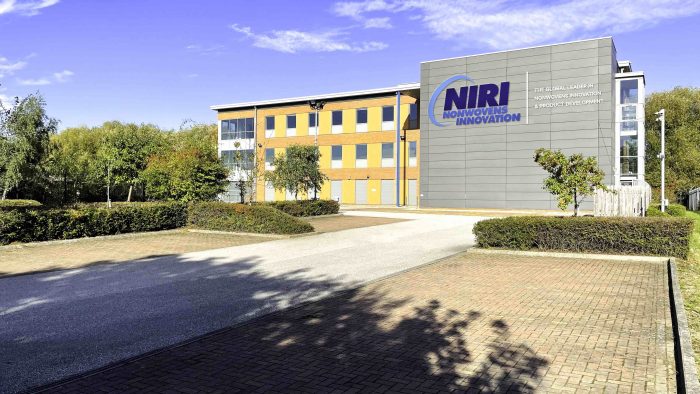
Global leaders in nonwovens innovation and consultancy, the Nonwovens Innovation and Research Institute (NIRI) now offers clients a ‘plug-in’ approach to R&D, through their novel NIRI Accelerator. The approach is designed to support world-class businesses to get products to market faster by streamlining product development through shared expertise and effective collaboration.
NIRI assign an Innovation Partner to a client’s development team whose primary task is to manage the communication channels and accelerate innovation across multiple projects and programs. Through the Innovation Partner, the customer has full access to NIRI’s extensive prototyping capability and support from NIRI’s 40-plus world-class textile scientists and engineers. Dr. Ross Ward, chief commercial officer at NIRI, explains the rationale behind the service,
“One arguably unexpected outcome from Covid is the current global recruitment challenge, felt across all sectors, which is impacting on the capacity and capability to develop new technologies and products within commercially viable timeframes. For companies that struggle to recruit highly skilled staff and train them up to the necessary level of expertise, NIRI offers instant expertise and capability through the NIRI Accelerator, to help clients with agile R&D and support them from concept though to commercialization.”
For the cost of one employee, clients have access not only to the scientist assigned to the project and embedded within the company, but also to NIRI’s full innovation team and the Institute’s world class facilities. As the innovation director at one £2.5billion company puts it, “NIRI has the abilities and the facilities that we do not.”
Facilities available to companies through the Accelerator include a full range of state-of-the-art prototyping equipment, covering fiber and filament, drylaid, wetlaid, spunmelt, nanofiber and bonding. NIRI’s comprehensive analytical services include fabric structure, fiber and surface analysis; chemical, thermal and filtration properties; hygiene testing and liquid transport, as well as physical testing facilities for fibers, yarns and fabrics. Ross comments,
Source: Nonwovens Innovation
Increase in demand for automotive technical textiles
Demand for technical textiles in the automotive market is growing as new applications emerge and manufacturers strive to increase comfort, improve safety and reduce weight, according to “Profiles of five major automotive technical textiles manufacturers”, a 20-page report from the global business information company Textiles Intelligence.
The average weight of textile materials now used in a mid-size car is 30 kg—50% more than the 20 kg used in 2000. One driving force behind the rise has been a focus on lowering weight in order to achieve higher fuel efficiency and reduce greenhouse gas emissions, in response to government directives.
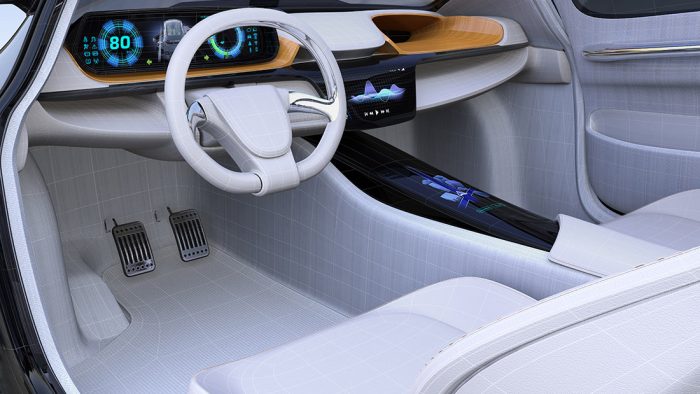
Technical textiles offer significant opportunities for reducing weight. For example, the use of components made from Lineo’s FlaxPreg sandwich panel composites has been proved to achieve a weight reduction of 50% compared with traditional components made from glass fiber and polyurethane. Also, the composites offer a cost advantage of around 5%. The composites are designed for manufacturing a number of automotive interior components, including door panels, instrument panels, load floors, roof trim and seat backs.
Similarly, the use of ELeather—an artificial leather material for automotive interior components—achieves a weight reduction of 40% compared with conventional leather.
Another driving force behind the rise in demand for technical textiles in automotive applications is a need for improved acoustic comfort as the popularity of new energy vehicles (NEVs) grows. In particular, sounds which were previously masked by the noise of the internal combustion engine (ICE) in standard ICE vehicles are clearly audible in NEVs—much to the discomfort of the user.
To remedy this discomfort, Adler Pelzer Group (APG) provides full system engineering and noise, vibration and harshness (NVH) packages to customers such as Tesla and, more recently, it has redefined its methods for developing NEV acoustics in a package which it calls EVO (evolution of automotive acoustics).
Meanwhile, Autoliv and Global Safety Textiles (GST) have benefited from rising demand in the airbag sector and, in particular, rising demand for new innovative products. For example, Autoliv has developed an exterior airbag for autonomous vehicles which covers the front of the vehicle when inflated in order to protect vulnerable road users such as cyclists, motorcyclists and pedestrians.
Despite the promise shown by increasing demand for technical textiles in the automotive market, however, suppliers of technical textile products to the automotive industry were severely impacted in 2020 and 2021 by a slowdown in the market caused by the COVID-19 pandemic. They were also impacted by supply chain issues, increased freight and transportation costs, higher energy prices, and shortages of supercapacitors.
Source: Textiles Intelligence
REPREVE®, demonstrates traceability and transparency at the Next Level
Unifi, Inc., makers of REPREVE® and a leading innovator in recycled and synthetic yarns, is featuring U TRUST® Product Certification, an enhanced supply chain certification, and REPREVE SmartDye™ technology at the Summer Outdoor Retailer Show taking place in June in Denver.
U TRUST Product Certification is one more way that Unifi builds trust and transparency around sustainability. From any point in the supply chain, and throughout the life of a product or fiber, Unifi can test and verify that REPREVE is present at expected content levels.
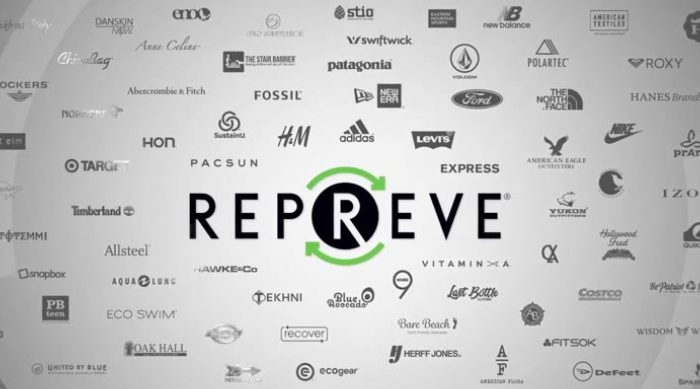
Unifi is also featuring its new REPREVE SmartDye™ recycled polyester, which is designed to be dyed at lower temperatures. REPREVE SmartDye delivers energy savings of up to 30% and has a lower carbon footprint than standard polyester dyeing, all without compromising a fabric’s integrity. This product meets performance requirements for an easy drop-in replacement of conventional polyester. REPREVE SmartDye is available in both polyester staple fiber and filament fiber.
Source: Unifi
Enzyme that breaks down PET
A multidisciplinary team based at the University of Texas at Austin (UT Austin), has developed a polyethylene terephthalate hydrolase (PETase) capable of breaking down untreated post-consumer PET in a single week, according to a study published in Nature.
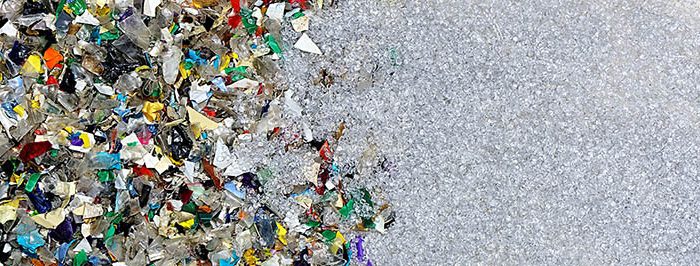
Testing included 51 different post-consumer plastic containers, five different polyester fibers and textiles, as well as PET water bottles. All were found to “almost completely degrade” when faced with the new enzyme variant, known as FAST-PETase (ie, functional, active, stable and tolerant PETase), the authors said.
The team employed a machine learning model to engineer five mutations to PETase, a natural enzyme which supports bacterial degradation of PET plastics. The scientists found that these mutations can quickly depolymerize post-consumer PET at low temperatures – between 30 and 50 degrees Celsius – and using a range of pH levels, it was found. Some PET products could even be fully broken down into monomers within 24 hours.
The team now intends to scale up enzyme production, in preparation for the patent-pending technology’s intended industrial and environmental application, the university said.
Source: University of Texas
Milliken & Company participates in two U.S. trials with Accelerating Circularity
The Textile Business of Milliken & Company announced its participation in two commercial textile-to-textile U.S. product trials with Accelerating Circularity. Serving as the fabric manufacturer in both trials, Milliken will be developing two separate garments—a polyester Polartec Fleece and a cotton/polyester twill—that will be manufactured at scale.
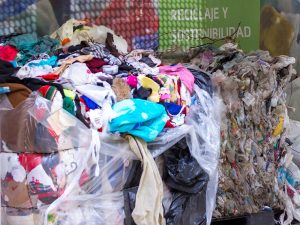
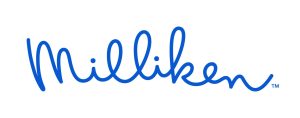
The polyester Polartec Fleece trial will use chemically recycled textiles made possible by Gr3n Recycling while the cotton/polyester twill trial will feature a mechanical recycling process. Milliken will use Unifi fiber to develop and manufacture the fabric used in each trial.
According to the EPA, approximately 16.9 million tons of textile waste go to landfills. The U.S. trials are designed to assist Accelerating Circularity in proving a functioning textile-to-textile circular supply chain that reduces textile waste is possible.
The Rapid Prototype Center (RPC) at Milliken, the largest privately-owned textile testing center in the United States, is a major contributor to the ability to run these trials quickly and efficiently. “Milliken’s RPC provides our organization with an invaluable tool—the ability to fail fast and adjust. Typical production equipment requires hundreds of pounds of fiber that leads to thousands of yards of fabric.
Milliken joined Accelerating Circularity as a Steering Committee member, a group of companies that provide strategy and guidance to the U.S.-based project, in 2021. Additional current members include Eastman, Gap Inc, Giotex, Gr3n, Lenzing, Nike, Target, VF Corp. and Unifi.
Source: www.milliken.com
International textile production cost varies significantly
A new report from International Textile Manufacturers Federation (ITMF) found that international textile production costs vary by up to 72%. A study from the organization reveals that producing 1 m of woven fabric from cotton 1-1/8″ in a continuous open width process (COW) cost US$ 1.36/m on average in 2021 and between $1.11/m in India and $1.91/m in Italy, a difference of 72%.
Spinning the yarn needed to produce this meter of a finished woven fabric costs 19% of the fabrics’ total production cost on average worldwide (range between 15% in Korea and 22% in Central America). Weaving this yarn adds an extra 19 percentage points (pp) on average to the total production cost of the fabric (range between 14 pp in Egypt and 26 pp in Italy). Finally, finishing this meter of woven fabric increases the final production cost by 31%.
Source: ITMF.org
Australia releases new national flushability standard
Standards Australia has released a new national standard that builds on the test methods and criteria of the INDA/EDANA Flushability Guidance Document, Fourth Edition (GD4). It also includes a new user-friendly labeling approach to indicate what products can be flushed down the toilet.
INDA and EDANA – the two leading nonwoven trade associations representing consumer wipes manufacturers and supply chains – issued a copyright license for the testing method under a collaborative agreement with Water Services Association of Australia (WSAA).
Australia and New Zealand manufacturers will now follow the same rigorous seven-test process established by INDA and EDANA, with minor modifications, to determine which wipes can be safely flushed in Australia and New Zealand.
WSAA worked with Standards Australia – the country’s leading independent, non-governmental, not-for-profit standards organization – to develop the new standard in response to increasing blockages experienced by water utilities and customers across Australia.
The standard specifies test methods and criteria for determining if products are suitable for disposal by flushing them down a toilet and also provides guidance on labeling and marking of these products. Toilet paper, liquids and soluble products are excluded.
Source: www.inda.org
Eastman’s Mark Costa set to receive International Palladium Medal
Mark Costa, Eastman Chemical Co. Board chair and chief executive officer, has been awarded the 2022 International Palladium Medal.
Costa earned the award for his contributions to the chemical industry and his leadership in enhancing the international aims and objectives of the Société de Chimie Industrielle. Costa has dedicated his career at Eastman to harnessing the power of innovation and science to solve the world’s biggest challenges, most notably in the circular economy.
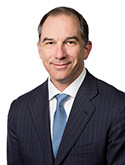
Costa will receive the award at a dinner in his honor on Sept. 12 at the New York Hilton Midtown.
Eastman is headquartered in Kingsport and employs approximately 14,500 people around the world.
The International Palladium Medal was established in 1958 and was first presented to Ernest-John Solvay of Belgium in 1961. Subsequent awards have been made to American, French, British and German recipients biennially.
Source: Eastman
Lanxess, Advent International establish global joint venture
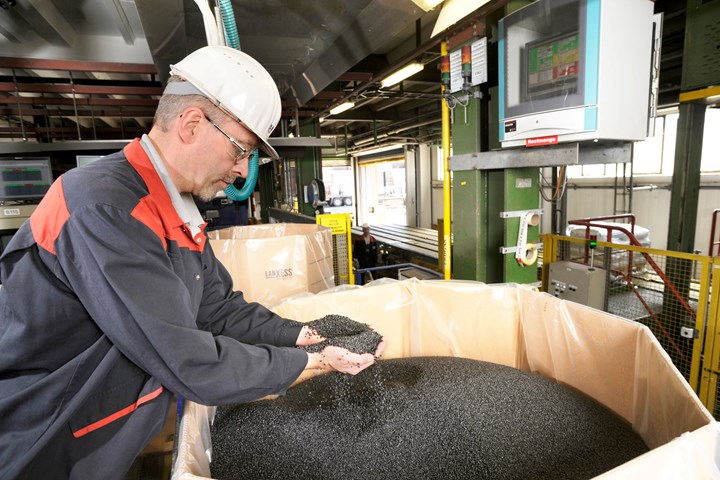
Lanxess of Germany and Advent International of Boston, Mass., U.S., a global private equity investor, are establishing a joint venture (JV) for high-performance engineering polymers. The two companies signed an agreement to acquire the DSM Engineering Materials business (DEM) from Dutch group Royal DSM (Heerlen, Netherlands), which will become part of the new JV. The purchase price is around €3.7 billion and will be financed by the JV via equity from Advent and external debt. The business represents sales of around EUR €1.5 billion with an EBITDA margin of approximately 20%. DEM is global suppliers in high-performance specialty materials that address key market needs in electronics, electrical and consumer goods.
Source: Lanxess
INDA promotes Fragnito to president to succeed Rousse, who is retiring in January
The Board of Directors at INDA, Association of the Nonwoven Fabrics Industry, has elevated Tony Fragnito from chief operating officer of INDA to president of INDA, effective May 31.
Fragnito will assume the position currently held by Dave Rousse, who will become president emeritus and provide support and assistance to Fragnito as needed until Rousse fully retires in January 2023.
Fragnito joined INDA November 29, 2021 as chief operating officer and has been leading INDA’s implementation of its new Strategic Plan, as well as updating INDA’s technology platform. This follows decades of leadership experience assisting trade and professional organizations in realizing their organizational and operational potential. A certified public accountant, Fragnito brings strong financial acumen in addition to extensive information technology, human resource and program management accomplishments from organizations representing a variety of professions and industries.
Source: INDA
Agreement to commercialize novel biopolymer solutions
CJ BIO, a division of South Korea-based CJ CheilJedang and leading producer of polyhydroxyalkanoate (PHA), and NatureWorks, an advanced materials company that is the world’s leading producer of polylactic acid (PLA), have signed a letter of intent (LOI) establishing a strategic alignment between the two organizations and have announced that the two companies are working toward a Master Collaboration Agreement (MCA). The companies will work together to develop sustainable materials solutions based on CJ BIO’s PHACT® Marine Biodegradable Polymers and NatureWorks’ Ingeo™ biomaterials technology. The goal of the agreement is to develop high-performance biopolymers that will replace fossil fuel-based plastics in applications ranging from compostable food packaging and food serviceware, to personal care, and beyond.
NatureWorks is a pioneer in the development of bio-based materials that reduce carbon impact and enable new end-of-use options with its Ingeo technology. As a company, it has developed many of the leading high-volume applications for PLA. In recent years, PLA has experienced significant growth as a bio-based material in a broad range of finished products. Due to its unique functionality, it has been used to replace petrochemical-based plastics, with 100% bio-based content, and enable end-of-use recovery options, including compostability and chemical or coated paper recycling. Both companies realize the potential to further enhance performance and end-of-use solutions for biopolymers and increase the level of adoption across many new applications. By combining their expertise and technology platforms, NatureWorks and CJ aim to deliver next generation solutions together. Initial development and collaboration are showing very promising results when using CJ BIO’s unique amorphous PHA in combination with Ingeo biopolymer.
Source: natureworksllc.com
Foster Corporation/MedNet to represent Arkema
Foster Corporation/MedNet will represent Arkema in all countries in Europe, the Middle East, and Africa (EMEA) beginning July 1, 2022. This agreement includes Arkema’s Pebax® MED, Rilsan® MED, Rilsamid® MED, Rilsan® Clear MED and Kynar® MED product ranges.
MedNet, headquartered in Germany, has been supplying the medical industry since 1990. As a supplier of raw materials and components, they have developed outstanding knowledge and expertise which are essential to successfully grow this highly technical market.
Foster Corporation, Arkema’s primary high performance medical polymers distributor globally will support MedNet by supplying them with their extensive range of compounds based on Arkema’s specialty polyamides and will bring their in-depth technical knowledge of Arkema’s high performance polymers portfolio.
Source: fostercomp.com
Suominen launches a nonwoven made with recycled paper
Suominen of Finland has strengthened its position as the frontrunner in sustainable nonwovens by launching HYDRASPUN® Circula, the market’s first ever nonwoven made with recycled paper.
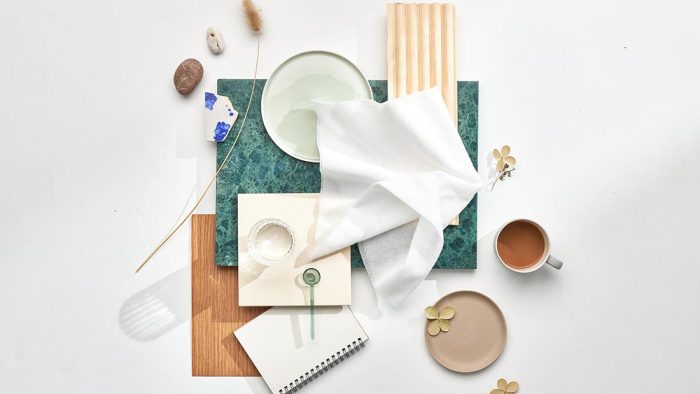
HYDRASPUN® Circula is biodegradable, plastic-free and can be used in multiple applications. The product was created in cooperation with Codi Group, one of Europe’s leading wet wipe producers. Drawing from both parties’ industry expertise, the new product offers a variety of applications to meet consumers’ daily needs.
“It is important for Suominen to continuously develop new sustainable products to be able to offer even more choices to our customers. HYDRASPUN® Circula is a perfect example of how we can develop our nonwovens with innovations and more sustainable raw materials. HYDRASPUN® Circula is also a proof of great product development towards circular economy without compromising excellent quality and functionalities,” said Johanna Kivistö, Manager, Category Management, Europe.
Source: Suominen.fi
Oerlikon to Sell Business in Russia to Local Team
Oerlikon has entered into an agreement with the local management team to sell all its operations in Russia. The business will continue to operate independently under the new owners.

On March 4, 2022, Oerlikon ceased all international cross-border business activities with Russia following its invasion in the Ukraine. As a final step, Oerlikon is now ceasing all business activities within Russia as well. Oerlikon currently employs 48 colleagues in Russia across 6 locations, and sales in 2021 were below CHF 5 million.
Source: Oerlikon.com
Aptean Apparel Manufacturing Solution Receives Software Innovation Award
Aptean, a global provider of mission-critical enterprise software solutions, announced that its industry-specific software for apparel manufacturers has been recognized with an Innovation Award from the Network Association of Uniform Manufacturers and Distributors (NAUMD). Aptean’s shop floor control solution from Exenta was honored with NAUMD’s 2022 Software Innovation Award.
Aptean’s shop floor control software was found to deliver a unique solution to apparel and sewn goods manufacturers, giving them up to the minute visibility into work in production and helping to identify and eliminate production bottlenecks. By automating incentive payroll calculations, the software also replaces manual processes that are both time-consuming and error prone. It provides immediate performance feedback on efficiency and quality to operators and managers, resulting in increased production and improved quality of finished goods.
Source: www.aptean.com
H&V welcomes seasoned executive James Noonan to the role of CFO at Hollingsworth & Vose
H&V has named longtime finance executive James Noonan to the role of chief financial officer, effective May 23, 2022. A seasoned professional and a fellow member of the Association of Chartered Certified Accountants, Noonan brings more than 20 years of experience in financial management to the CFO role at H&V.
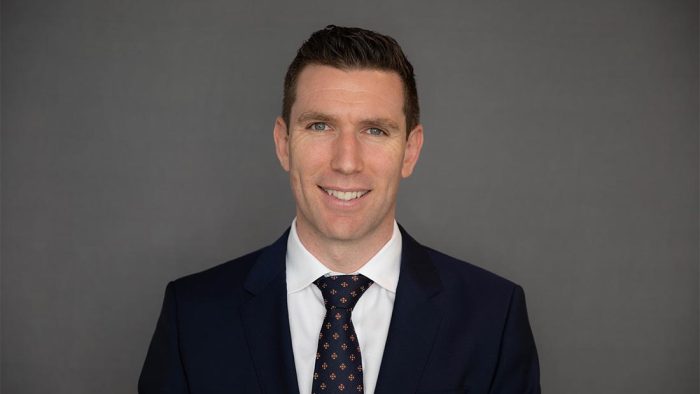
Prior to joining H&V, Noonan served for three and a half years as operations CFO for Suffolk Construction, the largest construction contractor in Massachusetts and one of the 20 largest in the country. From 2016 to 2018, he spent a year each as vice president of finance and CFO for CRH Americas Materials Inc. North Division, a global building materials group that employs more than 85,000 people at 3,600 locations worldwide. Noonan also worked for CRH Americas Materials Inc., CRH Americas Inc. and CRH Plc. from 2007 to 2016 in a range of roles, including group internal auditor, assistant audit manager and corporate controller. Before CRH, he was an accounting manager for tech firm Avaya Inc. and an accountant for Kerry Group Plc., a global food and nutrition company based in Tralee, Ireland.
Born and raised in Ireland, Noonan earned a B.S. in accounting from University College Cork in Cork, Ireland, and an MBA from the Massachusetts Institute of Technology.
Source: Hollingsworth & Vose