In the dynamic and global textile fiber industry with its various manufacturing processes and end-uses, news and information is breaking on a daily basis. International Fiber Journal is tracking stories relevant to our industry from manmade to natural to bio-based fibers, innovations in nonwoven, woven, braided and technical textiles, technologies for additives, bonding, coatings and polymers, and applications from apparel to hygiene to transportation, and more. Here we will post news stories relevant to textile fibers and their downstream applications on an ongoing basis. Please check back for regular updates. If you have news that you feel should be added to this summary report, please email it to Matt Migliore at mmigliore@inda.media.
Most recent update: September 30, 2021
RadiciGroup demonstrates industrial-scale nylon production from waste oil and oil industry byproducts
RadiciGroup, an Italian multinational headquartered in Bergamo, Italy, and producer of a wide range of chemical intermediates, polymers, high-performance engineering polymers and advanced textile solutions, demonstrated the feasibility of industrial-scale production of polyamides (nylon) starting from bio adipic acid obtained from renewable raw materials, including waste oil and by-products of the oil industry. Potential application sectors for the process and products are textile/fashion, automotive, design, electrical and electronics.
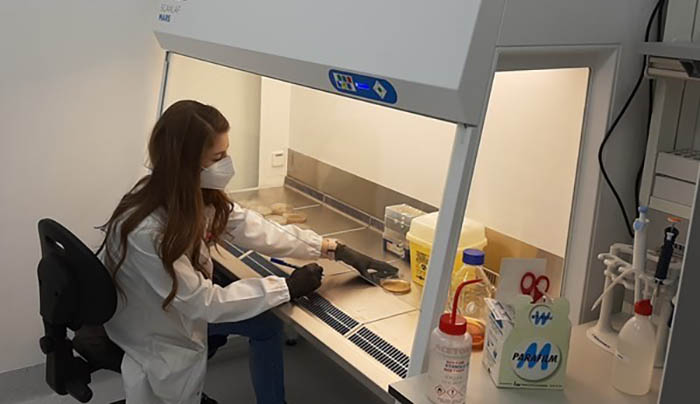
The research was conducted through the Ulysses project and experimentation was performed in collaboration with research centers and universities. Partial funding was received from the Region of Piedmont, Italy, within the scope of the “Call for Proposals IR2 (Industrialization of research results).” The ambitious, innovative multiyear project was launched in March 2018 and stemmed from RadiciGroup’s desire to increase the sustainability of its products, while delivering the same quality and performance as required by product standards. The research was also focused on meeting the demand coming from various strategic sectors, in line with the European targets for the development of low-emission businesses and a circular economy.
The funding amounted to EUR 6.2 million, of which EUR 1.7 million was contributed as a grant by the Piedmont Region.
Source: radicigroup.com
Freudenberg PM launches House of Sustainability, featuring sustainable solutions for apparel
Freudenberg Performance Materials Apparel announced the launch of its new House of Sustainability, an initiative designed to assist customers worldwide in enhancing the sustainability of their products. In the House of Sustainability, customers will find more than 500 sustainable solutions for a range of applications in the apparel industry. With this initiative, Freudenberg is making its entire portfolio of sustainable solutions visible and transparent, while also showing its roadmap of forward-looking innovations.
“Sustainability is a mission and driving force for us. We initiate sustainable programs at global and regional level and are constantly innovating globally available sustainable solutions,” said John McNabb, chief technology officer, for Freudenberg Performance Materials. “Many examples bear witness to our forward-looking efforts. To name just a few highlights, we are, for example, pioneers in recycling PET bottles, and commissioned our first recycling plant back in 1991. We developed the first biodegradable nonwoven interlinings in 1995. And today, we recycle more than 2.5 billion post-consumer PER bottles per year.”
The foundation for the Freudenberg House of Sustainability is made up of four elements: Certifications & Regulations, Raw Materials, Technology and Carbon Footprint. This foundation supports seven pillars (recycled general interlinings; recyclable interlinings; energy-saving interlinings; biodegradeable interlinings & thermal insulations; sustainable cotton interlinings; nature-based interlinings; and recycled thermal insulations and linings) providing customers with more than 500 sustainable solutions. The House of Sustainability enables customers to choose the right solutions for their sustainable applications and to meet their sustainability goals efficiently.
The House of Sustainability will be launched worldwide over a 12-week period. Each week, Freudenberg will post in-depth information about the elements and pillars on several channels. The complete House of Sustainability will be presented at ISPO Munich 2022.
Source: freudenberg-pm.com
INDA, EDANA publish 7th edition of Global Nonwoven Markets Report
A new report published jointly by the U.S. and European nonwoven trade associations forecasts strong market demand for nonwovens materials through the next five years. The joint publication from EDANA and INDA, titled Global Nonwoven Markets Report, A Comprehensive Survey and Outlook, 2020–2025 is the 7th edition and provides in-depth information and analysis of the global nonwoven macro drivers, supply and demand, and regional trade. Among the highlights of the report:
- In the historical period (2010–2020) production increased 6.2% annually, led by growth in the spunlaid processes and drylaid hydroentanglement.
- China led the growth in production, adding an additional 4.7 million tonnes from the end of 2010 through to the end of 2020, representing a 11.5% annual growth rate.
- Across the nonwoven end use segments, the wipes, filtration, medical segments expanded at the fastest rates, given the industry’s rapid response to provide materials that keep the surfaces we touch clean, protect the air we breathe, and provide a barrier to keep our bodies safe.
* International Fiber Journal is owned by INDA, Association of the Nonwoven Fabrics Industry (inda.org).
Spinnova receives Climate Leadership Coalition’s Carbon Handprint Recognition
To celebrate Zero Emissions Day, the Climate Leadership Coalition (CLC) in Finland awarded the first Carbon Handprint Recognition. One of the two recognitions was awarded to Spinnova’s textile fiber innovation for saving up to 65% of CO2 emissions compared to cotton.
“Continuous improvement of our carbon handprint is a big deal to us; one that’s been considered from the very start,” said Spinnova’s chief technology officer and co-founder Juha Salmela. “A climate friendly product must absolutely also be produced with minimal impact.”
The other recognition was given to Neste’s NesteMY Renewable Diesel for helping reduce motoring emissions by up to 90% when compared to fossil fuels.
Zero Emission Day’s mission is to give the planet a day off from fossil emissions and add awareness of the drawbacks of carbon emissions. The day’s goal is to inspire people to make climate friendly choices in their personal everyday lives. In 2021, the event was held in collaboration with the Finnish city of Lahti. Lahti was named the EU Green Capital 2021.
CLC is Europe’s largest non-profit climate business network. Growing the positive impact and reducing carbon handprint is becoming an essential goal for companies, and many CLC members have already defined a metered carbon handprint for products and services.
Source: spinnova.com
BASF’s Haptex demonstrates environmental benefits in LCA study
A Life Cycle Assessment (LCA) of BASF’s synthetic leather solution Haptex demonstrates the environmental benefits compared to other conventional synthetic leather solutions.
The LCA study, conducted by Intertek, is based on a total value chain analysis of Haptex from its chemical production to the finished leather goods. Performance on greenhouse effect, cumulative energy demand, and water consumption figures were also calculated and measured.
Haptex produces 52% less greenhouse gas emissions than conventional synthetic leather, with more than a 20% reduction in energy consumption when using 1KG of chemicals for synthetic leather production. Eliminating the wet line from the production processes reduces 30% of water usage compared to solvent-based polyurethane production methods. Haptex does not use any organotin catalysts or plasticizer.
“The report comes at a time when pressure mounts on brands and OEMs to make stronger efforts towards sustainability by choosing alternative and animal-free leather for their products,” said Minli Zhao, vice president, Consumer Industry, Performance Materials Asia Pacific, BASF. “Therefore, we must provide concrete information on environmental emissions and how we are reducing the CO2 footprint to our customers. With this study, Haptex has proven that it is more sustainable compared to other conventional synthetic leather solutions, and at the same time can fulfill the different conventional requirements from OEMs and brands to produce products that are durable, stylish and eco-conscious.”
Haptex is suitable for automotive seating, furniture, footwear and fashion accessories like bags and caps.
“By commissioning an LCA at such an early stage, we are enabling life cycle considerations to be factored in the manufacturing process,” said Yunlong Ma, general manager, Green Initiatives, Intertek. “This supports OEMs and their customers such as footwear, automotive, and furniture brands in determining the right material – such as Haptex, which demonstrated significant environmental benefits – for their next innovation.”
Source: basf.com
Evian unveils 100% rPET bottles made from PET plastic and polyester fiber waste
This Recycle Week (Sept. 20-26), evian has launched a new recycled plastic (rPET, or recycled polyethylene terephthalate) prototype bottle using technology from Loop Industries. This marks a significant milestone in evian’s 2025 circularity journey, according to the company, which will see it accelerate the transition to 100% recycled plastic in all of its plastic bottles.
Loop Industries’ technology allows no- and low-value PET plastics (that will otherwise go to waste) to be recycled endlessly into new, virgin-like PET plastic. The process breaks down plastic into its base building blocks, or monomers. The monomers are then purified and repolymerized into Loop PET plastic. This innovative technology allows more plastic to be kept in use, reduces reliance on fossil fuels and avoids the creation of new plastic.
The cutting-edge technology enables a continuous loop for recycling at large scale, meaning that all types of PET plastic waste – from discarded gym bags to flip flops (and even ocean, colored and opaque plastics, as well as polyester fibers) – can be transformed into high quality plastic bottles.
To bring to life this latest concept, evian has renamed its prototype bottles to ‘evian Loop’ to highlight each bottle’s recycling potential.
evian’s partnership with Loop Industries spans four years, during which time Loop Industries worked diligently on perfecting its technology for commercial production on a global scale. The partnership will see this pioneering technology rolled out across markets beginning in 2022 and is part of evian’s continuous effort to lead the shift and accelerate the development of innovative sustainable packaging solutions. This will allow evian to recycle and repurpose more and more existing plastic waste, bringing them one step closer to their 2025 circularity objective.
Source: loopindustries.com
Freudenberg’s Evolon fabrics earn STeP and Made In Green labels from Oeko-Tex
Freudenberg in Colmar, France, has received the STeP by Oeko-Tex label for Evolon. The fabric was also granted the Made In Green by Oeko-Tex label. Both labels recognize the brand’s commitment to sustainable practices and products.
Certificates awarded by the independent Oeko-Tex institute are highly respected and trusted by the textile industry. For manufacturers, they are confirmation of ecologically and socially responsible production and products – a quality characteristic that plays a growing role in purchasing decisions of companies, as well as for end-users.
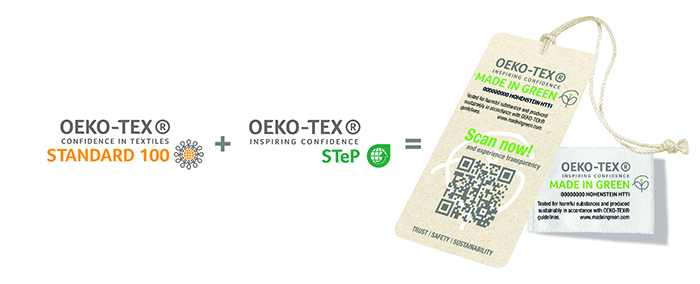
By awarding the STeP (Sustainable Leather & Textile Production) label, the Oeko-Tex Institute recently certified environmentally friendly production processes, a high level of health and safety and socially responsible working conditions at the Freudenberg site in Colmar. The company scored top marks and reached the highest grade of certification, Level 3, for “exemplary implementation of best practices”.
“Evolon fabrics have already earned the Standard 100 by Oeko-Tex label for more than 20 years. This is one of the world’s best-known certificates confirming that textiles have been tested for harmful substances. Here too, Evolon meets the most stringent requirements, and is ranked in product class I, which stands for suitability with baby skin contact”, said Achraf Khedimi, head of Global Sales for Evolon.
As part of the STeP certification, Evolon also meets Oeko-Tex’s Detox to Zero criteria, which specifically cover chemicals management and wastewater quality, following an initiative of Greenpeace aimed at eliminating harmful substances in the textile industry.
Source: freudenberg-pm.com
Glen Raven donates $250K to NC State Wilson College of Textiles’ Pioneer Scholarship Program
Glen Raven recently donated $250,000 to support North Carolina State’s Textile Pioneer Scholarship Program, as well as the Dean’s Textile Innovation Fund. The first needs-based scholarship program at the Wilson College, the Textile Pioneer Scholarship Program aims to identify and recruit qualified students from economically challenged Tier 1 and 2 counties – that designation being determined by calculating counties’ average unemployment rate, median household income, percentage growth in population and adjusted property tax base per capita. Currently, a little more than 25% of Wilson College students hail from Tier 1 or Tier 2 counties.
“We can’t thank Glen Raven enough for their tremendous contribution,” said Wilson College of Textiles Dean David Hinks. “We recognize the importance of providing opportunities for students across all 100 counties, and this helps level the playing field for many in order for many to compete and thrive.”
Since the Textile Pioneer Scholarship Program’s launch in 2019, eight students have entered the Wilson College as Pioneer Scholars, with the aim to add four per year and possibly more as the program continues to gain support, according to Michael Ward, executive director of the North Carolina Textile Foundation (NCTF), the fundraising arm of the college.
“The textile industry remains alive and well, and Glen Raven and our industry peers are continuing to create amazing innovations for the global markets that we all serve,” said Glen Raven CEO Leib Oehmig. “NC State’s Wilson College of Textiles is leading the way in preparing the next generation of leaders that will elevate our industry to new heights. Glen Raven has been around for more than 140 years, and we’re focused on the next 140 years. Therefore, we want to attract the best and brightest to our industry and to Glen Raven. We can think of no better investment than in those deserving students from diverse, underserved geographic and socioeconomic backgrounds. We’ve all needed someone to believe in us and through the Pioneer Scholarship program, Glen Raven is able to demonstrate that we believe in those students and invest in those who may not otherwise have an opportunity to succeed.”
“The Wilson College of Textiles will allow me to expand my knowledge creatively and divergently and I know that I would not be provided with this opportunity elsewhere,” Alex Hutchens, a current Pioneer Scholar from New Bern, North Carolina, said. She plans to study fashion and textile management with a concentration in fashion development and product management.
Another recipient, Jeana Grace Bowker, who grew up in Clinton, North Carolina, intends to study fashion and textile design.
“Being awarded this scholarship now lets me focus on my future without a huge financial roadblock,” said Bowker, whose grandfather taught her to sew and helped develop her passion for sewing and apparel design. “I am so thankful to have received this award. I am really excited about all of the doors this will open for me!”
Source: textiles.ncsu.edu
Sunlighten, Celliant partner to bring infrared fabrics technology to the sauna
Sunlighten, a provider of infrared saunas and portable light therapies, has partnered with Hologenix, the creators of Celliant infrared responsive textiles found in numerous performance, recovery and sleepwear brands, to further enhance the sauna experience.
“At Sunlighten, we are continually looking to innovate, and the addition of Celliant is another step toward enhancing and extending our sauna experience,” said Aaron Zack, Sunlighten co-founder and CEO.
Fabric infused with Celliant now covers Sunlighten’s infrared heaters in all its sauna cabins to maximize every detail of infrared available. In addition, Sunlighten is introducing its new luxury cotton accessories infused with Celliant for those who want to expand the health benefits of infrared and/or enjoy a spa-like experience. The dual-purpose fabric provides added health benefits, as well as comfort, luxury, and practicality both inside and outside the sauna – it epitomizes “Plush Performance.”
The new Sunlighten Celliant-infused accessories work with the infrared heat of its saunas to amplify the benefits even more. The Sauna Linen Collection consists of a Celliant/cotton hand towel, bath towel, robe and body wrap, perfect for use in the sauna or just for every day. Celliant’s natural, ethically sourced minerals embedded into yarns transform body heat into full-spectrum infrared energy and return it to the body safely and naturally. Celliant promotes local circulation and cell oxygenation in healthy individuals while keeping the user dry and at the perfect temperature. This results in stronger performance, faster recovery and better sleep.
The only sauna company to offer branded accessories, Sunlighten’s line creates a resort feeling with spa-level luxury and is plush, densely woven and has a heavy 760-gram weight. Sauna cushion covers, sauna throw pillow covers and SoloSystem SoloPad covers will also be available soon.
Hologenix co-founder and CEO Seth Casden said, “This is a natural partnership for us. Sunlighten infrared saunas and our Celliant infrared performance technology, working in tandem to maximize health and wellness. The Celliant/cotton-blend fabric is also the perfect combination of luxurious comfort and our revolutionary infrared technology.”
Source: sunlighten.com | celliant.com
Spinnova reports 2021 first-half results
Key results from January to June 2021:
- Revenue grew to EUR 370 thousand (EUR 87 thousand).
- Operating loss for the period was EUR 3 093 thousand (EUR 1 993 thousand)
- Total investments were EUR 2 949 thousand (EUR 2 287 thousand).
- The number of permanent employees at the end of the period grew to 49 (28).
In the first half of 2021, Spinnova started building its first commercial factory for Woodspin, the joint venture the company owns 50/50 with its strategic partner Suzano, with the aim of commercially scaling of Spinnova wood-based fiber. The company also started building a proof-of-concept production line for leather waste-based fiber for Respin, the joint venture that Spinnova owns 50/50 with ECCO’s sister company KT Innovations AG. In June, Spinnova also met the capital requirement for its growth plan by listing Spinnova on the Nasdaq Helsinki First North Growth Market.
In the first half of 2021, Spinnova announce that both adidas and the H&M Group joined as brand partners, joining the company’s other brand partners including Bergans, Bestseller, ECCO, Icebreaker and Marimekko, paving the way to a joint commercial future. With adidas’ cornerstone investment in Spinnova’s initial public offering, adidas intends to secure access to significant volumes of Spinnova material in the future. Our partner ECCO showed its strong support for us by investing in Spinnova shares in our initial public offering.
Spinnova also announced a collaboration with The North Face, with the goal of commercializing sustainable products using Spinnova fiber materials and securing access to the first commercial volumes of the fiber.
Spinnova began construction work for the first Woodspin commercial factory in Jyväskylä, Central Finland during the reporting period. The factory is expected to be completed at the end of 2022. Spinnova is the exclusive technology provider for Woodspin, as well as Respin. In the spring, Spinnova agreed on a co-operation with Valmet, a global leader in pulp and paper technology, who will provide drying components for the first Woodspin production line.
Suzano supports scaling plans and has committed to the Woodspin joint venture producing more than one million tonnes of Spinnova fiber per year within a decade. Suzano is investing in a micro fibrillated cellulose production facility next to the Woodspin factory in Jyväskylä.
Finally, Spinnova announced it has raised 115 million euros through our successful initial public offering in June with approximately 20 000 investors participating. Spinnova’s key long-term partners, Suzano and Lenzing, continued as significant shareholders and, in addition to numerous private and institutional investors. Spinnova’s strategic partners adidas and ECCO joined Spinnova as shareholders. The company’s IPO financing plays an important part in securing its growth plan.
Source: spinnova.com
FET continues growth in biomedical sector
Fiber Extrusion Technology has delivered nine meltspinning systems to clients in the biomedical sector since the onset of the COVID-19 pandemic. The company has a similar number on order for 2021/22.
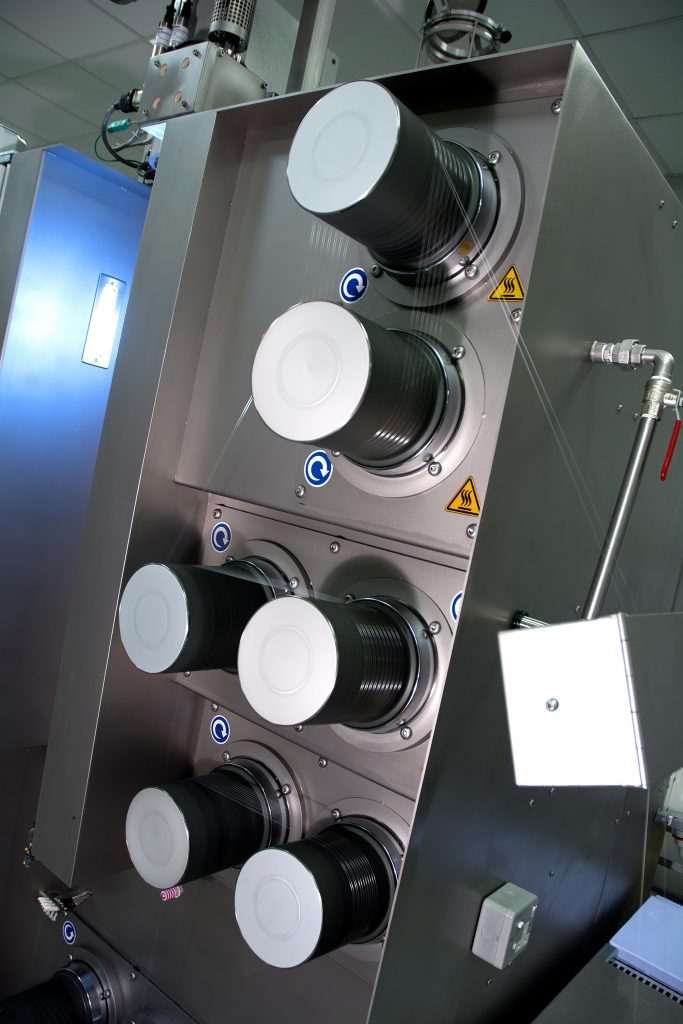
“FET has a long tradition in the highly regulated biomedical sector and we believe our experience is unrivaled,” said Managing Director Richard Slack. “We have built a world leading reputation for melt spinning medical grade polymers in both synthetic resorbable and non-absorbable polymers and FET is now reaping the rewards of this initiative”.
Recent installations include a multi-functional system that can produce multifilament and monofilament pre-cursor fibers and nonwoven systems driven by the demand for FFP3 masks, gowns and other medical products. Sales have been completed in the Far East, USA and Europe. Research organizations such as the University of Leeds have also invested in FET systems for biomedical applications.
To support its biomedical melt spinning technologies, FET will be expanding its in-house Process Development Laboratory by opening a new facility and Visitor Center in early 2022.
Source: fetuk.com
Designers partner with DITF to employ ‘hair of the dog’ approach for sustainable fashion
The young brand modus intarsia is utilizing the undercoat of dogs, which is normally combed out and ends up in the garbage, for the development of high-quality yarn. Fashion designer Ann Cathrin Schönrock came up with the idea, and textile engineer Franziska Uhl from Reutlingen University, together with scientists at the German Institutes of Textile and Fiber Research Denkendorf (DITF), tested the developed yarn on industrial machines and produced it on a larger scale.
Chiengora is what they call the cashmere-like yarn – “Chien,” French for “dog,” and “gora”, in reference to the fine angora that originally comes from rabbits. The yarn has the advantage over cashmere in that the raw material does not have to be flown in from Mongolia and the animals are not bred and kept for wool production. The raw material for the yarn is produced incidentally during daily animal care, especially when the animals shed their winter coats in the spring. Thus, the use of Chiengora not only conserves resources, but also serves animal welfare.

The founding team consists of Ann Cathrin Schönrock (31) from Berlin and Franziska Uhl (25) from Reutlingen. As a trained fashion and knitwear designer with high demands on quality, ethics and sustainability, Ann Cathrin Schönrock started collecting the undercoat from her own dog, from dogs of acquaintances and friends, but also from groomers and breeders back in 2017. After initial feasibility studies, Franziska Uhl from the Faculty of Textile & Design at Reutlingen University joined the team. As part of her bachelor’s thesis, she researched which dog hairs are particularly suitable for yarn development. At the DITF, together with Volkan Ünal and Waltraud Abele, she tested her theses on industrial-scale machines and optimized the production processes – from wool fiber flakes to finished wool yarn.
The potential is great, according to the researchers. There are more than 10.4 million dogs in Germany alone. Although not all dog breeds have suitable undercoat, so far more than 1,000 tons of it end up in the garbage every year throughout Europe. Schönrock and Uhl have set up a decentralized collector network. Anyone can participate, collect the undercoat of their four-legged friend and send it to Reutlingen. The project is supported by the state EXIST start-up grant and an investment from the textile industry. The entrepreneur Anna Yona from Wildling invests in “Yarnsustain.”
Source: DITF
Indorama Mobility notes inflation for various cost items, announces price increase
Due to the COVID-19 pandemic, inflation has been notable for various cost items for Indorama Mobility Group, resulting in a general price increase effective October 1, 2021.
Cost items include:
- Utilities: gas price has tripled in the past few months in Europe (from a level of 15 EUR/MWh in Q4’20 to 45 EUR/MWh recently), while increasing by 50% in USA
- CO2 emissions and compliance cost: prices for CO2 certificates in Europe have almost doubled, approaching 60 EUR/ton from 30 EUR/ton at the end of last year, while regulations continue to expand the need for CO2 compensation
- Chemicals and additives (spinfinish, dip chemicals, coating & laminating chemicals): cost have increased by 5%
- Packaging: prices for standard packaging materials have increased by more than 30%
- Logistics: despite a local manufacturing footprint, which is not fully affected by global freight issues, regional logistics costs are also increasing up to 20% (road transport)
Source: mobility.indoramaventures.com
Study shows Celliant infrared fiber’s potential effectiveness for chronic wrist and elbow pain
Celliant, infrared responsive technology from Hologenix, has completed its 9th peer-reviewed published study. Celliant technology is a process for adding micron-sized thermo-responsive quartz, silicon oxide and titanium oxide particles to fibers.
Celliant has previously completed studies on tissue oxygen levels, recovery, sleep and pain reduction and inflammation. The most recent study focused on Celliant’s ability to increase grip strength when used in armbands on people with chronic wrist or elbow pain caused by carpal tunnel syndrome, epicondylitis or arthritis. The study was a randomized double-blind placebo-controlled trial containing 68 people. It was published in the Research Journal of Textile and Apparel.
The 68 subjects, male and female aged 21 or older, had a six-month history of chronic wrist or elbow pain and wore the armband on the affected wrist or elbow for at least 12 hours per day for 14 days. Thirty-five participants wore Celliant armband containing 42% Celliant polyethylene terephthalate (PET) fibers while 33 wore zero Celliant PET placebo armbands. Grip strength was measured by a dynamometer before and after the two-week study. The mean grip strength percentage increased over two weeks by 7.8% for the placebo group and 16.8% for the Celliant group. No adverse effects were observed.
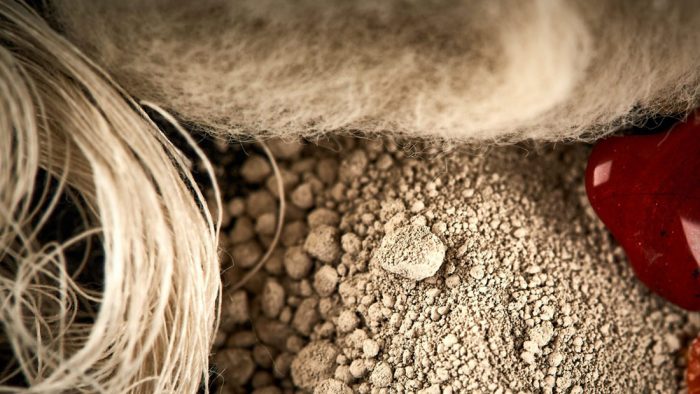
The protocol for the study was approved by the IRB of Southern California Institute for Research and Education and registered at clinicaltrials.gov. Ian L. Gordon of Veterans Affairs Long Beach Healthcare System in Long Beach, Calif., participated in the conception and design of the study, carried out subject recruitment and data collection and took part in the statistical analysis.
Seth Casden, Hologenix Co-Founder and CEO, participated in the conception and design of the study, provided materials and funding and helped draft the manuscript.
Michael R. Hamblin of the Laser Research Center, University of Johannesburg – Doornfontein Campus, Doornfontein, South Africa, wrote the manuscript and critically reviewed the data. Hamblin, who serves on the Hologenix Science Advisory Board and is a world-renowned expert on infrared and light therapy, was supported by the U.S. National Institutes of Health (NIH) grants. All authors read and approved the final manuscript.
Source: celliant.com
Unifi publishes 2021 sustainability report
Unifi, Inc published its latest sustainability report, featuring key accomplishments and highlights for 2021.
“Unifi’s commitment to environmental, social and governance responsibility is at the forefront of everything we do,” said Meredith Boyd, Senior Vice President of Technology, Innovation & Sustainability. “This latest sustainability report highlights the hard work our organization has put into the last year, making it one of our most impactful years since our founding a half century ago. We invested in technology and product development that prioritized reducing our environmental impact and took even further steps toward sustainability through enhanced transparency.”
The sustainability report includes:
- Investing in Sustainability – Unifi is prioritizing new, innovative products and processes to reduce total energy and water impacts throughout the life cycles of both Unifi’s products and those of its customers.
- Achieving Further Sustainability Scoring – Unifi’s pledge to continue using Life Cycle Assessment (LCA) on its products provides the company a pathway to further reduce the environmental impact for customers, brands, and end-consumers.
- Building the REPREVE® Portfolio – Sales of Unifi’s flagship recycled brand continue to grow quarter over quarter, emphasizing the promise to lower-impact materials.
- 2021 Diversity Champions – Unifi was honored as the 2021 Diversity Champion by the University of North Carolina School of Law’s Director Diversity Initiative, highlighting Unifi’s commitment to diversity and inclusion.
- Pursuit of Zero Waste to Landfill Manufacturing – Six of Unifi’s seven owned and operated facilities achieved zero waste to landfill.
- A Culture of Safety – Unifi’s Total Recordable Incident Rate continues to stay below 1.0, a testament to its people promoting and embracing a safe work culture.
- Alignment with Global Standards – Unifi provides in-progress Global Reporting Initiative and Sustainability Accounting Standards Board disclosure grids in the appendix of the sustainability report.
“As a global leader in textile solutions, we have a responsibility to be a vocal and engaged participant in the pursuit of a better future for people and our planet,” said Eddie Ingle, CEO. “I’m proud of the significant progress we have made over the last year, including taking further steps towards our goal of recycling 30 billion bottles from landfills in 2022. Through strategic innovation in our processes and the inherent ingenuity of our people, we’ll continue making progress towards our vision of working today for the good of tomorrow.”
Source: unifi.com
Kelheim, Hologenix to showcase Celliant viscose at Dornbirn Global Fiber Conference
Kelheim Fibers and Hologenix partnered to create Celliant viscose and will present it in a joint webinar during the Dornbirn Global Fiber Conference.
Celliant features natural, ethically sourced minerals embedded into plant-based fibers to create infrared products that capture and convert body heat into infrared for cellular oxygenation. It is suitable for performance wear, luxury loungewear, casual wear, bedding, towels and beauty, and blends with cotton, regular viscose, MicroModal, lyocell and wool.
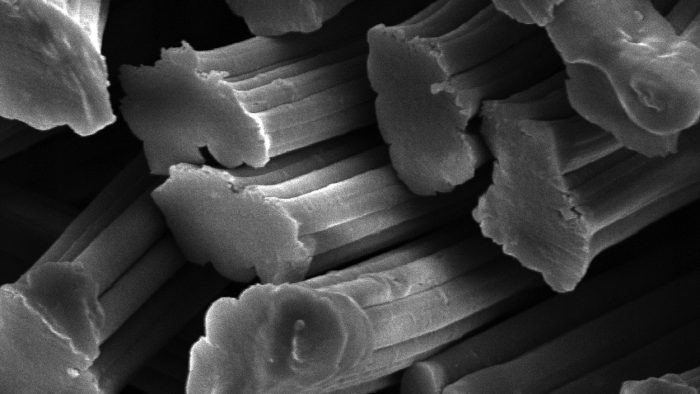
Celliant is available in Textile 1,7 dtex/40 mm, Nonwovens 1,7 dtex/40 mm, Wool 2,5 dtex/Variable Cut, and Filling/Nonwovens 6,7 dtex/60 mm.
Source: kelheim-fibers.com
Autefa Solutions supplies needle punching lines to Confidence Infrastructure
Autefa Solutions announced that it will supply two complete needle-punching Geotextile lines to Confidence Infrastructure. The scope of supply includes solution from fiber opening and blending, Double Doffer card, crosslapper Topliner with web profile control WebMax and needle punching machines Stylus NL with winders.
Confidence Infrastructure will produce 300-600gsm polypropylene and polyester nonwoven geotextile with maximum width up to 4.2m. The majority of the production will be consumed in Geobag application for erosion control.
“We chose Autefa as our partner for this project because of its proven technology in needle-punching nonwoven field,” said Shahid Islam, Sr. GM & COO of Confidence Infrastructure Ltd. “This contract is the beginning of long partnership of Confidence group with Autefa Solutions.”
Source: autefa.com
B.I.G. Yarns awarded HPR status for second European plant
B.I.G. Yarns (part of Beaulieu International Group) announced it has won FM Global’s “Highly Protected Risk” Achievement Award (HPR Award) for its yarn production facility in Komen, Belgium. The award is assigned by insurer FM Global, Beaulieu International Group’s insurance partner of five years in its ongoing efforts toward property loss prevention. The FM Global assessment considered implementation of measures to protect against fire, natural hazard, mechanical breakdown of machinery and cyber risks.
“Achieving the prestigious HPR Award recognizes the commitment of the teams at B.I.G. YARNS and the wider Beaulieu International Group to proactive risk management and contingency planning to ensure the safety and protection of our workplaces,” said Emmanuel Colchen, General Manager B.I.G. Yarns. “Safeguarding property is a key element in enabling us to provide business continuity for our customers in demanding sectors like automotive, commercial contract and residential flooring.”
The Komen production facility is the fifth plant at B.I.G. Yarns to receive HPR status.
Source: beaulieuyarns.com
Researchers produce spider silk fibers from engineered bacteria
Spider silk is said to be one of the strongest, toughest materials on the Earth. Now engineers at Washington University in St. Louis have designed amyloid silk hybrid proteins and produced them in engineered bacteria. The resulting fibers are stronger and tougher than some natural spider silks.
Their research was published in the journal ACS Nano.
To be precise, the artificial silk — dubbed “polymeric amyloid” fiber — was not technically produced by researchers, but by bacteria that were genetically engineered in the lab of Fuzhong Zhang, a professor in the Department of Energy, Environmental & Chemical Engineering in the McKelvey School of Engineering.

Zhang has worked with spider silk before. In 2018, his lab engineered bacteria that produced a recombinant spider silk with performance on par with its natural counterparts in all of the important mechanical properties.
“After our previous work, I wondered if we could create something better than spider silk using our synthetic biology platform,” Zhang said.
The research team, which includes first author Jingyao Li, a PhD student in Zhang’s lab, modified the amino acid sequence of spider silk proteins to introduce new properties, while keeping some of the attractive features of spider silk.
Read the full story: https://source.wustl.edu/2021/07/microbially-produced-fibers-stronger-than-steel-tougher-than-kevlar/
Source: source.wustl.edu
SPESA to host Executive Conference Oct. 27-28 in Boston
The Sewn Products Equipment and Suppliers of the Americas (SPESA) will host its annual Executive Conference Wednesday, October 27-28 at the Omni Parker House in the heart of downtown Boston. The two-day event is themed “Riding the Momentum.” This is the first in-person Executive Conference SPESA has hosted since its 2019 version, which took place in New Orleans. Last year’s event was held virtually.
According to SPESA, this year’s Executive Conference will take place at an important time in history for the sewn products industry, as the industry has experienced a surge of momentum over the past two years as it adopted new technologies, mended supply chains, and developed more flexible manufacturing strategies in response to the COVID-19 pandemic. Through a combination of keynote addresses and panel discussions, the conference will aim to discuss how the industry landscape has shifted over the past few years, while also doing a deep dive into where the industry is headed next.
As a new feature this year, SPESA will be hosting an offsite tour to a local manufacturing facility on Thursday, October 29. This optional activity is a value-add for member and non-member registrants interested in attending.
Registration for the Executive Conference is currently open. As an added member benefit this year, SPESA members are being offered a discounted registration rate of $645. The non-member registration rate is $695. Registration for both members and non-members includes all education, the offsite tour, and networking events on the evenings of October 27 and 28. A spouse rate of $245 is also available, which includes access to both networking events on the evenings of October 27 and 28.
SPESA is offering a limited-time discount of $50 on all event registration through September 15, 2021. Registrants will be asked to use code “Boston” at checkout to receive the discount.
A full agenda for the Executive Conference will be available soon at spesa.org.
Source: spesa.org
INDA announces finalists for 2021 RISE Innovation Awards program
INDA, the Association of the Nonwoven Fabrics Industry, announced three finalists for its RISE Innovation Award, which will be presented during the 11th edition of the Research, Innovation & Science for Engineered Fabrics Conference, (RISE®) to be held virtually September 28-30, 2021. The award recognizes novel innovations in the nonwovens industry that creatively use next-level science and engineering principles to solve material challenges and expand the usage of nonwovens and engineered fabrics. The three finalists will present at the RISE conference as they compete for the Innovation Award. Finalists are:
Canopy Respirator
Canopy is an innovative respirator that is fully mechanical, non-electrostatic, with a filter designed for superior breathability while offering the wearer facial transparency. The breakthrough respirator features 5.5mm water column resistance at 85 liters (3 cubic feet) per minute, two-way filtration, and a pleated filter that contains over 500 square centimeters of surface area. The patented Canopy respirator resists fluids and eliminates fogging of eyeglasses.
Evalith 1000 Series
Johns Manville’s innovative Alpha Binder is a formaldehyde-free, high bio-carbon content, toxic-free binder formulation ideal for carpet mat applications. Alpha Binder eliminates monomer and polymer synthesis, uses a bio-degradable catalyst, and requires 70% less water in manufacturing. The resulting glass mats made of Alpha Binder are named “Evalith 1000” and reduce energy consumption during manufacturing by over 70% compared to alternative petroleum-based binders. Evalith 1000 was commercialized in North America in 2020.
Fiber Coated, Heat Sealable, Breathable, Hybrid Membrane, Fabric Protection
TiGUARD protective fabric is a construction of monolithic or hybrid imperious/moisture-eliminating membranes with a surface covered with micro-fiber. This nonwoven product is a multi-layer all polyester fabric specifically for chemical and microbial protective fabrics, products, and garments. It is constructed of compatible heat seal-able materials, which lend themselves to high-speed heat sealable production and ultimately automated manufacture of garments without sewing. It is a combination of a densely flocked polyester fiber surface on polyester membrane supported by polyester scrim.
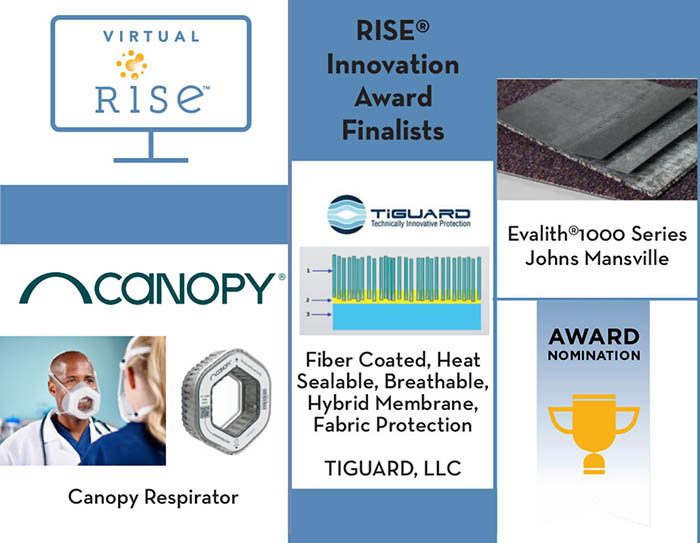
Virtual RISE conference attendees include technology scouts and product developers in the nonwoven/engineered fabrics industry seeking new developments to advance their businesses. These attendees will electronically vote for the recipient of the 2021 RISE® Innovation Award, on Wed. Sept. 29th. The winner will be announced Thurs., Sept. 30th.
Industry experts on INDA’s Technical Advisory Board selected three finalists from among 20 nominations. The 22-member board of technical professionals is represented by companies such as Absorbent Hygiene Insights LLC, Attindas Hygiene Partners, Berry Global, Cotton Incorporated, Crown Abbey, LLC, The DAK Group, Fi-Tech, Inc. Freudenberg Performance Materials, Jacob Holm, Lenzing Fibers, Inc., Natureworks LLC, Nice-Pak Products, Inc., Nonwovens by Design, Norafin (Americas) Inc., North Carolina State University, Poccia Consulting, LLC, The Procter & Gamble Company, RKW North America, Inc., Rockline Industries, Smith, Johnson & Associates, Suominen, and Texas Tech University.
In 2020, the RISE Innovation Award was presented to The Nonwovens Institute for their Spunbond High Efficiency Filter.
Source: riseconf.net
* International Fiber Journal is owned by INDA, Association of the Nonwoven Fabrics Industry (inda.org).
Kelheim Fibres to increase viscose fiber prices on Oct. 1
While Kelheim Fibres GmbH reported that it has been successful in limiting the impact of the pandemic on fibre production, it is increasing prices for its range of viscose fibers by €0,20/kg as of Oct. 1, 2021.
As a company operating its own cogeneration energy plant and with a high level of export business outside Europe, Kelheim said cost factors have had a severe negative impact on margins during the second and third quarters of 2021. With energy costs set to remain at unprecedentedly high levels and potentially increase further in the fourth quarter, no relief to the high level of freight costs foreseeable, and raw material costs also remaining at a high level, the company needs to take steps to prevent further margin erosion.
Kelheim Fibres GmbH is therefore announcing that with effect from Oct. 1, 2021, or as contracts and agreements allow, prices for its range of viscose fibres will be increased by €0,20/kg. In addition, freight cost adjustments will be applied on an individual customer basis. In cases where energy cost adjustments are not included in contracts and agreements, a temporary energy surcharge will be applied.
“The measures we are taking are absolutely necessary to ensure that Kelheim Fibres remains in a position to supply fibres with the levels of quality and service expected by our customers,” said Matthew North, commercial director for Kelheim Fibres.
Source: kelheim-fibres.com
Sateri announces all of its viscose mills in China are now EU-BAT BREF compliant
All of Sateri’s five viscose mills in China are now fully compliant with the emission limits set out in the European Union Best Available Techniques Reference Document (EU-BAT BREF) on Polymers, following recent verification of Sateri Jiangsu and Sateri China mills.
Verified by independent consultant Sustainable Textile Solutions (STS), a division of BluWin Limited (UK), the parameters assessed included resource utility efficiency, wastewater discharge and air emission.
Allen Zhang, president of Sateri said, “Sateri Jiangsu was established in 2019 following an acquisition while Sateri China was built in the same year. We had aimed to have both mills meet EU-BAT’s recommended emission levels by 2023. To achieve this two years ahead of schedule underscores our continuous efforts in process improvement and control of pollutant emissions, and resource utilization efficiency. We will continue to pursue manufacturing excellence and invest in best-in-class technologies for all our mills – existing, acquired, and newly constructed ones – as part of our Vision 2030 commitment towards closed-loop and cleaner production.”
Source: sateri.com
Aurora Specialty Textiles hosts Congresswoman Lauren Underwood & U.S. Trade Ambassador Katherine Tai to discuss infrastructure investment
Aurora Specialty Textiles Group welcomed Congresswoman Lauren Underwood (IL-14) and United States Trade Representative Ambassador Katherine Tai to Aurora’s Yorkville, Illinois, manufacturing plant. The visit included a tour of Aurora’s operations and was tied to the Bipartisan Infrastructure Investment and Jobs Act, which has passed the United States Senate and is pending for vote in the House of Representatives. The bill would include support across Illinois communities for public transit, improvements to roads and bridges, infrastructure for clean drinking water, electric vehicle support, and improved passenger and freight rail and programs.
“It was an honor and privilege to host these two accomplished and pioneering women to Aurora Specialty Textiles,” said Marcia Ayala, president of Aurora Specialty Textiles Group. “It was a great event and the discussion was enlightening as we shared the concerns and challenges manufacturers and employees face today.”
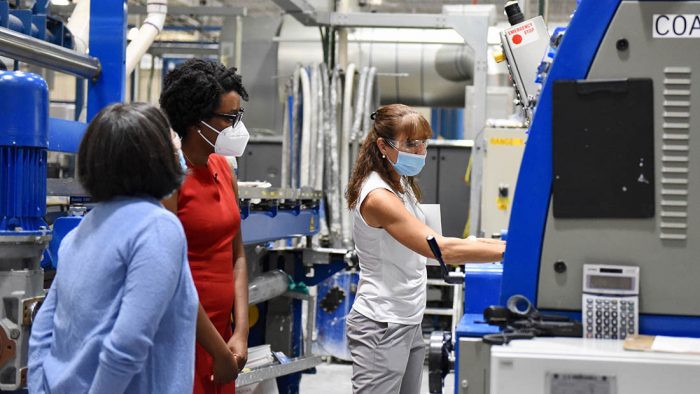
During the visit, Congresswoman Underwood and Ambassador Tai held a roundtable discussion that featured women-led manufacturing firms and union representatives from the Illinois 14th Congressional District. The event was hosted by Ayala and Bruce Pindyck, the chairman and CEO of Meridian Industries, Aurora’s parent company.
In addition to Marcia Ayala, manufacturing leaders who attended the round table discussion included Patricia Miller, CEO of Matrix 4; Chandler Slavin-Bond, Owner Doran Manufacturing, Inc.; Gina Lipscomb of RJ Lipscomb Engineering; and Nicole Wolter, president of H. M. Manufacturing. Brian Simmons, Gladys Campos and John Gedney represented regional labor unions and their employees. David Boulay, president of the Illinois Manufacturing Excellence Center also participated.
“We discussed the bipartisan infrastructure bill and other initiatives beneficial to U.S. manufacturers that Congresswomen Underwood and Ambassador Tai are working on,” said Ayala. “It was a great opportunity to give our perspectives on issues currently facing manufacturers and issues specific to our businesses,” Ayala added. “The Congresswoman and Ambassador were very interested to learn about the challenges we face running our businesses and to discuss how those problems can be addressed through legislation and trade policies.
”During the event’s roundtable discussion, Ambassador Tai said she is touring U.S. manufacturing companies to learn what manufacturers need in terms of trade policy. The roundtable discussion also covered questions and concerns related to infrastructure, supply chain, the lack of a skilled workforce, women in manufacturing, climate change and the post-COVID economy.”
Source: auroratextile.com
Textile Exchange releases 2021 global fiber market report
According to a new report by Textile Exchange, global fiber production, hit by the COVID-19 pandemic, decreased from 111 million tonnes in 2019 to 109 million tonnes in 2020 after years of growth.
While overall fiber production declined in 2020, the market share of what Textile Exchange describes as preferred fiber and materials is increasing. But even with this growth, preferred fibers still only represent less than one-fifth of the global fiber market. This number includes – in descending order:
- Recycled polyester (8.4 million tonnes), preferred cotton as defined by a list of recognized standards (7.8 million tonnes)
- FSC/PEFC certified manmade cellulosic fibers (~3.9 million tonnes)
- Other recycled and biobased fibers produced according to recognized standards (0.57 million tonnes).
The market share of recycled fibers increased from 6.9% in 2016 to 8.1% in 2020 – with the majority (7.6%) coming from recycled PET bottles – and only a minor part (0.5%) from other recycled feedstock.
Overall, less than 0.5% of the global fiber market was from pre- and post-consumer recycled textiles in 2020. The increase of the preferred fibers market should not make us forget that the overall fiber and materials market continues to grow and with this also its overall impacts.
Global fiber production has almost doubled in the last 20 years from 58 million tonnes in 2000 to 109 million tonnes in 2020. While it is not yet clear how the pandemic and other factors will impact future development, global fiber production is expected to increase by another 34% to 146 million tonnes in 2030 if the industry will build back business as usual. In absolute numbers, virgin fossil-based fibers also increased from 55.7 million tonnes in 2016 to 59.7 million tonnes in 2020.
View the full report: https://textileexchange.org/wp-content/uploads/2021/08/Textile-Exchange_Preferred-Fiber-and-Materials-Market-Report_2021.pdf
Source: textileexchange.org