In the last five years, smart yarn technology has gone from being an enabler of smart materials to being the carrier – and the dispenser – of intelligence in wearables. And, nowhere more so than in the health and wellness sector. This is certainly a boon for yarn manufacturers, but it is also a time of risk with significant progress being made by a disrupter in the market. Here, we look at some of the key innovations emerging and consider their likely trajectory in the short- to medium-term, taking account of challenges and opportunities. In concluding, we look at overall challenges and opportunities, including that of the already present disrupter.
The changing research and development landscape
In the early days of smart materials dating back to the 1990s, the technologies were being dismissed as ‘answers looking for questions.’ This was not entirely unfounded as anyone who remembers the thermochromic T-shirt that loudly proclaimed underarm sweat will attest to! In the rush to file patents there was sometimes a lack of consideration of how the idea might be scaled up for manufacturing. Admittedly, this is not a primary function of the patent process, but it is one of the reasons that patents once granted often failed to commercialize. This is changing as is evident not just in the language of the patents filed but in the academic research papers and funding applications that usually precede this. The language is becoming more directed in laying out the path to the consumer product. Whether it is driven by or is a driver of this trend, the smart yarn for health and wellbeing applications has undoubtedly become more detailed and specific in its characteristics, means of production, use and future potential.
For fiber and yarns, the research institute has become a key enabler. They are a bridge between pure research and the manufacturer with a firm eye on scale for commercialization from a very early stage. The facilities offered include their own research lab as standard, but alongside this is often a suite of capabilities that can include testing facilities, familiarization with standards both local and global, prototyping facilities to test not just the yarn but the whole process of manufacturing to scale, and a network of manufacturers across the value chain. Examples for illustrative purposes are the German Institutes of Textile and Fiber Research (DITF) and, in Switzerland, Empa.
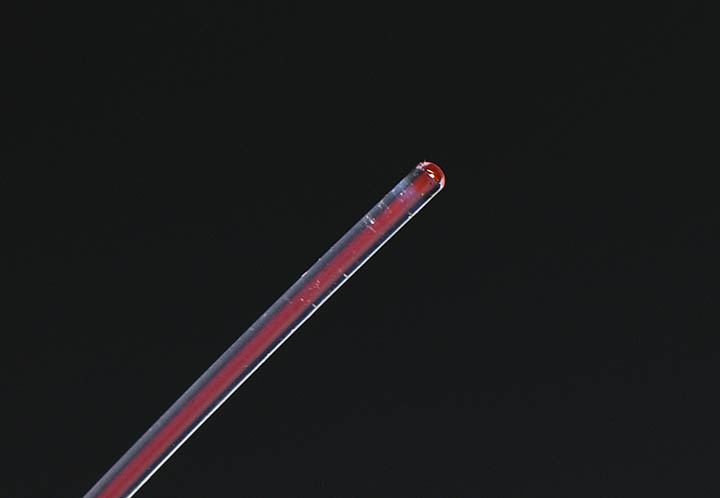
Researchers at DITF have developed a sensoric yarn that has the capability to offer areas of different capacitive sensitivity within the yarn. It is suited for integration in firefighter jackets or babies’ bodysuits to offer more precise information on location when activated. The yarn is produced by wrapping fine conductive wires around a conventional yarn so that the mechanical properties of the conventional yarn remain essentially unchanged and the fine wires do not have to bear any load in the finished textile. Such yarns, when configured to suit the application, can be processed in a standard textile manufacturing processes without sacrificing productivity.
Whether it is driven by or is a driver of this trend, the smart yarn for health and wellbeing applications has undoubtedly become more detailed and specific in its characteristics, means of production, use and future potential.
Nearly any yarn and any wire material can be used in this process. Capacitive and resistive sensory textile structures can be produced in this way and used to record a wide range of measured variables. The use of capacitive textile structures has the significant advantage that an electrical contact only has to be made at one point. The aim of a research project is to create zones of different capacitive sensitivity within a single yarn. In this way, it is possible to measure not only whether the yarn has been touched, but also where. For this reason, the winding parameters are varied sequentially, and sequential coatings applied. The requirements are determined and known coating processes are combined and modified in such a way that the desired properties of the yarns can be set differently in different zones.
Empa have developed melt-spun filaments with a liquid core using the rationale that with bicomponent melt-spinning, several functionalities could be combined in one fiber. They envisaging three potential fields of applications: remote stress and strain sensors, microhydraulic elements within very restricted space, and fragrance-releasing fibers for improved ambience. The institute reports that the first industrial upscaling trials have proven very promising.
Conventionally, the filling of fine hollow fibers with a liquid is seen as becoming increasingly slow and uneconomic with the move to extended filament lengths. Empa researchers chose another approach to supply the polymer from single-screw extruder and gear pump, with a high-pressure syringe pump injecting the core fluid immediately during production. A process that has more than a passing resemblance to the food industry. Liquids in the core of a synthetic filament have the potential to provide novel qualities without compromising mechanical properties, dyeability or washability.
Empa have already shown the technique offers promising properties regarding damping, flame retardancy, perfuming and sensing. “In terms of optically conductive polymer fibers, we’ve tried all kinds of things,” says Rudolf Hufenus, Empa R&D manager. “But even with the best solid fiber cores, we can never achieve such elasticity as with our liquid-filled fiber.” The special combination of optical and mechanical properties could now open up new markets for Empa’s two-component fiber.
Over the past seven years, the Advanced Fibers lab in St. Gallen has been home to a machine that can produce kilometer-long fibers filled with a liquid. With this expertise, Empa is a world leader. “Two-component fibers with a solid core have been around for more than 50 years,” says Hufenus. “But fabricating a continuous liquid core is considerably more complex. Everything has to be just perfect.”
The fiber is extremely stretchable, and can measure how far it has been stretched. Hufenus and his team added a small amount of a fluorescent dye to the glycerol and examined the optical properties of this luminescent fiber during the stretching process. The result: When the fiber is stretched, the path of the light is lengthened, but the number of dye molecules in the fiber remains constant. This leads to a small change in the color of the emitted light, which can be measured using suitable electronics. Thus, the liquid-filled fiber can indicate a change in length or a tensile load that is occurring.
Refining and extending smart fiber capabilities
At this year’s Techtextil trade show in Frankfurt, one of the key trends for smart yarns was the level of refinement and the extension of capabilities for the health and wellbeing sector in particular. Noble Biomaterials Circuitex yarn is already one of the most successful of these comprised of 99.9% pure silver that is permanently bonded to the surface of nylon or other non-conductive polymer. The result is a pure silver surface area with a number of grades available depending on the application requirements. It offers softness, is lightweight and flexibility making it easy and comfortable to integrate into the fabric for detection, monitoring, and the transmission of data into the garment or product.
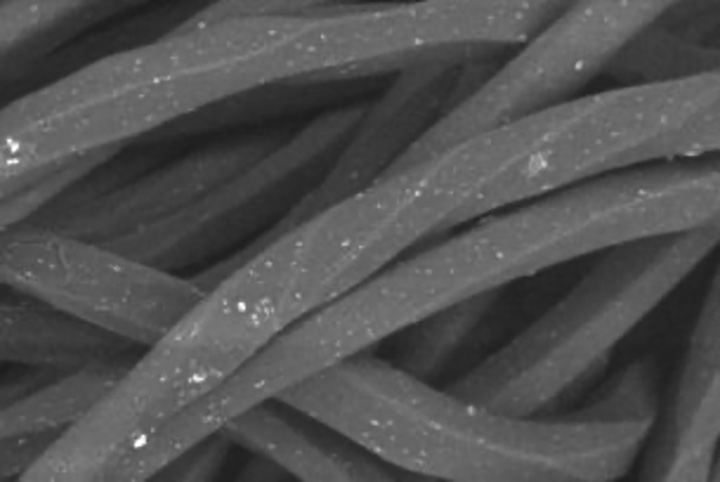
In medical applications, it can be knitted or woven into smart diagnostic garments and used to sense and transmit electrophysiological signals to a healthcare professional or data analysis app. In consumer health and wellness apparel, Circuitex can be used for collecting data, delivering stimulus, storing energy, or controlling temperature, among other things. It can be used to sense and transmit electrophysiological signals such as electroencephalogram (EEG), electrocardiogram (ECG), and polysomnography (PSG). In the role of biometric monitoring, it can detect and transmit information about sleep patterns and weight distribution or can alert healthcare professionals about hot spots on patients who are confined to a bed or wheelchair.
Healthcare Associated Infections (HAIs) are one of the world’s leading healthcare challenges with infections leading to significant levels of morbidity and mortality each year. Noble Biomaterials produce anti-microbial fibers and yarns with their Ionic+ technology that works by the release of silver ions to fight microbes on soft surfaces. The ion release is activated by the presence of moisture, such as moisture vapor naturally emitted by the skin, working to inhibit and eliminate microbes on the surface of the product, protecting it from microbial impacts.
Noble Biomaterials offers three levels treatment in their portfolio of products, from consumer to healthcare to wound care. Ionic+ Antimicrobial Advantage is used in healthcare applications to inhibit the growth of microbes on the surface of fabrics including drug-resistant bacteria and viruses providing clinical-quality antimicrobial performance. In advanced wound care applications, silver can help to prepare the wound for closure by managing the microbial contamination at the surface. Ionic+ for Infection Management & Healing uses silver-based antimicrobial technology used for mission-critical healthcare applications, including advanced wound care.
Noble Biomaterials currently holds multiple FDA approvals for advanced wound and burn care dressings. The products provide a sustained release of silver cations for broad spectrum coverage and high versatility, allowing dressings to be used for indicated wound applications such as partial thickness burns, incisions, skin grafts, donor sites, lacerations, abrasions, and Stage I-IV dermal ulcers (vascular, venous, pressure and diabetic).
The disruptor
The future competition in the health and wellbeing yarn market may come from outside the fiber industry. The 3D printing technology has already moved into areas that were not anticipated even a few years ago, and they may well pose the biggest market challenge to the yarn industry in high value applications such as medical, health and wellness.
Researchers at POSTECH and UNIST are making advances in the development of a wearable sensor patch that is thinner than a human hair and the capability of measuring pulse wave signals with a high level of precision using inkjet printing technology. The fineness of the print means that although referred to as a ‘patch’ and printed onto a substrate – making it effectively a fiber by virtue of its scale.
In an interview in Printed Electronics Now, Klaus Hecker, managing director of the OE-A, commented that “COVID boosted the interest for medical applications such as smart patches to monitor vital parameters,” reflecting what he sees as a growing interest in healthcare applications.
The importance of the pulse wave as a bio signal is as an indicator of cardiovascular health and is used in the diagnosis of cardiac conditions including high blood pressure and arteriosclerosis. As with many wearable medical devices user comfort is an issue with conventional pulse wave measuring devices requiring the wearing of a blood-pressure measuring cuff, or stiff tong-shaped sensor making them cumbersome. In this development, the research team have fabricated a pressure sensor that mimics skin’s tactility.
“The newly developed technology allows for at-home diagnosis of diseases that are usually performed only at hospitals,” according to Professor Sung-Min Park of POSTECH, who sees its future potential. “It can be used for medical applications such as pre-diagnosis of cardiovascular diseases and arterial catheter injections in daily life.” The device contains one hundred sensor pixels used to obtain a two-dimensional pressure map on the wrist with sensor patches of different sizes to take account of age, gender and body sizes for a customized design and fit.
The flexible hybrid electronics (FHE) industry already has its eye on the medical market. In a December 2021 interview in Printed Electronics Now, Klaus Hecker, managing director of the OE-A commented that “COVID-19 boosted the interest for medical applications such as smart patches to monitor vital parameters,” reflecting what he sees as a growing interest in healthcare applications. The FHE and textile industry have long been regarding one another with interest. Now would seem a really good time to establish a more formal cooperation.