Sai Aditya Pradeep is pursuing a Ph.D. in Automotive Engineering in the Materials and Manufacturing Specialization at Clemson University where he is conducting research on the scalable production of thermoplastic nano-cellular foams via supercritical fluid assisted injection molding. Another important area of Pradeep’s research is the characterization of recycled nonwoven carbon fiber composites and development of material models in order to accelerate their adoption by the automotive sector.
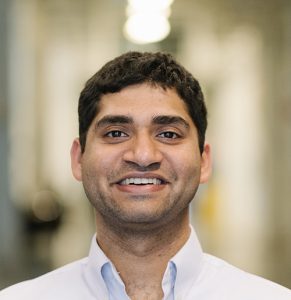
3rd Year, Ph.D. Student
Clemson University
Automotive Engineering (Materials and Manufacturing)
Clemson Composites Center
Pradeep was exposed to these topics during his work as a research assistant during his master’s program where he had some exposure on processing and characterization of polymer blends and composites. During this time, he developed a keen interest in working on the challenges faced by bio-based and recycled materials and their adoption in industry.
Research overview
Pradeep’s research is focused on accurate characterization and development of material models of recycled carbon fiber nonwoven composites and how this, in conjuncture with FEA simulations, can be employed to identify automotive applications for this system in dynamics crash like environments.
A major motivation for this research stems from two issues:
- A significant amount of scrap is generated by the aerospace sector during their traditional composites manufacturing process posing an environmental concern; and
- The fact that these have been designed from a stiffness critical objective.
One value proposition for this scrap is using these relatively low-cost raw materials that are extremely attractive for automotive lightweight applications, since most components designed are stiffness critical. However, major issues with adoption of these materials are supply chain, historical knowledge for design & processing, and the lack of accurate material models.
Pradeep’s work tackles the issue of lack of material models by processing and systematically characterizing microstructure (CT Scan) mechanical (tensile, shear, compression) and thermal (DSC, TGA and CTE) properties of these nonwoven composites in comparison to traditional long fiber injection (LFT) molded composites.
Theoretically these nonwoven composites should exhibit isotropic behavior due to random directionality of the carbon fibers. However, the CT scan images revealed a notable degree of directionality as a result of the combing and manufacturing process. Overall, the nonwoven composites provided better mechanical and thermal properties across the board, while having similar costs when compared to LFT composites.
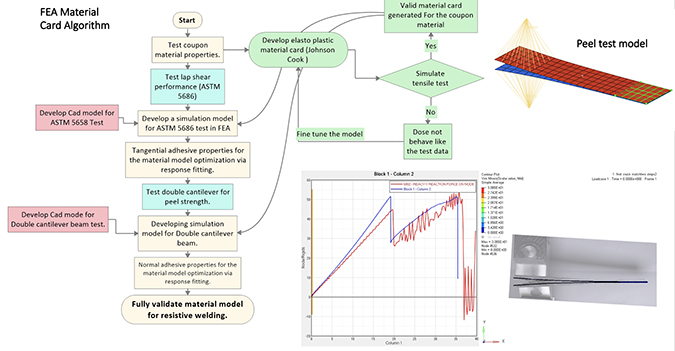
Finally, in conjunction with a colleague, these properties were used to develop and validate a MAT 59 nonlinear FEA material card that was used to simulate the crash performance of the nonwovens at a systems level.
These findings are extremely compelling for the use of nonwoven composites in dynamic crash-type environments for use as secondary structural parts. Furthermore, these results help understand the unique mechanical and thermal properties that these nonwovens composites possess and the value proposition they hold in the automotive sector.
Theoretically these nonwoven composites should exhibit isotropic behavior due to random directionality of the carbon fibers. However, the CT scan images revealed a notable degree of directionality as a result of the combing and manufacturing process.
Career goals
Pradeep is currently working towards completing his Ph.D. within the next year. His Ph.D. research focuses on the scalable production of thermoplastic nano-cellular foams via supercritical fluid assisted injection molding, geared for automotive application. His Ph.D. research has garnered awards at the Annual Automotive Composites Conference & Exhibition and prestigious Thermoplastic Elastomers Special Interest Group scholarship by the Society of Plastics Engineers.
Pradeep is currently engaged in a project with the Department of Energy (DOE) and Honda Research & Development Americas (HRAO), focusing on an Ultra-lightweight Carbon Fiber Reinforced Thermoplastic Composites Door Assembly. He has published two first author journal articles, two book chapters and co-authored three journal articles related to his master’s research and foaming in bio-based thermoset systems.
Pradeep has also interned at Apple, Inc., working on next-generation touch sensor technology in the panel processing and optics department. Upon completion of his Ph.D. he is extremely keen on working in Polymer R&D space focusing on either automotive or consumer electronics sectors.