Stadium roofs made from high-tech membranes, fiber-reinforced concrete, geogrids crafted from polyester in road construction and nonwovens for insulating or roofing. Textiles have long been an integral aspect of the construction sector and play an innovative role as the “fifth construction material” – alongside steel, concrete, wood and glass – and also feature in the technological quality solutions supplied by Oerlikon’s Manmade Fibers business unit.
The very first textile construction project is almost as old as humanity itself, but already revealed – and still reveals – some of the central benefits of the material used: the tent. Light and flexible, suitable for covering large areas and, depending on its composition, light- and air-permeable – the properties of this archaic mobile housing are also factors in one of the construction materials of the future. Even today, so-called textile membranes enable impressive architectural ventures, including the stadiums for the UEFA Euro 2012 in Warsaw and Kiev, and Bangkok’s international airport.
Their outer skin, or roofing, deploys specially coated polyester or fiberglass fabrics. These flexible, highly durable materials permit not just new forms of architectural expression and moving constructions. Combined with PVC, PVDF or PTFE coatings, with insulating materials or as multi-layer systems, they also provide tailor-made heat and fire protection and can even be dirt-repellant. Membrane constructions can also be used as secondary building layers or for thermal refurbishment – with corresponding, also publicly funded, development projects already under way.
This example clearly demonstrates that construction textiles offer innovation potential – and hence also market potential. To this end, the increasing utilization of textile materials within the construction sector alone is predicted to generate annual global growth rates of between 5 and 8 percent for industrial textiles. The U.S. market researchers at the Freedonia Group predict annual global growth of 8.3 percent for so-called geo-textiles or geo-plastics used in civil engineering and waterway and road construction.

Oerlikon Barmag technologies have also been able to contribute towards this development. To this end, the Remscheid-based market leader for manmade fiber spinning systems and texturing machines offers special low-shrinkage systems for polyester fabrics with PVC coating, as in the sample application of membranes mentioned above. In conjunction with modern HF godet systems, these systems permit the spinning of evenly drawn, break-resistant and (super) low-shrinkage industrial yarns with titers of up to 18,000 denier per position. Similarly highly productive, multi-end and energy-saving machine concepts for yarns with maximum titers of up to 18,000 denier permit the manufacture of high-tenacity polyester yarns for so-called geogrids.
These stable, woven geo-plastics are water-permeable and – in road construction – are used above all for stabilizing the subsoil. As a reinforcement for asphalt, for instance, and as filter and drainage elements, as a separating layer between sand and gravel, or for anchoring embankments, dams and supporting walls – these strong fibers excel above all with their uncomplicated and, hence, cost-efficient processing. Due to the fact that their reinforcing character permits a reduction in the excavation depth of the carriageway substructure and the volume of the base layer material including transport costs and construction times, geogrids are becoming increasingly interesting for deployment on difficult-to-access terrain or in large countries such as China, India and Russia – particularly in view of the fact that the tear-resistant yarns also reduce long-term maintenance costs. The final application requirement decides which types of geotextile provide the optimum properties.
The company also supplies systems for woven, fibrillated polypropylene tapes with the highest tenacities – in excess of 7.5 grams/den – available on the market, which can also be used in road and railway track construction, tunnel protection or soil reinforcement for coastal and riverbank protection. “With the support of partners, we can offer the entire process chain for manufacturing these materials,” said Senior Expert R&D Industrial Yarn Machines at Oerlikon Manmade Fibers, Stefan Becker.
Four-Fold Load-Bearing Capacity: Textile-Reinforced Concrete
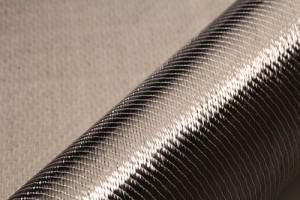
Oerlikon Barmag also has a special winder for one of the most promising textile materials of all: WinTrax supports the efficient production of carbon fibers of the very highest quality with simultaneously perfect package build. The light and extremely high-tenacity carbon fibers are not only superlative when used in vehicle and aircraft construction, they are also increasingly replacing strengthening steel in so-called textile-reinforced concrete. This not only reduces corrosion problems in the construction sector, it also increases fire safety at the same time. Textile reinforcement with two- or three-dimensional fabrics made from fiber glass or carbon fibers can also be considerably thinner – a huge benefit for structural design freedom when looking at filigree buildings. This is shown at the longest textile-reinforced concrete bridge in the world, which was opened in 2010 in Albstadt, in southern Germany. Nevertheless, just one layer of carbon fibers in concrete can quadruple the load-bearing capacity. Structural approval for utilizing carbon fibers in textile-reinforced concrete is expected to be issued in the near future. As soon as the first approval is available, additional approvals will follow, paving the way for broader applications.
Stomping Ground For Innovation: Nonwovens
A completely different breed of textile materials is also perfect for utilization in concrete – and not just here: that is, nonwovens. Since 2002, these diverse textile fabrics have seen something of a stratospheric rise with six percent annual growth in terms of its utilization for geo-textiles. According to expert reports from the organization ‘Bayern Innovativ,’ the construction sector was conversely the second-largest purchaser of nonwovens in 2010 with 18.2 percent of the overall market – just behind the cleaning cloth market. This cross-fertilization with the development of innovative products and the opening of new applications for the construction industry will ensure even wider utilization and greater demand over the coming years.
Important driving forces behind this trend are the increasing orientation of the construction industry on topics such as heat preservation, energy consumption and (sound) insulation including the corresponding legal guidelines. Even in thin layers, polyester nonwovens, for example, protect – as in the case of functional textiles – against overcooling and absorb very little moisture. They also easily adapt to roof constructions and are quick and easy to use as insulating materials and to replace, render or cover cracks in façade systems and can also benefit impact insulation. In both refurbishments and new-builds, they are therefore an excellent alternative to foams, glass and mineral wool, particularly in view of the fact that these materials frequently lack the required flexibility for optimum sealing. Not least, nonwovens are resistant to environmental influences and can be recycled to a high extent.
Flexible textiles have a very promising future – and are also entering the high-tech sector. To this end, the company already has smart nonwovens, which integrate conductors or conducting materials. In the case of “intelligent floors,” they can automatically – by means of sensors – activate lights and are able to register the fact that a senior citizen has fallen over in a retirement home.
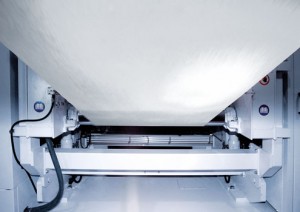
Roofing: Trend Towards Spunbonds
In terms of industrial nonwoven applications, so-called roofing currently has the lion’s share of the global market with in excess of 420,000 tons per year. On the one hand, this application focuses on calendered polypropylene spunbonds, which are laminated with a breathable PP film and inserted between roof tiles and the load-bearing wood construction. In addition to these roofing underlayment membranes, bitumen roofing as a cover layer is predominantly used for flat roofs. The material comprises needle punched and heat-set PET spunbond that has been treated with an acrylic binder.
These nonwoven applications excel as a result of a series of functional properties: they provide a moisture barrier, but are nonetheless air-permeable and resistant to mold and mildew as well as being stable in terms of their dimensions and temperature; they can be installed easily onsite and be glued or welded together; they are resistant to fatigue, impact and penetration as well as resilient to debonding, and work well with standard paints and lacquers.
With systems and equipment for manufacturing substrates for bitumen roofing membranes, for roofing underlayment and also for geo-textiles, Oerlikon Neumag, one of the leading suppliers of nonwoven technologies, offers the complete spunbond process – from polymer granulate all the way through to rolled goods. “The combination of effectiveness, productivity and nonwoven product is particularly innovative in the case of the spunbond process. In terms of the system width, the company’s machines are not just able to produce up to four times more material, they also help cut operating costs for energy and maintenance and save on operating staff costs,” explained Dr. Ingo Mählmann. The Oerlikon Manmade Fibers Business Development Manager for Nonwovens sees growing opportunities for spunbonds within the construction sector, also because they are particularly inexpensive to manufacture: “The trend is very clearly moving towards utilizing spunbonds, also as a substitute for fiberglass products. Bitumen roofing and geo-textiles are perfect examples of this, but this trend fundamentally also applies to many other construction nonwovens, such as those used for reinforcement or drainage.”