Since 2019, Säntis Textiles has been producing around 300-350 tons of 100% recycled cotton monthly using specially-developed RCO100 technology at the plant of its partner Kipas in Kahramanmaras, Turkey.
The technology has been under development since 2016 and was commercially launched for third-party manufacturers by a second Kahramanmaras-based company, textile machinery builder Temsan, at ITMA 2023 in Milan in June.
“Our main business is still technical and home textiles, but since 2010 we have worked on recycling, initially with polyester and from 2016 with cotton,” explained Stefan Hutter, owner of Säntis Textiles, which is headquartered in Singapore and now has a branch office in Switzerland. “Recycling will be a significant pillar for us going forward and for me it’s like the closing of a circle.
“The challenge of developing the technology for 100% cotton recycled yarns and fabrics took us initially to China where we did trials with different machine modules and moved them around until we obtained some first encouraging results. It took us about two years until we were able to produce denim fabrics and some chinos and knits out of 100% recycled cotton.”
Kipas
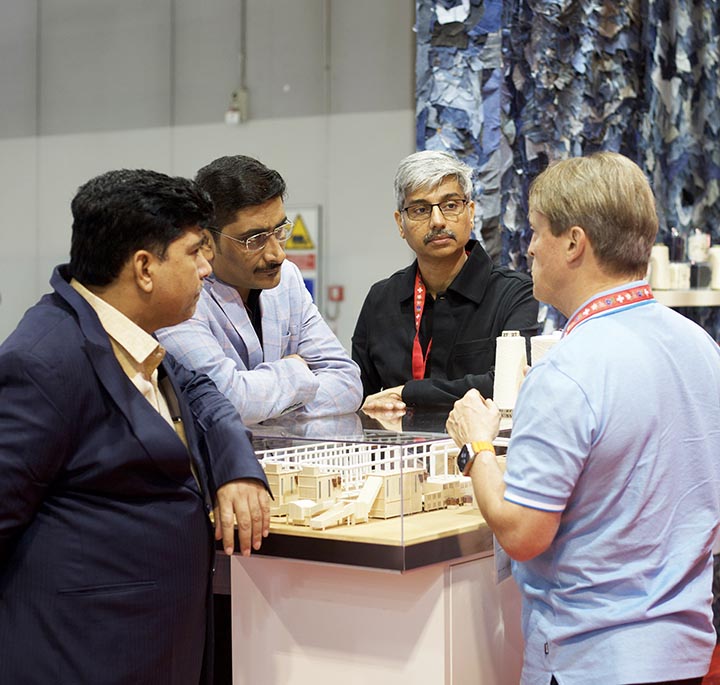
Säntis then moved the project to Kipas where the first full RCO100 recycling system was installed.
Kipas Holding is a conglomerate of 25 companies with more than 10,000 employees and annual sales of more than $100 million. Its textile operations have an annual capacity of 400,000 tons of yarn and 100 million meters of woven fabrics, with an emphasis on denim.
“Kipas is fully vertical, with spinning, weaving, dyeing and finishing under one roof and is also a major denim producer,” Hutter explained. “Kipas then introduced us to Temsan which is in the same region and this made development of the project very fast. If something was needed or had to be changed on the machine, the guys from Kipas would go over to Temsan immediately to look at issues, fix them and learn. It seems incredible that 15 months after receiving the first technical drawing, they had produced a commercial machine. The Temsan team worked day and night to have the machine ready for ITMA.”
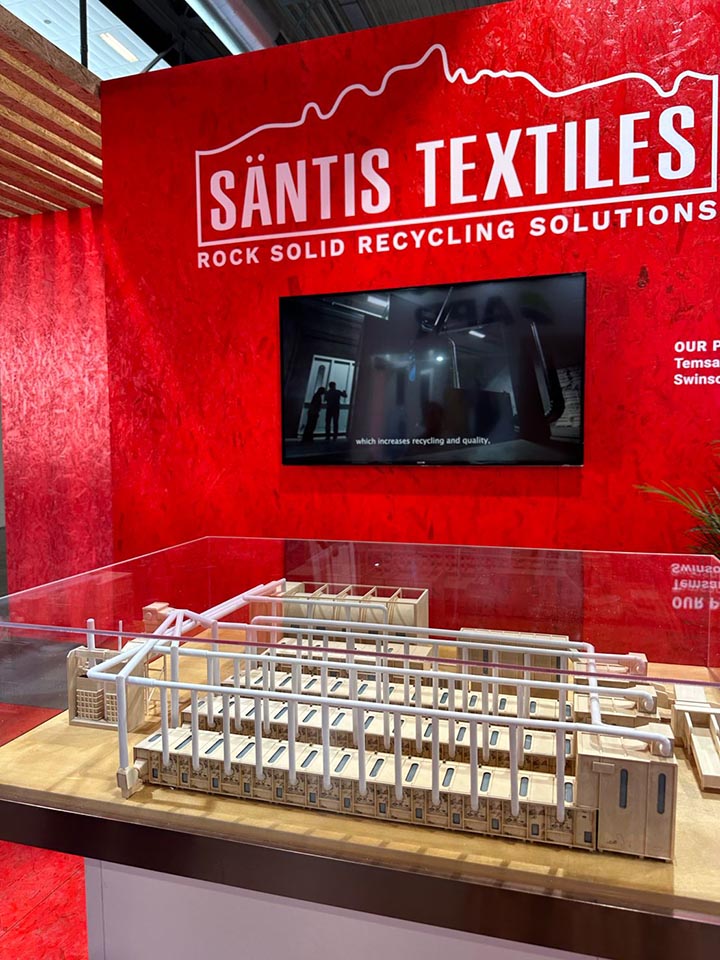
“Sustainability has become a critical factor in the textile industry,” added Cem Erdoğrul, managing director at Temsan. “There is a growing need for recycling, both pre and post-consumer, to reduce waste and promote a circular economy. While this project may be an initial step, it shows that we recognize the importance of embracing recycling technologies to create high quality, sustainable textiles.”
Fiber Length
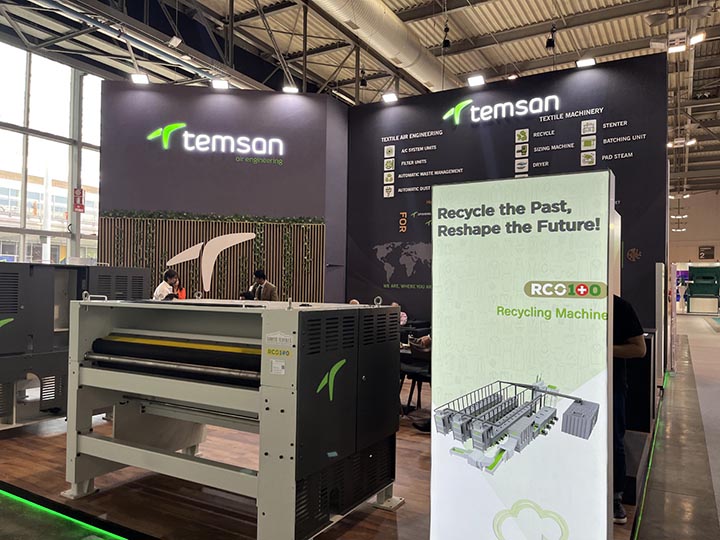
The RC100 recycling system has been developed to carry out the gentlest fiber treatment in order to achieve maximum fiber length.
A standard line includes two conveyors and two guillotine knives positioned at 90-degree angles to achieve the best possible cutting results.
An initial buffer unit also acts as a mixing chamber for the cut material and controls the feeding to the four pin or saw-toothed pre-opener cylinders.
Feeding of the cylinders is through feed rollers but without clamping points or counter-rotating cylinders. Transport is by perforated drums which not only de-dust the fiber sliver, but also forward it without stressing the material.
From the pre-openers, the material is sent to three parallel fine-opener lines, each equipped with 12 opening cylinder modules. It can be run through the system as many times as necessary until the fibers are fully opened before being pressed into standard bales.
Compact Spinning
In addition, working with Swinsol, a Swiss machine components specialist, Säntis has developed a compact ring spinning system specifically designed for yarns to be produced from the RCO100 recycled fibers.
“From day one our aim was on retaining fiber length – the only way to achieve good results in spinning and weaving,” Hutter said. “Turkish cotton has a staple length of approximately 31-32mm and when we recycle this we achieve an 80% staple length of approximately 25-26mm. The output length depends on the input length of course, but we can say we have approximately 15-20% loss. We can also retain longer fibers by reducing the production rate.”
The RC100 technology can spin Open End yarns in counts from Ne 5.9-20 and carded ring compact yarns from Ne8-30. In addition, carded ring compact yarns can be produced up to Ne20 with 40 den and 70 den recycled elastane.
“All of the other players on the recycling market come from the nonwovens sector because it’s all about tons per hour, but a lot less about fiber quality,” Hutter said.
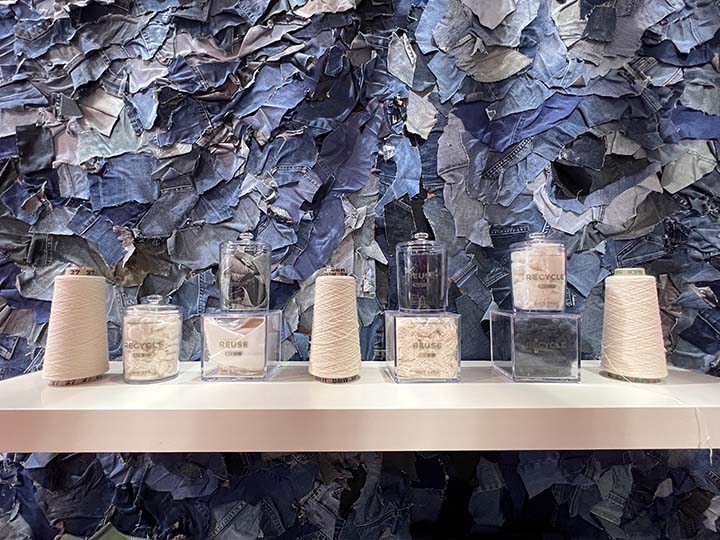
Brand Support
Säntis has ongoing partnerships with fashion brands such as Tommy Hilfiger, Calvin Klein Jeans and Lacoste, and is also partnering with FibreTrace to develop a unique traceable ID specifically for RCO100 fibers, yarns and fabrics.
FibreTrace technology gives brands 20/20 vision of their supply chains at every step from sourcing of raw fiber to store, combining physical and digital technology to provide unparalleled intelligence. It is indestructible through the entire textile supply chain, auditable and traceable in real-time, verifies brand claims, builds trust and engages the consumer.
Since 2020, Hutter has worked with his daughter Annabelle Hunter, who is now Säntis’ managing director.
“We had a fantastic time at ITMA this year,” she said. “The textile world is changing – there is legislation coming, first in the EU, and this will give the recycling sector a big push.”
“We now have further ideas in development for combining our recycling system with spinning technology and also on approaching the recycling of poly-cotton blend fibers,” said her father.
“I’m really proud of the invention of our RC100 technology because this machine is not exclusively designed to downcycle – it is designed to recycle, and that means textile-to-textile directly.”
Annabelle Hutter
All in the Family …
“We are a family-owned company built on generations of Swiss textile expertise,” Annabelle Hutter proudly shares as the next generation leader in the company. Her grandfather was a textile engineer at Saurer, where Stefen Hutter also did his apprenticeship before moving to Rieter, where he worked for many years.
Säntis was formed in 2016 and Annabelle joined the company four years ago, when they were at the stage of commercializing the 100% recycled cotton.
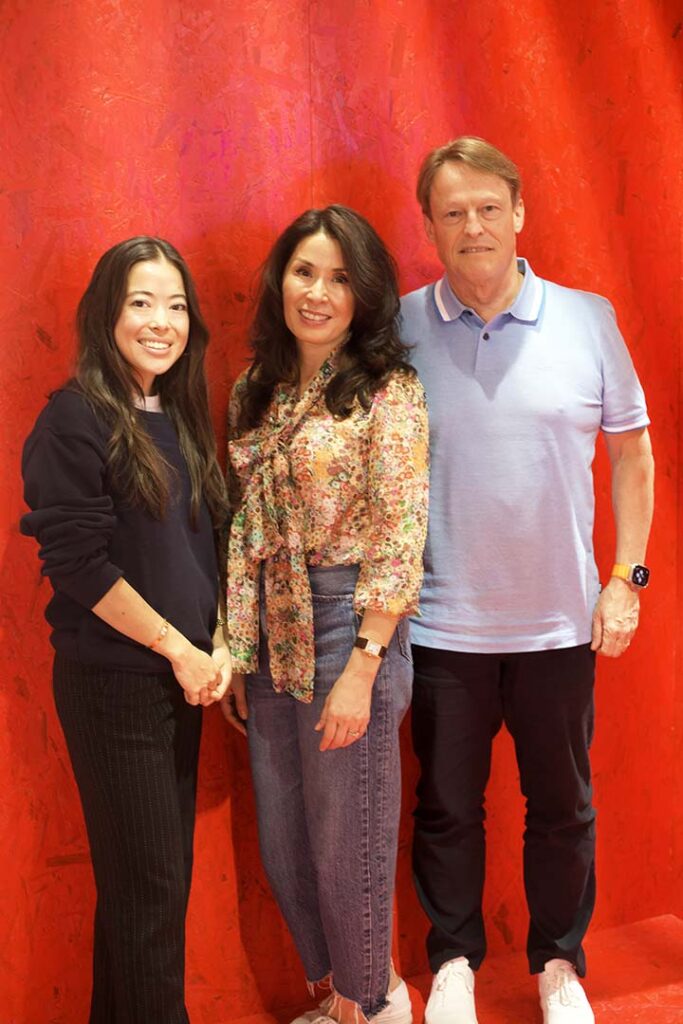
“I’m really proud of the invention of our RC100 technology because this machine is not exclusively designed to downcycle – it is designed to recycle, and that means textile-to-textile directly,” she says.
“That was the whole notion from the beginning. The machine’s gentle opening system shreds very gently.”
On being in the family business, she says, “Working with my father has been a very exciting journey. It hasn’t always been easy, but it’s very rewarding and I think it’s a great synergy we have. I am more of the creative thinker and he’s definitely the technical brain in the family. I really believe that more daughters should hopefully strive to work with their fathers one day.”
Stefan shares he is confident in what Annabelle brings to the company will expand its vision. “I’m very happy to have had Annabelle on board since 2020. She is in charge of the newly-established Säntis Textiles in Switzerland, which focuses mainly on the marketing and promotion of our recycled cotton technology. For me, it’s nice to have a family member to continue what we began. It’s also nice to see how fast she has learnt about the textile process and how she’s willing to elaborate on her own ideas. Annabelle’s also an inspiration for young women to work in this industry and I couldn’t be prouder.”