Over 105,000 visitors descended on Barcelona, Spain, from June 20-26 for this year’s ITMA textile technology exhibition, which takes place once every four years in Europe. The technologies of the 1,717 exhibitors from 45 countries on display are employed in producing a wide range of fiber-based products, ranging from clothing and home furnishings to more technical products, such as construction materials and reinforcements for composites.
Egyptian cotton
While the textile machinery industry appears to be in something of a cyclical downturn right now, the big investment news at the show was the announcement of a comprehensive modernization program for Egypt’s upstream textile industry valued at around €1 billion, with the full backing of the country’s president, Abdul Fatah Al-Sisi.
Egypt, of course, is famous for its extra-long staple (ELS) cotton which continues to be one of the country’s biggest competitive advantages, with a reputation for being the world’s finest due to its softness and strength. This allows the production of the finest yarns and the fabrics made from them to be more solid and resistant to stress. In addition, Egyptian cotton’s ability to absorb liquids gives fabrics deeper, brighter and more resistant colors.
Egyptian cotton is hand-picked, which guarantees the highest levels of purity and puts no stress on the fibers as mechanical picking does, leaving the fibers straight and intact.
Major impact
It makes perfect sense for Egypt to be fully profiting from its cotton, rather than allowing all the added value to be taken from third party countries once it is simply sold as fiber.
“The Government of Egypt has decided to make a big investment into the public sector textile industry,” said Dr. Ahmed Moustafa Mohammed, chairman of Cotton and Textiles Industries Holding Company (CCTIHC), which is implementing the new investment program, during the signing ceremony at ITMA 2019. “The program will have a major impact on the competitiveness and success of the Egyptian textile industry in the future.”
Among ITMA exhibitors awarded contracts to supply new equipment, including some 780,000 new spindles and 1,250 weaving looms, were the fiber spinning companies Rieter of Switzerland and Savio of Italy. Weaving machines will be supplied by Italy’s Itema Group and knitting technology from Karl Mayer of Germany. Finishing technologies will be supplied by Benninger (Switzerland) and Brückner and Thies (both Germany). Italian digital printing specialist EFI Reggiani will also be supplying technologies as part of the deal.
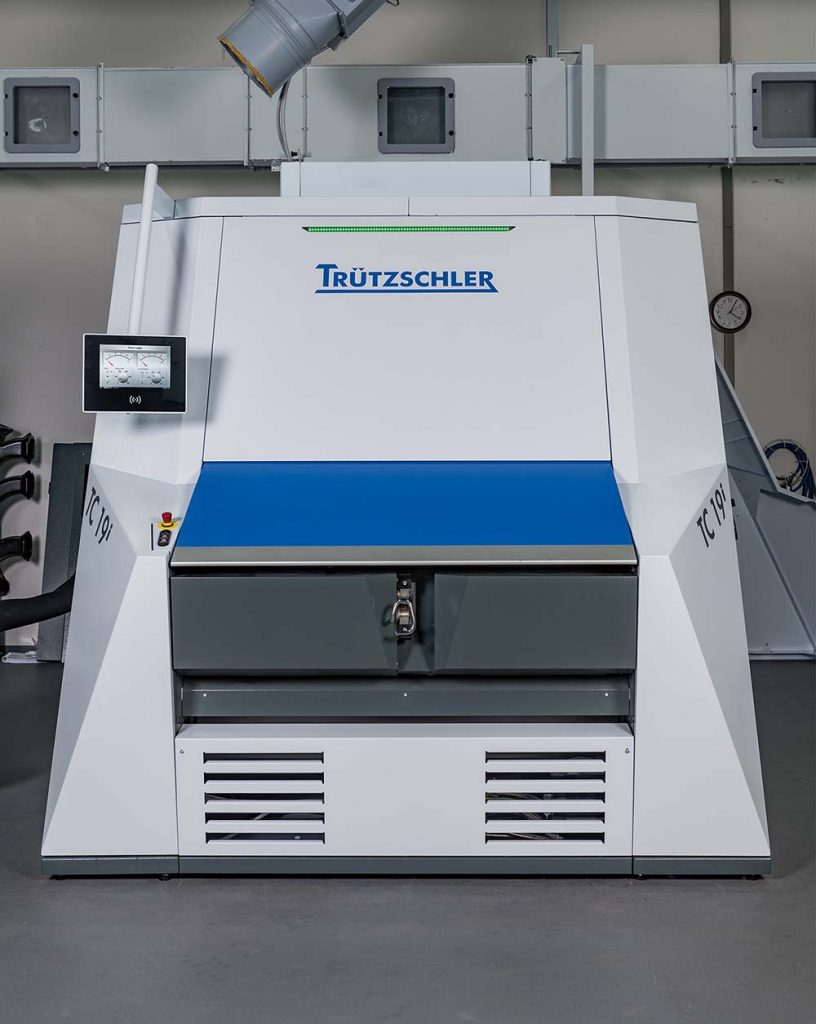
Sustainability award
The 2019 ITMA Sustainability Award was meanwhile claimed by Italy’s Candiani, for its work with Austrian cellulosic fibers producer Lenzing on the production of denim fabric using regenerated and recycled raw materials.
Also nominated were Levi Strauss, and Jeanologia, for their work in the creation of the FLX Customization Studio, which allows Levi customers to pick their denim finish and create a unique pair of jeans in less than two hours and Lee and Tonello, for their collaboration on the All-in-One System, which combines four technologies that drastically reduce the water needed in the finishing stages of Lee denim jeans manufacturing.
Candiani’s new Re-Gen fabric comprises 50 percent Tencel x Refibra Lyocell made from pulped cotton scraps and wood pulp using Lenzing’s closed-loop process and the other 50 percent consists of post-industrial recycled fibers from Candiani’s own manufacturing waste.
“It’s interesting to note that all three of us finalists have been involved in efforts to clean up the denim industry,” said Roberto Candiani, of Candiani. “We are definitely flying the indigo flag here, but there’s a long way to go. In our work with Lenzing and Refibra we have proved for the first time that a regenerated product can be as good, if not better, than the products from which the waste came from in the first place – and we have not made any compromises on either aesthetics or performance. Five years ago, I would not have believed this was possible.”
“Refibra lyocell is the first commercially-viable manmade cellulosic fiber using waste to make new lyocell fiber,” added Tricia Carey, Lenzing’s director of global business development for denim. “Refibra technology uses post-industrial cotton waste, which is made into pulp. This pulp is combined with wood pulp and utilizes the closed-loop manufacturing of lyocell to make new fiber. Additionally, Refibra technology incorporates fiber identification, so there is transparency in the supply chain.
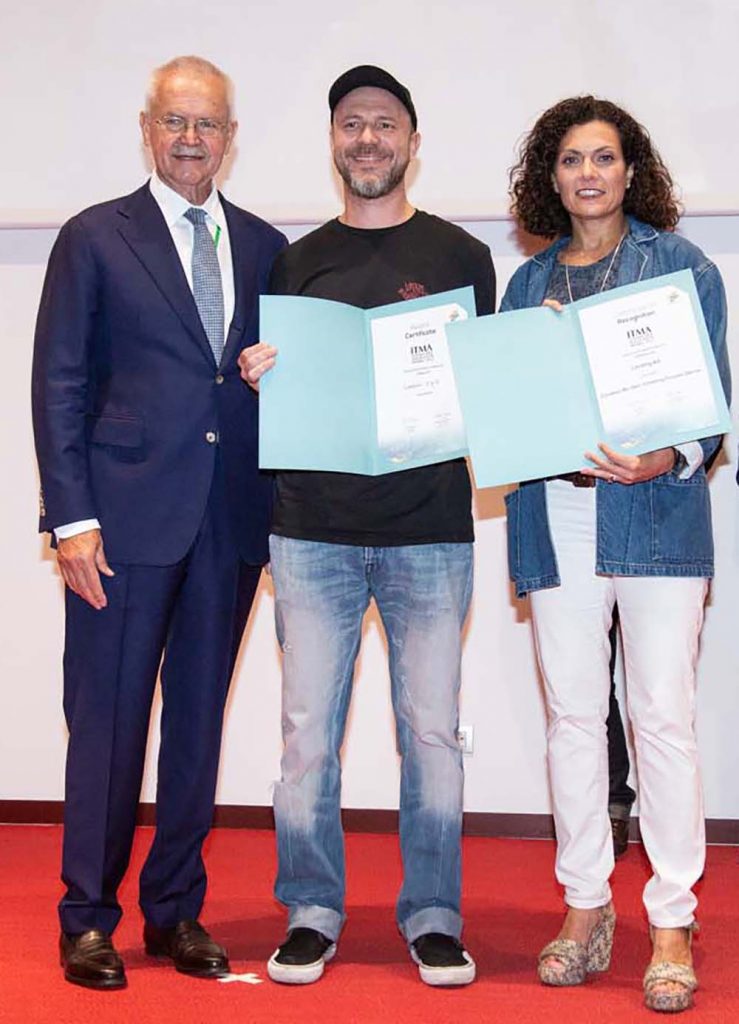
Recycling POY and FDY
Among key new fiber production technologies introduced at ITMA 2019 were a number of new concepts from Oerlikon Manmade Fibers of Neumünster, Germany, including the new VacuFil, developed in cooperation with its subsidiary BBEngineering for the full recycling of POY and FDY filaments via a process of homogenization drying, extrusion, pre-filtration, the BBE vacuum filter, pelletizing and downstream melt application.
“The recycling of PET bottle grades and flakes is state of the art but the recycling of POY and FDY back into full production is really new,” said Dr. Klaus Schäffer, MD of BBEngineering. “I strongly believe this can change the scale of operations for our big fiber spinning customers, who can now bring all of their waste directly back into first class production.”
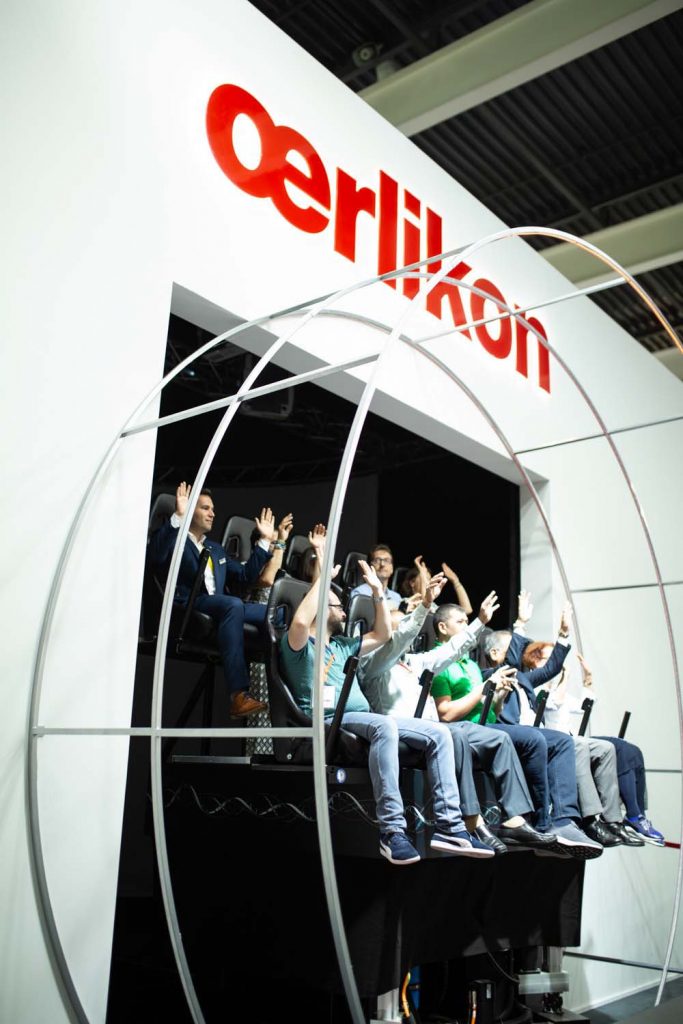
Recycled tapes
The Starlinger Group, based in Vienna, Austria, meanwhile introduced the FX 6.1 circular loom for weaving tapes made of recycled PET. The FX 6.1 is a six-shuttle loom that is primarily used for the production of high-performance fabrics and does not possess any sliding parts that require lubrication, ensuring that the fabric is completely oil-free and can be used for packaging food products.
The resulting rPET fabric is suitable for the manufacturing of flexible intermediate bulk containers (FIBCs) and container sacks, as a result of its stability, flexibility and high melting point.
Starlinger, which exhibited with its new subsidiary STC Spinnzwirn for the first time in Barcelona, claimed to be the only supplier in the world to sell all of the equipment needed for the production of plastic fabrics – from tape extrusion lines and circular looms to machines for sack conversion, plant monitoring and the recycling of production scrap.
Carding gap
Finally, in a notable innovation for staple fiber production, Germany’s Trützschler introduced the new self-optimizing card.
The setting of the carding gap on card openers has a critical influence on quality and performance and the new TC 19i intelligent card can now automatically and continuously optimize it to within a tolerance of 3/1,000ths of an inch – something that has not before been possible through human operation of a machine.
“The card is the heart of the spinning mill and not only is the TC 19i very easy to operate but continuously automatically adjusts the carding gap to its optimum position, so there’s no manual setting needed,” said Dr. Bettinna Temath, the company’s head of global marketing.
ITMA 2019 technology roundup
Mobile, fully automatic handling and transport system
SAHM presented its “BoDo” fully automatic doffing and transport system at ITMA, positioning it as a technology that will revolutionize bobbin and tube handling in any winding process workflow. In combination with automatic SAHM winding machines, the BoDo mobile bobbin-handling robot can take up to two bobbins from the winding machine, transport them to a pre-defined position, and deliver them there for the next process step. BoDo’s routes through the production environment, as well as the pick-up and delivery points for bobbins, can be freely programmed and adjusted for any manufacturing situation. After taking the full bobbins, BoDo places empty tubes on the winding heads for a continuous workflow.
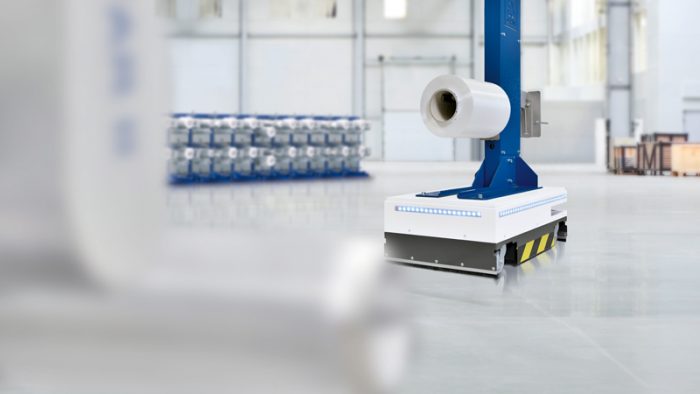
With an optional RFID system, “IntelliTexCORE RFID,” BoDo becomes an Industry 4.0 solution. Through the automated RFID tracking of bobbins, workflows can be visualized and monitored – for full transparency from production to final use.
Technology for high-efficiency, high-performance nonwoven manufacturing
DiloGroup had a large booth at ITMA, showcasing its full line of technology for the manufacturing of nonwovens, including DiloTemafa for fiber preparation, opening and blending. Dilo also showcased its updated bale opener series, Baltromix Pro, with design features for operating assistance with Industry 4.0 components for cleaning control, better accessibility for maintenance, and the DI-LOWATT system for energy savings in fiber transport.
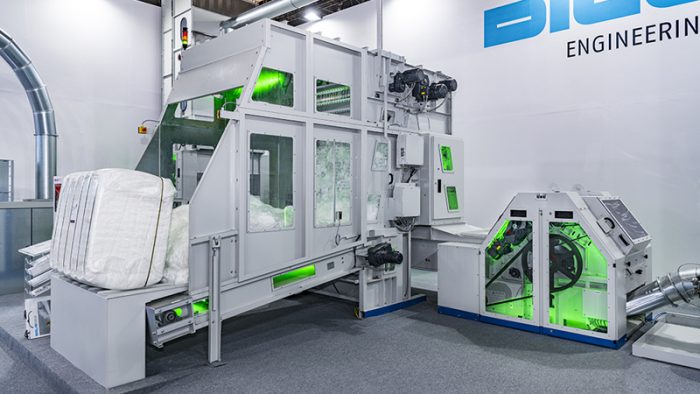
HyperLayer NT is Dilo’s latest state-of-the-art high-speed precision layering technique, which plays an important role in hydroentanglement lines. In this application, the technology is capable of layering speeds up to 190 m/minute using sophisticated viscose fibers and a layering width of about 4 m, while at the same time showing high layering precision in cross and longitudinal direction.
Dilo’s FutureLine 3D-Lofter enables web forming units to deposit fiber masses on freely programmable spots in longitudinal and cross direction, thus saving overall fiber mass in applications such as deep molded parts for automotive interiors. This ability reduces costs in production and operation. Another application is the structuring of flat needlefelt floor coverings, which may be further processed with Dilo’s DI-LOUR and DI-LOOP technology.
The high stitch distribution uniformity achieved by the new needle pattern 6000 X in conjunction with the new Hyperpunch kinematics Hα reduces investment costs for numerous needlefelt production lines and to increase surface quality. Dilo also highlighted its “smart industry” capabilities for more transparency and control of the production process and the operating conditions can be realized with the aid of software, internet and cloud functionality.
Zero twist feeder for composite fabrics
IRO AB, a member of the Vandewiele group, presented its ZTF Zero Twist Feeder at ITMA. The technology is designed to ensure there is no twist in the feed, which is a key requirement in the weaving of fibers such as carbon, glass and aramids, as well as thermoplastic tapes for highly engineered composite fabrics. The unit can accommodate tapes in widths up to 10mm and weight up to 7kg, with an insertion length of up to 3.4 meters. It is equipped with a buffer arm synchronized with the rapier movement of the weaving machine to deliver the exact amount of yarn from the bobbin required for the weft insertion. A tension and sensor arm ensures constant yarn tension is maintained during the entire insertion cycle.
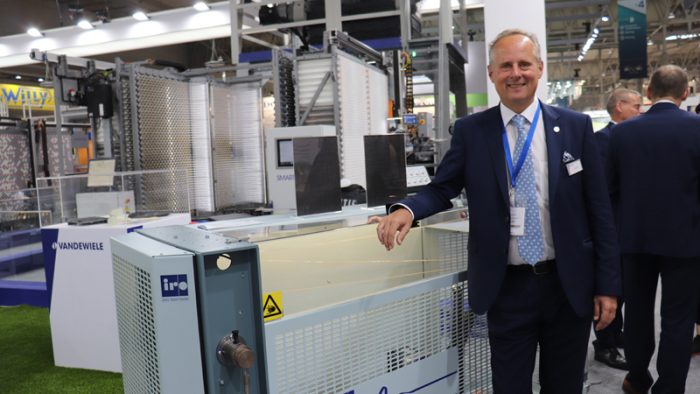
Designed for use with rapier machines, the ZTF can be installed on new CAN (controller area network) communication machines or retrofitted to older non-CAN machines using a specially-designed conversion kit.
Digital connectivity for textile machinery
The new Karl Mayer business unit, KM.ON, was presenting for the first time at an ITMA. The unit showcased its new k.ey connectivity system for networking multiple machines. Karl Mayer describes the technology as the first bidirectional networking solution, which permit the seamless transfer of pattern data to the new HKS-3M-ON and RSJ 4/1 ON machines. Thus reducing time-to-market considerably.
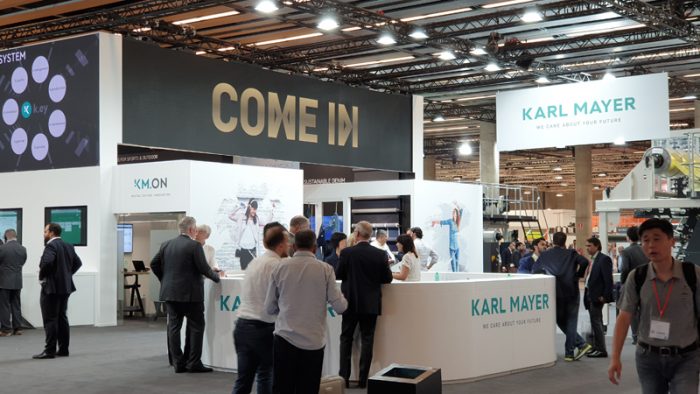
Using the k.ey technology, HKS 3-M-ON technology can be linked directly to the company’s KM.ON cloud via the k.ey system, which enables lapping data to be loaded directly onto the machine. The RSJ 4/1 ON uses k.innovation technology to optimally support virtual textile development. Meanwhile, Karl Mayer’s new machine, SIM.PLY, produces thermoplastic, unidirectional tapes (UD tapes) using fiber spreading technology. Its products – premium tapes with precisely aligned, continuous fibers – are suitable for use in highly stressed, fiber-reinforced, lightweight structures. The thermoplastic matrix is also easy to process, which makes mass production feasible.
Karl Mayer was also showing its new GREENDYE technology under the slogan of SUSTAINABLE DENIM. This system uses the advantages of indigo dyeing in a nitrogen atmosphere to achieve greater efficiency and sustainability in denim production.
Multi-color yarn dyeing system
Monforts debuted what it describes as a revolutionary new system for yarn dyeing based on the company’s Econtrol dyeing system for fabrics. This CYD denim processing technology integrates new functions and processes into the weaving preparatory processes – spinning, direct beaming, warping and assembly beaming, followed by sizing and dyeing – in order to increase quality, flexibility, economic viability, and productivity.
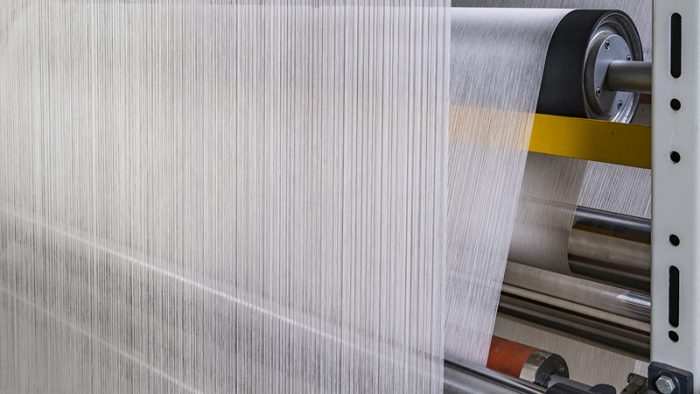
Econtrol is a pad-dry process employed in Monforts continuous dyeing in which the reactive dyestuff is fixed to the cellulose fibers during drying and the CYD multi-color yarn dyeing system introduces a number of new concepts based on it, including the unique Eco Bleach process. The Eco Bleach system is combined with the washing units and the fabric is then dyed immediately, resulting in considerable savings in water and chemicals.
In its raw state, cotton has a light brownish/yellow tinge and bleaching is necessary to ensure its pure whiteness prior to dyeing. On conventional systems, this involves a separate process step, but with the CYD multi-color yarn dyeing system it is now integrated into the Econtrol process for full dyeing pre-treatment.
Heated godet rolls with temperature control
Retech showed its heated godet product line at ITMA, including a new take on its yarn tension sensor with HALL technology. A version for application in extrusion was demonstrated at the show with an enhanced sensor that was able to withstand the demands and influences of a spinning process at high speeds (4000 m/min. +) and high yarn counts (3000 dtex +).
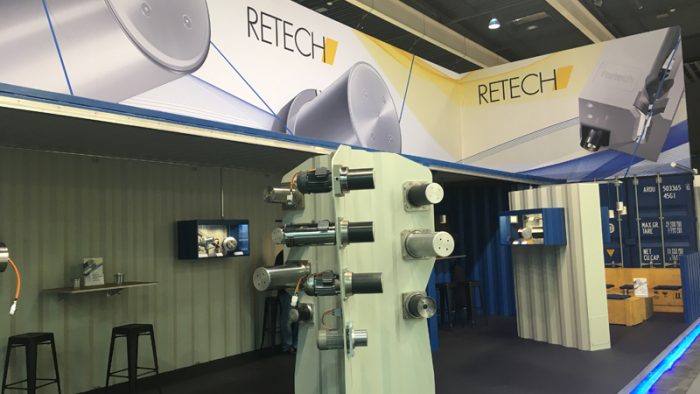
Retech’s new godet generation is designed for the drawing and heat treatment of all kinds of synthetic yarns. Based on motor technology by means of permanent synchro magnet technology, the system features a new temperature control concept named “blue line,” providing:
- UCR-6 temperature controller for multi-zone godet rolls (1-6 heating zones)
- UCR-6P temperature controller for six independent heating positions (1 zone STS godet rolls or other heating components)
- USC temperature converter (to convert the digital into an analogue signal)
UTR-4A measured value temperature transmitter as a technical and robust further development for the hostile working environment of man-made fiber manufacturing.