Many of Japan’s major corporations began as fiber manufacturers, and their expansion has been decades long, typically involving diversification into other fields such as chemicals, plastics, pharmaceuticals, life sciences, real estate, etc.
Asahi Kasei, Kuraray, Teijin, Toray Industries and Toyobo, for example, all emerged as manufacturers of viscose rayon in the 1920s and have remained loyal to fiber technology as a key component in their research and development structures, inevitably drawing in academia and third-party cooperations.
A century later, it is certainly with a nod to this ingrained culture that electronics giant Sony has introduced a new material called Triporous that is based on rice husk fibers.
In 1991, Sony became the first company in the world to commercialize a rechargeable lithium ion battery and has since continued advancing its R&D efforts in pursuit of improving its performance.
It was during this development work, however, that Triporous – as a material that exhibits a greater and faster rate of absorption of various substances than existing activated carbons – was also invented.
Structure
Triporous consists of a unique finely structured porous carbonous material derived from surplus biomass such as rice husks, including silica.
In addition to its micro-pores of 2nm or less, which are also found in conventional activated carbons, it contains mesopores of 2-50nm and macropores of approximately 1µm – all of which exist in a multiplex.
As a result, it can easily absorb large substances at larger molecular weights that have been difficult to absorb with conventional technologies. This includes organic molecules such as humin and poisonous algae blooms that cause water pollution, as well as allergens, viruses, and small proteins such as enzymes. It is also capable of quickly absorbing low molecular weight compounds such as organochlorides and pesticides.
Triporous will provide new value for various products, including environmental filters that remove pollutants from the air and water. Other applications include toiletries such as deodorants, odor removers, and other anti-bacterials, as well as applications in cosmetics, pharmaceuticals and clothing and textile products.

Sustainable story
Approximately two million tons of rice husks are disposed of annually in Japan alone and over 100 million tons worldwide every year, so the product has a compelling story when it comes to sustainability.
The first step in the production process for Triporous is to carbonize the rice husks by clearing the large amount of silica accumulated between the cells of the husks. The silica is then etched to form large macropores, and then mesopores and micropores are developed in a high-temperature water vapor activation process.
Sony has obtained end-to-end patent protection on the material and investigated the possibility of commercializing and mass-producing it itself but has now decided to make the material available through third-party licenses.
CNFs
The pursuit of more sustainable alternatives to synthetic fibers has led Japanese researchers down some very interesting avenues over the past decade, and one of the most intriguing is the development of cellulose nanofibers (CNFs) and applications for them.
Composites based on CNFs can be a fifth of the weight of steel yet five times stronger. At the same time, they have a low linear heat expansion, high recyclability and reuse potential and their production is carbon neutral. They are finer than the wavelengths of visible light and among other outstanding characteristics, they have an elastic modulus as high as that of high-strength aramid fiber, exhibit thermal expansion on par with glass, and show high barrier properties in respect of oxygen and other gases.
Despite their wood pulp origins, CNFs also have the same transparency as glass and higher strength than conventional plastic films, as well as better dimensional stability under high heat.
Japanese corporations including Toyota, Denso and Panasonic have all been actively involved in CNF development work.
Fibrillation
“CNFs are light weight and strong nanofibers made from plants, typically by first pulping wood, which is then fibrillated to nano levels,” explains Professor Hiroyuki Yano of Kyoto University. “Pulp is an aggregate at this stage and the chemical structure of the individual CNFs are transformed to become nano-compatible. As the pulp is subsequently kneaded with molten resin, the nanofibers further fibrillate and mix well with it, strengthening the resin.”
Forest covers approximately 70% of the land in Japan and two thirds of it is planted and managed woodland, with the Japanese cedar and cypress trees already used for the production of paper and construction materials.
Despite its use for these raw materials, there is still around 15 million tons of wood available for CNFs produced in the mountains of Japan each year, which is extremely rare anywhere else in the world.
NCV Project
Since 2016, research teams at Kyoto University, along with the Kanazawa Institute of Technology, have coordinated the Nano Cellulose Vehicle (NCV) Project which has involved a consortium of 22 Japanese universities, research institutes and automotive suppliers and OEMs, with funding from Japan’s Ministry of the Environment.
At the 2019 Tokyo Motor Show, the Nano Cellulose Vehicle (NCV) was unveiled as a highlight of the project.
CNFs made from wood, plants and recycled agricultural waste were employed across the body, including as the doors, roof, and bonnet, in addition to extensively in the car’s structural frame.
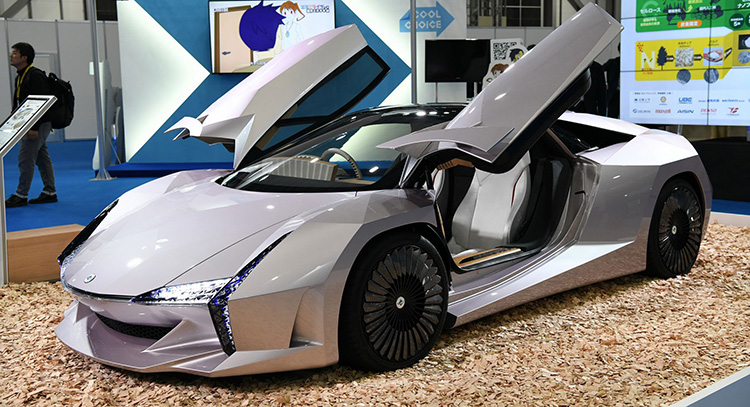
Negative legacy
“The biggest negative legacy of today’s cars is the amount of CO2 they emit,” says Professor Yuji Kageyama of Kanazawa Institute of Technology. “Weight saving is an extremely important factor that will contribute to its reduction. Something else that is required is for them to be carbon neutral. There are great expectations for CNFs as the answer to achieving both.”
Using CNFs based on the nanotechnology developed around a decade ago at Kyoto University, the NCV partners are aiming to achieve an overall reduction in the weight of vehicles by 10%.
If this is achieved, it will reduce CO2 emissions by a total of 2,000kg per vehicle – from the production of the parts through the vehicle’s lifetime and disposal.

Industrial scale
The race is now on to achieve industrial production and CNFs into a wide range of end-use markets, from automotive parts to household appliance bodies and even flexible display panels.
Japanese investors in CNF technology, including Asahi Kasei, Daio Paper, Nippon Paper and Oji Holdings, are now hoping to lower the cost per kg of CNFs to around the US$10 mark, through their commercial-scale production. Analysts have predicted that the market for CNFs will grow to 1 trillion yen (US$8.7 billion) by 2030.