There can be no more potent a symbol of the golden age of synthetic fibers than the planting of the U.S. flag on the moon by Buzz Aldrin on July 21st, 1969.
The flag was famously purchased by a NASA secretary from Sears for $5.50, and despite nylon’s unbeatable durability, cannot possibly have endured what is now approaching 53 years of the Moon’s lunar dust and alternating fortnights of extreme heat and perishing cold.
In 2022, however, nylon’s durability is no longer a cause for much celebration, as attempts are made to replace its oil-based building blocks, establish recycling chains for nylon-based products and also address the plastic’s persistence in the oceans and the environment in general.
DuPont and I.G. Farben
Initially a DuPont trademark, nylon is now the generic term for a wide group of polyamides, of which nylon 6 and nylon 6.6 are the most abundantly used in the textile industry.
Nylon 6.6 was invented by W.H. Carothers at DuPont in 1938, taking its name from its two different monomers – hexamethylenediamine and adipic acid – each of which has six carbon atoms. In response to the development of Carothers, Paul Schlack of the German company I.G. Farben polymerized caprolactam to nylon 6, which was commercialized by Perlon and manufactured from 1941 at British Nylon in the UK.
Both nylon 6 and 6.6 have since been widely employed in textiles, notably in hosiery, sportswear, protective clothing, automotive interiors and carpets, as a result of favorable properties such as toughness, abrasion resistance and easy washability. Nylon filament yarns enable smooth, soft and lightweight fabrics with high resilience and their water absorption rate is higher compared to other synthetics, especially to polyester, allowing the development of more comfortable fabrics due to evaporative cooling.
Recycling
In examining the potential for recycling nylon, it becomes apparent that there is a lack of any major waste stream, such as exists for polyester with PET bottles.
According to a 2021 Textile Exchange report, nylon accounted for just 5% of global fiber production in 2020, with 5.45 million tons produced, down from 5.58 million tons in 2019, but up from 3.74 million tons 20 years ago.
Recycled nylon represented just 1.9%, or 0.11 million tons of total nylon production in 2020.
Several brands have, however, made commitments to increasing the use of recycled nylon so this figure will have to increase in the coming years.
The most common source of feedstock for recycled nylon is in mechanically regrinded post-industrial quantities diverted from manufacturing processes such as spinning and injection molding.
Rencycle
A ski suit made totally from yarns spun from recycled materials, which are fully recyclable at end-of-life, for example, was showcased at the 34th Milano Unica fabric show by Italy’s RadiciGroup at the beginning of February this year.
This new uniform for the RadiciGroup Ski Club has been designed by the company in collaboration with the Italian sportswear brand DKB.
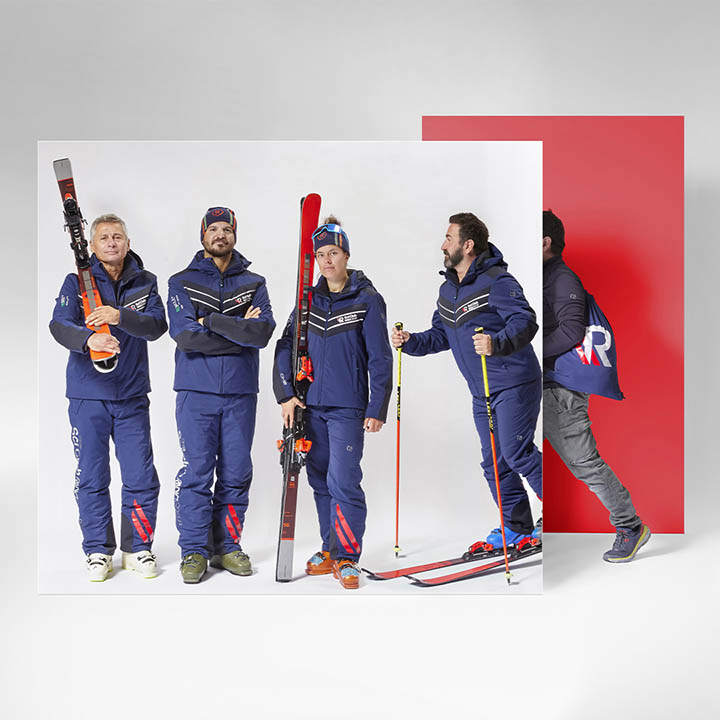
“The ski suit, consisting of jacket and trousers, is fashioned with fabric made of Rencycle, a yarn obtained from mechanically recycled nylon,” said Marco De Silvestri, sales and marketing manager at RadiciGroup. “In addition, the suit’s padding and numerous accessories, such as zippers, Velcro, buttons and thread, are also made of polyamide. It was an ambitious project and we reached a definitive goal – circularity in sportswear without compromising on performance. This was achieved through continuous close collaboration with other companies in the chain to develop chemically compatible materials that guarantee the high technical performance required by this kind of application.”
re/cor RN66
Invista’s Cordura brand has also just announced the debut of Cordura re/cor RN66 made from 100% pre-consumer fibers and 100% GRS (Global Recycled Standard) certified.
The new recycled nylon 6.6 collection is described as durable, long-lasting in fabric constructions, and in terms of quantifiable benefits compared to virgin nylon 6.6, its production decreases greenhouse gas emissions by 83%, consumes 82% less energy and uses 57% less water.
“One of the main goals behind Cordura re/cor was to continue to deliver the performance expected of Cordura advanced fabrics, while expanding our portfolio of responsible products,” said Cordura vice president Anthony Green. “It’s something our customers and partners have been asking for and something we’ve been working hard to deliver.”
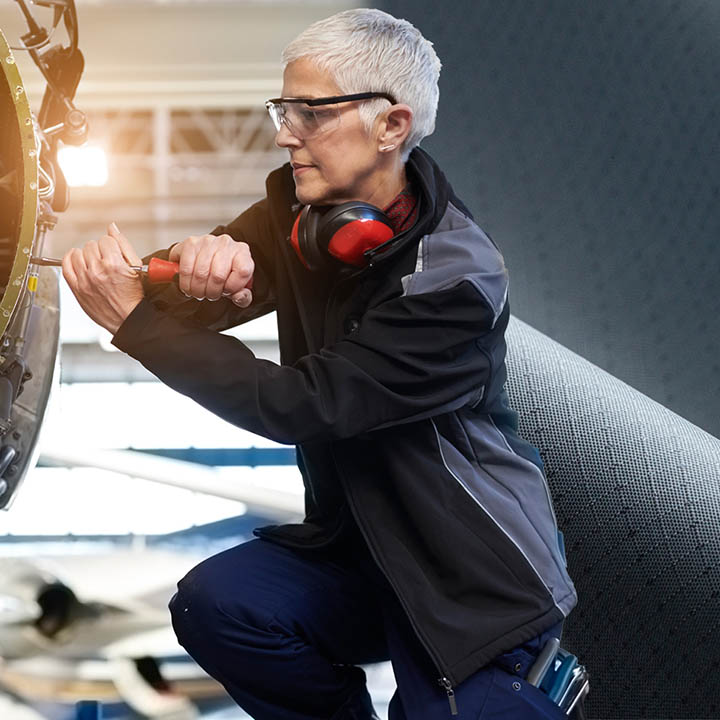
Econyl
Post-consumer nylons are generally too contaminated for mechanical recycling, but several chemical recycling routes are arising.
Probably the best-known nylon recycled from post-consumer resources is Econyl produced by Aquafil in Slovenia.
Aquafil’s 100% regenerated nylon from waste for Econyl products provides the same quality and performance as normal nylon 6.
A portion of the nylon Aquafil recovers for it is from the oceans, in the much-acclaimed Healthy Seas initiative, in which deep sea divers recover abandoned fishing nets from the coastal regions of the Mediterranean. Much more comes from the massive quantities of discarded carpeting that Aquafil is now recycling at its two purpose-built facilities in the U.S.
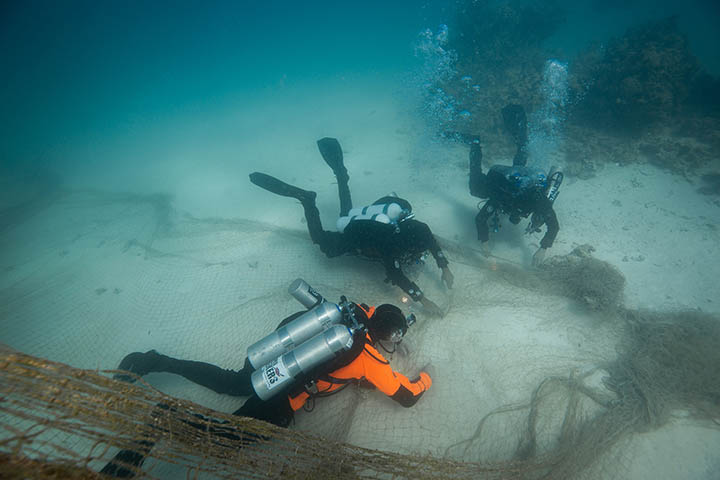
Fish waste
In an oddly-related development, a team of Scottish researchers at University of Edinburgh is currently exploring a new bio-based process that could see fish processing waste used to create adipic acid as the precursor to the production of nylon 6.6.
The group is taking waste material generated as part of fish processing and using biological enzymes to extract its fatty components of the fish waste. Through advanced molecular biology, genetically modified bacteria can then turn the fatty components into a mixture of adipic acid and useful by-products.
As much as 492,000 tons of waste is created annually by the UK’s fish processing industry, comprising fish remains, oils, and wastewater collected during the clean down of processing plants. Currently, the waste must go through either expensive and energy-intensive treatment and separation or is used in low value products such as animal feed or fertilizer, but this new process could uncover alternative uses for the waste material.
Car tires
Another potential waste stream for partially recycled nylon currently being explored is that of old car tires.
The tires are being recycled into Ultramid Ccycled nylon (polyamide), in a process called ChemCyling developed by BASF.
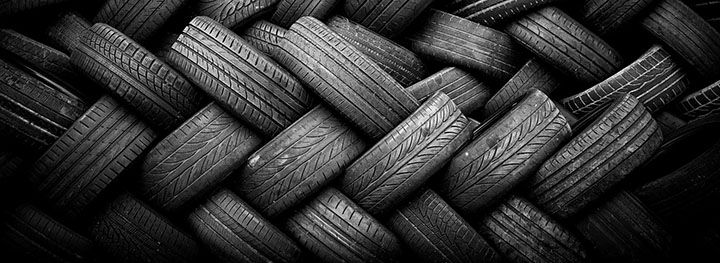
In this process, BASF feeds pyrolysis oil from old tires into its German production plant in Ludwigshafen, and in doing so partially replaces fossil resources. The share of recycled raw material is assigned to certain products using a certified mass balance approach, and because products with Ccycled in their name have exactly the same properties as the equivalents made from fossil raw materials, customers can process them in the same manner and use them in their conventional processes. As a result, Ultramid Ccycled can also be used in applications with high quality and performance requirements, such as in the textile industry.
Yarn producer Fulgar, of Castel Goffredo, Italy, is already producing yarns based on Ultramid Ccycled, and in March 2022 leading outdoor apparel brand Vaude launched performance pants based on the material as well.
Biopolymers
In August 2021 Canadian athletic apparel brand Lululemon announced a multi-year collaboration with San-Diego-based Genomatica to create a lower-impact, plant-based nylon.
The agreement is lululemon’s first equity investment in a sustainable materials company and Genomatica’s largest partnership within the retail sector.
Genomatica uses biotechnology and fermentation to convert plant-based ingredients into widely used chemical building blocks, like those used to make nylon. These building blocks are converted into pellets and yarns, and the two companies will be working closely with lululemon’s fabric supply chain to incorporate this material into future products.
“Genomatica’s bio-based innovations, along with its distinctive track record of successful commercial applications, will help us deliver on our goals to make 100% of our products with sustainable materials and end-of-use solutions by 2030, as we move towards a circular ecosystem,” said lululemon CEO Calvin McDonald.
“The combination of biotechnology, fermentation and renewable feedstocks can provide a powerful means to disrupt the apparel industry through sustainable sourcing,” added Christophe Schilling, CEO, Genomatica.
Precursor
Genomatica is also working with Aquafil on a new demonstration scale facility to produce 100% renewable bio-based nylon 6.
In examining the potential for recycling nylon, it becomes apparent that there is a lack of any major waste stream, such as exists for polyester with PET bottles.
The two companies first teamed up in January 2020 to produce the world’s first ton of bio-nylon 6 precursor at pilot scale and are now moving directly to a larger-than-typical demonstration scale to support initial commercial applications by committed brand partners. The first production runs are slated to create 50 tons of bio-nylon for pre-commercial use by Genomatica’s brand partners, with the demonstration plant supporting product needs until commercial scale plants are in operation.
Aquafil will build and operate the downstream operations of this large-scale demonstration plant at its facility in Slovenia, where it will convert Genomatica’s bio-based precursor to commercial-quality bio-nylon 6 yarns, as well as films and engineered plastics.
Ecodear
The development of a nylon 510 fiber that incorporates 100% biobased synthetic polymer has been further announced by Toray Industries, headquartered in Tokyo, Japan.
Ecodear N510, will be the first 100% plant-based nylon fiber in Toray’s Ecodear lineup and has been developed by polymerizing sebacic acid from castor-oil plants and pentamethylenediamine from corn and spinning waste.
Unlike other wholly plant-based nylons, Ecodear N510 is said to have a high melting point and outstanding dimensional stability. It is as strong and heat-resistant as nylon 6, the company says.
Toray is looking to combine various proprietary technologies to drive further fiber advances including making them thinner and lighter or adding functionality by changing cross-sectional shapes.
Biomethane
Nilit, the largest backward-integrated nylon 6.6 manufacturer headquartered in Migdal Haemek, Israel, meanwhile plans to launch a significant quantity of nylon based on biomethane derived from waste in 2022.
“There is a need to make pragmatic decisions, because we don’t want to wait for 2050,” said the company’s head of global marketing, Sagee Aran. “We at Nilit want to promote actions that we can put in place right now, and that are available not just for the premium sector, but for everybody. Our design solutions are bold and we already have a wide variety of them because in each region there are different sustainable needs to tackle.”
All of these initiatives promise much to boost that tiny percentage of nylon fibers made from either recycled or bio-based content in the coming years.