It was very apparent at this year’s combined Techtextil, Texprocess and one-time-only Heimtextil Summer Special shows which were held in Frankfurt, Germany, from June 21-24, that European legislation is currently driving textile innovation as never before.
Among other things, from January 1, 2025, the separate collection of textile waste, which is already in place in some countries, will be mandatory for all EU Member States and this is leading to some very ambitious proposed solutions.
Chief amongst them is the new ReHubs initiative of Euratex – the Brussels-based organization which represents around 154,000 companies employing 1.47 million workers in the European textiles and clothing industries.
In Frankfurt, Euratex held a somewhat low-key press conference – given the scale of its proposal – to announce an action plan for what is needed to successfully recycle a further 2.5 million tons of Europe’s textile waste by 2030.
ReHubs aims to establish between 150-250 dedicated new recycling hubs throughout Europe in the next few years, as just the starting point for the establishment of a total fiber-to-fiber supply chain.
I’ll return to this far-reaching but totally feasible project later, because it is likely to be highly influential going forward.
Energy
Around 63,000 visitors from 117 countries and 2,300 exhibitors ensured the successful re-launch of the international textile fairs in Frankfurt.
Across all three Messe Frankfurt events there was a palpable sense of energy and real pleasure to be returning to face-to-face business. Exhibitors reported brisk order activity and high satisfaction with the organization in place.
The hangover from the COVID-19 pandemic put considerable obstacles in the way of exhibitors and visitors alike, in terms of delayed deliveries, long queues at airports and other infrastructural problems, but in the end, a determination for success prevailed.
In addition, despite ongoing travel restrictions, the three trade shows maintained their pre-pandemic level of internationality, with the notable exceptions of course – for wildly differing ºreasons – of China and Russia.
From outside Europe, Pakistan, India, South Korea and the USA were among the top visitor nations. Buyers from all over the world took the chance of the trade shows running in parallel for cross-networking and to initiate new business.
“As is the case for many other industries, times are challenging for the textile industry,” said Detlef Braun, Messe Frankfurt’s executive board member, in opening the show. “The consequences of COVID-19, the Ukraine war, strained supply chains, sustainability issues and rising energy prices and recruitment problems ensure the textile industry is under pressure from many sides.
“More than almost any other industry, however, it is also very adept at meeting these challenges with new ideas, developments and business models.”
Innovation
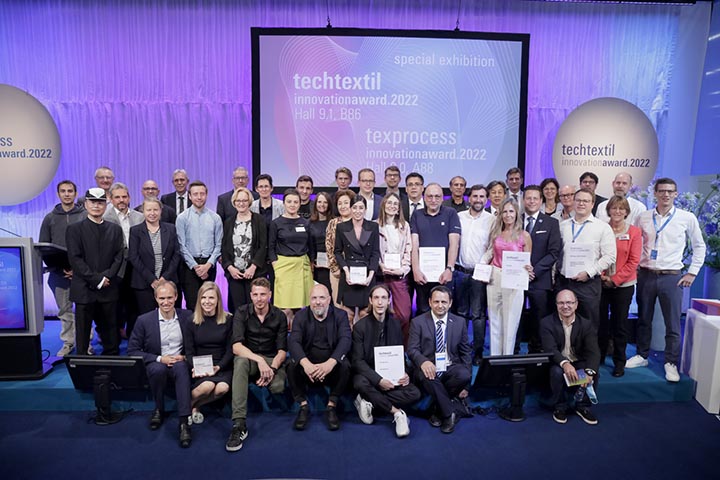
There was no absence of diverse new ideas recognized at the Techtextil Innovation Awards this year.
Researchers at the University of Dresden’s ITM, for example, have developed the world’s first seamless woven heart valve. This development received the 2022 Techtextil New Product Innovation Award.
Every year, cardiovascular disease kills more than 17 million people worldwide and when patients need a heart valve replacement today, they usually receive either mechanical or biological valves.
One disadvantage of the mechanical solutions, however, is that they require lifelong anticoagulant therapy. Biological heart valves, on the other hand, have a much shorter lifespan and their manufacture is complex.
ITM’s valve is made possible by a proprietary Jacquard coil weaving technique which enables tubes with built-in valves to be created without sewing steps. Initial trials have shown promising functionality.
“This is the first woven heart valve that does not require a single seam or other joining technique,” said Dilbar Aibibu, research group leader for bio and medical textiles at ITM. “Due to the complex geometry and function of heart valves, they have not been produced simply by weaving without additional process steps before.”
Strength and conductivity
AluCoat, a new aluminum-coated basalt fiber which combines the strength of basalt with the electrical conductivity of aluminum, earned the 2022 Techtextil New Technology Innovation Award for its German developers Fibrecoat, of Aachen and Deutsche Basalt Faser, of Sangerhausen.
Among many potential applications, it will provide electromagnetic shielding as wallpaper – in buildings such as hospitals or server farms – that is 20 times cheaper than conventional aluminum foil, according to Fibrecoat, based in Aachen, Germany.
It is produced on standard glass and basalt fiber spinning lines to which a coating module is added below the fiber formation area, enabling the coating of each individual filament with liquid aluminum.
Oilseed hemp waste
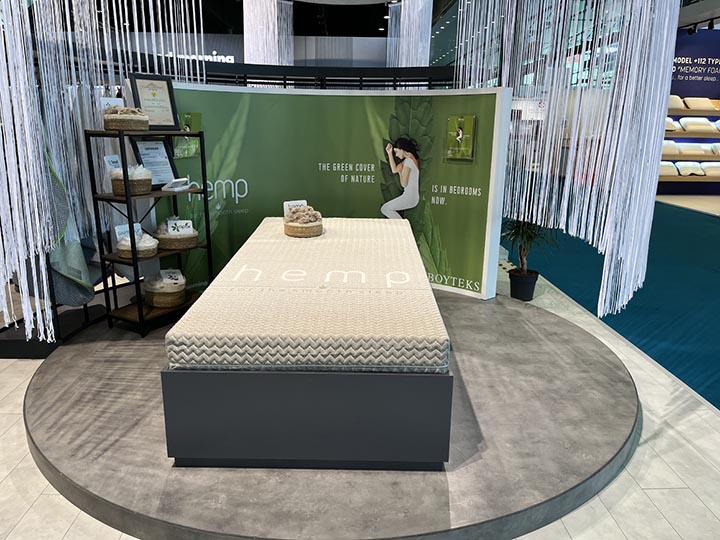
RBX Créations, based in Neuillac, France, received the 2022 Techtextil New Material Innovation Award for its Iroony-branded fiber which is based on a new process for extracting cellulose from the waste of oilseed hemp.
Since hemp is currently grown either to make fibers or to produce hemp oil, it makes perfect sense to combine the two, enabling farmers to combine the markets and resulting in an optimized use of arable land.
Biochemistry is employed to extract the different components from the stems, most notably the cellulose. A patent-pending process is then employed to transform the hemp cellulose into fibers, through dissolution and regeneration technologies.
The company is using HighPerCell technology patented by DITF Denkendorf in Germany and based on ionic liquids as a direct solvent process. For the filament spinning, RBX Créations partnered with DITF through the ELIIT European program.
The goal now is to set-up a new value chain starting from the farmers, and RBX Créations will also valorize the co-products of its process and recycle the solvents for enhanced circularity.
Sumo concept
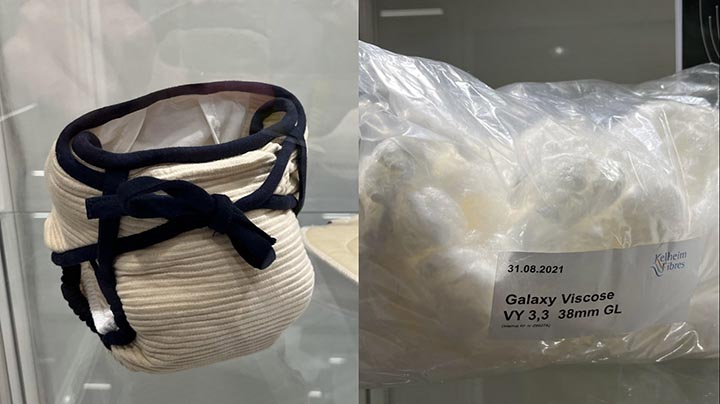
The synergies between knitted and woven structures and randomly-laid nonwovens – along with the separate benefits of viscose and PLA in a highly-engineered absorbent core – are exploited to the full in the new cloth diaper which is now being marketed by Berlin-based design studio Sumo.
This development earned Kelheim Fibres the 2022 Techtextil New Concept Innovation Award.
Up to the age of three, a baby uses around 5,000 diapers which generates an enormous amount of plastic waste – in Germany alone, ten million diapers are disposed of every day.
There are two ways to solve this dilemma – either disposable products are made from bio-based or biodegradable materials, or reusable products with a longer life span replace disposable products.
Sumo has combined both solutions, creating a reusable cloth diaper that is made entirely of sustainable materials while offering high performance and an innovative design.
The fitted Sumo diaper consists of a waterproof cover and absorbent inserts. The cover is sewn to create a pocket in which the absorbent pad is inserted to prevent slipping.
To further enhance the performance of the absorbent pad, the Sumo team turned to Kelheim.
Trilobal fibers
Needlepunched and thermobonded nonwovens with a blend of adapted cross-section viscose and PLA bicomponent fibers were selected to ensure the product’s washability. By combining nonwovens, usually found mainly in the single-use sector, with reusable products, Sumo and Kelheim have taken a completely new approach.
Inside the pad, fibers from Kelheim provide special properties. In the acquisition and distribution layer (ADL), the trilobal cross-section of Galaxy fiber forms capillary channels that enable efficient and optimized liquid distribution and optimum use of the capacity of the absorbent core, offering the lowest rewet values.
In the absorbent core, Bramante segmented hollow fiber stores liquid not only between but also inside the fiber. The liquid remains there even when pressure is applied to the construction, providing excellent rewet values. Bramante can absorb up to 260% of its own weight in liquid compared to cotton, which only achieves values of around 50% here.
The core performs significantly better in tests in terms of air permeability, liquid absorption and rewetting than commercially available solutions made of synthetic fibers or cotton in knitted structures.
Other solutions honored with Techtextil 2022 Innovation Awards were all bio-based, with coatings, binders and materials from Centexbel of Belgium, Portugal’s CITEVE, Italy’s Vérabuccia, Germany’s DITF and Sweden’s OrganoClick.
“Sooner or later, textile materials become non-reusable waste, making recycling a must once all other options are exhausted,” said Euratex president Robert van de Kerkhoff.
ReHubs
All of these bio-based developments feed, of course, into the move away from synthetics and the push to establish circular supply chains, which is certainly what the new ReHubs initiative is all about.
With the backing of a business council of key companies spanning the entire textile supply chain – from fiber leaders like Indorama Ventures and Lenzing to leading sports brand Decathlon and fashion giant Inditex – ReHubs is seeking to transform textile recycling in Europe.
The aim is to make possible the fiber-to-fiber recycling of 2.5 million tons of waste at an investment cost of €6-7 billion, largely to scale up sufficient sorting and processing infrastructure. Each of the 150-250 new recycling centers envisaged would have annual capacities of between 50-100,000 tons.
Once matured and scaled, Euratex believes this could become a profitable industry, with a total annual market size of between €6-8 billion generating around 15,000 direct new jobs by 2030.
“Sooner or later, textile materials become non-reusable waste, making recycling a must once all other options are exhausted,” said Euratex president Robert van de Kerkhoff. “A supply chain requires sorting for both re-use and recycling and a range of mechanical and chemical recycling solutions to be established. We are aiming for the fiber-to-fiber recycling of between 18-26% of Europe’s total textile waste by 2030. However, success is not a given, and to reach critical scale, real collaboration and transition funding is required, along with investments at company level and a huge public sector push.”
The first immediate project will examine current sorting technologies to accurately identify materials for subsequent circular recycling processes. Led by Texaid AG, of Schattdorf, Switzerland, the aim is to establish the first 50,000 ton facility by the end 2024.
Techtextil and Texprocess will next be held that year, from April 23 to 26, so it will be very interesting to see how things have progressed. The next Heimtextil will take place from January 10-13 2023.